Gestion de la production
La gestion de la production est l'ensemble des activités qui participent à la conception, la planification des ressources (matérielles, financières, ou humaines), leur ordonnancement, l'enregistrement et la traçabilité des activités de production, le contrôle des activités de production de l'entreprise.
Du fait du développement des activités de services dans les économies développées (Ainsi le secteur tertiaire représentait en France en 2004 75 % de l'emploi civil et 76 % de la valeur ajoutée), la gestion de la production s'est élargie aux services et ne concerne plus seulement l'industrie.
L'objectif est d'améliorer de façon continue la gestion des flux et stocks inclus dans la chaîne de travail qui débute avec les fournisseurs et se termine chez les clients intermédiaires ou finaux.
Mais dans les entreprises de services la production ne peut par définition pas être stockée du fait de son caractère immatériel. De plus d'autres caractéristiques des services, comme l'inséparabilité, qui tient à ce que la consommation et la production aient lieu forcément ensemble et que le client soit de ce fait fortement impliqué dans la production du service, imposent aux entreprises du secteur tertiaire des formes spécifiques de la gestion de production des services
L'ensemble de ces activités doit être réalisé dans le respect des procédures établies (implicitement ou explicitement) par l'entreprise et tenir compte à la fois de la qualité de ses produits ou services, mais aussi de la sécurité de ses salariés ou de son environnement.
Pour mener à bien ces différentes tâches, les entreprises s'aident d'outils informatiques, de la gestion de la production assistée par ordinateur aux progiciels de gestion intégrés : PGI ou ERP en passant par la supervision ou le MES.
Historique
- Le système de production Ford (Voir Taylorisme et Fordisme)
- Le système de production Toyota (Voir Toyotisme)
La société Toyota a été pionnière dans l'élaboration des méthodes modernes de gestion de la production, aujourd'hui regroupées sous le nom des méthodes flexibles, méthodes agiles ou, faute de meilleure traduction de l'anglais, « méthodes lean ». Il s'agit de produire en essayant de s'inspirer du principe des 5 zéros : « zéro stock, zéro défaut, zéro papier, zéro panne, zéro délai ».
Décisions de production
L'organisation de la production diffère selon les entreprises et leur environnement : et plus particulièrement en fonction de la clientèle, des fournisseurs, de la nature du produit et des quantités à réaliser. « Les décisions de production se situent à deux niveaux : Niveau stratégique avec le choix d'un mode de production et d'une politique de production . Niveau opérationnel, soit l'ensemble des décisions de court terme prises dans le cadre résultant des choix précédents »[1].
Choix du mode de production
- Les besoins du marché et les exigences de la clientèle en matière de qualité et de diversité pèsent fortement sur la configuration des modes de production.
- Lorsque l'ensemble des paramètres dessinent un profil de produit plutôt stable, peu différencié ou simple, le cycle de vie du produit a tendance à s'allonger et à durer, conduisant le système de production vers un profil analogue : C'est-à-dire produisant des produits plutôt standardisés, en s'efforçant de produire les volumes requis en optimisant les coûts.
- Au contraire, lorsque le profil produit fait place à davantage de variété (largeur et profondeur de gamme) voire de volatilité (effet de mode), le cycle de vie des produits peut être considérablement raccourci contraignant le système de production à favoriser flexibilité et mise en œuvre rapide de la créativité et de l'innovation. (time to market)
- La technologie offre une large palette de choix possibles pour fabriquer le mieux possible à condition que le cahier des charges de fabrication ou le Plan industriel et commercial (PIC) soit suffisamment explicité.
Faible quantité | Grande quantité | |
---|---|---|
Produit unique | (1) Production par projet (ex: ouvrage d'art) | (2) Production en continu (ex: électricité) |
Produits multiples | (4) Production de petites séries (ex:outillages spécialisés) | (3) Production de masse (ex:électroménager) |
Cette typologie est inspirée de celle de Joan Woodward et commentée par T.Alberto et P.Combemale [2]
- La production par projet : « l'objet à réaliser est souvent complexe et/ou de haute technicité ( ouvrage d'art, navire, satellite...). Les problèmes majeurs à résoudre ressortissent aux coûts et aux délais (chemin critique du projet). L'accent est mis sur les fonctions Études et Ordonnancement. L'organisation est conditionnée par l'impératif de flexibilité. »
- La production en continu: « il s'agit de réaliser un flux de produits ( hydrocarbures, électricité, sidérurgie ...) en fonction d'un objectif de volume qui oriente les choix techniques et détermine en grande partie les coûts. L'intégration des opérations est souvent un impératif, ce qui explique le fort degré d'automatisation des processus. Ainsi la raffinerie BP (British Pétroleum) de Dunkerque est prévue pour fonctionner après modernisation avec 3 opérateurs, au lieu de 70 ! [3]». Ce type de configuration est très peu flexible, ce qui peut poser problème en cas de variation brusque ou importante (à la hausse ou à la baisse) de la demande. (Voir la Loi de King.)
- La production de masse : « L'objectif est de réaliser des produits standardisés en très grande quantité afin de bénéficier d'économies d'échelle. Les équipements sont spécialisés par opérations et/ou type de produits. C'est le domaine par excellence du travail à la chaine avec une main-d'œuvre peu qualifiée ». Une telle organisation n'est pas non plus particulièrement flexible.
- La production de petites séries : « C'est une situation intermédiaire entre la production par projet et la production de masse. Le système est alors organisé en ateliers spécialisés (par opération et/ou par produit) où sont regroupés des équipements polyvalents et une main-d'œuvre qualifiée. Un arbitrage doit être réalisé entre productivité ( compétitivité par les coûts) et flexibilité ( pour répondre à des demandes spécifiques et tenir les délais.) Ce système en réalité hybride peut évoluer vers la production de masse si la demande se stabilise et les volumes augmentent. Dans le cas inverse, il tend vers une organisation par projet.»
Une même entreprise peut recourir à l'un voire à simultanément plusieurs de ces types si la multiplicité ou la complexité de ses activités de production l'exigent : Organisation par projet pour la confection d'un prototype, Ateliers spécialisés pour la fabrication de certains composants, chaîne d'assemblage au stade final.
Choix de la politique de production
- L'entreprise doit choisir la façon dont la politique de fabrication s'articule avec la demande de biens ou de services qui lui est adressée. Cette articulation peut être modulée selon différentes formules[4] :
- La fabrication à la commande repose sur l'existence d'une logique -sinon d'un lien- directe entre l'ordonnateur (le client) et l'exécution.
- La fabrication sur stock établit une “zone tampon” entre les produits demandés par le client et le système qui les fabrique ou les approvisionne.
- L'assemblage à la commande organise un lien mixte fait de réactivité (travail d'assemblage à la commande) et anticipation (stocks de composants).
- La différenciation retardée qui consiste à stocker les produits sous forme d'en cours relativement élaborés qui ne sont finalisés qu'à la commande effective du client. Ce procédé ouvrant la porte à une personnalisation de “dernière minute” en fonction d'une demande client particulière.
- L'entreprise doit également trancher l'alternative suivante : Soit fabriquer en interne la totalité du produit et/ou service ; soit confier certaines activités à des entreprises “extérieures”. Les arguments pesant sur la décision sont donnés par la question de la maitrise du savoir-faire, la structure des coûts, les volumes en cause ainsi que des considérations relevant de la politique générale (Contrôle des activités en amont ou en aval, Stratégies d'alliance, degré de flexibilité ...). La décision de recourir à la sous-traitance est l'une des décisions majeures se posant aux responsables d'une entreprise[2].
Arbitrage entre des objectifs multiples et contradictoires
Au stade de l'exécution, les contraintes ressources et moyens se manifestent et nécessitent une hiérarchisation claire des priorités d'application, notamment entre les notions de volume produit, de coût, de délai et de qualité, qui spontanément sont le plus souvent antagonistes. Par exemple :
- Priorité à la qualité peut s'opposer à la réduction des coûts ou des délais.
- Priorité au délai peut contredire l'objectif de qualité, de coût, voire de volume produit.
- Priorité au coût est rarement compatible avec la recherche de qualité, voire le raccourcissement des délais
- Priorité au volume génère des contraintes assez strictes qui ne facilitent pas une véritable optimisation d'autres objectifs.
La solution pratique pour sortir de la quadrature du cercle consiste à fixer un objectif prioritaire parmi les quatre et à considérer les autres comme des contraintes à respecter (selon une certaine hiérarchie ou non). Ce qui implique la définition pour chacune de ces contraintes de respect de niveaux souhaitables ou impératifs. Exemple : L'objectif premier peut être le volume produit,
avec en contrainte 1 le respect d'un niveau de coût,
en contrainte 2 le respect d'un niveau de qualité,
et en contrainte 3 le respect d'un niveau de délai.
Décisions de mise en œuvre au quotidien
Les tâches de planification et d'ordonnancement des fabrications conduisent quotidiennement ou en tout cas périodiquement à déterminer l'ajustement souhaitable dans le cadre des micro-décisions propres au domaine de la fabrication.
- Comment produire ? : Le bureau d'études ou le service Méthodes ont à déterminer les conditions les plus appropriées dans le cadre du système existant et notamment le choix des équipements, outillages et ressources en fonction des nomenclatures et gammes de fabrication.
- Combien et Quand produire ? : Planning et ordonnancement établissent les programmes de fabrication qui optimisent disponibilité, capacité et délai de mise à disposition constatés.
Ces décisions de court-terme doivent en cas de difficulté faire l'objet d'une prise de recul pour intervenir en amont sur d'autres décisions -opérationnelles ou non- d'un échelon plus élevé, comme la remise en cause des produits à fabriquer (composition de la Gamme des produits), l'adaptation des ressources en personnel ou en capacité de production (recours à sous-traitance de capacité ou de spécificité, ou changement des procédés de maintenance...), ou la clarification ou la révision des exigences “qualité”, ou enfin l'amélioration du système d'information de la production.
Organisation de la production
Typologie des ateliers de production
Il existe plusieurs types d'ateliers de production :
- l'atelier à postes de charge (machines ou postes de travail manuel) isolés, en anglais jobshop ; la production y est discontinue ; certains postes peuvent être regroupés en îlots. (voir : Technologie de groupe),
- l'atelier à flux continu, en anglais flowshop, dont les postes sont mis en ligne (chaîne),
- l'atelier ou la cellule flexible, à production discontinue, dont les transferts entre postes sont automatisés.
Modes d'organisation de la gestion des flux
Plusieurs types de gestion des flux sont pratiqués :
- flux poussés :
- Lorsqu'une étape de la production d'un produit est terminée, le produit est « poussé » vers l'étape suivante. C'est la disponibilité du produit venant de l'amont qui déclenche l'étape suivante de fabrication. Cette méthode de production implique le stockage des produits finis avant leur commercialisation. Par exemple, l'industrie sucrière n'est pas maîtresse des périodes de récolte des betteraves, qui, par ailleurs, consomment leur sucre une fois récoltées. Il faut donc les transformer au fur et à mesure de leur disponibilité et stocker le sucre, sans se préoccuper des ventes.
- flux tirés :
- Le déclenchement d'une étape de fabrication d'un produit ne peut se faire que s'il y a une demande par l'étape suivante.
- La méthode kanban : méthode de gestion des réapprovisionnements des épiceries, dont l'application à la production industrielle, notoirement d'origine japonaise, consiste à créer un circuit d'étiquettes (kanbans), les unes accompagnant les conteneurs des produits gérés, les autres s'accumulant sur un tableau jusqu'au déclenchement du réapprovisionnement. Avec la méthode kanban, c'est l'aval (le client) qui commande l'amont (le fournisseur).
- flux tendus :
- Le travail en flux tendu est équivalent au travail avec le minimum de stocks et d'en-cours. Souvent employée dans le cas de flux tirés, l'expression est synonyme de « mise en ligne » et peut tout aussi bien s'appliquer aux flux poussés qu'aux flux tirés.
Modes de Gestion des stocks
Les modes de gestion des stocks peuvent se classer en trois grandes catégories :
- production sur stock, à partir d'un seuil, ou quantité minimum de réapprovisionnement,
- production juste à temps, type kanban, en appel par l'aval,
- production à la demande, sur commande.
Pilotage de la production
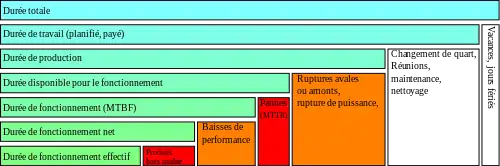
Tâches de planification
Les principales méthodes de planification sont :
- la méthode PERT (initiales de l'anglais Project Evaluation and Review Technique, litt. « technique d’évaluation et d’examen de projets ») : méthode de planification de projet permettant de définir les tâches et délais d’un projet et d’en assurer le suivi (inaugurée par la marine des États-Unis dans les années 1950).
- le calcul MRP (initiales de l'anglais Materials Requirement Planning, litt. « planification des besoins en matières ») : Développée dans les années 1960, elle calcule les approvisionnements en fonction des besoins prévisionnels en produits finis[5]. La méthode reste classique dans sa conception. Les prévisions de vente sont traduites en planification de production et par la suite en détermination des besoins (matières, composants, main-d'œuvre). Sa flexibilité - moyennant un appui fort d'informatisation dans la réalisation des calculs - la rend particulièrement bienvenue pour planifier les activités présentant un caractère saisonnier.
- la méthode OPT[6] (initiales de l'anglais Optimized Production Technology, litt. « techniques de production optimisée ») est à la fois une méthode et un type de logiciel d'ordonnancement.
- Elle repose sur un compromis entre les logiques « flux poussés » et « flux tirés ». C'est une planification des ordres de fabrication en priorité sur les outils de production à capacité limitée[7].
- À partir de la demande client évaluée par les prévisions commerciales, il s'agit de détecter les goulots d'étranglement prévisibles (c'est-à-dire les postes de travail les plus chargés) et d'en déduire les stocks de sécurité pertinents.
- Puis lorsque se déclenchent les commandes clients, on lance l'activité des postes en situation de forte charge (goulots d'étranglement) puis celle des autres postes, en remontant vers l'amont.
Tâches d'ordonnancement
L'ordonnancement se charge de lancer les ordres de fabrication ou d'achat (ou autres suivant le type de valeur ajoutée de l'entreprise) auprès du service concerné, à la date prévue.
Système d'information de la production
Enregistrement et traçabilité des données de production
Contrôle de la production
Le contrôle de la production se fait généralement sur le plan qualité et le plan prix de revient.
Voir aussi :
Méthodes, outils et progiciels
Les différentes méthodes, ou principes de gestion de la production sont de plus en plus souvent accompagnés d'outils dédiés à leur mise en œuvre pratique.
Méthodes
- Planification des besoins en composants ;
- SMED (single minute exchange of die) ;
- le principe des 5S (rangement efficace du matériel) ;
- la TPM, Maintenance Productive Totale ;
- la théorie des contraintes (TOC) ;
- le Lean Management, l'entreprise « agile » (issu du Toyota Production System) ;
- le kanban : autorégulation de la production en fonction des quantités consommées (T. Ohno, 1959) ;
- la gestion de projet ;
- la gestion par affaire.
Outils
- Diagramme de Gantt et Réseau PERT pour la gestion de projet ;
- Diagramme de Pareto pour la gestion de la qualité ;
- Réseaux de Petri pour les enchaînements automatisés ;
- Fiches de production ou de manutention sous forme d'étiquettes kanban.
Progiciels
- progiciels ou logiciels de gestion de la production assistée par ordinateur ;
- progiciels de gestion des processus industriels (monitoring de la production en temps réel) : MES ;
- progiciels de visualisation, d’analyse et d’optimisation des systèmes de production et des processus logistiques ;
- progiciels de gestion intégrés : PGI ou ERP ;
- progiciels de gestion de projet ;
- superviseurs servant à l'acquisition de données ou au pilotage.
Gestion de la production spécifique aux services
Une gestion spécifique s'est développée progressivement afin de faire face aux particularités de la production de services. Le caractère immatériel et périssable des services ainsi que leur inséparabilité et leur variabilité (liée à celle de la relation prestataire-client) imposent la recherche d'un mode de production adapté. Celui-ci, après une phase de conception associant marketing et technique, se développe à travers un front office (en interaction avec le client) et un back-office (ou back-stage), invisible au client et impliquant des activités souvent répétitives[8].
Notes et références
- Pascal Combemale et T. Alberto, Comprendre l'entreprise : théorie, gestion, relations sociales, Paris, Nathan, , 155 p. (ISBN 2-09-180096-1, OCLC 29584110, lire en ligne)
- Comprendre l'Entreprise, op. cit.
- l'Usine nouvelle, 12 septembre 1991
- Pierre Baranger et Guy Huguel, Gestion de la production, acteurs, techniques et politiques, Paris, Vuibert, coll. « Vuibert gestion », , 368 p. (ISBN 2-7117-7631-X et 9782711776313, BNF 34973663).
- J. Orlicky, 1975
- P. Baranger, Gestion de la production, Vuibert Entreprise, 1987.
- E. Goldratt, 1969.
- G. Bressy et C. Konkuyt, Management et économie des entreprises, Éd. Dalloz Sirey, 2014, 11e édition, chap. 16 et 17.
Voir aussi
Articles connexes
- Gestion des opérations
- Gestion de la production assistée par ordinateur
- progiciel de gestion intégré : PGI ou ERP
- Manufacturing execution system
- Gestion des ressources humaines, flexibilité des ressources humaines
- Gestion des stocks
- Gestion des flux
- Chaîne de production
- Réactivité industrielle
- Gestion de projet
- Gestion de la qualité
- Sécurité
- Sûreté de fonctionnement
- Portail du management
- Portail de la production industrielle