Forage
Le forage est l'action de creuser un trou (aussi appelé « puits » dans le domaine de la prospection) dans la Terre. L'équipement du puits, tel les tubages, et de manière générale les moyens techniques permettant de creuser, varient en fonction de son dimensionnement et de ses objectifs. On fore pour prospecter et/ou exploiter le sous-sol. Par exemple, des puits sont forés pour :
- trouver et exploiter des ressources naturelles enfouies (eau, pétrole, ressources minières) ;
- la géotechnique ;
- la géothermie ;
- l'environnement et la décontamination de sols[1] ;
- la recherche scientifique pure.
Ne doit pas être confondu avec Perforation ou Perçage.
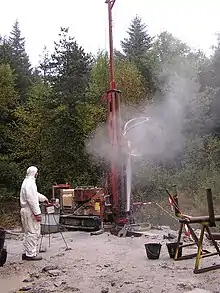
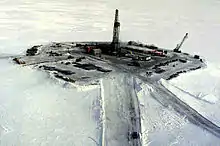
Les moyens techniques mis en œuvre diffèrent largement : de la foreuse manuelle, à la foreuse légère et mobile pour les forages de moins de 10 mètres, à une installation onshore avec un puits de pétrole ou bien à une plate-forme pétrolière pour l'exploitation pétrolière offshore.
En 2014, une étude scientifique de données officielles provenant d'Australie, Autriche, Bahreïn, Brésil, Canada, Pays-Bas, Pologne, Royaume-Uni et États-Unis montrait que plus de quatre millions de puits d'hydrocarbures terrestres avaient déjà été forés rien que dans ces pays[2]. Une fois l'exploitation terminés, très peu d'entre eux sont surveillés, et des pertes d'intégrité de cuvelage ou béton sont régulièrement constatées[2].
Systèmes principaux
Alimentation
Dans pratiquement tous les cas, un moteur Diesel fournit la puissance nécessaire aux forages. La puissance est alors délivrée soit par électricité, soit mécaniquement. Dans le cas de forages profonds, des générateurs électriques alimentés par un moteur Diesel sont le plus souvent utilisés. L'option « électrique » a de nombreux avantages dont, entre autres, la réduction du bruit et une organisation du chantier plus simple.
Transmission mécanique
Les moteurs qui fournissent l'énergie mécanique sont reliés soit à une table de rotation qui transmet le mouvement à la tige carrée [comme son nom l'indique, elle est carrée ou hexagonale pour permettre sa rotation ; cette tige est raccordée aux tiges de forage par un raccord d'usure, qui transmet le mouvement à l'outil de forage (bit en anglais)], soit à une tête de rotation (powered swivel) qui transmet le mouvement directement aux tiges de forage.
Système Rotary
Le système de rotation comprend habituellement une tête d'injection, une tige d'entraînement qui passe à travers une table de rotation et qui est reliée à une colonne de forage (en) (ou train de tiges) et en bout de colonne un outil de forage creusant le sol. La tige d'entraînement, et de fait la colonne de forage, et l'outil de forage, tous subissent une rotation via la table de rotation et une section angulaire de la colonne qui se trouve au niveau de la table, ou bien si la table n'est pas le moyen de rotation de la machine de forage, via la tête d'injection qui sert également à l'entraînement de la colonne.
La garniture peut être définie par « l'ensemble des matériels tubulaires descendus dans le puits, à l'exception des cuvelages »[3].
Turboforage
Le turboforage est une variante du forage rotary. Dans celui-ci, les tiges de forage ne tournent pas, et le trépan est fixé directement sous la turbine, qui est mise en rotation par le fluide de forage (eaux boueuses). Le turboforage a été mis au point par la société Neyrpic et les équipements commercialisés à partir de 1956 sous le nom commercial de Neyfor[4]. Plus rapide mais bien plus cher que le forage rotary, le turboforage est rapidement cantonné à des usages spécifiques, particulièrement l'off-shore.
Colonne montante de forage
La colonne de forage est une suite de tiges vissées entre elles et habituellement de tailles standard. L'ajout de tiges au fur et à mesure permet de progresser plus profondément. Pour les appareils de forage de taille moyenne et importante, la taille des tiges a été standardisée et elles font en moyenne 9,5 m. Cette taille standard peut paraître bâtarde, mais il s'avère qu'elle fut définie en fonction des normes API et correspond à une longueur de 30 pieds.
Raccordement des tiges de forage
Les tiges de forage sont reliées entre elles par des filetages standardisés. Le diamètre des tiges est plus important au niveau des raccords afin de les renforcer et de les protéger contre l'usure.
Outils de forage
Pour le foreur, l'outil de forage qui se trouve au bout de la colonne de forage, est une des clés de son activité. L'outil doit être choisi dans un catalogue aussi varié que peut l'être la lithologie rencontrée. Si un outil de type marteau peut briser une roche compacte, il sera inefficace pour creuser une argile, à la différence d'une tarière et des outils de type trilame.
Selon son diamètre, l'outil peut peser de quelques kilogrammes à plusieurs centaines de kilogrammes. On distingue différents types d'outils de forage :
- couronnes qui sont des tiges, améliorées ou non, munies de dents ou de picots renforcés ;
- forages au diamant (diamant synthétique polycristallin), qui font appel à des outils de formes très variées [dont les formes de type tricône (trépan) et trilame] dont l'utilisation se restreint à l'industrie pétrolière et minière du fait du coût d'exploitation élevé. Les diamants ont la forme de pastilles noires prises dans la masse métallique de l'outil ;
- tricônes, outils montés par trois cônes rotatifs ou molettes (libres) munis de picots pour les terrains durs (longs picots pour les terrains très compétents[pas clair], tels les quartzites, et picots courts pour les terrains moins compétents[pas clair] tels les schistes), et de dents pour les terrains durs (calcaires) à argileux (marnes) - les dents étant plus longues lorsque le terrain est plus argileux. On trouve également des tricônes à pastilles faites de matériaux ultra-résistants (diamant et carbure de tungstène par exemple) ;
- trilames, outils montés par trois « lames » en chevron pour les terrains les plus argileux et en gradin ou escalier pour les terrains plus durs (marnes et calcaires) ;
- marteaux fond-de-trou (MFT), qui sont des outils à percussion prédestinés aux sols durs et cassants.
Les aléseurs ne sont pas à proprement parler des outils de tête, puisqu'ils peuvent être montés en complément de l'outil principal. Le but des aléseurs est d'agrandir un trou, ou simplement d'en racler les bords et parfois de compacter le fond du forage. On distingue donc les aléseurs compacteurs, en forme de pointe, ouverts à lames ou cylindriques, étagés, etc.
- Tricône
- Trilame
- Tricônes
- Tricône
- Tricône
- Tricône
- Tricône
- Tricône
- Tricône
Mât et derrick

Le mot derrick utilisé dans le domaine pétrolier désigne une tour en bois ou en métal soutenant le dispositif de forage d'un puits de pétrole. Le mot anglais a d'abord désigné une potence ou gibet et viendrait de Thomas Derrick (en), célèbre bourreau de Tyburn, principal lieu des exécutions capitales des criminels anglais. Puis il désigne plus généralement un dispositif de levage. Au XIXe siècle, en français, le terme est appliqué au cadre supportant l'appareil de forage dans une plate-forme pétrolière terrestre.
Fluide
Le fluide dans un forage est un élément clé, car il évacue les déblais qui s'accumulent au fond du puits, il stabilise les parois du puits lorsque ce dernier est encore « nu » (sans cuvelage) et enfin il peut aussi lubrifier et refroidir l'outil en activité. Le choix d'un fluide ne s'arrête pas là : les eaux souterraines (parfois potables) peuvent être contaminées par certains fluides utilisés.
Pour évacuer les déblais de forage, soit le fluide doit circuler très vite (air comprimé), soit le fluide, alors liquide, doit être d'une densité et d'une viscosité contrôlées régulièrement par le foreur. L'ajustement de ces paramètres se fait par ajout de bentonite et de polymères pour la viscosité, ainsi que de baryte, formiate de césium ou de sels de sodium ou de potassium pour la densité. Le problème de l'évacuation des cuttings ne dépend pas uniquement des propriétés du fluide - la pression et le débit qui lui sont imposés, la surface de la colonne d'évacuation et les pertes sont d'autres facteurs dont il faut tenir compte.
Les divers fluides de forage sont :
- l'air comprimé ;
- l'eau ;
- la bentonite (ou « boues bentonitiques ») ;
- les gels de polymère - utilisés pour la fabrication des boues ou comme additifs ;
- les mousses ;
- le formiate de césium saturé dans l'eau est assez dense (densité d=2,3) pour que certains sédiments flottent ;
- la baryte en émulsion et les sels de sodium et de potassium augmentent aussi la densité des fluides.
Circulation des fluides
La circulation de l'air se fera au moyen d'un compresseur pour l'air comprimé, et de la puissance du compresseur dépendra la profondeur du forage. La boue, quant à elle, est envoyée au moyen de pompes spéciales. On appelle le fluide en circulation directe, celui qui descend par le train de tiges, et le fluide en circulation inverse celui qui descend par l'espace annulaire. La circulation inverse possède plusieurs avantages :
- si, lors de la circulation du fluide, les parois nues du forage s'éboulent, l'éboulis est repris directement par la circulation. Dans le cas contraire, l'éboulis pourrait s'accumuler plus facilement ;
- les échantillons de sol et d'eau prélevés pour analyse ne sont pas contaminés par les parois nues du forage.
Une « perte de fluide » indique habituellement la présence des fractures ou autres vides dans les terrains traversés. La perte de fluide mène habituellement à une diminution de la pression, ce qui peut poser des problèmes majeurs au foreur.
- Schéma d'un forage en circulation directe
- Schéma d'un forage en circulation inverse
Personnel présent sur un chantier de forage
Poste soit 3x8 (France), soit 2x12 (autres pays)
Appareil de forage ou rig de forage
- 1 à 4 roughneck ou sondeurs par poste, soit 3x8 (France), soit 2x12 (autres pays)
- 1 derrickman ou derrickhand
- 1 assistant driller ou second
- 1 driller ou chef de poste
- 1 toolpusher ou chef de chantier
- 1 drilling supervisor jour et nuit
- 1 company man jour et nuit
- 1 bitman jour et nuit
plus :
- 1 chef d'équipe surface et manœuvre
- 1 à 4 surfaciers
plus :
- 1 chef mécanicien
- 1 chef électricien
- 1 à 2 mécaniciens
- 1 à 2 électriciens
- 1 superviseur HSE
Systèmes auxiliaires
Bloc d'obturation de puits pour la maîtrise des venues
La maîtrise des éruptions provenant d'un puits, nécessite un bloc d'obturation consistant en un système de vannes. Cette maîtrise peut se faire en contenant les venues dans le puits (coiffage) ou en évacuant ces dernières. Dans le cas de forages pétroliers, le bloc d'obturation doit permettre de réaliser les points suivants[5] :
- le cisaillement du train de tiges
- la suspension du train de tige, obturation ferme ;
- la maîtrise du puits avant sa réouverture.
Système de chauffage
Sous climat très froid, comme au Québec, les fonctions principales du système de forage ne doivent pas geler ; pour cela, un système de chauffage est nécessaire. Un système typique comprend un chauffe-eau au Diesel et un réseau de tuyaux reliant le chauffe-eau aux différentes unités du forage. Le même système peut être utilisé pour les besoins du personnel du chantier.
Tubages, crépines, sabots
Tube guide ou cuvelage
Le tube guide est dans presque tous les cas nécessaire et peut être défini[3] comme le tube qui isole tout le puits des terrains encaissants et qui durant les opérations contient le fluide de forage.
Tubage intermédiaire
Le tubage intermédiaire est facultatif et peut être défini[6] comme « le tubage installé dans un puits après l'installation et à l'intérieur du tubage de surface et dans lequel les opérations de forage ultérieures peuvent être effectuées à l'intérieur du puits ».
Tubage de production
Le tubage de production isole l'encaissant du système d'exploitation (pompe et tiges). Ce tubage est cimenté dans l'encaissant, du moins dans la partie basse du forage si un tubage intermédiaire est utilisé.
Crépines
Les crépines sont les tubages possédant des espaces laissant passer le fluide de l'encaissant. Il existe une grande variété de matériaux et de modèles de crépines.
Sabot
Le sabot se trouve à la terminaison du tubage de production ou des crépines. Il est censé créer une zone morte du point de vue de la circulation en cas de pompage ou d'injection. Il permet la sédimentation de particules, et la mise à l'écart de la circulation des objets qui tomberaient malencontreusement dans la colonne.
Ciments et cimentation
Le ciment est le complément indispensable à la mise en place et à la bonne tenue de la colonne métallique.
La cimentation du puits doit assurer le support mécanique du cuvelage, l'étanchéité entre la roche et le cuvelage, une protection de la colonne de tubage contre la corrosion côté terrain, et l'isolation entre les différentes couches géologiques (pour éviter les transferts de fluides entre ces zones)[7]. Le cuvelage du puits présente ensuite toutes les caractéristiques d’un ouvrage bétonné armé, avec une colonne d’acier ayant une bonne résistance à la traction et un ciment offrant en complément une bonne résistance à la compression.
La cimentation d’un puits profond est une opération délicate. Elle se fait pendant l’opération de complétion du forage, par des sociétés spécialisées. Le coulis de ciment (du type Portland) est injecté en fond de puits sous pression de manière à le faire remonter derrière la colonne jusqu’à la tête du puits.
La solidification du ciment est une réaction exothermique qui entraîne de facto un rétreint qui peut le cas échéant entraîner une mauvaise adhérence du ciment sur la paroi en acier de la colonne. Cet espace annulaire peut être haut de plusieurs centaines de mètres de long et large de quelques cm d'épaisseur[7], il doit donc être impérativement contrôlé ainsi que les chenaux résiduels et le cuvelage réparé par une cimentation secondaire. Cette inspection in situ se fait par des outils de diagraphie différée du type acoustique comme les CBL (Cement Bond Log) ou VDL (Variety Density Log) sectorisées ou non. Ces diagraphies pourtant obligatoires ne sont pas toujours systématiquement effectuées et peuvent être entre autres la cause d’accidents majeurs (cf. Deepwater horizon). Depuis 2017 des outils d’auscultation électrodynamique utilisant des transducteurs à couplage sec (EMAT) sont également proposés. Le contrôle de la cimentation avec celui de la corrosion peut également s’inscrire dans un programme plus large de surveillance de l’intégrité du puits au cours du temps[8].
Les coulis injecté dans l'espace annulaire sont préparés en surface à température ambiante juste avant d'être pompés ; ils doivent être bien plus fluides que ceux habituellement utilisés dans le BTP[7] et soigneusement ajustée en fonction de la nature géologique des roches traversées et de la profondeur[7]. Plus le puits est profond, plus la température et le temps de pompage augmentent[7] ; il faut donc maitriser la cinétique de prise du ciment en adaptant la formulation du coulis en tenant compte des effets de la prise et de la chaleur sur la rhéologie et la stabilité du coulis[7] (aucun phénomène de sédimentation ni de synérèse ne doit dégrader le ciment avant sa prise). Le volume réel de coulis à injecter est le volume théorique de ciment, majoré d'une certaine quantité « pour tenir compte des hors profils, irrégularités et surcreusements éventuels « caving » du trou »[7]. La prise du ciment d'une cimentation est d'au moins 48 heures[7].
D'autres problèmes sont que :
- le coulis de ciment doit avoir un comportement thermo-hydro-mécanique (THM) approprié[9], et donc répondre à des normes précises[10], mais la qualité du ciment Portland varie beaucoup d'un pays à l'autre[7] ;
- les plastifiants retardent et les retardateurs dispersent[7] ;
- les propriétés des additifs chimiques varient en fonction de la température[7] ;
- les additifs utilisés doivent être compatibles entre eux[7].
- traverser une nappe libre est une contrainte supplémentaire
- Sous haute pression (à grande profondeur), la stabilité du ciment (face aux conditions et aléas environnementaux (pression, contraintes dues aux microséismes ou aux séismes induits, attaque par es chlorures et sulfures, etc.), et sa microporosité, et sa nanoporosité prennent plus d'importance que près de la surface. La mesure et le suivi de ces paramètresnécessitent des moyens particuliers[11],[12].
Considérations juridiques
Pour des raisons économiques, sanitaires ou environnementales, la plupart des forages doivent faire l'objet de déclaration, d'autorisation, voire d'une étude d'impact, y compris dans certains pays les forages individuels.
Ainsi en France, depuis le , les particuliers doivent-ils déclarer leurs forages à la mairie ou sur un site Internet dédié aux Forages domestiques[13]. Depuis le , la déclaration doit précéder d'au moins un mois le début des travaux, et les puits ou ouvrages existants au doivent être déclarés avant le auprès du maire de la commune.
Considérations environnementales
Un forage est une opération lourde (et parfois dangereuse) qui peut induire la mobilisation d'importants volumes de terres, la présence d'engins, et nécessite de grandes quantités de carburant et parfois d'autres produits tels des acides et d'autres produits chimiques, et doit être mis en œuvre par un personnel parfois nombreux. Il peut avoir des impacts différés dans l'espace et dans le temps.
Dans le cas d'un forage pour l'alimentation en eau potable il faut s'assurer que l'aquifère qui sera exploité ne soit pas vulnérable à la présence du chantier.
Dans le cas de forages pétro-gazier les hydrocarbures exploités ne doivent pas polluer la nappe, l'air et les alentours.
Toute extraction importante de fluide souterrain (eau, pétrole, gaz) peut induire une séismicité induite voire des mouvements de sol de type affaissements de surface[14]. Des affaissements ou mouvements de sol en surface[15]. Des impacts sismiques (« séisme induit ») sont fréquents autour des forages pétroliers ou gaziers importants et des affaissements peuvent se produire lors de pompage d'eau souterraine dans un sol sédimentaire non consolidé[16].
Bruit
Un forage peut être très bruyant.
Réhabilitation du site
Elle est dans certains cas obligatoire, et peut alors intégrer des mesures compensatoires ou réparatrices. Certains puits industriels, en fin de vie, doivent être soigneusement colmatés de manière à empêcher des transferts verticaux ou horizontaux de polluants entre les nappes ou de la surface vers le sous-sol.
Sécurité du personnel, accidents fréquents
Sécurité du personnel
La sécurité du personnel passe par la très bonne connaissance des machines, le rangement du chantier, la prise en compte des risques liés à l'objectif du forage et la protection individuelle des foreurs et des visiteurs (casque de protection, protection auditive, chaussures de protection, gants, masque anti-poussière, lunettes de sécurité, appareil respiratoire isolant, etc.). Un forage inclut habituellement la manipulation d'objets extrêmement lourds (trains de tiges, outils forants, pompes submersibles, etc.), de possibles travaux en hauteur du fait du mât de forage, de la soudure, de la mécanique (moteurs, pompes, compresseurs, etc.) et des branchements électriques. Un forage crée de la poussière. Il n'est pas non plus anecdotique de mentionner le stress qui retombe sur le personnel : délais, frustrations du fait du manque de résultat, cadences accélérées, fatigue. Ce stress doit être pris en compte par les superviseurs et les chefs d'équipe.
Les deux principaux risques pour le personnel de forage sont le happement par les tiges et les blessures aux mains. Les vêtements flottants (écharpes, tee-shirts amples…) sont généralement interdits et les combinaisons sont préconisées. Lors de la manipulation des tiges, il faut faire très attention au placement de ses mains : jamais de mains sous les tiges.
Selon la géologie et l'environnement, le forage peut mettre les foreurs et riverains en présence de gaz dangereux (dioxyde de carbone CO2, sulfure d'hydrogène H2S…) du fait de leur explosivité ou leur toxicité, de terres et de liquides contaminés (sous les décharges, les sites industriels…).
Accidents fréquents
Voici une liste non exhaustive d'accidents parmi les plus fréquents :
- présence de lignes électriques en hauteur, et risque de contact avec certains éléments hauts du forage (mât, grue) ;
- présence de lignes électriques, canalisations de gaz ou d'eau, de cuves à fioul dans le sous-sol, pouvant être forées ;
- pièces lourdes qui tombent d'une certaine hauteur créant de potentiels accidents/blessures (décrochage d'une tige, éboulement d'un amas de tiges, renversement d'un outil posé à la verticale, etc.) ;
- risque de chutes des structures élevées (plancher de forage, mât) ;
- assourdissement ;
- pincement des doigts, des bras ;
Problèmes et accidents techniques
Pertes de fluide
Il existe deux types de pertes :
- les pertes partielles : petite fissure provoquant la perte du fluide de circulation ; cette perte peut être maîtrisée en ajoutant des additifs à la bentonite pour l'alourdir ;
- les pertes totales : grande fissure qui peut dépasser largement les 500 m horizontalement, cette perte provoque la perte totale de la boue de forage, ce qui nécessite le forage à l'eau claire pour limiter les pertes ; on peut aussi envisager une cimentation partielle de la partie fissurée.
Ces pertes proviennent essentiellement des fissures (formations compétentes[pas clair] fracturées) et cavités (karsts) rencontrées au cours du forage.
Coincement des tiges dans le trou
La non verticalité du trou (cf. déviation), des éboulements et des tubes brisés ou déboîtés sont des origines possibles du coincement des tiges de sondage dans le trou. Des objets qui tombent dans le trou et des éléments fragiles de la colonne, qui se brisent, peuvent également conduire au coincement des tiges.
Dévissages impossibles, vissages trop serrés
Un pas de vis mâle et un pas femelle peuvent rester coincés l'un dans l'autre. Il faut alors faire appel à des machines particulièrement puissantes utilisant des vérins hydrauliques pour dévisser les deux éléments.
Déviation
Souvent dû au fait que les formations géologiques ont un certain pendage, la déviation des trous de forage est assez fréquente. En tout premier lieu, il faut s'assurer de la verticalité du mât de forage qui sert de guide au train de tige. L'inclinaison du mât peut au besoin être adaptée pour corriger une déviation. La non-verticalité d'un forage est peu souhaitable, sauf dans le cadre de forages dirigés, les carottages et la géotechnique.
Éboulement
L'éboulement est un problème très fréquent dans les zones où le recouvrement est assez épais (l'altération dépasse 15m). cette formation non consolidée, va s'écrouler forcément sous l'effet de vibrations de la foreuse. Pour y remédier on utilise le PVC ou des fluides tels que la bentonite, le polymer CR650...
Détachement d'une partie de la colonne de forage
Intentionnellement ou non, le foreur peut perdre une partie de la colonne de forage. Les causes peuvent être diverses : une tige peut se dévisser ou doit être dévissée, ou casser pour être remontée.
Les outils de repêchage servent à accrocher et remonter des trains de tiges ou autres morceaux qui se sont décrochés et sont tombés ou coincés dans le trou de forage.
Forage horizontal et forage dirigé
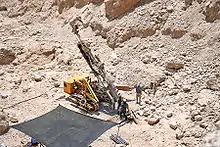
Le forage horizontal est une technique de génie civil permettant de faire passer des canalisations et des câbles sous des obstacles (chaussées, bâtiments, cours d'eau, etc.) sans intervenir directement sur ces obstacles. Ainsi, on pourra réaliser un forage horizontal perpendiculaire à l'axe d'une chaussée, sous la structure de celle-ci, afin d'y faire passer des canalisations sans avoir à réaliser de tranchée qui endommagerait la structure de la chaussée.
Le forage dirigé (Directional drilling) profond est une application récente nécessitant de puissants moyens informatiques. Grâce au forage dirigé, des ressources qu'il était difficile d'atteindre en forage classique du fait d'obstacles géologiques (lithologies rebelles), deviennent accessibles. Les secteurs pétrolier et gazier sont de gros demandeurs de forages dirigés, dont à puits multilatéraux, en particulier pour l'extraction du gaz de schiste, après fracturation hydraulique des formations géologiques schisteuses. Pour ces forages, on estime par modélisation ou suivi la direction empruntée.
Forage en mer
Les forages offshores sont réalisés en mer. Des navires spécialement équipés, comme le JOIDES Resolution, permettent de forer le fond des océans à une grande profondeur[17].
Méthodes de tubages à l'avancement
Méthode du Casing drilling
La technique dite du Casing drilling a été développée et brevetée par la compagnie canadienne Tesco Drilling Technology[18]. Cette méthode consiste à utiliser les tubes - qui formeront les parois du puits - comme tubes de forage ; c'est donc un double emploi pour un même tube. Les avantages sont en général multiples : gain de temps, forage dans des milieux avec un potentiel de perte total (le casing en général est alors posé dans cette zone).
Cette méthode est employée à travers le monde, sur certains champs d'Afrique de l'Ouest, afin de réaliser des économies de temps substantielles sur les phases de surface. D'autres exemples peuvent être cités comme en Algérie en collaboration avec l'entreprise algérienne EPE Steppe Forage à Laghouat dans la région de Batna « Amdoukel ». Le forage réalisé avec cette technique a atteint une profondeur de 650 m.
Pose de tiges simultanées lors du forage (méthodes Odex et Jucon)
Initialement développée par Atlas Copco, la méthode Odex suit la méthode du marteau fond de trou et comprend en plus un tube en acier qui repose par-dessus un aléseur excentrique[19] ou sabot un peu plus large que le tube. Ce tube forme le tubage externe du forage. L'énergie de la percussion du marteau et le propre poids du tube enfoncent ce dernier dans le trou. L'Odex est composé de trois parties rétractables et formant l'outil forant. Le Jucon est quant à lui composé de quatre parties rétractables et est pour le reste très semblable à l'Odex.
Tubage enroulé
Cette technique (Coiled tubing (en)) permet de dérouler un tube continu (futur tube externe de l'ouvrage) avec l'avancement du forage en profondeur. Le tube continu est enroulé sur un cylindre et est injecté ou tiré par une structure en arc de cercle (arche) plongeant dans le puits et sur laquelle sont montées des chaînes à très gros maillons permettant d'appliquer une pression, contrôlée par des cylindres hydrauliques, sur le tube. Le passage du tube continu dans l'arche et les pressions exercées sur ce dernier pour l'injecter ou le retirer du trou accélèrent son vieillissement. Ce vieillissement est, entre autres, influencé par le rayon de l'arche d'injection. La technique du tubage enroulé possède de nombreux avantages, notamment dans la réalisation de forages déséquilibrés et de forages dirigés. Toutefois, cette technique s'avère parfois coûteuse, notamment si le matériel reste inutilisé, tandis que la mise en place du tubage peut (contre toute attente) être plus lente comparée à une installation traditionnelle.
Forages profonds
L’objectif des forages profonds tels celui du programme KTB ((en) Kontinentales Tiefbohrprogramm der Bundesrepublik Deutschland (en)) qui a atteint 9 800 m en Allemagne ou du forage sg3 de 12 kilomètres dans la péninsule de Kola (Russie), est de mieux connaître la lithosphère et d’atteindre la zone de transition entre la croûte et le manteau supérieur : le Moho (discontinuité de Mohorovičić).
Si ces forages ont permis de confirmer la structure et la composition de la croûte, ou de tracer des profils sismiques régionaux, elles n’ont malheureusement pas permis d’atteindre à ce jour la couche sous-jacente tant convoitée. On a pu ainsi mesurer par exemple que la température des roches atteint environ 300 °C à 10 kilomètres de profondeur.
Comme la croûte océanique est plus mince que les plaques continentales, plusieurs projets de forage océanique ont vu le jour, MOHOLE puis DSDP[20] (1968-1983) aux États-Unis, puis des programmes internationaux comme ODP[21] (1985-2003) puis IODP[22] (2003-2013). Pour l'instant, aucun navire n’a encore réussi à forer jusqu’à la discontinuité de Mohorovičić.
Exploitation des forages d'eau
Les forages visant à prélever de l'eau, selon leur importance peuvent induire un « cône de rabattement de nappe » voire une baisse de la nappe et du niveau piézométrique, voire un épuisement de la nappe avec disparition des sources ou de rivières ou de zones humides. Aussi, comme la plupart des formes d'exploitation de ressources naturelles sont-ils généralement réglementés. Un pompage important peut favoriser des transferts de polluants via les déplacements horizontaux de la masse d'eau souterraine ou via la descente verticale de l'eau. Pour ces raisons, des périmètres de protection des « zones de captage » peuvent être obligatoires autour d'un captage d'eau potable, ainsi que des mesures pour la protection du champ captant. Dans la plupart des pays, les forages individuels, agricoles ou industriels doivent être déclarés, et peuvent faire l'objet d'une taxe.
Uphole
Le uphole (ou carottage sismique) est une technique de géophysique.
Le principe consiste à placer une source dans un forage (explosif, air gun, sparker...) et à enregistrer les premières arrivées en surface à l'aide d'un sismographe et de géophones.
L'interprétation des données permet de proposer un profil vitesse/profondeur.
Fuites durant l'exploitation et devenir des forages après leur exploitation
Une méta-analyse de 25 études ayant porté sur les problèmes de fuites de tubages de puits de production, d'injection (puits actifs, inactifs et/ou abandonnés, tant onshore qu'offshore, dans des réservoirs conventionnels ou non conventionnels) a montré que les pertes d'intégrité sont plus fréquentes qu'on ne l'imaginait (avec u risque variant selon le type de forage et l'âge des puits)[2]. Ainsi sur 8030 puits récents forés dans le schiste de Marcellus et inspecté en Pennsylvanie de 2005 à 2013, 6,3% présentaient au moins une fuite. Une surveillance faite de 2008 à 2011 de 3 533 puits de Pennsylvanie a mis au jour 85 défaillances de ciment ou de cuvelages d'acier, et quatre de ces puits ont connu une éruption et deux des fuites importantes de gaz[2]. Au Royaume-Uni ce sont 2152 puits d'hydrocarbures qui ont été forés (onshore, c'est-à-dire sur terre) entre 1902 et 2013 dans des réservoirs conventionnels la plupart du temps ; et pour 143 puits actifs encore en production fin 2000 « il existe des preuves d'un échec de l'intégrité des puits »[2]. La loi anglaise impose une remise en état de chaque puits après abandon de son exploitation, mais pour 65,2% de ces sites il ne reste plus de traces de leur présence en surface et aucune surveillance n'est faite ; de plus, pour 53% d'entre eux, la propriété du puits (et donc la responsabilité associée) n'est pas claire (50 à 100 de ces puits seraient des sites orphelins)[2]. La situation semble encore plus grave pour les forages anciens (ex : une étude (2005) a montré que 70 % des puits terrestres du champ pétrolier de Santa Fe (découvert en 1921 en Californie) présentent des pertes d'intégrité (avec observation de bulles de gaz remontant en surface le long des tubes)[23]. La plupart des forages récents comportent des sections horizontales, or selon un rapport parlementaire canadien « une cimentation de qualité supérieure est universellement reconnue comme étant plus difficile lorsque le tubage est incliné (par exemple dans les puits horizontaux) »[24], et les injections profondes sous haute pression peuvent elles-mêmes être sources de séismes induits par l'Homme (de magnitude 4 à 4,7 par exemple dans l'Ohio[25]).
Notes et références
- « Cahier 5 - Échantillonnage des sols »
- Davies, R. J., Almond, S., Ward, R. S., Jackson, R. B., Adams, C., Worrall, F.... & Whitehead, M. A. (2014). Oil and gas wells and their integrity : Implications for shale and unconventional resource exploitation. Marine and Petroleum Geology, 56, 239-254.
- Ministère de l'Économie, des Finances et de l'Industrie de la France, décret no 2000-278 du 22 mars 2000 complétant le règlement général des industries extractives institué par le décret no 80-331 du 7 mai 1980 modifié
- Anne Dalmasso, Neyrpic, Dire l'entreprise, (ISBN 978-2-9534279-0-5), p. 133
- Ministère de l'Énergie et des Mines d'Algérie, décret exécutif no 94-43 du 18 Chaâbane 1414 correspondant au 30 janvier 1994 fixant les règles de conservation des gisements d'hydrocarbure et de protection des aquifères associés, p. 3 (no JORA : 008 du 13 février 1994)
- Gouvernement du Québec, Règlement sur le pétrole, le gaz naturel, la saumure et les réservoirs souterrains, Loi sur les mines, (L.R.Q., c. M-13.1, a. 306, par. 2 à 5, 10, 14 à 21, a. 310 et 313)
- Bruno Drochon, La formulation des coulis de ciment mis en oeuvre dans la construction des puits de pétrole, EDP Sciences, , 26–34 p. (ISBN 978-2-7598-0143-5, DOI 10.1051/978-2-7598-0143-5.c003, lire en ligne)
- Stéphane Sainson, Les diagraphies de corrosion : acquisition et interprétation des données. Ed. Lavoisier, 2010
- BOURISSAI, Monsef, MEFTAH, Fekri, BRUSSELLE, Nadège et BONNET, Guy, « Comportement thermo-hydro-mécanique (THM) de la pâte de ciment au très jeune âge dans des conditions de température et de pression élevées », Congrès français de mécanique, (ISSN 2491-715X, lire en ligne, consulté le )
- ex. : 10A/ISO 10426-1 : 2000. Industries du pétrole et du gaz naturel – Ciments et matériaux pour la cimentation des puits- Partie 1 : Spécification. American Petrolum Institut (API)
- (en) Jennings H.M. Thomas J.J. Gevrenov J. Constantinides G. Ulm F.J. (2007) A multi-technique investigation of the nanoporosity of cement paste. Cement and Concrete Research 37, 329–336.
- E. Nauleau, F. Martineau, C. Kréziak et S. Ghabezloo, « Effet des conditions environnementales sur les propriétés mécaniques d’un ciment de puits géothermique », Proceedings of the 18th International Conference on Soil Mechanics and Geotechnical Engineering, Paris, 2013.
- Site Internet dédié aux Forages domestiques cf. code général des collectivités territoriales ; décret du 2 juillet 2008, entrée en vigueur le 1er janvier 2009 ; articles 54 et 57 de la Loi du 30 décembre 2006 sur l'eau et les milieux aquatiques, et document déclaratif Cerfa 13837-01
- Yerkes, R. F., & Castle, R. O. (1976). Seismicity and faulting attributable to fluid extraction. Engineering Geology, 10(2-4), 151-167.
- Castle RO, Yerkes RF (1976) Recent surface movements in the Baldwin Hills, Los Angeles County, California—a study of surface deformation associated with oil field operations: US Geol Surv Prof Pap 882, 125 pp
- Holzer, T. L. (1984). Ground failure induced by ground-water withdrawal from unconsolidated sediment. Reviews in Engineering Geology, 6, 67-106.
- http://www-odp.tamu.edu/resolutn.html
- (en) Tesco Corporation
- Ministère de l'Économie, des Finances et de l'Industrie de la France, Les techniques de forage utilisées en eau minérale - Note technique no 2, novembre 1995
- DSDP
- ODP
- IODP
- G. Chillingar, B. Endres (2005) Environmental hazards posed by the Los Angeles Basin urban oilfields: an historical perspective of lessons learned | Environ. Geol., 47, p. 302-317|résumé
- Becklumb P, Chong J & Williams T.G (2015). Le gaz de schiste au Canada: risques environnementaux et réglementation. Service d'information et de recherche parlementaires.
- Ward H & Nicol A.M (2016) Comprendre l'incidence sur la santé publique de la production de gaz de schiste et de la fracturation hydraulique. Centre de collaboration nationale en santé environnementale.
- Cet article est partiellement ou en totalité issu de l'article intitulé « Uphole » (voir la liste des auteurs).
Annexes
Articles connexes
Bibliographie
- Bertrand Gonthiez, Réaliser et entretenir son puits, éd. Eyrolles, 2009.
- Michel Detay, Le Forage d'eau - Réalisation, entretien, réhabilitation, éd. Masson, 1993.
- Albert Mabillot, Le forage d'eau : guide pratique, éd. Lavoisier, 1989.
- Magdeleine Moureau, Gerald Brace, Dictionnaire du forage et des puits, éd. Technip, 2000.
- Jean-Paul Nguyen, Techniques d'exploitation pétrolière. Le forage, éd. Technip, 1993.
- Stéphane Sainson, Les diagraphies de corrosion : acquisition et interprétation des données, éd. Lavoisier, 2010
Liens externes
- Portail des sciences de la Terre et de l’Univers
- Portail des énergies fossiles