NATO EPVAT testing
NATO EPVAT testing is one of the three recognized classes of procedures used in the world to control the safety and quality of firearms ammunition.
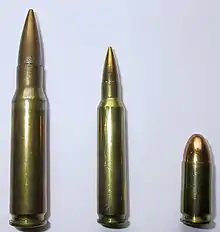
Beside this, there are also the Commission internationale permanente pour l'épreuve des armes à feu portatives (C.I.P.) class of procedures and the Sporting Arms and Ammunition Manufacturers' Institute (SAAMI) class of procedures.
EPVAT Testing is described in unclassified documents by NATO, more precisely by the AC/225 Army Armaments Group (NAAG).[1] It was accepted as NATO Standardization Agreement STANAG 4823 and Allied Engineering Publication 97 (AEP-97) on November 2020.[2]
EPVAT is an abbreviation for "Electronic Pressure, Velocity and Action Time" (French "Pression électronique, vitesse et durée d’action"). Action Time here means the (short amount of) time required between the ignition of the primer and the projectile leaving the barrel. This is a comprehensive procedure for testing ammunition using state-of-the-art instruments and computers. The procedure itself was initially described in NATO document AC/225 (Com. III/SC.1)D/200.
Unlike the C.I.P. procedures aiming only at the user's safety, the NATO procedures for ammunition testing also include comprehensive functional quality testing in relation with the intended use. That is, not only the soldier's safety is looked at, but also their capacity to incapacitate the enemy. As a result, for every ammunition order by NATO, a complete acceptance approval on both safety and functionality is performed by both NATO and the relevant ammunition manufacturers in a contradictory fashion.
For this, a highly accurate and indisputable protocol has been defined by NATO experts using a system of reference cartridges.[1][3][4]
The civilian organisations C.I.P. and SAAMI use less comprehensive test procedures than NATO, but NATO test centres have the advantage that only a few chamberings are in military use. The C.I.P. and SAAMI proof houses must be capable of testing hundreds of different chamberings requiring many different test barrels, etc.
NATO Reference cartridges system
In this system, the ammunition manufacturers, in close cooperation with NATO, have set aside a batch (also termed "lot") of ammunition they consider to be of very good quality and representative of ammunition that should be delivered to the armies in the following years. This batch is maintained at approved NATO test centres and distributed to the manufacturers involved. When a new batch (lot) is delivered, a set of 20 reference cartridges are fired to see how they behave with the local equipment and with the current atmospheric conditions. Results are then compared to the reference values, as maintained by NATO and correctors (delta values) are computed. Then, samples of the current batch (lot) of ammunition are fired and the correctors are applied on the measured value giving a result "comparable" to the reference itself.[5]
This test is performed under normal conditions at 21 °C (70 °F), but also by simulating cold polar −54 °C (−65 °F) or hot desert 52 °C (126 °F) conditions using special cooling equipment and ovens to cool or heat the ammunition under test to the appropriate levels of humidity and temperatures required.[4][6]
Proofing
The minimum proof and performance requirements for small arms ammunition of NATO calibres are covered in STANAGs as follows:[7]
- 5.56 mm. STANAG 4172 and NATO Manual of Proof and Inspection AC/225 (LG/3-SG/1) D/8.[8]
- 7.62 mm. STANAG 2310 and NATO Manual of Proof and Inspection AC/225 (LG/3-SG/1) D/9.
- 9 mm. STANAG 4090 and NATO Manual of Proof and Inspection AC/225 (P111-SP1) D/170(REV).
- 12.7 mm. STANAG 4383 and NATO Manual of Proof and Inspection AC/225 (LG/3-SG/1) D/11.
Each weapon and component considered vulnerable to the effects of a rapid change in pressure, for example barrels, breech blocks and bolts, will be tested by firing one dry round at a corrected minimum of 25% over-pressure and one oiled round at a corrected minimum of 25% over-pressure. 25% over-pressure means 25% in excess of the Service Pressure (Pmax). The Service Pressure is defined as the mean pressure generated by the Service Cartridge at a temperature of 21 °C (70 °F). Such a high pressure proof is conducted with both the weapon and ammunition conditioned to an ambient temperature of 21 °C (70 °F).
Each weapon will be individually tested, from an ammunition lot that produces a minimum corrected mean chamber pressure in accordance with the table below:[1]
Calibre | Specific Weapon Detail | Service Pressure Pmax MPa / (psi) |
Proof Round Pressure Requirement MPa / (psi) |
Detailed Requirement for Proof Ammunition |
---|---|---|---|---|
5.56 mm (5.56×45mm NATO) | Designed to chamber NATO ammunition | 430.0 / (62,366) | 537.5 / (77,958) | Pressure recorded in NATO design EPVAT Barrel with Kistler 6215 Transducer,[9][10] HPI GP6 Transducer[11] or by equipment to Commission internationale permanente pour l’épreuve des armes à feu portatives (C.I.P.) requirements |
7.62 mm (7.62×51mm NATO) | Designed to chamber NATO ammunition | 415.0 / (60,190) | 519.0 / (75,275) | Pressure recorded in NATO design EPVAT Barrel with Kistler 6215 Transducer, HPI GP6 Transducer or by equipment to C.I.P. requirements |
9 mm (9×19mm NATO) | Designed to chamber NATO ammunition | 252.0 / (36,550) | 315.0 / (45,687) | Pressure recorded in C.I.P. design barrel at mid-case position |
12.7 mm (12.7×99mm NATO) | Designed to chamber NATO ammunition | 417.0 / (60,481) | 521.3 / (75,608) | Pressure recorded in NATO design EPVAT Barrel with Kistler 6215 Transducer, HPI GP6 Transducer or by equipment to C.I.P. requirements |
All other small arms ammunition for use in "non-NATO Chamber" weapons | As defined by the current C.I.P. legislation. | As defined by the current C.I.P. legislation |
The above proof round pressure requirements for the 9 mm and 12.7 mm rounds established by the British Ministry of Defence are higher than the current (2008) C.I.P. proof round pressure requirement legislation for the civilian equivalent 9 mm Parabellum (C.I.P. Pmax rating 235 MPA / (34,083 psi) and .50 Browning (C.I.P. Pmax rating 370 MPA / (53,663 psi) rounds.[12][13] The 9×19mm NATO and 12.7×99mm NATO rounds can be regarded as overpressure ammunition
Unlike the civilian C.I.P. test procedures NATO EPVAT testing procedures for the "NATO chamberings" require the pressure sensor or transducer to be mounted ahead of the case mouth. The advantage of this mounting position is that there is no need to drill the cartridge case to mount the transducer. Drilling prior to firing is always a time-consuming process (fast quality control and feedback to production is essential during the ammunition manufacturing process). The disadvantage of this mount is that the pressure rises much faster than in a drilled cartridge case. This causes high frequency oscillations of the pressure sensor (approx 200 kHz for a Kistler 6215 transducer) and this requires electronic filtering with the drawback that filtering also affects the lower harmonics where a peak is found causing a slight error in the measurement. This slight error is not always well mastered and this causes a lot of discussion about the filter order, cutoff frequency and its type (Bessel or Butterworth).[14]
Since NATO EPVAT uses technically differing proof test standards than SAAMI and C.I.P. do, EPVAT pressures cannot be directly compared with SAAMI and C.I.P. pressures.[15][16]
See also
- NATO
- NATO cartridge
- Small arms ammunition pressure testing
- Overpressure ammunition
- CIP, a European standardization organization for firearm cartridges
- SAAMI, an American standardization organization for firearm cartridges
- DEVA, a German firearms test institute
- Wildcat cartridge
References
- Notes
- "Defence Standard 05-101, Proof of Ordnance, Munitions, Armour and Explosives, Part 1, Requirements" (PDF). Ministry of Defence Defence Standardization. 20 May 2005. Archived from the original (PDF) on 16 July 2011.
- AEP-97, Multi-Calibre Manual of Proof and Inspection (M-CMOPI) for NATO Small Arms Ammunition / Manuel des procédures d’épreuve et d’inspection (MOPI) multicalibre pour les munitions OTAN des armes de petit calibre, edition A, version 1, volume 12: Combination Electronic Pressure, Velocity and Action Time (EPVAT) Test Procedures, NATO Army Armaments Group (AC/225-NAAG), NATO Standardization Office (NSO), October 2020
- "Defence Standard 05-101, Proof of Ordnance, Munitions, Armour and Explosives, Part 2, Guidance" (PDF). UK Government Web Archive. Ministry of Defense Defence Standardization. 20 May 2005. Archived from the original (PDF) on 8 April 2010.
- "Defence Standard 05-101, Proof of Ordnance, Munitions, Armour and Explosives, Part 3, Statistical Methods for Proof" (PDF). Ministry of Defence Defence Standardization. 20 May 2005. Archived from the original (PDF) on 16 July 2011.
- Gacek, Józef; Stępniak, Wiesław; Piątek, Marian (2006). "The Analysis of Application and Requirements Small Caliber Reference Ammunition and Polish Achievement in the Field of Working Out National Reference Ammunition" (PDF). Biblioteka Nauki. Archived from the original (PDF) on 22 January 2016.
- Geddes III, Lascelles A. (9 May 2007). "NATO Small Arms Ammunition Interchangeability via Direct Evidence Testing" (PDF). Defense Technical Information Center. US Army RDECOM. Archived from the original (PDF) on 2010-02-15. Retrieved 2008-02-10.
- Pellegrino, Dominic; Kirkman, Charles “Tim” (25 May 2011). "NATO Small Arms Ammunition Interchangeability via Direct Evidence Testing" (PDF). Defense Technical Information Center. US Army RDECOM. Archived from the original (PDF) on 19 July 2013.
- "STANAG 4172 5.56 mm Ammunition (Linked or Otherwise) MAS/176-MMS/4172" (PDF). NATO Military Agency for Standardization. 5 May 1993. Archived from the original (PDF) on 12 November 2020.
- Meier, Walter; Engeler, Paul; Metz, Robert (20–21 June 2000). "Defining Parameters for Ballistic High Pressure Sensors (Transducer Workshop June 20-21, 2000)" (PDF). Kistler Instrument Corporation. Archived from the original (PDF) on 6 December 2008.
- "Type 6215 Quartz High-Pressure Sensor for Ballistic Pressure Measurement to 6000 bar" (PDF). Industrial Engineering News Europe. Kistler Instrument Corporation. 2010. Archived from the original (PDF) on 3 March 2016.
- "HPI Piezoelectric High Pressure Transducers – GP Series including NATO Approval" (PDF). High Pressure Instrumentation. March 2018. Archived from the original (PDF) on 7 July 2021.
- "TDCC 9 mm Luger" (PDF). CIP. 14 June 1984. Archived from the original (PDF) on 7 October 2013.
- "TDCC 50 Browning" (PDF). CIP. 31 May 1996. Archived from the original (PDF) on 23 August 2014.
- Geddes, Lascelles A. (October 1995). "Technical Report ARCCD-TR-95005 5.56 mm M856 Tracer Mini Round Round Robin Study" (PDF). Defense Technical Information Center. US Army ARDEC/CCAC. Archived from the original (PDF) on 6 August 2022.
- "MEKEK 5.56 mm×45 (SS109/M855) Ball Cartridge EPVAT Specifications".
- "MEKEK 5.56 mm×45 (L11/M856) Tracer Cartridge EPVAT Specifications".
- Bibliography
- Proof of Ordnance, Munitions, Armour and Explosives, Ministry of Defence Defence Standard 05-101 Part 1 – Requirements (Archived)
- Proof of Ordnance, Munitions, Armour and Explosives, Ministry of Defence Defence Standard 05-101 Part 2 – Guidance (Archived)
- Proof of Ordnance, Munitions, Armour and Explosives, Ministry of Defence Defence Standard 05-101 Part 3 – Statistical Methods for Proof (Archived)
- NATO Small Arms Ammunition Interchangeability via Direct Evidence Testing (Archived)
- C.I.P. decisions, texts and tables, CD-ROM version download (ZIP and RAR format) (Archived)
- NATO Standard AEP-97, Multi-Calibre Manual of Proof and Inspection (M-CMOPI) for NATO Small Arms Ammunition, Volume 8, NATO Reference Ammunition, Edition A Version 1 (from page 261) Archived
External links
- NATO Army Armaments Group (NAAG) (Archived)
- Thales brochure on 5.56 mm F1 ball ammunition conforming to the design parameters of the NATO STANAG 4172 and tested with Kistler 6215 transducers at different temperatures (Archived)
- The Analysis of Application and Requirements Small Caliber Reference Ammunition and Polish Achievement in the Field of Working Out National Reference Ammunition Archived
- NATO Small Arms Ammunition Interchangeability via Direct Evidence Testing, 25 May 2011 (Archived)
- Pressure and accuracy test barrels for ammunition testing to SAAMI, CIP or NATO standard Archived