Shielded cable
A shielded cable or screened cable is an electrical cable that has a common conductive layer around its conductors for electromagnetic shielding.[1] This shield is usually covered by an outermost layer of the cable. Common types of cable shielding can most broadly be categorized as foil type (hereunder: metallised film), contraspiralling wire strands (braided or unbraided) or both.[2] A longitudinal wire may be necessary with dielectric spiral foils to short out each turn.[1]
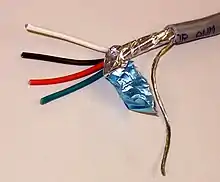

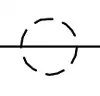
The shield acts as a Faraday cage – a surface that reflects electromagnetic radiation. This reduces both the interference from outside noise onto the signals and the signals from radiating out and potentially disturbing other devices (see electromagnetic compatibility). To be effective against electric fields (see also capacitive coupling), the shield must be grounded.[3] The shield should be electrically continuous to maximize effectiveness, including any cable splices. For high frequency signals (above a few megahertz), this extends to connectors and enclosures, also circumferentially: The cable shielding needs to be circumferentially connected to the enclosure, if any, through the connector or cable gland.[1][4][5]
Some types of shielded cable use the shield as the return path for the signal. As contrasting examples, coaxial cable does, whereas twinax cable does not.
High voltage power cables with solid insulation are shielded to protect the cable insulation, people and equipment.
Types
There are many types of cable shields available commercially, and usage depends on the application.
- Combination shields
- Foil shields
- Metallic braid shields
- Spiral shields
- Serve shields
- Tape shields
- Screen shields
Applications
The use of shielded cables in security systems provides some protection from power frequency and radio frequency interference, reducing the number of false alarms being generated. The best practice is to keep data or signal cables physically separated by at least 3 inches (75mm) from 'heavy' power circuits which are in parallel.
Analog signal cable used in professional audio applications is usually shielded twisted pair cable terminated in XLR connectors. The twisted pair carries the signal in a balanced audio configuration. The audio multicore cable laid from the stage to the mixing console is also shielded.
Consumers use screened copper wire with one central conductor in an unbalanced configuration.
In signal cables
The best way to wire shielded cables for screening is to ground the shield at both ends of the cable.[6] Traditionally there existed a rule of thumb to ground only the source end of the shield to avoid ground loops. Best practice is to ground at both ends, but there is a possibility of ground loops. In airplanes, special cable is used with both an outer shield to protect against lightning and an inner shield grounded at one end to eliminate hum from the 400 Hz power system.[7]
In power cables
Medium and high-voltage power cables, in circuits over 2000 volts, usually have a shield layer of copper or aluminium tape or conducting polymer. If an unshielded insulated cable is in contact with earth or a grounded object, the electrostatic field around the conductor will be concentrated at the contact point, resulting in corona discharge, and eventual destruction of the insulation. Leakage current and capacitive current through the insulation presents a danger of electrical shock. The grounded shield equalizes electrical stress around the conductor, diverts any leakage current to ground. Stress relief cones should be applied at the shield ends, especially for cables operating at more than 2 kV to earth.
Shields on power cables may be connected to earth ground at each shield end and at splices for redundancy to prevent shock even though induced current will flow in the shield. This current will produce losses and heating and will reduce the maximum current rating of the circuit. Tests show that having a bare grounding conductor adjacent to the insulated wires will conduct the fault current to earth more quickly. On high-current circuits the shields might be connected only at one end. On very long high-voltage circuits, the shield may be broken into several sections since a long shield run may rise to dangerous voltages during a circuit fault. There is a risk of shock hazard from having only one end of the shield grounded. The maximum recommended shield potential rise is 25 volts. IEEE 422 and 525 lists the cable lengths that would limit shield potential to 25 volts for a single point ground application.[8][9][10]
Size Conductor | One Cable per Duct (ft) | Three Cables per Duct (ft) |
---|---|---|
1/0 AWG | 1250 | 4500 |
2/0 AWG | 1110 | 3970 |
4/0 AWG | 865 | 3000 |
250 kcmil | 815 | 2730 |
350 kcmil | 710 | 2260 |
400 kcmil | 655 | 2100 |
500 kcmil | 580 | 1870 |
750 kcmil | 510 | 1500 |
1000 kcmil | 450 | - |
2000 kcmil | 340 | - |
See also
- Electromagnetic shielding
- Speaker wire
- Door loop, a method for mechanically protecting electric cabling to a door
References
- "EMC techniques in electronic design Part 2 - Cables and Connectors" (PDF). May 2009. Retrieved 2022-04-18.
For good shielding performance, the electrical bonding between a cable's shield and the shields of its connectors or glands and any shielded enclosures should have no gaps in it either. This means that there should be a seamless low-impedance electrical connection all around the perimeter or circumference of the electrical joint. This is often referred to as 360° shield bonding (even when the connector or gland isn't circular), and it applies between a cable shield and connector shield, the shields of two mating connectors and between the shield of a connector and the metal chassis or structure it is mounted on.
- "Popular Shielding Types". 2021. Retrieved 2022-04-18.
- "Shield Grounding". Retrieved 2019-02-28.
- "Introduction to electromagnetic compatibility" (PDF). Analog Devices. May 2009. Retrieved 2022-04-18.
In summary, for protection against low-frequency (<1 MHz) electric-field interference, grounding the shield at one end is acceptable. For high-frequency interference (>1 MHz), the preferred method is grounding the shield at both ends, using 360° circumferential bonds between the shield and the connector, and maintaining metal-to-metal continuity between the connectors and the enclosure.
- "Effectiveness of Shield Termination Techniques Tested with TEM Cell and Bulk Current Injection" (PDF). NASA. 2009. Retrieved 2022-04-18.
Although it has long been known that pigtail shield connections underperform 360° termination methods, our experiments indicated that pigtails were typically worse by more than 35 dB for frequencies above a few MHz.
- "Bonding Cable Shields at Both Ends to Avoid Noise".
- "Aero 10 - Loop Resistance Tester". 090528 boeing.com
- Thomas P. Arnold; C. David Mercier (1997). Southwire Company Power Cable Manual (2 ed.). Carrollton, GA 30119: Southwire Company.
{{cite book}}
: CS1 maint: location (link) - IEEE 422: IEEE Guide for the Design and Installation of Cable Systems in Power Generating Stations
- IEEE 525: IEEE Guide for the Design and Installation of Cable Systems in Substations