Reasons for Keeping Inventory
In many cases (such as retail), a business must have its product on hand in order to complete a sale. For these companies, the reason for keeping one of each item on hand (in inventory) is that it enables them to make sales and capture revenue. However, many businesses keep more than one of every item on hand and also keep raw materials and unfinished goods on stock in factories. Why do they do this?
There are three basic reasons for keeping an inventory:
- Time: The time lags present in the supply chain, from supplier to user at every stage, requires that you maintain certain amounts of inventory to use in this lead time. However, in practice, inventory is to be maintained for consumption during variations in lead time. Lead time itself can be addressed by ordering that many days in advance.
- Uncertainty: Inventories are maintained as buffers to meet uncertainties in demand, supply and movements of goods.
- Economies of scale: Ideal condition of "one unit at a time, at a place where a user needs it, when he needs it" principle tends to incur lots of costs in terms of logistics. So bulk buying, movement and storing brings in economies of scale, thus inventory. All these stock reasons can apply to any owner or product.
Managing Inventory
Inventory management is primarily about specifying the location and amount of stocked goods. Optimizing inventory management requires balancing many factors, including:
- Replenishment lead time
- Carrying costs of inventory
- Asset management
- Inventory forecasting
- Inventory valuation
- Inventory visibility
- Future inventory price forecasting
- Physical inventory
- Available physical space for inventory
- Quality management
- Replenishment
- Returns and defective goods
- Demand forecasting
Balancing these competing requirements leads to optimal inventory levels, which is an on-going process as the business needs to react to the wider environment. Optimal inventory levels are those that maximize profit from sales, while minimizing cost from storage, shipping, and working capital deployment.
While accountants often discuss inventory in terms of goods for sale, other organizations (such as manufacturers, service-providers and not-for-profits) also have inventories (fixtures, furniture, supplies, etc.) that they do not intend to sell. Manufacturers', distributors', and wholesalers' inventory tends to cluster in warehouses. Retailers' inventory may exist in a warehouse or in a shop or store accessible to customers. Inventories not intended for sale to customers or to clients may be held in any premises an organization uses. Stock ties up cash and, if uncontrolled, it will be impossible to know the actual level of stocks, and therefore impossible to control them.
Stages of Inventory
While the reasons for holding stock were covered earlier, most manufacturing organizations usually divide their "goods for sale" inventory into:
- Raw materials: materials and components scheduled for use in making a product
- Work in process (WIP): materials and components that have began their transformation to finished goods
- Finished goods: goods ready for sale to customers
- Goods for resale: returned goods that are salable
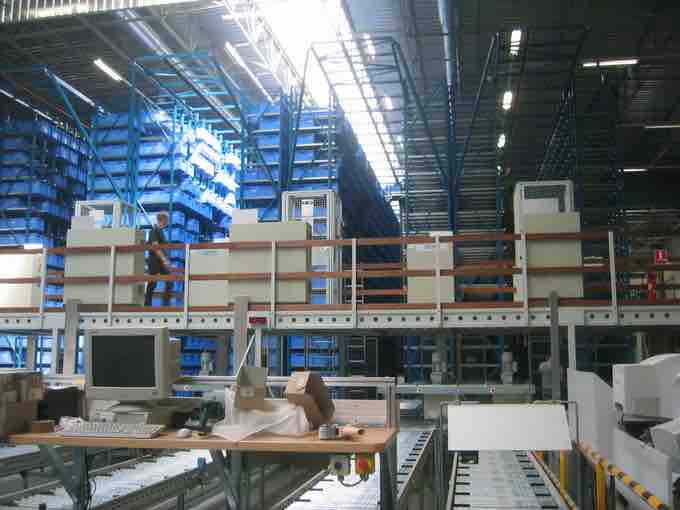
Inventory
Inventory in a warehouse