Liquid apogee engine
A liquid apogee engine (LAE), or apogee engine, refers to a type of chemical rocket engine typically used as the main engine in a spacecraft.
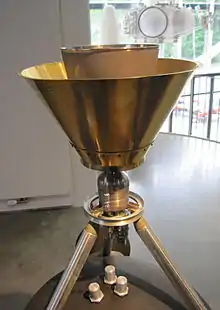
The name apogee engine derives from the type of manoeuvre for which the engine is typically used, i.e. an in-space delta-v change made at the apogee of an elliptical orbit in order to circularise it. For geostationary satellites, this type of orbital manoeuvre is performed to transition from a geostationary transfer orbit and place the satellite on station in a circular geostationary orbit. Despite the name, an apogee engine can be used for a range of other manoeuvres, such as end-of-life deorbit,[1] Earth orbit escape, planetary orbit insertion[2][3] and planetary descent/ascent.[4]
In some parts of the space industry an LAE is also referred to as a liquid apogee motor (LAM), a liquid apogee thruster (LAT) and, depending on the propellant, a dual-mode liquid apogee thruster (DMLAT). Despite the ambiguity with respect to the use of engine and motor in these names, all use liquid propellant. An apogee kick motor (AKM) or apogee boost motor (ABM) such as the Waxwing, however, uses solid propellant.[5] These solid-propellant versions are not used on new-generation satellites.[5][6]
History
The apogee engine traces its origin to the early 1960s, when companies such as Aerojet, Rocketdyne, Reaction Motors, Bell Aerosystems, TRW Inc. and The Marquardt Company were all participants in developing engines for various satellites and spacecraft.[7]
Derivatives of these original engines are still used today and are continually being evolved[8][9][10] and adapted for new applications.[11]
Layout
A typical liquid apogee engine scheme could be defined[12] as an engine with:
- pressure-regulated hypergolic liquid bipropellant feed,
- thermally isolated solenoid or torque motor valves,
- injector assembly containing (though dependent on the injector) central oxidant gallery and outer fuel gallery,
- radiative and film-cooled combustion chamber,
- characteristic velocity limited by thermal capability of combustion chamber material,
- Thrust coefficient limited by supersonic area ratio of the expansion nozzle.
To protect the spacecraft from the radiant heat of the combustion chamber, these engines are generally installed together with a heat shield.
Propellant
Apogee engines typically use one fuel and one oxidizer. This propellant is usually, but not restricted to,[7] a hypergolic combination such as:
Hypergolic propellant combinations ignite upon contact within the engine combustion chamber and offer very high ignition reliability, as well as the ability for reignition.
In many instances mixed oxides of nitrogen (MON), such as MON-3 (N
2O
4 with 3 wt% NO), is used as a substitute for pure N
2O
4.[13]
The use of N
2H
4 is under threat in Europe due to REACH regulations. In 2011 the REACH framework legislation added N
2H
4 to its candidate list of substances of very high concern. This step increases the risk that the use of N
2H
4 will be prohibited or restricted in the near- to mid-term.[14][15]
Exemptions are being sought to allow N
2H
4 to be used for space applications, however to mitigate this risk, companies are investigating alternative propellants and engine designs.[16] A change over to these alternative propellants is not straightforward, and issues such as performance, reliability and compatibility (e.g. satellite propulsion system and launch-site infrastructure) require investigation.[15]
Performance
The performance of an apogee engine is usually quoted in terms of vacuum specific impulse and vacuum thrust. However, there are many other details which influence performance:
- The characteristic velocity is influenced by design details such as propellant combination, propellant feed pressure, propellant temperature, and propellant mixture ratio.
- The thrust coefficient is influenced primarily by the nozzle supersonic area ratio.
A typical 500 N-class hypergolic liquid apogee engine has a vacuum specific impulse in the region of 320 s,[17][18][19][20] with the practical limit estimated to be near 335 s.[7]
Though marketed to deliver a particular nominal thrust and nominal specific impulse at nominal propellant feed conditions, these engines actually undergo rigorous testing where performance is mapped over a range of operating conditions before being deemed flight-qualified. This means that a flight-qualified production engine can be tuned (within reason) by the manufacturer to meet particular mission requirements, such as higher thrust.[21]
Operation
Most apogee engines are operated in an on–off manner at a fixed thrust level. This is because the valves used only have two positions: open or closed.[22]
The duration for which the engine is on, sometimes referred to as the burn duration, depends both on the manoeuvre and the capability of the engine. Engines are qualified for a certain minimal and maximal single-burn duration.
Engines are also qualified to deliver a maximal cumulative burn duration, sometimes referred to as cumulative propellant throughput. The useful life of an engine at a particular performance level is dictated by the useful life of the materials of construction, primarily those used for the combustion chamber.[12]
Applications
A simplified division can be made between apogee engines used for telecommunications and exploration missions:
- Present telecommunication spacecraft platforms tend to benefit more from high specific impulse than high thrust.[23] The less fuel is consumed to get into orbit, the more is available for station keeping when on station. This increase in the remaining propellant can be directly translated to an increase in the service lifetime of the satellite, increasing the financial return on these missions.
- Planetary exploration spacecraft, especially the larger ones, tend to benefit more from high thrust than high specific impulse.[24] The quicker a high delta-v manoeuvre can be executed, the higher the efficiency of this manoeuvre, and the less propellant is required. This reduction in the propellant required can be directly translated to an increase in the bus and payload mass (at design stage), enabling better science return on these missions.[12][23]
The actual engine chosen for a mission is dependent on the technical details of the mission. More practical considerations such as cost, lead time and export restrictions (e.g. ITAR) also play a part in the decision.
References
- "Unified Propulsion System - Background". Airbus Defence and Space. Archived from the original on 2014-09-25. Retrieved 29 January 2015.
- Amos, Jonathan (2012-09-04). "Juno Jupiter probe gets British boost". BBC News. Retrieved 29 January 2015.
- Domingue, D. L.; Russell, C. T. (19 December 2007). The MESSENGER Mission to Mercury. Springer Science & Business Media. p. 197. ISBN 978-0-387-77214-1.
- "Industrial Policy Committee, Robotic Exploration Plan, Programme of Work 2009-2014 and relevant Procurement Plan" (PDF). European Space Agency. Archived from the original (PDF) on 2016-03-03. Retrieved 25 January 2015.
- Pocha, J. J. (1987). "The Apogee Manoeuvre". Space Technology Library Volume 1. An introduction to mission design for geostationary satellites. Chapter 4: The Apogee Manoeuvre. Springer. pp. 51–66. doi:10.1007/978-94-009-3857-1_4. ISBN 978-94-010-8215-0.
- Ley, Wilfred; Wittmann, Klaus; Hallmann, Willi, eds. (2009). Handbook of space technology. John Wiley & Sons, Ltd. pp. 323–324. ISBN 978-0-470-69739-9.
- Stechman, Carl; Harper, Steve (2010). "Performance improvements in small earth storable rocket engines - an era of approaching the theoretical". 46th AIAA/ASME/SAE/ASEE Joint Propulsion Conference (2010–6884).
- "ESA investigates ALM for in-space satellite engines". LayerWise. Archived from the original on 2014-11-29. Retrieved 15 November 2014.
- Hyde, Simon (2012). "Combustion chamber design for additive manufacturing". Space Propulsion 2012 Conference, Bordeaux, France.
- Hyde, Simon (2012). "A design optimisation study of a generic bi-propellant injector for additive manufacturing". Space Propulsion 2012 Conference, Bordeaux, France.
- Werner, Debra (2013-07-15). "Space propulsion - Moog sees higher-thrust liquid propellant engine as right fit for Mars missions". www.spacenews.com. Archived from the original on November 15, 2014. Retrieved 15 November 2014.
- Naicker, Lolan; Wall, Ronan; David, Perigo (2014). "An overview of development model testing for the LEROS 4 High Thrust Apogee Engine". Space Propulsion 2014 Conference, Cologne, Germany (2969298).
- Wright, A. C. (February 1977). USAF Propellant Handbooks: Nitric Acid / Nitrogen Tetroxide Oxidizers (AFRPL-TR-76-76 ed.). Martin Marietta Corporation. p. 2.3–3.
- "Considering hydrazine-free satellite propulsion". ESA. Retrieved 15 November 2014.
- Valencia-Bel, Ferran (2012). "Replacement of Conventional Spacecraft Propellants with Green Propellants". Space Propulsion 2012 Conference, Bordeaux, France.
- "Green propulsion". www.sscspace.com. Archived from the original on 29 November 2014. Retrieved 15 November 2014.
- "Apogee/Upper Stage Thrusters". www.moog.com. Archived from the original on 2015-03-02. Retrieved 15 November 2014.
- "400 N Bipropellant Apogee Motors". Astrium Space Propulsion. Archived from the original on 2014-04-26. Retrieved 15 November 2014.
- "Bipropellant Rocket Engines". www.rocket.com. Retrieved 15 November 2014.
- "Satellite Propulsion System". www.ihi.co.jp. Archived from the original on 24 November 2014. Retrieved 15 November 2014.
- "LEROS engine propels the Juno spacecraft on its historic voyage to Jupiter". Retrieved 15 November 2014.
- Houston, Martin; Smith, Pete; Naicker, Lolan; Perigo, David; Wall, Ronan (2014). "A high flow rate apogee engine solenoid valve for the next generation of ESA planetary missions". Space Propulsion 2014 Conference, Cologne, Germany (2962486).
- Naicker, Lolan; Baker, Adam; Coxhill, Ian; Hammond, Jeff; Martin, Houston; Perigo, David; Solway, Nick; Wall, Ronan (2012). "Progress towards a 1.1 kN apogee engine for interplanetary propulsion". Space Propulsion 2012, Bordeaux, France (2394092).
- Perigo, David (2012). "Large platform satellite propulsion with a focus on exploration applications". Space Propulsion 2012 Conference, San Sebastian, Spain.