Cascade filling system
A cascade filling system is a high-pressure gas cylinder storage system that is used for the refilling of smaller compressed gas cylinders.[1][2] In some applications, each of the large cylinders is filled by a compressor, otherwise they may be filled remotely and replaced when the pressure is too low for effective transfer. The cascade system allows small cylinders to be filled without a compressor. In addition, a cascade system is useful as a reservoir to allow a low-capacity compressor to meet the demand of filling several small cylinders in close succession, with longer intermediate periods during which the storage cylinders can be recharged.
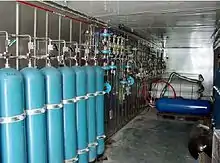
Principle of operation
When gas in a cylinder at high pressure is allowed to flow to another cylinder containing gas at a lower pressure, the pressures will equalize to a value somewhere between the two initial pressures. The equilibrium pressure is affected by transfer rate as it will be influenced by temperature, but at a constant temperature, the equilibrium pressure is described by Dalton's law of partial pressures and Boyle's law for ideal gases.
The formula for the equilibrium pressure is:
- P3 = (P1×V1+P2×V2)/(V1+V2)
- where P1 and V1 are the initial pressure and volume of one cylinder
- P2 and V2 the initial pressure and volume of the other cylinder
- and P3 is the equilibrium pressure.
An example could be a 100-litre (internal volume) cylinder (V1) pressurised to 200 bar (P1) filling a 10-litre (internal volume) cylinder (V2) which was unpressurised (P2 = 1 bar) (resulting in both cylinder equalising to approximately 180 bar (P3). If another 100-liter cylinder pressurized this time to 250 bar were then used to "top-up" the 10-liter cylinder, both of these cylinders would equalize to about 240 bar. However, if the higher pressure 100-liter cylinder were used first, the 10-liter cylinder would equalize to about 225 bar and the lower pressure 100-liter cylinder could not be used to top it up. In a cascade storage system, several large cylinders are used to bring a small cylinder up to the desired pressure, by always using the supply cylinder with the lowest usable pressure first, then the cylinder with the next lowest pressure, and so on.
In practice, the theoretical transfers can only be achieved if the gases are allowed to reach a temperature equilibrium before disconnection. This requires significant time, and a lower efficiency may be accepted to save time. Actual transfer can be calculated using the general gas equation of state if the temperature of the gas in the cylinder is accurately measured.
Uses
Breathing sets
A breathing set cylinder may be filled to its working pressure by decanting from larger (often 50 liters) cylinders. (To make this easy the neck of the cylinder of the Siebe Gorman Salvus rebreather had the same thread as an oxygen storage cylinder, but the opposite gender, for direct decanting.) The storage cylinders are available in a variety of sizes, typically from 50 litre internal capacity to well over 100 litres.[3]
In the more general case, a high-pressure hose known as a filling whip is used to connect the filling panel or storage cylinder to the receiving cylinder.
Cascade filling is often used for partial pressure blending of breathing gas mixtures for diving, to economize on the relatively expensive oxygen, for nitrox, and the even more expensive helium in trimix or heliox mixtures.[2]
Compressed natural gas fueling
Cascade storage is used at compressed natural gas (CNG) fueling stations. Typically three CNG tanks will be used, and a vehicle will first be fueled from one of them, which will result in an incomplete fill, perhaps to 2000 psig for a 3000 psig tank. The second and third tanks will bring the vehicle's tank closer to 3000 psi. The station normally has a compressor, which refills the station's tanks, using natural gas from a utility line. This prevents accidentally overfilling the tank, which could happen with a system using a single fueling tank at a higher pressure than the target pressure for the vehicle.
Hydrogen storage
In cascade storage systems for hydrogen storage, for example at hydrogen stations, fuel dispenser A draws hydrogen from tank A, while dispenser B draws fuel from hydrogen tank B. If dispenser A is over-utilized, tank A will become depleted before tank B. At this point dispenser A is switched to tank C. Tank C will then supply dispensers A and B and tank A until tank A is filled to the same pressure as tank B and the dispensers are disconnected, after which the control system will close the control valves to switch to its former state. [4]
Arrangement of system

The storage cylinders may be used independently in sequence using a portable transfer whip with a pressure gauge and manual bleed valve, to transfill the receiving cylinder until the appropriate fill pressure has been reached, or the storage cylinders may be connected to a manifold system and a filling control panel with one or more filling whips.
Ideally, each storage cylinder has an independent connection to the filling panel with a contents pressure gauge and supply valve dedicated to that cylinder, and a filling gauge connected to the filling whip, so the operator can see at a glance the next higher storage cylinder pressure compared to the receiving cylinder pressure.
The storage cylinders may be filled remotely and connected to the manifold by a flexible hose when in use, or maybe permanently connected and refilled by a compressor through a dedicated filling system, which may be automated or manually controlled.
An over-pressure safety valve is usually installed inline between the compressor and the storage units to protect the cylinders from overfilling, and each cylinder may also be protected by a rupture disc.
References
- Millar IL; Mouldey PG (2008). "Compressed breathing air – the potential for evil from within". Diving and Hyperbaric Medicine. South Pacific Underwater Medicine Society. 38: 145–51. Archived from the original on 2010-12-25. Retrieved 2009-02-28.
{{cite journal}}
: CS1 maint: unfit URL (link) - Harlow, V (2002). Oxygen Hacker's Companion. Airspeed Press. ISBN 0-9678873-2-1.
- Specialty Gas Cylinder Dimensions Archived September 11, 2008, at the Wayback Machine Air Products
- Hydrogen Fueling Station Pag 4. Archived July 26, 2007, at the Wayback Machine Broken link
External links
Media related to Cascade filling system at Wikimedia Commons