Chemical looping combustion
Chemical looping combustion (CLC) is a technological process typically employing a dual fluidized bed system. CLC operated with an interconnected moving bed with a fluidized bed system, has also been employed as a technology process. In CLC, a metal oxide is employed as a bed material providing the oxygen for combustion in the fuel reactor. The reduced metal is then transferred to the second bed (air reactor) and re-oxidized before being reintroduced back to the fuel reactor completing the loop. Fig 1 shows a simplified diagram of the CLC process. Fig 2 shows an example of a dual fluidized bed circulating reactor system and a moving bed-fluidized bed circulating reactor system.
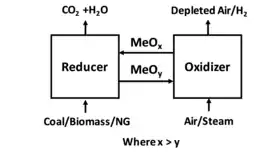
Isolation of the fuel from air simplifies the number of chemical reactions in combustion. Employing oxygen without nitrogen and the trace gases found in air eliminates the primary source for the formation of nitrogen oxide (NOx), produces a flue gas composed primarily of carbon dioxide and water vapor; other trace pollutants depend on the fuel selected.
Description
Chemical looping combustion (CLC) uses two or more reactions to perform the oxidation of hydrocarbon-based fuels. In its simplest form, an oxygen-carrying species (normally a metal) is first oxidized in the air forming an oxide. This oxide is then reduced using a hydrocarbon as a reducer in a second reaction. As an example, an iron based system burning pure carbon would involve the two redox reactions:
-
C(s) + Fe
2O
3(s) → Fe
3O
4(s) + CO
2(g)(1)
-
(2)
If (1) and (2) are added together, the reaction set reduces to straight carbon oxidation i.e.:
-
C(s) + O
2(g) → CO2(g)(3)
CLC was first studied as a way to produce CO2 from fossil fuels, using two interconnected fluidized beds.[3] Later it was proposed as a system for increasing power station efficiency.[4] The gain in efficiency is possible due to the enhanced reversibility of the two redox reactions; in traditional single stage combustion, the release of a fuel's energy occurs in a highly irreversible manner - departing considerably from equilibrium. In CLC, if an appropriate oxygen carrier is chosen, both redox reactions can be made to occur almost reversibly and at relatively low temperatures. Theoretically, this allows a power station using CLC to approach the ideal work output for an internal combustion engine without exposing components to excessive working temperatures.
Thermodynamics

Fig 3 illustrates the energy exchanges in a CLC system graphically and shows a Sankey diagram of the energy fluxes occurring in a reversible CLC based engine. Studying Fig 1, a heat engine is arranged to receive heat at high temperatures from the exothermic oxidation reaction. After converting part of this energy to work, the heat engine rejects the remaining energy as heat. Almost all of this heat rejection can be absorbed by the endothermic reduction reaction occurring in the reducer. This arrangement requires the redox reactions to be exothermic and endothermic respectively, but this is normally the case for most metals.[5] Some additional heat exchange with the environment is required to satisfy the second law; theoretically, for a reversible process, the heat exchange is related to the standard state entropy change, ΔSo, of the primary hydrocarbon oxidation reaction as follows:
- Qo = ToΔSo
However, for most hydrocarbons, ΔSo is a small value and, as a result, an engine of high overall efficiency is theoretically possible.[6]
CO2 capture
Although proposed as a means of increasing efficiency, in recent years, interest has been shown in CLC as a carbon capture technique.[7][8] Carbon capture is facilitated by CLC because the two redox reactions generate two intrinsically separated flue gas streams: a stream from the air reactor, consisting of atmospheric N
2 and residual O
2, but sensibly free of CO2; and a stream from the fuel reactor predominately containing CO2 and H
2O with very little diluent nitrogen. The air reactor flue gas can be discharged to the atmosphere causing minimal CO2 pollution. The reducer exit gas contains almost all of the CO2 generated by the system and CLC therefore can be said to exhibit 'inherent carbon capture', as water vapor can easily be removed from the second flue gas via condensation, leading to a stream of almost pure CO2. This gives CLC clear benefits when compared with competing carbon capture technologies, as the latter generally involve a significant energy penalty associated with either post combustion scrubbing systems or the work input required for air separation plants. This has led to CLC being proposed as an energy efficient carbon capture technology,[9][10] able to capture nearly all of the CO2, for example, from a Coal Direct Chemical Looping (CDCL) plant.[11][12] A continuous 200-hour demonstration results of a 25 kWth CDCL sub-pilot unit indicated nearly 100% coal conversion to CO2 with no carbon carryover to the air reactor.[13][14]
Technology development
First operation of chemical-looping combustion with gaseous fuels was demonstrated in 2003,[15] and later with solid fuels in 2006.[16] Total operational experience in 34 pilots of 0.3 to 3 MW is more than 9000 h.[17][18][19] Oxygen carrier materials used in operation include monometallic oxides of nickel, copper, manganese and iron, as well as various combined oxides including manganese oxides.combined with calcium, iron and silica. Also natural ores have been in use, especially for solid fuels, including iron ores, manganese ores and ilmenite.
Cost and energy penalty
A detailed technology assessment of chemical-looping combustion of solid fuel, i.e. coal, for a 1000 MWth power plant shows that the added CLC reactor costs as compared to a normal circulating fluidized bed boiler are small, because of the similarities of the technologies. Major costs are instead CO2 compression, needed in all CO2 capture technologies, and oxygen production. Molecular oxygen production may also be needed in certain CLC configuration for polishing the product gas from the fuel reactor. In all the added costs were estimated to 20 €/tonne of CO2 whereas the energy penalty was 4%.[20]
Variants and related technologies
A variant of CLC is Chemical-Looping Combustion with Oxygen Uncoupling (CLOU) where an oxygen carrier is used that releases gas-phase oxygen in the fuel reactor, e.g. CuO/Cu
2O.[21] This is helpful for achieving high gas conversion, and especially when using solid fuels, where slow steam gasification of char can be avoided. CLOU operation with solid fuels shows high performance[22][23]
Chemical Looping can also be used to produce hydrogen in Chemical-Looping Reforming (CLR) processes.[24][25] In one configuration of the CLR process, hydrogen is produced from coal and/or natural gas using a moving bed fuel reactor integrated with a steam reactor and a fluidized bed air reactor. This configuration of CLR can produce greater than 99% purity H2 without the need for CO2 separation.[19][26]
Comprehensive overviews of the field are given in recent reviews on chemical looping technologies.[7][27][28]
In summary, CLC can achieve both an increase in power station efficiency simultaneously with low energy penalty carbon capture. Challenges with CLC include the operation of dual fluidized bed (maintaining carrier fluidization while avoiding crushing and attrition[29]), and maintaining carrier stability over many cycles.
See also
- Chemical looping reforming and gasification
- Combustion
- Oxy-fuel combustion
- Oxidizing agent
- Redox (reduction/oxidation reaction)
- Carbon capture and storage
- Lane hydrogen producer
References
- Ströhle, Jochen; Orth, Matthias; Epple, Bernd (January 2014). "Design and operation of a 1MWth chemical looping plant". Applied Energy. 113: 1490–1495. doi:10.1016/j.apenergy.2013.09.008. ISSN 0306-2619.
- Liang-Shih, Fan. Chemical looping partial oxidation : gasification, reforming, and chemical syntheses. Cambridge. ISBN 9781108157841. OCLC 1011516037.
- Lewis, W., Gilliland, E. and Sweeney, M. (1951). "Gasification of carbon". Chemical Engineering Progress. 47: 251–256.
{{cite journal}}
: CS1 maint: multiple names: authors list (link) - Richter, H.J.; Knoche, K.F. (1983). "Reversibility of combustion processes, in Efficiency and Costing – Second law analysis of processes". ACS symposium series (235): 71–85.
{{cite journal}}
: Cite journal requires|journal=
(help) - Jerndal, E., Mattisson, T. and Lyngfelt, A. (2006). "Thermal analysis of chemical-looping combustion". Chemical Engineering Research and Design. 84 (9): 795–806. doi:10.1205/cherd05020.
{{cite journal}}
: CS1 maint: multiple names: authors list (link) - McGlashan, N.R. (2008). "Chemical looping combustion – a thermodynamic study". Proc. Inst. Mech. Eng. C. 222 (6): 1005–1019. CiteSeerX 10.1.1.482.5166. doi:10.1243/09544062JMES790. S2CID 14865943.
- Liang-Shih., Fan (2010). Chemical looping systems for fossil energy conversions. Hoboken, NJ: Wiley-AIChE. ISBN 9780470872888. OCLC 663464865.
- Fan, Liang-Shih; Zeng, Liang; Wang, William; Luo, Siwei (2012). "Chemical looping processes for CO2 capture and carbonaceous fuel conversion – prospect and opportunity". Energy & Environmental Science. 5 (6): 7254. doi:10.1039/c2ee03198a. ISSN 1754-5692.
- Ishida, M.; Jin, H. (1997). "CO2 Recovery in a power plant with chemical looping combustion". Energy Conv. MGMT. 38: S187–S192. doi:10.1016/S0196-8904(96)00267-1.
- Brandvoll, Ø.; Bolland, O. (2004). "Inherent CO2 Capture Using Chemical Looping Combustion in a Natural Gas Fired Power Cycle". Journal of Engineering for Gas Turbines and Power. 126 (2): 316–321. doi:10.1115/1.1615251.
- Gorder, Pam (February 5, 2013). "New Coal Technology Harnesses Energy Without Burning, Nears Pilot-Scale Development". researchnews.osu.edu. Archived from the original on December 21, 2016. Retrieved 2016-11-04.
- Bayham, Samuel; McGiveron, Omar; Tong, Andrew; Chung, Elena; Kathe, Mandar; Wang, Dawei; Zeng, Liang; Fan, Liang-Shih (May 2015). "Parametric and dynamic studies of an iron-based 25-kW th coal direct chemical looping unit using sub-bituminous coal". Applied Energy. 145: 354–363. doi:10.1016/j.apenergy.2015.02.026. ISSN 0306-2619.
- Bayham, Samuel C.; Kim, Hyung R.; Wang, Dawei; Tong, Andrew; Zeng, Liang; McGiveron, Omar; Kathe, Mandar V.; Chung, Elena; Wang, William (2013-03-08). "Iron-Based Coal Direct Chemical Looping Combustion Process: 200-h Continuous Operation of a 25-kWth Subpilot Unit". Energy & Fuels. 27 (3): 1347–1356. doi:10.1021/ef400010s. ISSN 0887-0624.
- Chung, Cheng; Pottimurthy, Yaswanth; Xu, Mingyuan; Hsieh, Tien-Lin; Xu, Dikai; Zhang, Yitao; Chen, Yu-Yen; He, Pengfei; Pickarts, Marshall (December 2017). "Fate of sulfur in coal-direct chemical looping systems". Applied Energy. 208: 678–690. doi:10.1016/j.apenergy.2017.09.079. ISSN 0306-2619.
- Lyngfelt, A. (2004). "A New Combustion Technology". Greenhouse Gas Issues. No.73: 2–3.
- Lyngfelt, A. (2007). "Chemical-looping combustion of solid fuels". Greenhouse Gas Issues. No. 85: 9–10.
- Lyngfelt, A. (2011). "Oxygen carriers for chemical-looping combustion - 4000 h of operational experience". Oil & Gas Science and Technology. 66:2 (2): 161–172. doi:10.2516/ogst/2010038.
- Lyngfelt, A; Linderholm, C. "Chemical-Looping Combustion of Solid Fuels – status and recent progress". 13th International Conference on Greenhouse Gas Control Technologies, GHGT-13, 14–18 November 2016, Lausanne, Switzerland.
- Tong, Andrew; Bayham, Samuel; Kathe, Mandar V.; Zeng, Liang; Luo, Siwei; Fan, Liang-Shih (January 2014). "Iron-based syngas chemical looping process and coal-direct chemical looping process development at Ohio State University". Applied Energy. 113: 1836–1845. doi:10.1016/j.apenergy.2013.05.024. ISSN 0306-2619.
- Lyngfelt, Anders; Leckner, Bo (2015-11-01). "A 1000 MWth boiler for chemical-looping combustion of solid fuels – Discussion of design and costs". Applied Energy. 157: 475–487. doi:10.1016/j.apenergy.2015.04.057.
- Mattisson, T., Lyngfelt, A. and Leion, H. (2009). "Chemical-Looping with Oxygen Uncoupling for Combustion of Solid Fuels". International Journal of Greenhouse Gas Control. 3: 11–19. doi:10.1016/j.ijggc.2008.06.002.
{{cite journal}}
: CS1 maint: multiple names: authors list (link) - Abad, A., Adánez-Rubio, I. Gayán, P. García-Labiano, F. de Diego L. F. and Adánez, J. (2012). "Demonstration of chemical-looping with oxygen uncoupling (CLOU) process in a 1.5kW th continuously operating unit using a Cu-based oxygen-carrier". International Journal of Greenhouse Gas Control. 6: 189–200. doi:10.1016/j.ijggc.2011.10.016. hdl:10261/75134.
{{cite journal}}
: CS1 maint: multiple names: authors list (link) - Zhou, Zhiquan; Han, Lu; Nordness, Oscar; Bollas, George M. (2015-05-01). "Continuous regime of chemical-looping combustion (CLC) and chemical-looping with oxygen uncoupling (CLOU) reactivity of CuO oxygen carriers". Applied Catalysis B: Environmental. 166–167: 132–144. doi:10.1016/j.apcatb.2014.10.067.
- Rydén, M.; Lyngfelt, A. (2006). "Using steam reforming to produce hydrogen with carbon dioxide capture by chemical-looping combustion". Journal of Hydrogen Energy. 31 (10): 1631–1641. doi:10.1016/j.ijhydene.2005.12.003.
- Rydén, M.; Lyngfelt, A. & Mattisson, T. (2006). "Synthesis gas generation by chemical-looping reforming in a continuously operating laboratory reactor". Fuel. 85 (12–13): 1631–1641. doi:10.1016/j.fuel.2006.02.004.
- Tong, Andrew; Sridhar, Deepak; Sun, Zhenchao; Kim, Hyung R.; Zeng, Liang; Wang, Fei; Wang, Dawei; Kathe, Mandar V.; Luo, Siwei (January 2013). "Continuous high purity hydrogen generation from a syngas chemical looping 25kWth sub-pilot unit with 100% carbon capture". Fuel. 103: 495–505. doi:10.1016/j.fuel.2012.06.088. ISSN 0016-2361.
- Lyngfelt, A. and Mattisson, T. (2011) ”Materials for chemical-looping combustion”, in D. Stolten and V. Scherer, Efficient Carbon Capture for Coal Power Plants, Weinheim, WILEY-VCH Verlag GmbH & Co.. KGaA, 475-504.
- Adánez, J.; Abad, A. Garcia-Labiano; F. Gayan P. & de Diego, L. (2012). "Progress in Chemical-Looping Combustion and Reforming technologies'". Progress in Energy and Combustion Science. 38 (2): 215–282. doi:10.1016/j.pecs.2011.09.001. hdl:10261/78793.
- Kim, J.Y., Ellis, N., Lim, C.J. and Grace, J.R. (2019). "Attrition of Binary Mixtures of Solids in a Jet Attrition Unit". Powder Technology. 352: 445–452. doi:10.1016/j.powtec.2019.05.010. S2CID 164585879.
{{cite journal}}
: CS1 maint: multiple names: authors list (link)
External links
- http://www.entek.chalmers.se/lyngfelt/co2/co2.htm
- chemical-looping.at
- Chemical Looping, Institute for Combustion Science, Western Kentucky University.
- http://www.icb.csic.es/index.php?id=144&L=1
- http://www3.imperial.ac.uk/carboncaptureandstorage
- http://www.encapco2.org/sp4.htm Archived 2008-04-21 at the Wayback Machine
- Carbon capture and chemical looping technology - an update on progress. Webinar recording, Carl Bozzuto and the Global CCS Institute, 11 July 2012.