Vehicle armour
Military vehicles are commonly armoured (or armored; see spelling differences) to withstand the impact of shrapnel, bullets, shells, rockets, and missiles, protecting the personnel inside from enemy fire. Such vehicles include armoured fighting vehicles like tanks, aircraft, and ships.
Civilian vehicles may also be armoured. These vehicles include cars used by officials (e.g., presidential limousines), reporters and others in conflict zones or where violent crime is common. Civilian armoured cars are also routinely used by security firms to carry money or valuables to reduce the risk of highway robbery or the hijacking of the cargo.
Armour may also be used in vehicles to protect from threats other than a deliberate attack. Some spacecraft are equipped with specialised armour to protect them against impacts from micrometeoroids or fragments of space debris. Modern aircraft powered by jet engines usually have them fitted with a sort of armour in the form of an aramid composite kevlar bandage around the fan casing or debris containment walls built into the casing of their gas turbine engines to prevent injuries or airframe damage should the fan, compressor, or turbine blades break free.[1]
The design and purpose of the vehicle determines the amount of armour plating carried, as the plating is often very heavy and excessive amounts of armour restrict mobility. In order to decrease this problem, some new materials (nanomaterials) and material compositions are being researched which include buckypaper,[2] and aluminium foam armour plates.[3]
Materials
Steel
Rolled homogeneous armour is strong, hard, and tough (does not shatter when struck with a fast, hard blow). Steel with these characteristics are produced by processing cast steel billets of appropriate size and then rolling them into plates of required thickness.[4] Rolling and forging (hammering the steel when it is red hot) irons out the grain structure in the steel, removing imperfections which would reduce the strength of the steel.[5] Rolling also elongates the grain structure in the steel to form long lines, which enable the stress the steel is placed under when loaded to flow throughout the metal, and not be concentrated in one area.[6]
Aluminium
.jpg.webp)
Aluminium is used when light weight is a necessity. It is most commonly used on APCs and armoured cars. While certainly not the strongest metal, it is cheap, lightweight, and tough enough that it can serve as easy armour.
Iron
Wrought iron was used on ironclad warships. Early European iron armour consisted of 10 to 12.5 cm of wrought iron backed by up to one meter of solid wood. It has since been replaced by steel due to steel being significantly stronger.
Titanium
Titanium has almost twice the density of aluminium, but can have a yield strength similar to high strength steels, giving it a high specific strength. It also has a high specific resilience and specific toughness. So, despite being more expensive, it finds an application in areas where weight is a concern, such as personal armour and military aviation. Some notable examples of its use include the USAF A-10 Thunderbolt II and the Soviet/Russian-built Sukhoi Su-25 ground-attack aircraft, utilising a bathtub-shaped titanium enclosure for the pilot, as well as the Soviet/Russian Mil Mi-24 attack helicopter.
Uranium
Because of its high density, depleted uranium can also be used in tank armour, sandwiched between sheets of steel armour plate. For instance, some late-production M1A1HA and M1A2 Abrams tanks built after 1998 have DU reinforcement as part of the armour plating in the front of the hull and the front of the turret, and there is a program to upgrade the rest (see Chobham armour).
Plastic
Plastic metal was a type of vehicle armour originally developed for merchant ships by the British Admiralty in 1940. The original composition was described as 50% clean granite of half-inch size, 43% of limestone mineral, and 7% of bitumen. It was typically applied in a layer two inches thick and backed by half an inch of steel.
Plastic armour was highly effective at stopping armour piercing bullets because the hard granite particles would deflect the bullet, which would then lodge between plastic armour and the steel backing plate. Plastic armour could be applied by pouring it into a cavity formed by the steel backing plate and a temporary wooden form.
Some main battle tank (MBT) armour utilises polymers, for example polyurethane as used in the "BDD" applique armour applied to modernized T-62 and T-55.
Glass
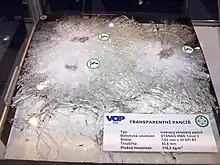
Bulletproof glass is a colloquial term for glass that is particularly resistant to being penetrated when struck by bullets. The industry generally refers to it as bullet-resistant glass or transparent armour.
Bullet-resistant glass is usually constructed using a strong but transparent material such as polycarbonate thermoplastic or by using layers of laminated glass. The desired result is a material with the appearance and light-transmitting behaviour of standard glass, which offers varying degrees of protection from small arms fire.
The polycarbonate layer, usually consisting of products such as Armormax, Makroclear, Cyrolon, Lexan or Tuffak, is often sandwiched between layers of regular glass. The use of plastic in the laminate provides impact-resistance, such as physical assault with a hammer, an axe, etc. The plastic provides little in the way of bullet-resistance. The glass, which is much harder than plastic, flattens the bullet and thereby prevents penetration. This type of bullet-resistant glass is usually 70–75 mm (2.8–3.0 in) thick.
Bullet-resistant glass constructed of laminated glass layers is built from glass sheets bonded together with polyvinyl butyral, polyurethane or ethylene-vinyl acetate. This type of bullet-resistant glass has been in regular use on combat vehicles since World War II; it is typically about 100–120 mm (3.9–4.7 in) thick and is usually extremely heavy.
Newer materials are being developed. One such, aluminium oxynitride, is much lighter but at US$10–15 per square inch is much more costly.
Ceramic
Ceramic's precise mechanism for defeating HEAT was uncovered in the 1980s. High speed photography showed that the ceramic material shatters as the HEAT round penetrates, the highly energetic fragments destroying the geometry of the metal jet generated by the hollow charge, greatly diminishing the penetration. Ceramic layers can also be used as part of composite armour solutions. The high hardness of some ceramic materials serves as a disruptor that shatters and spreads the kinetic energy of projectiles.
Composite
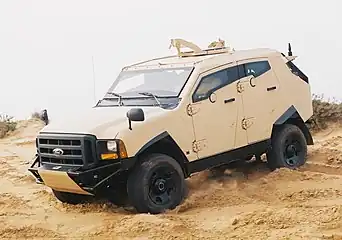
Composite armour is armour consisting of layers of two or more materials with significantly different physical properties; steel and ceramics are the most common types of material in composite armour. Composite armour was initially developed in the 1940s, although it did not enter service until much later and the early examples are often ignored in the face of newer armour such as Chobham armour. Composite armour's effectiveness depends on its composition and may be effective against kinetic energy penetrators as well as shaped charge munitions; heavy metals are sometimes included specifically for protection from kinetic energy penetrators.
Composite armour used on modern Western and Israeli main battle tanks largely consists of non-explosive reactive armour (NERA) elements - a type of Reactive armour. These elements are often a laminate consisting of two hard plates (usually high hardness steel) with some low density interlayer material between them. Upon impact, the interlayer swells and moves the plates, disrupting heat 'jets' and possibly degrading kinetic energy projectiles. Behind these elements will be some backing element designed to stop the degraded jet or projectile element, which may be of high hardness steel, or some composite of steel and ceramic or possibly uranium.
Soviet main battle tanks from the T-64 onward utilised composite armour which often consisted of some low density filler between relatively thick steel plates or castings, for example Combination K.[7] For example, the T-64 turret had a layer of ceramic balls and aluminum sandwiched between layers of cast steel armor,[8] whilst some models of the T-72 features a glass filler called "Kvartz". The tank glacis was often a sandwich of steel and some low density filler, either textolite (a fibreglass reinforced polymer) or ceramic plates.[9] Later T-80 and T-72 turrets contained NERA elements, similar to those discussed above.[10][11]
Ships

Belt armour is a layer of armour-plating outside the hull (watercraft) of warships, typically on battleships, battlecruisers, cruisers and some aircraft carriers.[12]
Typically, the belt covers from the deck down someway below the waterline of the ship. If built within the hull, rather than forming the outer hull, it can be fitted at an inclined angle to improve the protection.
When struck by a shell or torpedo, the belt armour is designed to prevent penetration, by either being too thick for the warhead to penetrate, or sloped to a degree that would deflect either projectile. Often, the main belt armour was supplemented with a torpedo bulkhead spaced several meters behind the main belt, designed to maintain the ship's watertight integrity even if the main belt were penetrated.
The air-space between the belt and the hull also adds buoyancy. Several wartime vessels had belt armour that was thinner or shallower than was desirable, to speed production and conserve resources.
Deck armour on aircraft carriers is usually at the flight deck level, but on some early carriers was at the hangar deck. (See armoured flight deck.)
Aircraft
Armour plating is not common on aircraft, which generally rely on their speed and maneuverability to avoid attacks from enemy aircraft and ground fire, rather than trying to resist impacts. Additionally, any armour capable of stopping large-calibre anti-aircraft fire or missile fragments would result in an unacceptable weight penalty. So, only the vital parts of an aircraft, such as the ejection seat and engines, are usually armoured. This is one area where titanium is used extensively as armour plating. For example, in the American Fairchild Republic A-10 Thunderbolt II and the Soviet-built Sukhoi Su-25 ground attack aircraft, as well as the Mil Mi-24 Hind ground-attack helicopter, the pilot sits in a titanium enclosure known as the "bathtub" for its shape. In addition, the windscreens of larger aircraft are generally made of impact-resistant, laminated materials, even on civilian craft, to prevent damage from bird strikes or other debris.
Armoured fighting vehicles
The most heavily armoured vehicles today are the main battle tanks, which are the spearhead of the ground forces, and are designed to withstand anti-tank guided missiles, kinetic energy penetrators, high-explosive anti-tank weapons, NBC threats and in some tanks even steep-trajectory shells. The Israeli Merkava tanks were designed in a way that each tank component functions as added back-up armour to protect the crew. Outer armour is modular and enables quickly replacing damaged parts.
Layout
For efficiency, the heaviest armour on an armoured fighting vehicle (AFV) is placed on its front. Tank tactics require the vehicle to always face the likely direction of enemy fire as much as possible, even in defence or withdrawal operations.
Sloping and curving armour can both increase its protection. Given a fixed thickness of armour plate, a projectile striking at an angle must penetrate more armour than one impacting perpendicularly. An angled surface also increases the chance of deflecting a projectile. This can be seen on v-hull designs, which direct the force of an Improvised explosive device or landmine away from the crew compartment, increasing crew survivability.[13]
Spall liners
Beginning during the Cold War, many AFVs have spall liners inside of the armour, designed to protect crew and equipment inside from fragmentation (spalling) released from the impact of enemy shells, especially high-explosive squash head warheads. Spall liners are made of aramids (Kevlar, Twaron), UHMWPE (Dyneema, Spectra Shield), or similar materials.
Appliqué

Appliqué armour,[14] or add-on armour, consists of extra plates mounted onto the hull or turret of an AFV. The plates can be made of any material and are designed to be retrofitted to an AFV to withstand weapons that can penetrate the original armour of the vehicle.[15][16] An advantage of appliqué armour is the possibility to tailor a vehicle's protection level to a specific threat scenario.
Improvised
Vehicle armour is sometimes improvised in the midst of an armed conflict by vehicle crews or individual units. In World War II, British, Canadian and Polish tank crews welded spare strips of tank track to the hulls of their Sherman tanks.[17] U.S. tank crews often added sand bags in the hull and turrets on Sherman tanks, often in an elaborate cage made of girders. Some Sherman tanks were up-armoured in the field with glacis plates and other armour cut from knocked-out tanks to create Improvised Jumbos, named after the heavily armoured M4A3E2 assault tank. In the Vietnam War, U.S. "gun trucks" were armoured with sandbags and locally fabricated steel armour plate.[18] More recently, U.S. troops in Iraq armoured Humvees and various military transport vehicles with scrap materials: this came to be known as "hillbilly armour" or "haji armour" by the Americans.[17] Moreover, there was the Killdozer incident, with the modified bulldozer being armoured with steel and concrete composite, which proved to be highly resistant to small arms.
Spaced

Armour with two or more plates spaced a distance apart, called spaced armour, has been in use since the First World War, where it was used on the Schneider CA1 and Saint-Chamond tanks. Spaced armour can be advantageous in several situations. For example, it can reduce the effectiveness of kinetic energy penetrators because the interaction with each plate can cause the round to tumble, deflect, deform, or disintegrate. This effect can be enhanced when the armour is sloped. Spaced armour can also offer increased protection against HEAT projectiles. This occurs because the shaped charge warhead can detonate prematurely (at the first surface), so that the metal jet that is produced loses its coherence before reaching the main armour and impacting over a broader area. Sometimes the interior surfaces of these hollow cavities are sloped, presenting angles to the anticipated path of the shaped charge's jet in order to further dissipate its power. Taken to the extreme, relatively thin armour plates, metal mesh, or slatted plates, much lighter than fully protective armour, can be attached as side skirts or turret skirts to provide additional protection against such weapons. This can be seen in middle and late-World War II German tanks, as well as many modern AFVs. Taken as a whole, spaced armour can provide significantly increased protection while saving weight.
The analogous Whipple shield uses the principle of spaced armour to protect spacecraft from the impacts of very fast micrometeoroids. The impact with the first wall melts or breaks up the incoming particle, causing fragments to be spread over a wider area when striking the subsequent walls.
Sloped
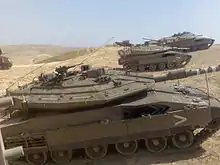
Sloped armour is armour that is mounted at a non-vertical and non-horizontal angle, typically on tanks and other armoured fighting vehicles. For a given normal to the surface of the armour, its plate thickness, increasing armour slope improves the armour's level of protection by increasing the thickness measured on a horizontal plane, while for a given area density of the armour the protection can be either increased or reduced by other sloping effects, depending on the armour materials used and the qualities of the projectile hitting it. The increased protection caused by increasing the slope while keeping the plate thickness constant, is due to a proportional increase of area density and thus mass, and thus offers no weight benefit. Therefore, the other possible effects of sloping, such as deflection, deforming and ricochet of a projectile, have been the reasons to apply sloped armour in armoured vehicles design. Another motive is the fact that sloping armour is a more efficient way of covering the necessary equipment since it encloses less volume with less material. The sharpest angles are usually seen on the frontal glacis plate, both as it is the hull side most likely to be hit and because there is more room to slope in the longitudinal direction of a vehicle.
Reactive
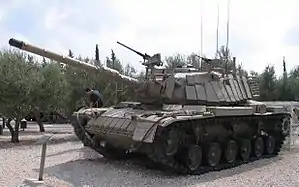
Explosive reactive armour, initially developed by German researcher Manfred Held while working in Israel, uses layers of high explosive sandwiched between steel plates. When a shaped-charge warhead hits, the explosive detonates and pushes the steel plates into the warhead, disrupting the flow of the charge's liquid metal penetrator (usually copper at around 500 degrees Celsius; it can be made to flow like water by sufficient pressure). Traditional "light" ERA is less effective against kinetic penetrators. "Heavy" reactive armour, however, offers better protection. The only example currently in widespread service is Russian Kontakt-5. Explosive reactive armour poses a threat to friendly troops near the vehicle.
Non-explosive reactive armour is an advanced spaced armour which uses materials which change their geometry so as to increase protection under the stress of impact.
Active protection systems use a sensor to detect an incoming projectile and explosively launch a counter-projectile into its path.
Slat

Slat armour is designed to protect against anti-tank rocket and missile attacks, where the warhead is a shaped charge. The slats are spaced so that the warhead is either partially deformed before detonating, or the fuzing mechanism is damaged, thereby preventing detonation entirely. As shaped charges rely on very specific structure to create a jet of hot metal, any disruption to this structure greatly reduces the effectiveness of the warhead.[19] Slat armour can be defeated by tandem-charge designs such as the RPG-27 and RPG-29.[20]
Electric armour
Electric armour is a recent development in the United Kingdom by the Defence Science and Technology Laboratory.[21][22][23][24][25][26][27] A vehicle is fitted with two thin shells, separated by insulating material. The outer shell holds an enormous electric charge, while the inner shell is at ground. If an incoming HEAT jet penetrates the outer shell and forms a bridge between the shells, the electrical energy discharges through the jet, disrupting it. Trials have so far been extremely promising, and it is hoped that improved systems could protect against KE penetrators. The developers of the Future Rapid Effect System (FRES) series of armoured vehicles are considering this technology.
See also
References
- "Containment Device: Transport Armor: Pinnacle Armor – Body Armor and Armoring Products". Pinnacle Armor. Archived from the original on September 28, 2011. Retrieved 2012-01-29.
- "Buckypaper armour". Slipperybrick.com. 2008-10-19. Archived from the original on 2012-02-17. Retrieved 2012-01-29.
- "Lightweight aluminum foam armour plates". Ntnu.no. Archived from the original on 2012-09-05. Retrieved 2012-01-29.
- Thomas, Daniel J. (October 2016). "Laser cut hole matrices in novel armour plate steel for appliqué battlefield vehicle protection". Defence Technology. 12 (5): 351–359. doi:10.1016/j.dt.2016.07.002. ISSN 2214-9147.
- Administrator, System (2009-01-27). "Advanced armour steel". The Engineer. Retrieved 2020-09-16.
- Thomas, Daniel J. (2016-10-01). "Laser cut hole matrices in novel armour plate steel for appliqué battlefield vehicle protection". Defence Technology. 12 (5): 351–359. doi:10.1016/j.dt.2016.07.002. ISSN 2214-9147.
- Foss, Christopher F., ed. (15 August 2005). Jane's Armour & Artillery, 2005-06 (26th ed.). Janes Information Group. p. 102. ISBN 978-0-7106-2686-8.
- Zaloga, Steven J. (21 July 2022). Tanks at the Iron Curtain 1960–75. Bloomsbury Publishing. p. 44. ISBN 978-1-4728-4817-8.
- Warford, James M. (January–February 1998). Blakely, LTC Terry A.; Clemens, Jon T. (eds.). "Soviet-Russian Tank Turret Armor: The Cold War Shell-Game". Armor: The Professional Bulletin of the Armor Branch. U.S. Army Armor Center, 4401 Vine Grove, Fort Knox, KY 40121: U.S. Armor Association. CVII (1): 16–18. ISSN 0004-2420. Retrieved 1 October 2023.
{{cite journal}}
: CS1 maint: location (link) - "T80 Tank Characteristics". Military Analysis Network. Federation of American Scientists. Retrieved 1 October 2023.
- United States Marine Corps (1995). Soviet/Russian Armor and Artillery Design Practices: 1945-1995 (Report). Quantico, VA: Marine Corps Intelligence Activity. pp. I-92−I-93. Retrieved 1 October 2023.
- those converted from other warships
- Katzman, Joe (2007-04-26). "In Praise of Senator Biden: Survivable Rides for the Troops". Winds of Change.NET. Archived from the original on 2008-05-18. Retrieved 2012-01-29.
- Oxford English Dictionary "appliqué, n. and adj: "Ornamental needlework in which small decorative pieces of fabric are sewn or stuck on to a fabric or garment to form a pattern or trim; the practice of this as a technique or activity; (also) (a piece of) decoration or trim made in this way. Also in extended use in metalwork, and fig". adj. "Of fabric or a garment: decorated by sewing or sticking on small pieces of fabric to form a pattern or trim; (of decoration, trim, etc.) attached in this way".
- Gary W. Cooke Combat Vehicle Protection Archived 2009-02-04 at the Wayback Machine 1 August 2004. cites "FM 3-22.34 TOW Weapon System." and "FM 5-103 Survivability."
- US Patent 6962102 - Armour constructions Archived 2011-04-29 at the Wayback Machine US Patent Issued on November 8, 2005. PatentStorm Archived 2009-02-01 at the Wayback Machine, Retrieved 2009-02-04
- Moran, Michael. "Frantically, the Army tries to armour Humvees: Soft-skinned workhorses turning into death traps," MSNBC, April 15, 2004.
- Gardiner, Paul S. "Gun Trucks: Genuine Examples of American Ingenuity," Archived 2007-11-02 at the Wayback Machine Army Logistician, PB 700-03-4, Vol. 35, No. 4, July–August 2003, Army Combined Arms Support Command, Fort Lee, Virginia. ISSN 0004-2528
- "Slat Armour for Stryker". Defense-update.com. Archived from the original on 2012-01-30. Retrieved 2012-01-29.
- "BAE's LROD Cage Armor". Defenseindustrydaily.com. 2011-03-15. Archived from the original on 2012-01-29. Retrieved 2012-01-29.
- U.S. Military Uses the Force Archived 2013-04-09 at the Wayback Machine (Wired News)
- 'Star Trek' shields to protect supertanks Archived 2008-01-04 at the Wayback Machine (The Guardian)
- "'Electric armour' vaporises anti-tank grenades and shells". Archived from the original on 2008-04-23. Retrieved 2018-11-18.
- MoD Develops 'Electric Armour' Archived February 17, 2008, at the Wayback Machine
- "New Age Electric Armour – Tough enough to face modern threats". Armedforces-int.com. Archived from the original on 2009-05-02. Retrieved 2012-01-29.
- "Add-On – Reactive Armor Suits". Defense-update.com. 2006-04-25. Archived from the original on 2012-01-26. Retrieved 2012-01-29.
- "Advanced Add-on Armor for Light Vehicles". Defense-update.com. 2006-04-25. Archived from the original on 2007-10-15. Retrieved 2012-01-29.
External links
