Carburetor
A carburetor (American English)[1] or carburettor (British English)[2][3] is a device that mixes air and fuel for internal combustion engines in an appropriate air–fuel ratio for combustion.[4] The term is sometimes colloquially shortened to carb in the UK and North America or to carby in Australia.[5]


To carburate or carburete (and thus carburation or carburetion, respectively) means to mix the air and fuel or to equip (an engine) with a carburetor for that purpose.
Fuel injection technology has largely supplanted carburetors in the automotive and, to a lesser extent, aviation industries. Carburetors are still common in small engines for dirt bikes, lawnmowers, and other equipment.
Etymology
The name "carburetor" is derived from the verb carburet, which means "to combine with carbon,"[6] or in particular, "to enrich a gas by combining it with carbon or hydrocarbons."[7] Thus a carburetor mixes intake air with hydrocarbon-based fuel, such as petrol or autogas (LPG).[8]
Operating principle
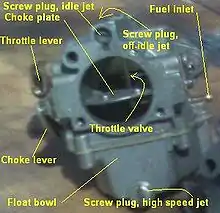
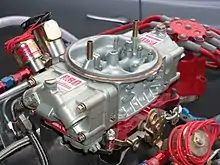
The carburetor is located upstream of the inlet manifold. Air from the atmosphere enters the carburetor (usually via an air cleaner), has fuel added within the carburetor, passes through the inlet valve(s) and then enters the combustion chamber. Most engines use a single carburetor shared between all of the cylinders, however some high-performance engines have used multiple carburetors.
The carburetor works on Bernoulli's principle: the static pressure of the intake air reduces at higher speeds, drawing more fuel into the airstream. In most cases (except for the accelerator pump), the driver pressing the throttle pedal does not directly increase the fuel entering the engine. Instead, the airflow through the carburetor increases, which in turn increases the amount of fuel drawn into the intake mixture.
The main disadvantage of basing a carburetor's operation on Bernoulli's Principle is that being a fluid dynamic device, the pressure reduction in a venturi tends to be proportional to the square of the intake airspeed. The fuel jets are much smaller and fuel flow is limited mainly by the fuel's viscosity so that the fuel flow tends to be proportional to the pressure difference. So jets sized for full power tend to starve the engine at lower speed and part throttle. Most commonly this has been corrected by using multiple jets. In SU and other variable jet carburetors, it was corrected by varying the jet size.
The orientation of the carburetor is a key design consideration. Older engines used updraft carburetors, where the air enters from below the carburetor and exits through the top. From the late 1930s, downdraft carburetors become more commonly used (especially in the United States), along with sidedraft carburetors (especially in Europe).
Fuel circuits
Main metering circuit
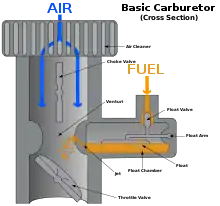
The main metering circuit consists of a pipe which temporarily narrows, forming a venturi. Fuel is introduced into the air stream through small holes (the main jets) at the narrowest part of the venturi, where the air is at its highest speed.
Downstream of the venturi is a throttle (usually in the form of a butterfly valve) which is used to control the amount of air entering the carburettor. In a car, this throttle is connected to the vehicle's throttle pedal, a which (along with the brakes) is the driver's main method of controlling the car's speed.
At greater throttle openings, the speed of air passing through the venturi increases, which lowers the pressure of the air and draws more fuel into the airstream.[9] At the same time, the reduced manifold vacuum results in less fuel flow through the idle and off-idle circuits.
At lesser throttle openings, the air speed through the venturi is insufficient to maintain the fuel flow, therefore the fuel is instead supplied by the carburetor's idle and off-idle circuits.
Choke
When the engine is cold, fuel vaporizes less readily and tends to condense on the walls of the intake manifold, starving the cylinders of fuel and making the engine difficult to start, thus additional fuel is required (for a given amount of air) is required to start and run the engine until it warms up.
A choke is used to supply this extra fuel. While the engine is warming up, a partially closed choke restricts the flow of air at the entrance to the carburetor, which increases the vacuum in the main metering circuit, causing more fuel to be supplied to the engine via the main jets. In older cars, the choke was manually operated by the driver, often using a lever or knob on the dashboard. Automatic chokes became more commonplace from the late 1950s, whereby a thermostat was used to automatically open the choke based on the temperature of the engine's coolant liquid. Leaving the choke closed after the engine has warmed up increases the engine's fuel consumption and exhaust gas emissions.
Another method used by carburetors to improve the operation of a cold engine is a fast idle cam. This cam is connected to the choke and prevents the throttle from closing fully while the choke is in operation. The resulting increase in idle speed provides a more stable idle for a cold engine (by better atomizing the cold fuel) and helps the engine warm up quicker.
Off-idle circuit
As the throttle valve is opened slightly from the fully closed position, the throttle plate uncovers additional fuel delivery holes behind the throttle plate where there is a low-pressure area created by the throttle plate/Valve blocking the airflow; these allow more fuel to flow as well as compensating for the reduced vacuum that occurs when the throttle is opened, thus smoothing the transition to metered fuel flow through the regular open throttle circuit.
Power valve
For open throttle operation, a richer fuel/air mixture will produce more power, prevent pre-ignition detonation, and keep the engine running cooler. This is usually addressed with a spring-loaded "power valve", which is held shut by engine vacuum. As the throttle valve opens up, the manifold vacuum decreases and the spring opens the valve to let more fuel into the main circuit. On two-stroke engines, the operation of the power valve is the reverse of normal — it is normally "on" and at a set rpm it is turned "off". It is activated at high rpm to extend the engine's rev range, capitalizing on a two-stroke's tendency to rev higher momentarily when the mixture is lean.
Alternately to employing a power valve, the carburetor may utilize a metering rod or step-up rod system to enrich the fuel mixture under high-demand conditions. Such systems were originated by Carter Carburetor in the 1950s for the primary two venturis of their four-barrel carburetors, and step-up rods were widely used on most 1-, 2-, and 4-barrel Carter carburetors through the end of production in the 1980s. The step-up rods are tapered at the bottom end, which extends into the main metering jets. The tops of the rods are connected to a vacuum piston or a mechanical linkage which lifts the rods out of the main jets when the throttle is opened (mechanical linkage) or when manifold vacuum drops (vacuum piston). When the step-up rod is lowered into the main jet, it restricts the fuel flow. When the step-up rod is raised out of the jet, more fuel can flow through it. In this manner, the amount of fuel delivered is tailored to the transient demands of the engine. Some 4-barrel carburetors use metering rods only on the primary two venturis, but some use them on both primary and secondary circuits, as in the Rochester Quadrajet.
Accelerator pump
Liquid gasoline, being denser than air, is slower than air to react to a force applied to it. When the throttle is rapidly opened, airflow through the carburetor increases immediately, faster than the fuel flow rate can increase. Also, the air pressure in the manifold increases, decreasing the evaporation of the fuel, so less fuel vapor is drawn into the engine. This transient oversupply of air relative to the fuel causes a lean mixture, which makes the engine misfire (or "stumble")—an effect opposite to that which was demanded by opening the throttle. This is remedied by the use of a small piston or diaphragm pump which, when actuated by the throttle linkage, forces a small amount of gasoline through a jet into the carburetor throat.[10] This extra shot of fuel counteracts the transient lean condition on throttle tip-in. Most accelerator pumps are adjustable for volume or duration by some means. Eventually, the seals around the moving parts of the pump wear such that the pump output is reduced; this reduction of the accelerator pump shot causes stumbling under acceleration until the seals on the pump are renewed.
The accelerator pump can also be used to prime the engine with fuel prior to a cold start. Excessive priming, like an improperly adjusted choke, can cause flooding. This is when too much fuel and not enough air are present to support combustion. For this reason, most carburetors are equipped with an unloader mechanism: The accelerator is held at wide-open throttle while the engine is cranked, the unloader holds the choke open and admits extra air, and eventually, the excess fuel is cleared out and the engine starts.
Icing and carburetor heat mechanisms
Although this is rarely a concern for land-based applications, a critical property of carburetors in aviation is the pronounced temperature drop in the throttle body at the fuel vaporisation point. This is inherent to the operating principle of a venturi-based carburetor: since the air at the narrow part of the venturi has a lower pressure, it will also experience a drop in temperature. Furthermore, since the fuel is also vaporising at that point, its latent heat of evaporation will cause further temperature drop. This can result in a combined temperature drop by as much as 40 °C (104 °F),[11] meaning that even on a hot, 35 °C day, the temperatures at the venturi might be below freezing. If the air contains sufficient moisture, this will result in ice build-up at the venturi throat, and might eventually result in a complete blockage of the air supply and the engine quitting entirely.
Aviation applications are uniquely susceptible to carburetor icing, owing to a particular mode of operation not found in other engines: during descent to landing, the engine is run at idle for prolonged periods of time. Since the throttle valve is maximally constricted at idle RPM, the pressure (and consequently, also the temperature) drop is greatest, all the while the engine is not producing any useful power, so its overall temperature is also dropping. This creates the perfect conditions for carburetor icing, and a significant hazard of complete engine power loss. Carburetor icing can also occur in cruise conditions at altitude, if the aircraft is flying at altitudes and in atmospheric conditions favourable to icing. To counteract carburetor icing, aircraft employing carburetor engines are equipped with a carburetor heat system.[11] The carburetor heat (or "carb heat" in common parlance) system consists of a pilot-operated bypass valve, which can be opened to redirect the engine air supply from the normal air intake through the air filter, to a secondary (normally unfiltered) intake duct that passes around the engine exhaust. This heats the incoming air enough to prevent icing.
If carburetor icing conditions are detected or suspected, immediate pilot action is required to engage the carb heat system until all ice build-up has been eliminated. If the engine is operating at idle RPM, periodically opening the throttle might also be necessary to ensure sufficient temperatures are maintained to prevent ice formation.[11]
Because the use of carb heat causes power reduction (owing to the lower density of heated air), and typically causes the air ingested to be unfiltered, it is not applied when maximum power is needed (such as on takeoff), or when no icing potential exists. Its use however is a part of standard operating procedure during descent in carbureted piston-engine aircraft.[11]
Other elements
The interactions between each circuit may also be affected by various mechanical or air pressure connections and also by temperature-sensitive and electrical components. These are introduced for reasons such as engine responsiveness, fuel efficiency or automobile emissions control. Various air bleeds (often chosen from a precisely calibrated range, similarly to the jets) allow air into various portions of the fuel passages to enhance fuel delivery and vaporization. Extra refinements may be included in the carburetor/manifold combination, such as some form of heating to aid fuel vaporization such as an early fuel evaporator.
When carburetors are used in aircraft engines, special designs and features are needed to prevent fuel starvation during inverted flight.
Fuel supply
Float chamber

To ensure a ready mixture, the carburetor has a "float chamber" (or "bowl") that contains a quantity of fuel at near-atmospheric pressure, ready for use. This reservoir is constantly replenished with fuel supplied by a fuel pump. The correct fuel level in the bowl is maintained by means of a float controlling an inlet valve, in a manner very similar to that employed in a cistern (e.g. a toilet tank). As fuel is used up, the float drops, opening the inlet valve and admitting fuel. As the fuel level rises, the float rises and closes the inlet valve. The level of fuel maintained in the float bowl can usually be adjusted, whether by a setscrew or by something crude such as bending the arm to which the float is connected. This is usually a critical adjustment, and the proper adjustment is indicated by lines inscribed into a window on the float bowl, or a measurement of how far the float hangs below the top of the carburetor when disassembled, or similar. Floats can be made of different materials, such as sheet brass soldered into a hollow shape, or of plastic; hollow floats can spring small leaks and plastic floats can eventually become porous and lose their flotation; in either case, the float will fail to float, fuel level will be too high, and the engine will not run unless the float is replaced. The valve itself becomes worn on its sides by its motion in its "seat" and will eventually try to close at an angle, and thus fails to shut off the fuel completely; again, this will cause excessive fuel flow and poor engine operation. Conversely, as the fuel evaporates from the float bowl, it leaves sediment, residue, and varnishes behind, which clog the passages and can interfere with the float operation. This is particularly a problem in automobiles operated for only part of the year and left to stand with full float chambers for months at a time; commercial fuel stabilizer additives are available that reduce this problem.
The fuel stored in the chamber (bowl) can be a problem in hot climates. If the engine is shut off while hot, the temperature of the fuel will increase, sometimes boiling ("percolation"). This can result in flooding and difficult or impossible restarts while the engine is still warm, a phenomenon known as "heat soak". Heat deflectors and insulating gaskets attempt to minimize this effect. The Carter Thermo-Quad carburetor has float chambers manufactured of insulating plastic (phenolic), said to keep the fuel 20 degrees Fahrenheit (11 degrees Celsius) cooler.
Usually, special vent tubes allow atmospheric pressure to be maintained in the float chamber as the fuel level changes; these tubes usually extend into the carburetor throat. Placement of these vent tubes is critical to prevent fuel from sloshing out of them into the carburetor, and sometimes they are modified with longer tubing. Note that this leaves the fuel at atmospheric pressure, and therefore it cannot travel into a throat that has been pressurized by a supercharger mounted upstream; in such cases, the entire carburetor must be contained in an airtight pressurized box to operate. This is not necessary for installations where the carburetor is mounted upstream of the supercharger, which is for this reason the more frequent system. However, this results in the supercharger being filled with compressed fuel/air mixture, with a strong tendency to explode should the engine backfire; this type of explosion is frequently seen in drag races, which for safety reasons now incorporate pressure releasing blow-off plates on the intake manifold, breakaway bolts holding the supercharger to the manifold, and shrapnel-catching ballistic blankets made from nylon or kevlar surrounding the superchargers.
Diaphragm chamber
If the engine must be operated in any orientation (for example a chain saw or a model airplane), a float chamber is not suitable. Instead, a diaphragm chamber is used. A flexible diaphragm forms one side of the fuel chamber and is arranged so that as fuel is drawn out into the engine, the diaphragm is forced inward by ambient air pressure. The diaphragm is connected to the needle valve and as it moves inward it opens the needle valve to admit more fuel, thus replenishing the fuel as it is consumed. As fuel is replenished the diaphragm moves out due to fuel pressure and a small spring, closing the needle valve. A balanced state is reached which creates a steady fuel reservoir level, which remains constant in any orientation.
2-barrel and 4-barrel carburetors
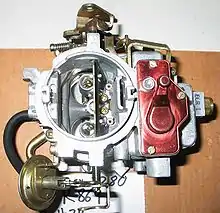

.JPG.webp)
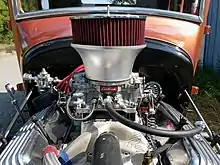
While basic carburetors have only one venturi, many carburetors have more than one venturi, or "barrel". Two barrel and four-barrel configurations are commonly used to accommodate the higher airflow rate with large engine displacement. Multi-barrel carburetors can have non-identical primary and secondary barrel(s) of different sizes and calibrated to deliver different air/fuel mixtures; they can be actuated by the linkage or by engine vacuum in "progressive" fashion, so that the secondary barrels do not begin to open until the primaries are almost completely open. This is a desirable characteristic that maximizes airflow through the primary barrel(s) at most engine speeds, thereby maximizing the pressure "signal" from the venturis, but reduces the restriction in airflow at high speeds by adding cross-sectional area for greater airflow. These advantages may not be important in high-performance applications where part throttle operation is irrelevant, and the primaries and secondaries may all open at once, for simplicity and reliability; also, V-configuration engines, with two cylinder banks fed by a single carburetor, may be configured with two identical barrels, each supplying one cylinder bank. In the widely seen V8 engine and 4-barrel carburetor combination, there are often two primary and two secondary barrels.
The first four-barrel carburetors, with two primary bores and two secondary bores, were the Carter WCFB and identical Rochester 4GC simultaneously introduced on the 1952 Cadillac Series 62, Oldsmobile 98, Oldsmobile Super 88 and Buick Roadmaster. Oldsmobile referred the new carburetor as the “Quadri-Jet” (original spelling)[12] while Buick called it the “Airpower”.[13]
The spread-bore four-barrel carburetor, first released by Rochester in the 1965 model year as the "Quadrajet" has a much greater spread between the sizes of the primary and secondary throttle bores. The primaries in such a carburetor are quite small relative to conventional four-barrel practice, while the secondaries are quite large. The small primaries aid low-speed fuel economy and driveability, while the large secondaries permit maximum performance when it is called for. To tailor airflow through the secondary venturis, each of the secondary throats has an air valve at the top. This is configured much like a choke plate and is lightly spring-loaded into the closed position. The air valve opens progressively in response to engine speed and throttle opening, gradually allowing more air to flow through the secondary side of the carburetor. Typically, the air valve is linked to metering rods which are raised as the air valve opens, thereby adjusting secondary fuel flow.
Multiple carburetors can be mounted on a single-engine, often with progressive linkages; two four-barrel carburetors (often referred to as "dual-quads") were frequently seen on high-performance American V8s, and multiple two barrel carburetors are often now seen on very high-performance engines. Large numbers of small carburetors have also been used (see photo), though this configuration can limit the maximum airflow through the engine due to the lack of a common plenum; with individual intake tracts, not all cylinders are drawing air at once as the engine's crankshaft rotates.[14]
History
In 1826, American engineer Samuel Morey received a patent for a "gas or vapour engine" which used a heated-surface carburetor to mix the turpentine fuel with air,[15][16] however the design did not reach production. In 1875, Jewish engineer Siegfried Marcus produced a car powered by the first petrol engine to use a carburetor (along with the first magneto ignition system).[17][18][19] Karl Benz's Benz Patent-Motorwagen, built in 1885, also used a carburetor.[20][21]
The aforementioned carburetors were all "surface curburetors", which operate moving air across the top of a vessel containing the fuel.[22] However, the 1885 'Grandfather Clock' engine created by German engineers Wilhelm Maybach and Gottlieb Daimler introduced the float-fed carburetor design, which used an atomizer nozzle.[23] The Butler Petrol Cycle car - built in England in 1888 - also used a float-fed carburetor.[24][25]
The first carburetor for a stationary engine was patented in 1893 by Hungarian engineers János Csonka and Donát Bánki.[26][27][28]
Carburetors were the common method of fuel delivery for most US-made gasoline engines until the late 1980s when fuel injection became the preferred method.[29] Once of the last motorsport uses of carburetors was NASCAR, which switched to electronic fuel injection after the 2011 Sprint Cup series.[30]
In Europe, carburetor-engined cars were being gradually phased out by the end of the 1980s in favor of fuel injection, which was already the established type of engine on more expensive vehicles including luxury and sports models. EEC legislation required all vehicles sold and produced in member countries to have a catalytic converter after December 1992. This legislation had been in the pipeline for some time, with many cars becoming available with catalytic converters or fuel injection from around 1990.
Carburetor adjustment
The fuel and air mixture is too rich when it has an excess of fuel, and too lean when there is not enough. The mixture is adjusted by one or more needle valves on an automotive carburetor, or a pilot-operated lever on piston-engined aircraft (since the mixture changes with air density and therefore altitude). Independent of air density the (stoichiometric) air to gasoline ratio is 14.7:1, meaning that for each mass unit of gasoline, 14.7 mass units of air are required. There are different stoichiometric ratios for other types of fuel.
Ways to check carburetor mixture adjustment include: measuring the carbon monoxide, hydrocarbon, and oxygen content of the exhaust using a gas analyzer, or directly viewing the color of the flame in the combustion chamber through a special glass-bodied spark plug sold under the name "Colortune"; the flame color of stoichiometric burning is described as a "Bunsen blue", turning to yellow if the mixture is rich and whitish-blue if too lean. Another method, widely used in aviation, is to measure the exhaust gas temperature, which is close to the maximum for an optimally adjusted mixture and drops off steeply when the mixture is either too rich or too lean.
The mixture can also be judged by removing and scrutinizing the spark plugs. Black, dry, sooty plugs indicate a mixture too rich; white or light gray plugs indicate a lean mixture. A proper mixture is indicated by brownish-gray/straw-colored plugs.
On high-performance two-stroke engines, the fuel mixture can also be judged by observing piston wash. Piston wash is the color and amount of carbon buildup on the top (dome) of the piston. Lean engines will have a piston dome covered in black carbon, and rich engines will have a clean piston dome that appears new and free of carbon buildup. This is often the opposite of intuition, but is caused by incomplete combustion stemming from poor fuel-air mixing in lean engines. Commonly, an ideal mixture will be somewhere in-between the two, with clean dome areas near the transfer ports but some carbon in the center of the dome.
When tuning two-strokes It is important to operate the engine at the rpm and throttle input that it will most often be operated at. This will typically be wide-open or close to wide-open throttle. Lower RPM and idle can operate rich/lean and sway readings, due to the design of carburetors to operate well at high air-speed through the venturi and sacrifice low air-speed performance.[31]
Where multiple carburetors are used the mechanical linkage of their throttles must be properly synchronized for smooth engine running and consistent fuel/air mixtures to each cylinder.
Feedback carburetors
In the 1980s, many American-market vehicles used "feedback" carburetors that dynamically adjusted the fuel/air mixture in response to signals from an exhaust gas oxygen sensor to provide a stoichiometric ratio to enable the optimal function of the catalytic converter. Feedback carburetors were mainly used because they were less expensive than fuel injection systems; they worked well enough to meet the 1980s emissions requirements and were based on existing carburetor designs. Frequently, feedback carburetors were used in lower-trim versions of a car (whereas higher specification versions were equipped with fuel injection). However, their complexity compared to both non-feedback carburetors and to fuel injection made them problematic and difficult to service. Eventually falling hardware prices and tighter emissions standards caused fuel injection to supplant carburetors in new-vehicle production.
Constant vacuum carburetors
Constant vacuum carburetors, also called variable choke carburetors and constant velocity carburetors, are carburetors where the throttle cable was connected directly to the throttle cable plate. Pulling the cord caused raw gasoline to enter the carburetor, creating a large emission of hydrocarbons.[32]
The Constant Velocity carburetor has a variable throttle closure in the intake air stream before the accelerator pedal operated the throttle plate. This variable closure is controlled by intake manifold pressure/vacuum. This pressure-controlled throttle provides relatively even intake pressure throughout the engine's speed and load ranges. The most common design of the CV carburetor would be that of the SU or Solex, among others, which use a cylindrical closure that is operated by a diaphragm. The cylinder and diaphragm are connected together with the fuel metering rod to provide fuel in direct relation to airflow. To provide a more smooth operation and more even intake pressure, the diaphragm is viscous dampened. These carburetors allowed for very good drivability and fuel efficiency. They are also widely adjustable for best performance and efficiency. (See variable venturi carburetors above)
Drawbacks of the CV carburetor include that it is limited to a single barrel, side draft design. This limited its use to mostly inline engines and also made it impractical for large displacement engines. The throttle linkage required to install 2 or more CV carbs on an engine is complex and proper adjustment is critical for even air/fuel distribution. This makes maintenance and tuning difficult.
Vaporizers
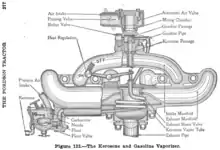
Internal combustion engines can be configured to run on many kinds of fuel, including gasoline, kerosene, tractor vaporizing oil (TVO), vegetable oil, diesel fuel, biodiesel, ethanol fuel (alcohol), and others. Multifuel engines, such as petrol-paraffin engines, can benefit from an initial vaporization of the fuel when they are running less volatile fuels. For this purpose, a vaporizer (or vaporiser) is placed in the intake system. The vaporizer uses heat from the exhaust manifold to vaporize the fuel. For example, the original Fordson tractor and various subsequent Fordson models had vaporizers. When Henry Ford & Son Inc designed the original Fordson (1916), the vaporizer was used to provide for kerosene operation. When TVO became common in various countries (including the United Kingdom and Australia) in the 1940s and 1950s, the standard vaporizers on Fordson models were equally useful for TVO. Widespread adoption of diesel engines in tractors made the use of tractor vaporizing oil obsolete.
See also
- List of carburetor manufacturers
- Humidifier
- Venturi effect
- Edelbrock
References
- "Definition of 'carburetor'". merriam-webster.com. merriam-webster. Retrieved 2020-09-11.
- "carburettor". dictionary.cambridge.org. Cambridge University Press. Retrieved 2020-09-11.
- "carburettor". oxfordlearnersdictionaries.com. Oxford University Press. Retrieved 2020-09-11.
- "What Is a Carburetor?". stateofspeed.com. 2018-11-05. Retrieved 2022-02-03.
- Beale, Paul; Partridge, Eric (2003), Shorter Slang Dictionary, Routledge, p. 60, ISBN 9781134879519
- "carburetor". www.etymonline.com. Retrieved 22 October 2022.
- "How does a carburetor work?". Explain that Stuff. 23 October 2009. Retrieved 22 October 2022.
- "Carburetors Explained". autoevolution. 1 August 2014. Retrieved 22 October 2022.
- "Carburetor Basics - Tech Article - Chevy High Performance Magazine". MotorTrend. 1 June 2002. Retrieved 28 October 2022.
- Hillier, V.A.W.; Pittuck, F.W. (1966). "Section 3.6". Fundamentals of Motor Vehicle Technology (Second ed.). Hutchinson Educational. ISBN 9780091107116.
- Pilots' Handbook of Aeronautical Knowledge (PDF). US Federal Aviation Administration. pp. 7–9–7–10. Retrieved 11 April 2022.
- "1952 Oldsmobile prestige brochure" (PDF). wildaboutcarsonline.com. Archived from the original (PDF) on 2016-03-04. Retrieved 2016-05-09.
- "1952 Buick Airpower folder". Oldcarbrochures.com. Retrieved 2016-05-09.
- Hibbard, Jeff (1983). Baja Bugs & Buggies. HP Books. p. 24. ISBN 0-89586-186-0.
- "Samuel Morey". The Linda Hall Library. Retrieved 22 October 2022.
- "A Detailed History Of The Internal Combustion Engine". HotCars. 22 April 2021. Retrieved 22 October 2022.
- "Siegfried Marcus Car". www.asme.org. Retrieved 22 October 2022.
- "Siegfried Marcus Car". www.inventionandtech.com. Retrieved 22 October 2022.
- "HHF Factpaper: Siegfried Marcus - An Uncredited Inventive Genius". hebrewhistory.info. Retrieved 22 October 2022.
- "Carbueetoe". Google.com. Retrieved 8 October 2017.
- Inventors and Inventions. Marshall Cavendish. 2008. p. 91. ISBN 9780761477617. Retrieved 19 January 2014.
- Webster's Revised Unabridged Dictionary, 1913
- Eckermann, Erik (2001). World History of the Automobile. Society of Automotive Engineers. p. 276. ISBN 978-0-7680-0800-5.
- "Csonka János Emlékmúzeum - The pulverized (spray carburetor)". csonkamuzeum.hu. 2011. Retrieved 2 November 2020.
- Carlisle, Rodney (2005), Scientific American Inventions and Discoveries: All the Milestones in Ingenuity—From the Discovery of Fire to the Invention of the Microwave Oven, John Wiley & Sons, p. 335, ISBN 9780471660248, retrieved July 27, 2014
- Rigden, John S.; Stuewer, Roger H. (2009). The Physical Tourist: A Science Guide for the Traveler. Springer. ISBN 978-3-7643-8933-8.
- "Donát Bánki". Scitech.mtesz.hu. Archived from the original on 17 July 2012. Retrieved 19 January 2014.
- "Inspirator and Pulverizer".
- Eckermann, Erik (2001). World History of the Automobile. Society of Automotive Engineers. pp. 199–200. ISBN 9780768008005. Retrieved 2016-05-09.
- Aumann, Mark (11 January 2012). "NASCAR takes 'really big step' with fuel injection". Nascar.com. Archived from the original on 25 October 2012. Retrieved 19 January 2014.
- Carburetor#Principles
- Stermer, Bill (2002). Harley-Davidson Motorcycles. MotorBooks International. p. 154. ISBN 978-1-61060-951-7.
External links

- General information
- Packer, Ed (July 1953). "Know Your Carburetor – what it is, what it does". Popular Mechanics. 100 (1): 181–184.
- American Technical Society. (1921). Automobile engineering; A general reference work. Chicago: American technical society.
- Lind, W. L. (1920). Internal-combustion engines; Their principles and applications to automobile, aircraft, and marine purposes. Boston: Ginn.
- Hutton, F. R. (1908). The gas-engine. A treatise on the internal-combustion engine using gas, gasoline, kerosene, alcohol, or other hydrocarbon as source of energy. New York: Wiley.
- Patents
- U.S. Patent 610,040 — Carburetor — Henry Ford
- U.S. Patent 1,204,901 — Carburetor Antoine Prosper Plaut
- U.S. Patent 1,750,354 — Carburetor — Charles Nelson Pogue
- U.S. Patent 1,938,497 — Carburetor — Charles Nelson Pogue
- U.S. Patent 1,997,497 — Carburetor — Charles Nelson Pogue
- U.S. Patent 2,026,798 — Carburetor — Charles Nelson Pogue
- U.S. Patent 2,214,273 — Carburetor — J. R. Fish
- U.S. Patent 2,982,528 — Vapor fuel system — Robert S. Shelton
- U.S. Patent 4,177,779 — Fuel economy system for an internal combustion engine — Thomas H. W.
- G.B. Рatent 11119 — Mixing chamber — Donát Bánki