Cone calorimeter
A cone calorimeter is an instrument used to study the behavior of fire in small samples of various materials in their condensed phase. It is widely used in the field of Fire Safety Engineering.[1]
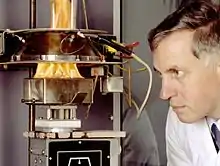
It gathers data about the ignition time, mass loss, combustion products, heat release rate and other parameters associated with the sample's burning properties. The principle of the measurement of the heat release rate is based on the Huggett's principle[2] that the gross heat of combustion of any organic material is directly related to the amount of oxygen required for combustion.
Oxygen consumption calorimetry has made the measurement of the heat release rate of a fire a routine part of fire testing for both research and for regulatory compliance. Heat release rate is a primary metric of fire energy and has informed modern fire protection engineering. The device allows a sample to be exposed to different heat fluxes over its surface. Its name comes from the conical shape of the radiant heater that produces a nearly uniform heat flux over the surface of the sample under study.[3]
Development
In the 1960's researchers at the National Institute of Standards and Technology (NIST) had determined that the heat release from a fire directly related to the growth rate of a fire and was thus a major factor in the fire's risk to life and property. However, existing devices used to measure heat release typically estimated the heat release of a fire by measuring the increase in temperature of ambient air flowing past the combusting material. These measurements of heat release were often inaccurate, so a more reliable method was desired.[4]
Through the 1960's and 1970's, efforts were made to develop a more accurate method for estimating heat release. In 1977, William Parker published research that found that the heat release during combustion was roughly constant per unit of oxygen consumed for a variety of fuels. By measuring the oxygen consumed during combustion, one could estimate heat release of a fire, with this method being termed oxygen consumption calorimetry.[5] This finding was actually a re-discovery of oxygen consumption calorimetry, which was first found in 1917 by W. M. Thornston whose research similarly found that, during combustion of organic liquids and gases, a constant amount of heat was released per unit mass of oxygen consumed.[6] Clayton Huggett provided a rigorous proof of concept in his 1980 paper that gave the fire protection engineering community confidence that oxygen consumption calorimetry was a significantly more accurate method for estimating heat release than prior methods. For their contribution to fire safety research through the development of oxygen consumption calorimetry, the 2016 DiNenno Prize was granted to William Parker with commendation for the late Clayton Huggett.
Following the development of oxygen consumption calorimetry, work began on implementing the principle into a bench scale instrument to measure heat release. In 1982, Vytenis Babrauskas and colleagues at the Center for Fire Research built the first cone calorimeter, a device that uses oxygen consumption calorimetry to measure the heat release (and this flammability) of materials.[7] The cone calorimeter was quickly realized as an important instrument for modern fire safety tests, being formally recognized in 1988 by an R&D 100 award. The cone calorimeter is used today for both regulatory and research purposes.[3]
Fire Safety
A cone calorimeter is also used in fire testing and research. It allows characterization of the fire properties of small samples of materials (approx. 100x100 mm square). The fire characteristics of a material can be determined from several different standard models of the cone calorimeter that can be used to evaluate different aspects of flammable materials. The research using the cone calorimeters can be used for product safety, environment, and health services testing.
This device can be important when dealing with safety issues. By using the device, it is easier to see how many different materials react with fire. Knowing that information, safety regulations can be made easily to protect the people that come in contact or work with the material often. It is important to know and understand the flammability, the heat of combustion, ignitability, heat release, and smoke production of many materials in order to maintain a safe environment, in which this can be achieved using a calorimeter. The cone calorimeter is a reduced-scale apparatus. Scale effects must be considered when using cone results to predict real-world fires.
Use
Many devices that were used before the invention of the cone calorimeter were known to be very faulty and had several experimental errors. However, research improved with the addition of the cone calorimeter in 1982. Unlike any other apparatus, the cone calorimeter introduced a system for measuring smoke optically and soot yield gravimetrically. The changes in design allowed for the operation of the device to become much easier and the data more reliable. It is now considered one of the most important devices for fire testing and fire protection engineering, and its usage in research has grown over the years.
The fire calorimeter is used by encasing a small sample in aluminium foil, wool, and a retainer frame that is ignited below an exhaust hood. A conical heater is placed in between in order for materials to combust. The cone-shaped Inconel heating element provides a controllable radiant flux onto the sample, turning electricity into heat not unlike an electric toaster or oven. The flammability of a sample can be characterized as a function of heat flux onto a sample. The conical heater is open in its center, allowing products of combustion to flow upwards into an exhaust duct.
Ventilation is also a very important part of the device, as well as the electrical power to run the conical heater. A small water supply is necessary to cool and regulate the heat in the system of the device. Since temperature and pressure are being evaluated, two different measurement tools are needed in the exhaust tube. Gas samples, smoke measurements, and soot collections are also acquired using this device.
Test standards
- ASTM E 1354
- ASTM D 5485
- CAN/ULC-S135
- ISO 5660-1
- NFPA 271
References
- Twilley, William H. (1988). "User's Guide for the Cone Calorimeter". NASA Sti/Recon Technical Report N. 89: 22086. Bibcode:1988STIN...8922086T.
- Hugget, C (1980). "Estimation of rate of heat release by means of oxygen consumption measurements". Fire and Materials. 4 (2): 61–65. CiteSeerX 10.1.1.208.8855. doi:10.1002/fam.810040202.
- Beyler, Craig (14 January 2017). "Oxygen consumption calorimetry, William Parker: 2016 DiNenno Prize". Fire Science Reviews. 61 (1). doi:10.1186/s40038-016-0016-z.
Material was copied from this source, which is available under a Creative Commons Attribution 4.0 International License.
- Lide, David R (2001). A century of excellence in measurements, standards, and technology 1901-2000 (Report). Gaithersburg, MD: National Institute of Standards and Technology. pp. 280–282.
- Parker, W J (1977). An investigation of the fire environment in the ASTM E 84 tunnel test (Report). Gaithersburg, MD: National Bureau of Standards.
- Thornton, W. M. (1917). "The relation of oxygen to the heat of combustion of organic compounds". The London, Edinburgh, and Dublin Philosophical Magazine and Journal of Science. 33 (194): 196–203. doi:10.1080/14786440208635627.
- Babrauskas, Vytenis; Lawson, J Randall; Walton, W D; Twilley, William H (1982). Upholstered furniture heat release rates measured with a furniture calorimeter (Report). Gaithersburg, MD: National Bureau of Standards.
External links
- U.S. National Bureau of Standards "NBS Special Publication 745: User Guide for Cone Calorimeter" 1988
- Cone Calorimeter by Fire Testing Technology Ltd
- Diagram of a cone calorimeter
- Color diagram of a cone calorimeter
- Ten Years of Heat Release Research with the Cone Calorimeter by Dr. Vyto Babrauska of Fire Science and Technology, Inc
- "Cone calorimeter analysis of UL-94 V-rated plastics" Fire Mater. 2007; 31:257–283