Quality can be thought of as the degree to which performance of a product or service meets or exceeds expectations. Quality control is a process that evaluates output against a standard and takes corrective action when output doesn't meet these predetermined standards. Therefore, quality control in relation to customers would be the continuous act of making sure products, designed and manufactured, are produced to meet and exceed the needs of customers. For contract work, particularly work awarded by government agencies, quality control issues are among the top reasons for not renewing a contract .
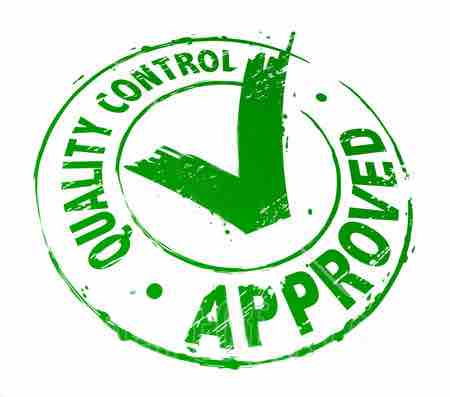
quality control
The purpose of quality control is to make sure that certain processes are performing up to a company's set standards.
This approach places an emphasis on three aspects:
- Elements such as controls, job management, defined and well-managed processes, performance and integrity criteria, and identification of records
- Competence, such as knowledge, skills, experience, and qualifications
- Soft elements, such as personnel integrity, confidence, organizational culture, motivation, team spirit, and quality relationships
Controls include product inspection, where every product is examined visually, often using a stereo microscope for fine detail before the product is sold on the external market. Inspectors will be provided with lists and descriptions of unacceptable product defects such as cracks or surface blemishes.
An emphasis on quality control heightened during World War II. At that time quality control evolved to quality assurance and is now better known as a Strategic Approach, a tool for improving not only products but also processes and services. Quality should be measured differently for products and services, and judged by their own set of dimensions. Responsibility for overall quality lies with top management. Top management must establish strategies, institute programs for quality, and motivate managers and workers. Most of the time, managers aim to improve or maintain the quality of an organization as a whole; this is referred to as Total Quality Management (TQM). TQM involves a continual effort for quality improvement by everyone in an organization. The entire supply chain must be involved for an organization to meet and exceed goals of quality control.