Duraluminio
El duraluminio es una aleación de aluminio con cobre, manganeso, magnesio y silicio. Pertenecen a la familia de las aleaciones aluminio-cobre (1998).[1]
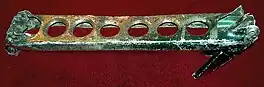
Contrariamente a lo que pudiera parecer, el nombre de duraluminio, no procede de "aluminio duro", sino de Düren, la ciudad alemana en la que Alfred Wilm fabricó dicha aleación por vez primera en 1909.[2]
Hoy en día, el término se refiere principalmente a las aleaciones de aluminio y cobre, designadas como la serie 2000 por el Sistema Internacional de Designación de Aleaciones (IADS), al igual que las aleaciones 2014 y 2024 utilizadas en la fabricación de fuselajes.
Presenta una elevada resistencia mecánica a temperatura ambiente, pero su resistencia a la corrosión, soldabilidad y aptitud para el anodizado son bajas. Se utilizan en la industria aeronáutica y la del automóvil. Tiene un límite elástico de unos 450 MPa, valor que varía según la composición y el temple.[1]
Descubrimiento
En 1906 el alemán Alfred Wilm desarrolló la primera aleación forjada exclusivamente como parte de las investigaciones para aumentar la resistencia de las aleaciones de aluminio.[3] Su descubrimiento fue aumentar la dureza de la aleación transfiriendo los métodos utilizados en la producción de acero para aumentar la resistencia a una aleación de aluminio. Se descubrió que las muestras de aleación que se dejaron unos días después del enfriamiento mostraron una mayor resistencia. El principio subyacente se conoce como endurecimiento por precipitación.
El nuevo material fue fabricado por la metalurgia Düren a partir de 1909 y el nombre Duralumin y algunos similares (DURAL) están protegidos como marcas registradas. La aleación de aluminio de Wilm, de 3,5 a 5,5 por ciento de cobre, de 0,5 a 0,8 por ciento de magnesio y 0,6 por ciento de manganeso, así como hasta un 1 por ciento de silicio y un 1,2 por ciento de hierro también se ha registrado para una patente. El nombre se deriva del latín durus para "duro" (o mejor: "perseverante" en el sentido de constante, resistente), aunque en la literatura existe una conexión ocasional con el lugar de trabajo Düren así como el componente principal de la aleación de aluminio. En la actualidad, existen numerosas aleaciones comparables que han agregado el nombre del fabricante a la designación de la aleación.
Historia
El duraluminio fue desarrollado por el metalúrgico alemán Alfred Wilm en Dürener Metallwerke AG. En 1903, Wilm descubrió que, tras el temple, una aleación de aluminio con un 4% de cobre se endurecía si se dejaba a temperatura ambiente durante varios días. Otras mejoras condujeron a la introducción del duraluminio en 1909.[4] El nombre se utiliza principalmente en pop-science para describir todas las aleaciones Al-Cu del sistema, o serie "2000", designadas mediante el sistema internacional de designación de aleaciones creado originalmente en 1970 por la Aluminum Association.

Composición
Además del aluminio, los principales materiales del duraluminio son el cobre, el manganeso y el magnesio. Por ejemplo, el duraluminio 2024 está compuesto por un 91-95% de aluminio, un 3,8-4,9% de cobre, un 1,2-1,8% de magnesio, un 0,3-0,9% de manganeso, <0,5% de hierro, <0,5% de silicio, <0,25% de zinc, <0,15% de titanio, <0,10% de cromo y no más de un 0,15% de otros elementos juntos.[5] Aunque la adición de cobre mejora la resistencia, también hace que estas aleaciones sean susceptibles a la corrosión. La resistencia a la corrosión puede mejorarse en gran medida mediante la unión metalúrgica de una capa superficial de aluminio de gran pureza, denominada alclad-duralum. Los materiales alclad se utilizan habitualmente en la industria aeronáutica hasta nuestros días.[6][7]
Protección contra la corrosión
Aunque la adición de cobre mejora la resistencia, también hace que estas aleaciones sean susceptibles a la corrosión . Para los productos en láminas, la resistencia a la corrosión se puede mejorar considerablemente mediante la unión metalúrgica de una capa de superficie de aluminio de alta pureza. Estas láminas se denominan alclad y se utilizan comúnmente en la industria aeronáutica.[8][9]
Usos y aplicaciones
El aluminio aleado con cobre (aleaciones Al-Cu), que se puede endurecer por precipitación, está designado por el Sistema Internacional de Designación de Aleaciones como la serie 2000. Es una aleación de las más usadas, dentro de los aluminios, que permite aplicaciones hasta entonces reservadas a los aceros, los usos típicos de las aleaciones de Al-Cu forjadas incluyen:[1]
- Tornillería.
- Automoción.
- Moldes de soplado.
- Mosquetones.
- Estampaciones.
- Utensilios.
Usos en la aviación

.jpg.webp)
Debido a las propiedades mejoradas del material, el reemplazo del acero por una aleación de aluminio en la tecnología de aviación y armas se volvió significativo en primer lugar. Las aleaciones anteriores, como las aleaciones de zinc- aluminio, eran significativamente más susceptibles a la corrosión bajo tensión y no alcanzaban ni mucho menos la resistencia requerida.[10][11]
El primer avión de producción en masa que hizo un uso extensivo de duraluminio, el sesquiplano blindado Junkers JI de la Primera Guerra Mundial La literatura científica alemana publicó abiertamente información sobre el duraluminio, su composición y tratamiento térmico, antes del estallido de la Primera Guerra Mundial en 1914. A pesar de esto, el uso de la aleación fuera de Alemania no se produjo hasta después de que terminaron los combates en 1918. Informes de uso alemán durante la Primera Guerra Mundial, incluso en revistas técnicas como Flight, aún podría identificar erróneamente su componente clave de aleación como magnesio en lugar de cobre.[12] Los ingenieros del Reino Unido mostraron poco interés en el duraluminio hasta después de la guerra.[13]
El primer intento conocido de usar duraluminio para una estructura de aeronave más pesada que el aire ocurrió en 1916, cuando Hugo Junkers introdujo por primera vez su uso en la estructura del avión Junkers J 3 un "demostrador de tecnología" monoplano monomotor que marcó el primer uso del revestimiento ondulado de duraluminio de la marca Junkers. La compañía Junkers completó solo las alas cubiertas y el armazón del fuselaje tubular del J 3 antes de abandonar su desarrollo. El sesquiplano blindado Junkers J.I un poco más tarde, designado únicamente por IdFlieg de 1917, conocido en la fábrica como Junkers J 4, tenía sus alas totalmente metálicas y su estabilizador horizontal fabricado de la misma manera que las alas del J 3, como el caza monoplaza Junkers J 7 de duraluminio experimental y en condiciones de volar diseño, que llevó al caza monoplano de ala baja Junkers D.I, introduciendo tecnología estructural de aeronaves totalmente de duraluminio a la aviación militar alemana en 1918.
Su primer uso en fuselajes aerostáticos se produjo en marcos rígidos de dirigibles , que finalmente incluyeron todos los de la era del "Gran dirigible" de las décadas de 1920 y 1930: el R-100 de fabricación británica, el Zeppelins de pasajeros alemán Graf Zeppelin LZ 127 , LZ 129 Hindenburg, LZ 130 Graf Zeppelin, y los dirigibles de la Armada de los Estados Unidos USS Los Angeles (ZR-3) , USS Akron (ZRS-4) y USS Macon (ZRS-5).[10] [11]
Usos en el ciclismo
El duraluminio se utilizó para fabricar componentes y cuadros de bicicletas desde la década de 1930 hasta la de 1990. Varias empresas de Saint-Étienne, Francia, se destacaron por su adopción temprana e innovadora del duraluminio: en 1932, Verot et Perrin desarrollaron las primeras bielas de aleación ligera; en 1934, Haubtmann lanzó un juego de bielas completo; a partir de 1935, varias empresas fabricaban ruedas libres, desviadores, pedales, frenos y manillares de duraluminio.
Rápidamente siguieron conjuntos de cuadros completos, incluidos los fabricados por: Mercier (y Aviac y otros licenciatarios) con su popular familia de modelos Meca Dural, los hermanos Pelissier y sus modelos La Perle dignos de una carrera, y Nicolas Barra y sus exquisitas creaciones de mitad del siglo XX. Otros nombres que surgen aquí también fueron: Pierre Caminade, con sus hermosas creaciones Caminargent y su exótica tubería octogonal, y también Gnome et Rhône, con su profunda herencia como fabricante de motores de aviación que también se diversificó en motocicletas, velomotores y bicicletas después de la Segunda Guerra Mundial.[14]
Mitsubishi Heavy Industries, a la que se le prohibió producir aviones durante la ocupación estadounidense de Japón, fabricó la bicicleta de "cross" con duraluminio sobrante de la guerra en 1946. La "cross" fue diseñada por Kiro Honjo, un ex diseñador de aeronaves responsable del Mitsubishi G4M.[14]
El uso de duraluminio en la fabricación de bicicletas desapareció en las décadas de 1970 y 1980. No obstante, la empresa de bicicletas Vitus lanzó el venerable cuadro “979” en 1979, un modelo “Duralinox” que se convirtió en un clásico instantáneo entre los ciclistas. El Vitus 979 fue el primer conjunto de marcos de aluminio de producción cuyo tubo 5083/5086 de pared delgada se deslizaba y luego se pegaba con un epoxi seco activado por calor. El resultado fue un cuadro extremadamente ligero pero muy duradero. La producción del Vitus 979 continuó hasta 1992.[15]
Otros usos
Antes del tratamiento térmico, la aleación es dúctil y maleable. Después del tratamiento térmico, una reacción entre el aluminio y el magnesio provoca un aumento de la dureza y la resistencia a la tracción.[1]
El duraluminio tiene una alta resistencia mecánica a temperatura ambiente, sin embargo, su resistencia a la oxidación, soldabilidad e idoneidad para anodizar son bajas. Se utilizan en la industria aeronáutica y automovilística.
- 2011 : Alambre, varilla y barra para productos de máquina de tornillos. Aplicaciones donde se requiere buena maquinabilidad y buena resistencia.
- 2014 : Piezas forjadas , placas y extrusiones deservicio pesadopara accesorios de aeronaves, ruedas y componentes estructurales principales, tanque y estructura de refuerzo espacial, bastidor de camión y componentes de suspensión. Aplicaciones que requieren alta resistencia y dureza, incluido el servicio a temperaturas elevadas.
- 2017 o Avional (Francia): Alrededor del 1% Si.[16] Buena maquinabilidad. Resistencia aceptable a la corrosión en el aire y propiedades mecánicas. También se llama AU4G en Francia. Utilizado para aplicaciones de aviones entre las guerras en Francia e Italia.[17] También se usó en aplicaciones de carreras de motor a partir de la década de 1960,[18] ya que es una aleación tolerante que podría moldearse a presión con equipo relativamente poco sofisticado.
- 2024 : Estructuras de aeronaves, remaches, herrajes, ruedas de camiones, productos de máquinas de tornillos y otras aplicaciones estructurales.
- 2036 : Chapa para paneles de carrocería.
- 2048 : Chapa y placa en componentes estructurales para aplicaciones aeroespaciales y equipos militares.
Nota: Los números indican la aleación de Duraluminio, las distintas series pueden diferenciarse por los aleantes que poseen, la proporción de los mismos, y los tratamientos térmicos o de otros tipos usados en su obtención.
Principales propiedades
Aleación de muy altas características y resistencia a la tracción, muy elevada resistencia mecánica a temperatura ambiente,[1] sin embargo, su resistencia a la corrosión, soldabilidad y aptitud para el anodizado son bajas. Se emplean en la industria aeronáutica[19] y de automoción.
- Buena mecanización.
- Poca resistencia a la abrasión.
- Poca resistencia a la corrosión.
Datos interesantes
- A finales de la década de 1930, los laboratorios de dirección e investigación de Dürener Metallwerke AG se encontraban en los alrededores de Borsigwalde. Berlína. Allí, a principios de la década de 1940, se desarrollaron aleaciones deformables de alta resistencia del sistema Al-Zn-Mg con una resistencia a la tracción de al menos 50 kgf/mm2, que se utilizaron en serie en aviones Heinkel y Junkers en forma de secciones prensadas y piezas forjadas[20]. En particular, para la aleación "Hydronalium Hy43" desarrollada en el Instituto DVL en 1940 (composición: 4,5 % Zn, 3,5 % Mg, 0,3 % Mn, 0,4 % Cu, el resto Al), en 1944 el Ministerio de Aviación RLM había publicado la especificación Flw3.425.5[21].
- El grado de aleación D16 apareció en 1946 como resultado de la reproducción sin licencia y el dominio por parte de la industria metalúrgica de la URSS de la tecnología para la producción de placas, láminas y perfiles de la aleación estadounidense 2024 (composición: 4% Cu, 1,5% Mg, 0,3% Cg, el resto - Al), que formó la base del fuselaje del bombardero pesado Boeing B-29 Superfortress. Detalle de la orden de copia ('...No se permiten desviaciones del prototipo americano, ni en ninguna parte, ni en ninguna unidad... firmada por Joseph Stalin) del avión Boeing B-29 fue dada personalmente por Stalin en 1944 en los planes y perspectivas para la creación del Tu-4 - Tu-4, el primer avión bombardero nacional portador de armas atómicas. VIAM investigó el peso de las piezas, su composición química, estructura y propiedades. Resultó que el duraluminio nacional era inferior en propiedades a la aleación 2024[22]. Resultó que la aleación estadounidense 2024 se diferenciaba del duraluminio nacional D1 por un mayor contenido de magnesio (hasta el 1,5%) y una pequeña adición (0,3%) de cromo.
Referencias
- ASM Handbook. Volume 2, In Properties and Selection: Nonferrous alloys and special purpose materials. ASM, 2002.
- «Duraluminio». Materialbox.cl. Consultado el 19 de marzo de 2016.
- J. Dwight. Aluminium Design and Construction. Routledge, 1999.
- J. Dwight. Diseño y construcción en aluminio. Routledge, 1999.
- «Aluminio Unido - ALEACIÓN 2024». Consultado el 8 de octubre de 2018.
- J. Snodgrass y J. Moran. Resistencia a la corrosión de las aleaciones de aluminio. En Corrosion: Fundamentals, Testing and Protection, volumen 13a de ASM Handbook. ASM, 2003.
- Parker, Dana T. Building Victory: Aircraft Manufacturing in the Los Angeles Area in World War II, p. 39, 87, 118, Cypress, CA, 2013. ISBN 978-0-9897906-0-4.
- J. Snodgrass and J. Moran. Corrosion Resistance of Aluminium Alloys. In Corrosion: Fundamentals, Testing and Protection, volume 13a of ASM Handbook. ASM, 2003.
- Parker, Dana T. Building Victory: Aircraft Manufacturing in the Los Angeles Area in World War II, p. 39, 87, 118, Cypress, CA, 2013. ISBN 978-0-9897906-0-4.
- Helmut Maier: Rüstungsforschung im Nationalsozialismus Organisation, Mobilisierung und Entgrenzung der Technikwissenschaften. Wallstein Verlag, 2002, ISBN 978-3-89244-497-8, pag. 378
- Otto Brandt, H. Dubbel, W. Franz, R. Hänchen, O. Heinrich, Otto Kienzle, R. Kühnel, H. Lux, K. Meller, W. Mitan, W. Quack, E. Sachsenberg: Taschenbuch für den Fabrikbetrieb. Springer-Verlag, 2013, ISBN 978-3-642-99589-7, S. 422
- «Zeppelin or Schütte-Lanz?». Flight: 758. 7 de septiembre de 1916.
- Thurston, A.P. (22 de mayo de 1919). «Metal Construction of Aircraft». Flight: 680-684.
- Isurugi, Tatsuhito (3 de septiembre de 2013). «"Kaze tachinu" toujou jinbutsu to tori ningen kontesuto. Honjou Kirou no sengo» [A Character form “The Wind Also Rises” and the Japan Birdman Rally: Kiro Honjo’s Postwar]. news.yahoo.co.jp (en japonés). Yahoo! Japan. Consultado el 2 de noviembre de 2020.
- Anschutz, Eric (31 de octubre de 2020). «Duralumin History & Use in Bicycle Building». Ebykr. Anschutz Media. Consultado el 1 de noviembre de 2020. «Duralumin was used to manufacture bicycle components and framesets from the 1930s to 1990s. »
- John P. Frick, ed. (2000). Woldman's Engineering Alloys. ASM International. p. 150. ISBN 9780871706911.
- «Italian Aircraft: Macchi C.200». Flight: 563. 27 de junio de 1940.
- Sackey, Joe (2008). The Lamborghini Miura Bible. Veloce Publishing. p. 54. ISBN 9781845841966.
- J. Snodgrass and J. Moran. Corrosion Resistance of Aluminum Alloys. In Corrosion: Fundamentals, Testing and Protection, volume 13a of ASM Handbook. ASM, 2003.
- «Organización de la OTB para el Estudio de la Ciencia y Tecnología de la Aviación Alemana». Archivado desde minot.ru/html/german/docs/d-49.htm el original el 20 de diciembre de 2016. Consultado el 17 de diciembre de 2016.
- Mühlenbruck A., Seeman H.J.. Untersuchungen an Al-Zn-Mg-Knetlegierungen. Luftfahrtforsch., 1942, Bd. 19, no. 9, s. 337-343
- Acerca de Friedlyander I. N. VIAM International Scientific and Technical Conference] Archivado el 8 de abril de 2016 en Wayback Machine.. 2013
Bibliografía
- Paul Krais: Werkstoffe. Band 2, A. Barth, Leipzig 1921, S. 517–518.
- Eintrag zu Duralumin. En: Römpp Online. Georg Thieme Verlag, abgerufen am 2. Januar 2015.
- A. von Zeerleder: Technologie der Leichtmetalle. Rascher, Zürich 1947.
- Stephan Hasse. Gießerei-Lexikon. 19. Auflage. Schiele und Schön, Berlin 2007, ISBN 978-3-7949-0753-3, véase: Duraluminium.
Véase también
Enlaces externos
Wikimedia Commons alberga una categoría multimedia sobre aleaciones de aluminio.
- * Duralumini - Gran Enciclopèdia Catalana (en catalán)