Steel belt
Steel belts are a type of conveyor belt used in many industries such as food, chemical, wood processing, and transportation.[1]
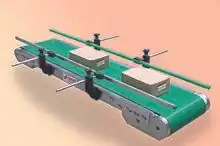
Description
Steel belts are generally made from carbon steel or stainless steel. They are corrosion-resistant, and are used primarily in the chemical, food, rubber, plastic, wood, and laminate industries. Carbon steel belts are energy efficient and especially suitable for applications necessitating radiant heating of products or in high-temperature applications that might exceed the annealing temperatures of less heat-resistant stainless steel belts. Carbon steel belts provide more heat distribution than provided by most stainless steel alloys. Carbon steel belts are used primarily in food processing, transport, and bake ovens. Non-stick surfaces are also commonly used when a non-stick surface is required, as in the laminate industry.[3]
Single and double belt systems
The two main systems using steel belts are single-belt and double-belt systems. Single-belt systems are appropriate for manufacturing single-sided products such as pastilles, flakes, strips, and sheets.[4] The double-belt system can manufacture the top and bottom of a product simultaneously, such as in chemical, rubber, laminate, and composite material processing operations.
Types
Ground
Ground stainless steel belts are normally produced with surface roughness ranging from 0.4 μm down to 0.1 μm, with well-rounded edges, and developed for level and straight contour. Such belts are supplied in open lengths, with the ends prepared for welding on site, or in endless condition with a welded joint.
Perforated
Perforated steel belts enable the drying media, for example hot air, to be transferred 'through' the belt, so that the air is in contact with all parts of the product on the belt. Normally, manufacturers offer perforated belts with five standard perforation patterns which cover most requirements. Other patterns, with a minimum hole diameter of 0.8 mm (0.03 in.) and different spacing, can be provided to suit specific applications.
Polished
Mirror polished stainless-steel belts to produce several types of thin film and ceramic sheets. The belts are available in thickness from 0.60 to 2.00 mm (0.02362 to 0.0787 in.) with thickness variation less than or equal to 80 μm. Polished steel belts are produced endlessly or as open-length belts.
Seamless
Seamless steel belts are suitable to produce of high-quality plastic foils and films such as optical film and packaging film. Thickness normally ranges from 0.03 to 0.60 mm (0.012 to 0.23 in.). Seamless steel belts are suitable for machines with narrow drum diameters using wide belts.
Solid
Solid stainless-steel belts are, as standard, delivered in cold-rolled condition with a mill finish of Ra < 0.4 μm and have rounded edges. Carbon steel belts are, as standard, delivered in a hardened and tempered condition with a mill finish of Ra < 0.4 μm and have rounded edges. Solid steel belts are leveled and straightened to obtain flatness and straightness and are supplied in open lengths, with the ends prepared for welding on site, or in endless condition with a welded joint.
Material
The material is a special grade for carbon or stainless steel specifically designed for use as a steel belt, with the material alloyed or treated to have improved properties such as ductility, strength, thermal conductivity etc. depending on the application.
Sizes
Steel belts are available in a range of sizes ranging typically from 40 cm wide x 0.6 mm thick to around 3,000 mm wide x 3.0 mm thick. There are special applications that may use belts of narrower and thinner or wider and thicker sizes, but these are not common. The length of the belts is typically in the range of 10 m to 100 m long, however it is theoretically possible to produce a belt of unlimited length by joining of shorter belt sections.[5]
Usage
Food industry
Steel belts used in the food business are made to be sanitary, simple to clean, dependable, and flexible in their use. They are employed in the cooking process as well as the drying and steaming of perishables, the freeze-drying of instant coffee, the casting of caramel and other candies, and the formation of chocolate droplets.
Chemical industry
Stainless-steel belts are part of continuous production processes. Unlike conveyor belts used purely for transportation purposes, steel belts used in this industry serve as media for transferring heat and/or pressure. Applications for steel belts in the chemical industry include casting, polymerizing of resins, waxes, paraffins and many other substances.
Transportation
Steel belts may be used to move the finished product or raw material or in parcel sorting systems, transporting of bottles, bulk loads, bricks, machinery parts and the like. Straight tracking, high abrasion resistance, and dynamic fatigue strength are crucial when transporting bulky material or unit load. Extremely high operating speeds cause a high number of load cycles and create severe operating conditions. Steel belts can be made to suit these extreme requirements.
Wood processing
Steel belts play an essential role in modern, continuous production processes for wood-based panels (WBP) such as particle boards, OSB- and MDF boards, where they serve as heat and pressure transfer media at the same time. As the steel belt surface has a direct influence on the final panel surface quality, this application imposes high demands on steel belts regarding thickness uniformity and surface finish.
Advantages and disadvantages
Cost
Compared to a plastic belt, the steel belt is generally more expensive upfront.[6] However, when considering the production price per linear foot, the steel belt proves to be more cost-effective. Additionally, the steel belt has a lower overall cost of process compared to plastic belts since it is not derived from petroleum products. This can lead to long-term savings and sustainability benefits.
Durability
Steel belts offer exceptional durability, making them suitable for applications involving extreme temperatures, vacuum conditions, and mechanical stresses. They are engineered to withstand bending, heating, cooling, and other demanding conditions. Different alloys can be used to enhance the belt's resistance to chemicals, humidity, and corrosion. Engineers typically choose a belt material based on its physical properties, availability, and cost, ensuring durability in various environments.
Maintenance
Maintenance of a steel belt is primarily focused on the steel belt conveyor system. This involves addressing belt tracking problems and replacing spare parts and consumables as needed. Proper maintenance ensures the smooth operation and longevity of the conveyor system, minimizing downtime and optimizing production efficiency.
Ease of Repair
Over time, a steel belt may develop deformations or curvature due to wear and tear. However, these deformations can be rectified through various methods. Shot peening, for example, is a commonly used technique to flatten out the cross curvature of deformed steel belts. This process can be performed quickly and cost-effectively on-site without interrupting production, allowing for efficient repairs and continuous operation.
References
- "Avoid those sticky situations when freezing baked goods | Baking Business".
- "Somefi-belts" (PDF). Somefi-belts.
- "Applications".
- "Steel belt cooler".
- "Reel dimensions".
- "Metal vs Plastic Belts". I.J. White Systems. Retrieved 2022-07-20.