Horno de reverbero
Un horno de reverbero se caracteriza porque el calor es reflejado (reverberado) por su bóveda hacia una zona de reacción química, separada físicamente de aquella donde tiene lugar la reacción de combustión que aporta energía al sistema. En este tipo de hornos, el combustible (carbón, gas, fuel oil, etc.) se quema en una cámara separada de la de los materiales a tratar. Así, se limitan el contacto directo y las interacciones indeseables entre el combustible y los materiales a transformar o refinar.

Estos hornos, cuyo principio de funcionamiento es muy antiguo, fueron objeto de mejoras en los siglos XVIII y XIX, particularmente para optimizar los procesos de transformación metalúrgica. Una de las primeras aplicaciones fue la pudelación del arrabio, un proceso esencial durante la primera revolución Industrial. Estos hornos han sido y son utilizados en la industria metalúrgica, la cocción de cerámicas y en la industria química.
Los hornos de reverbero son de poca altura y gran longitud. En uno de los extremos se encuentra el hogar donde se quema el combustible, y en el extremo opuesto la chimenea. Las llamas y productos de la combustión atraviesan el horno y son dirigidos, por la bóveda de forma adecuada hacia la solera del horno, donde está situada la carga del metal que se desea fundir. Esta carga se calienta, no solo por su contacto con las llamas y gases calientes sino también por el calor de radiación de la bóveda del horno de reverbero.
Historia
El uso del horno de reverbero está ligado a la necesidad de sustituir el carbón vegetal por el abundante y mucho más económico carbón de hulla. Sin embargo, los vapores sulfurosos que molestaban a los que usaban el carbón estaban correctamente asociados con la fragilización del hierro por el azufre. El metalúrgico inglés John Percy, remonta el uso del horno de reverbero en metalurgia a una patente otorgada en 1613 por Jacobo I de Inglaterra a Jean Rovenzon, quien había recuperado los derechos de una patente de Simon Sturtevant, quien no había logrado materializar la idea:[1]
Se afirma que Rovenzon "practicó satisfactoriamente" lo que Sturtevant había prometido y no había cumplido; pero no hay evidencia para apoyar el hecho. El nuevo titular de la patente había compuesto un Tratado sobre metalurgia (Treatise of Metallica), "diferente del publicado por Simon Sturtevant sobre su patente". Rovenzon parece ser el inventor de los “hornos de aumento; fuegos de refinado y cámaras de calderas de desvío [sic], en las que "los materiales a fundir o forjar podrán mantenerse separados del combustible"; y describe claramente el horno de reverbero. Termina su pequeño tratado, anunciando que “[…] este nuevo invento (su) […] producirá los “mismos resultados con el carbón mineral y sus nuevos hornos, si hay una fábrica adecuada para establecer el horno en ella”. El invento del que habla probablemente fue el uso del horno de reverbero.[1]John Percy (Tratado completo de metalurgia; tomo 3, p. 14-15)
El término horno de reverbero se menciona en los tratados de química o escultura del siglo XVII para designar a un horno utilizado para fundir esmaltes o descomponer sustancias en el laboratorio, y en el que la llama no se aplica directamente al producto a calentar sino que reverbera mediante una bóveda.
En metalurgia, el horno de reverbero tal como se entiende hoy aparece en Gran Bretaña, y más precisamente en el límite de Gales e Inglaterra, en el último tercio del siglo XVII. A partir de entonces, se caracterizó por la separación entre el calentamiento y el producto a calentar y por una chimenea alta que permitía activar el hogar por tiro natural. El combustible preferido era la hulla. Se utilizaba tanto para la metalurgia extractiva (reducción de cobre o minerales de plomo, refinación de plomo argentífero) como para refundir hierro (especialmente cañones antiguos) para producir nuevas piezas de fundición.
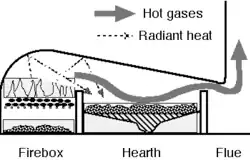
Se utilizaba en Francia para la reducción de plomo desde los años 1730, probablemente alimentado con madera; las temperaturas más bajas obtenidas de esta manera probablemente explican por qué no se usó entonces para la fusión.
Desde 1750, el horno de reverbero se asoció con los altos hornos utilizando coque para producir grandes piezas de hierro fundido (especialmente para piezas de artillería) en fábricas como Carron (Escocia) o Bersham (Gales). En 1775, la Armada francesa contrató a un maestro del hierro británico, William Wilkinson, para construir un horno de reverbero dedicado a la fabricación de piezas de artillería de fundición de hierro, creándose la Fundición d'Indret. Posteriormente se construyeron hornos del mismo tipo en Ruelle, en Angoumois y en Creusot (Borgoña).
Los hornos de reverbero se han utilizado para la fundición tanto de metales férreos como de metales no férreos, como cobre latón, bronce y aluminio. También se ha utilizado para realizar la fusión del concentrado de cobre y separar la escoria, así como para la fundición de minerales y el refinado o la fusión de metales de bajo punto de fusión como el aluminio. También se han usado en la producción de cobre, estaño y níquel, en la producción de ciertos hormigones y cementos y en el reciclado del aluminio.
Hoy en día, los hornos de reverbero no son una solución tan empleada como en el pasado, debido a la mayor disponibilidad de combustibles con mayor grado de pureza y a las normativas medioambientales, que prohíben el uso de los combustibles más contaminantes. Además, su eficiencia energética es menor por las pérdidas que supone que el mineral y el combustible no estén en contacto directo. Aun así continúan empleándose, especialmente en países menos desarrollados y con normativas de protección ambiental más laxas.
Configuración
Los hornos de reverbero han tenido varias formas. Los primeros fueron una mejora de los hornos de cuba. Permitieron el uso de combustible como la madera que producen llamas. En los primitivos hornos de reverbero, las llamas ocupan toda la cavidad del horno y en el medio se colocan los materiales a calentar. La mejora del horno de reverbero consistió en separar los combustibles de los materiales a calentar y en particular en realizar el calentamiento en un lado del horno. Además de mejorar el calentamiento, se evita mezclar los materiales metálicos con los combustibles y por lo tanto se impide que se contamine o modifique el metal así obtenido. El horno de reverbero, por lo tanto, consta de un hogar donde se quema el combustible y una cámara de trabajo donde se colocan los metales o minerales.
Diseño del horno de reverbero en los siglos XVIII y XIX
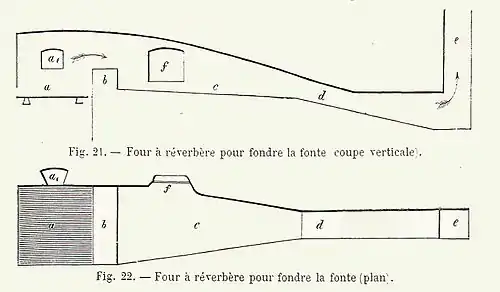
a: Rejilla
a1: Tronera
b: Altar
c: Cámara de trabajo
d: Rampa
e: Chimenea
f: Puerta que permite cargar el horno con la materia prima a tratar
(Manuel théorique et pratique de la métallurgie du fer" de Adolf Ledebur, 1895)
Un horno de reverbero consta de los siguientes elementos:
- Hogar:
- Rejilla: en la que se colocan los combustibles sólidos como el carbón o la madera. Esta rejilla está ausente si se utilizan combustibles gaseosos o líquidos.
- Cenicero: situado debajo de la rejilla para recoger las cenizas.
- Tronera: abertura provista de una puerta que permite depositar el combustible en la rejilla.
- Cámara de trabajo:
- Altar: a veces denominado puente o altar mayor (Grüner)
- Solera: la parte inferior del horno
- Puerta o hueco: provista de un portillo desmontable, permite la introducción de materiales metálicos. También permite intervenir sobre estos materiales (agitándolos mecánicamente como en el caso de la pudelación por ejemplo).
- Bóveda:
- La bóveda recubre el hogar y la cámara de trabajo, y su forma cóncava facilita que la radiación infrarroja se trasmita desde el primero hacia la segunda.
- Evacuación de gases:
- Rampa: conducción ubicada inmediatamente después de la cámara de trabajo que permite la circulación de gases.
- Compuerta: una especie de válvula que en ocasiones equipa la rampa, permitiendo así regular el caudal del gas circulante.
- Chimenea: permite la evacuación de gases. Sus dimensiones son sumamente importantes ya que condicionarán el "tiro". Dado que la mayoría de los hornos de reverbero generalmente no están equipados con un ventilador, es el tiro de la chimenea lo que determina la eficiencia del horno. Puede haber una chimenea por horno, pero en talleres con varios hornos, puede haber una chimenea común para todos los hornos.
El calor creado por la combustión pasa por encima del altar, pasa por la cámara de trabajo siguiendo la bóveda y luego es evacuado por la rampa y la chimenea.

Esquema procedente del Manuel théorique et pratique de la métallurgie du fer (Adolf Ledebur, 1895)
Rejilla
La rejilla está presente solo en hornos que utilizan combustibles sólidos, como carbón o leña. Soporta el combustible. El espaciado de las barras y sus formas permiten el flujo de cenizas hacia la parte inferior llamada cenicero, donde se facilita su retirada. Este espacio también permite la circulación del aire.
Las rejillas pueden ser horizontales, inclinadas o escalonadas. La rejilla horizontal tiene el gran inconveniente de la carga manual discontinua. Es necesario que el operario abra la cámara para cargar el horno. Esta apertura hace que el horno se enfríe. Grüner menciona un experimento de comparación entre el funcionamiento de un horno por diferentes operarios, cuyo resultado muestra diferencias de hasta el 25% en el consumo de combustible. Las rejillas inclinadas o escalonadas pueden ser alimentadas automáticamente por un dispositivo colocado fuera del horno, que permite el flujo del carbón por gravedad o por la acción de una persona.
Altar
El altar es el murete que separa la solera (y por tanto, los materiales a tratar) del combustible. A veces hay cierta ambigüedad sobre la definición exacta de esta parte. Gaspard Monge en su libro sobre la fabricación de cañones lo define como: ...la parte del horno sobre la que se coloca la masa de metal y no como la separación. Grüner lo llama en su tratado de metalurgia el puente o el altar mayor. El altar (o el puentecito) es un pequeño dique que separa la solera de la rampa. Esta separación existe en el caso de que la solera sea cóncava, impidiéndose así que el material fundido fluya hacia la rampa.
El altar está expuesto a altas temperaturas, por lo que está hecho de un material refractario. Opcionalmente puede estar equipado con medios de refrigeración. Su altura depende de su uso. Cuando se quiere proteger el metal de la llama y evitar así una acción química que modificaría su naturaleza, se construye más alto. Pero a cambio, el horno pierde parte de su eficiencia calorífica.
Solera
La solera también está hecha de materiales refractarios. Su naturaleza, forma y dimensiones dependen estrechamente del uso del horno.
Para los hornos de pudelado, en 1818 se introdujo la solera de fundición de hierro refrigerada por agua circulante. Se recubre con escoria básica, lo que mejora el refinado de la fundición.
La solera es plana cuando el horno solo se usa para calentar. Es hueca (o cóncava) cuando el horno está destinado a fundir un metal. La forma puede ser rectangular, si el operador no tiene ninguna acción que realizar durante el calentamiento u ovalada si tiene que intervenir (caso de hornos de pudelado).
En algunos casos, el calor residual del hogar se reutiliza equipando el horno con otros hogares o pasando el fundente a través de calderas de vapor.
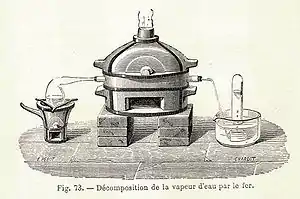
Bóveda
La bóveda, también construida con material refractario, tiene una doble misión: en primer lugar, conduce el humo caliente producido en el hogar una vez que supera el altar hacia la cámara de trabajo, donde cede su calor; y en segundo lugar, su forma abombada permite reflejar la radiación infrarroja generada por el fuego en el hogar hacia la cámara de trabajo, incrementando la temperatura de la misma.
Uso en metalurgia
El horno de reverbero se puede utilizar para varios tipos de operaciones, como la tostación (calentamiento de materiales sólidos como minerales), el recalentamiento o la fusión.
Industria siderúrgica
En siderurgia, el horno de reverbero se utilizó en todo siglo XIX en el proceso de pudelación, que permitía transformar el arrabio en hierro pudelado trabajando sobre un metal calentado hasta que se vuelve pastoso. El proceso se abandonó al comienzo del siglo XX, cuando los convertidores permitieron iniciar la producción masiva de acero.
Al comienzo de siglo XX apareció el horno de solera, que permite el afinado controlado del arrabio para producir aceros de calidad. En 1950, más de la mitad del acero mundial se producía mediante este proceso, que desapareció en la década de 1980 cuando se generalizó el convertidor de oxígeno.
Metalurgia de metales no ferrosos
El horno de reverbero se utiliza tanto para tostar como para fundir minerales. En este último cometido, compite con el alto horno. De hecho, permite la fusión de minerales de granulometría muy fina, como los de las plantas de enriquecimiento de minerales, sin ser arrastrados por los gases. Desde el final de siglo XX, debido a limitaciones ecológicas, el horno de reverbero ha ido desapareciendo, siendo reemplazado por otros procesos como el proceso de fusión flash.[2]
Tostación
El horno de reverbero está especialmente indicado para el tostado de materiales pulverulentos, que serían arrastrados por el flujo de gas si fueran tratados en un horno de cuba,[G2 1] donde además su permeabilidad al paso de los gases calientes es insuficiente.[G2 2] Aunque este método dominaba al final de siglo XIX, ya estaba desactualizado al comienzo de siglo XX. En efecto, siendo el contacto con la atmósfera caliente y oxidante relativamente bajo, el tostado es lento e incompleto, incluso si la carga se renueva regularmente.[3]
El tostado en el horno de reverbero consiste en extender una capa de 8 a 10 cm de espesor sobre la solera del horno y removerla (a mano en siglo XIX, luego automáticamente al principio de siglo XX, como en el horno Edwards). Como solo la capa superior se somete a un tostado oxidativo, es necesario efectuar un paleado manual o mecánico, pero esto a menudo es insuficiente para lograr un tostado rápido y completo. Además, los gases resultantes del tostado (como los gases sulfurosos o los óxidos de zinc) no son expulsados con fuerza del lecho de material y tienden a permanecer en los espacios entre los granos (por adsorción), lo que penaliza la progresión de la oxidación.[3] Sin embargo, este fenómeno es mucho menos penalizador en los hornos de reverbero que en otros procesos (horno de cuba, tostado en cubilote o en apilamiento) ya que los gases abandonan la carga más rápidamente. Gracias a su flexibilidad, el horno de reverbero, que permite el ajuste de la temperatura independientemente del grado de oxidación, es una herramienta popular para la desulfuración de minerales.[G2 3]
Los hornos de reverbero siguen teniendo la desventaja de su baja eficiencia térmica.[G2 4] Para mejorarla y facilitar el acceso a la carga, la solera de los hornos de tostación es larga y estrecha. En el siglo XIX, medía al menos 10 metros de largo y como máximo 2 metros de ancho. Hay dos zonas: la zona de calentamiento, cerca del puente de fuego (o altar), y la cámara de trabajo, donde el material se calienta lentamente, que es de 15 a 20 veces mayor. Los materiales son empujados desde la chimenea hacia el hogar. Por eso, para facilitar su movimiento, el suelo a veces está inclinado o está diseñado para un flujo en cascada (horno con estantes). Para obtener una rejilla oxidante, se aumentan las entradas de aire. El aire frío, más denso, circula bajo los humos, en contacto con la carga que oxida. Pero si se pretende tratar los gases de combustión (por ejemplo, para recuperar el azufre), el exceso de aire debe limitarse.[G2 1] En este caso, el volteo frecuente del producto esparcido sobre la solera debe hacerse de forma mecanizada, porque de lo contrario el acceso a la carga conduce a entradas de aire recurrentes. Se han propuesto muchos sistemas, desde hornos con estantes inclinados en los que la carga cae en cascada (horno Hasenclever) hasta hornos equipados con sistemas mecánicos de paleo.[G2 5]
Como la mayoría de los procesos de tueste, debe evitarse la sinterización para facilitar el manejo del material. Pero para el tostado de minerales de plomo, es común que la sinterización, o incluso la fusión, se lleve a cabo en el mismo horno.[G2 6] [nota 1]
![]() Horno de reverbero utilizado en 1883 para tostar mineral de plomo, entonces llamado "diseño moderno" |
![]() Horno de reverbero utilizado para tostar mineral de plata, comercializado en 1897 por la Anaconda Mining Company. |
![]() Horno de reverbero con solera inclinada a 18° (horno de Ferras), utilizado para la calcinación de cascarilla fina a principios del siglo XX |
![]() Horno de reverbero de solera múltiple (horno de mesa), utilizado a finales del siglo XIX para la tostación de minerales sulfurosos de plomo. La carga pasa sucesivamente del hogar superior al hogar inferior, circulando en sentido contrario a los humos |
![]() Vista en sección del sistema de silleta giratoria del horno Edwards, tal como se usó en 1921 |
Fundición de mineral de cobre o níquel en mate
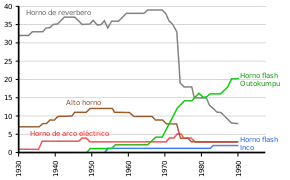
Al comienzo de siglo XXI, la fundición flash proporcionó más del 60% de la producción de cobre. Destaca frente al horno de reverbero, primero por consideraciones ecológicas, y sobre todo por el ahorro energético que permite. Durante la crisis del petróleo de 1973, lo sustituyó definitivamente.[4]
Como el horno de reverbero quema principalmente hidrocarburos, logra la fusión en un ambiente con poco oxígeno libre. La mata está poco oxidada, y por tanto contiene poco cobre, entre un 40 y un 50%. El rendimiento es bajo porque al estar el baño poco agitado, los intercambios de calor son menos efectivos. Por otro lado, la separación entre el metal y la lechada es buena: la escoria, que contiene menos del 0,6% de cobre, no se reprocesa. Finalmente, los humos de la combustión de hidrocarburos son abundantes y contienen menos del 1% de SO
2: esta concentración es demasiado baja para asegurar una desulfuración económica, y demasiado alta para ser liberada a la atmósfera.[5]
Al comienzo de siglo XXI, el horno de reverbero solo sobrevive en unas pocas fábricas. Así, de los 30 hornos de reverbero que operaban en 1984, solo 10 operaban en 2002.[5] Se utiliza para fundir minerales de cobre, que posiblemente contengan zinc, a partir de mata. Dicho horno tiene una longitud de aproximadamente 40 m y está construido principalmente con material refractario ácido (a base de sílice). Está equipado con un recuperador de calor capaz de reutilizar del 35 al 50% de la energía de los humos que se escapan del horno a 1200 °C. El bajo rendimiento térmico del horno de reverbero se compensa con el hecho de que se contenta con prácticamente cualquier combustible. Pero "una gran desventaja hace imposible el uso de tales hornos en muchas áreas habitadas: es el enorme volumen de humos producidos tanto por la combustión como por la oxidación de sulfuros. La extracción de polvo de los gases de combustión es costosa y, a menudo, incompleta debido a su volumen. Contienen gas SO
2 contaminante, pero en una concentración demasiado baja para producir ácido sulfúrico". Así, la chimenea de los hornos de reverbero de la Hudson Bay Mining and Smelting Co, en Flin Flon, mide 250 m de alto.[6]
Una configuración típica de un horno de reverbero de finales del siglo XX es el que se usa en la fundición de Onahama (Japón): 2 hornos de 9,73 x 33,55 x 3,69 m y 11,1 x 33,27 x 4,0 m, que producen 1000 tm por día de mata con un 43 % de cobre y otras tantas escorias, con el 0,6 % de cobre. Estos hornos son alimentados con mineral de cobre concentrado y con la escoria procedente de un convertidor Peirce-Smith en cantidad equivalente. El gas se desulfura en una unidad que produce yeso.[5]
Desarrollos actuales y futuros
La fusión flash a principios de siglo XXI concentra el 50% de la producción mundial de cobre y el 30% de la producción de níquel.[7] Se trata de una evolución directa del horno de reverbero.[8]
Notas
- El tostado de minerales sulfurosos de plomo es complejo. Si la oxidación es demasiado vigorosa, se forma sulfato de plomo(II) (PbSO
4), que es infusible y difícil de oxidar, que luego se reduce mezclándolo con un material carbonoso (como coque o hulla): PbSO
4(s) + C (s) → PbO (s) + SO
2(g) + CO(g)
2. Este método de alternar el calentamiento oxidante y reductor también permite eliminar el arsénico y el zinc presentes en el mineral.[G2 7]
Referencias
- Grüner, Emmanuel-Louis (1878). Dunod, ed. Traité de métallurgie — métallurgie générale. 2, procédés métallurgiques, chauffage et fusion, grillage, affinage et réduction (I).
- p. 31 ; 100 ; 106-107
- p. 83
- p. 115
- p. 32
- p. 120-121 ; 128-132
- p. 109
- p. 113-114
- Otras referencias
- Percy, John (1865). Librairie polytechnique de Noblet et Baudry éditeur, ed. Traité complet de métallurgie (traduction supervisée par l'auteur, trad.) 3. Paris.
- PdfSARA Group, ed. (janvier de 2008). «3-6 ; 3-7». Historical review of air emission from the smelting operations (en inglés).
- Corbion, Jacques (2003). «§ Grillage». En 5, ed. Le Savoir… fer — Glossaire du haut fourneau [Le langage… (savoureux, parfois) des hommes du fer et de la zone fonte, du mineur au… cokier d'hier et d'aujourd'hui] (en francés). Prefacio: Yvon Lamy.
- Korhonen, Janne M.; Välikangas, Liisa. «Constraints and Ingenuity: The Case of Outokumpu and the Development of Flash Smelting in the Copper Industry» (pdf) (en inglés). Archivado desde el original el 3 de marzo de 2016. Consultado el 21 de abril de 2022.
- Davenport, William G. I.; King, Matthew J.; Schlesinger, Marc E.; Biswas, A. K. (2002). «403-405». En Elsevier, ed. Extractive Metallurgy of Copper (en inglés) (4 edición). Oxford/New York/Tokyo. p. 432. ISBN 0-08-044029-0.
- Blazy, Pierre; Jdid, El-Aid (10 de décembre de 2001). «Pyrométallurgie et électroraffinage du cuivre - Pyrométallurgie». En Éditions techniques de l'ingénieur, ed. Techniques de l'ingénieur (en francés).
- PdfOutokumpu (ed.). «Outokumpu Flash Smelting» (en inglés). Archivado desde el original el 24 de julio de 2011. Consultado el 21 de abril de 2022.
- Queneau, Paul E.; Marcuson, Samuel W. (1996). «Oxygen Pyrometallurgy at Copper Cliff—A Half Century of Progress». The Minerals, Metals & Materials Society (en inglés). Archivado desde el original el 22 de mayo de 2015. Consultado el 21 de abril de 2022.
Bibliografía
- Jacques Corbion – Le savoir...fer : glossaire du haut fourneau – 4e édition – 11/2003 – publicado por la asociación Le savoir...fer ISBN 2-9520787-0-X, en particular los artículos Four à réverbère (página 1609, Volumen II), Calefacción puente (pág. 2627, Tomo IV), Altar (pág. 299, Tomo I), Pequeño altar (pág. 2517, Tomo III), Gran altar (pág. 1736, Tomo III ), Tisard (página 3216, Tomo IV).
- Gaspard Monge -Description de l'art de fabriquer des canons - Imprenta del comité de seguridad pública - año II (1793-1794) de la república francesa.
- E.L. Grüner: Traité de métallurgie, primer volumen, agente y aparato metalúrgico, principio de combustión. 1875, Editorial Dunod
- A. Ledebur (traducido del alemán por Barbary de Langlade revisado y anotado por F.Valton) - Manuel théorique et pratique de la métallurgie du fer - Volumen I - Librairie polytechnique Baudry et Cie, editor - 1895.
- B.Bussard, H.Dubois, Leçons élémentaires de chimie de l'enseignement secondaire des jeunes filles, quinta edición, Eugène Belin Classic Bookstore, 1906
Enlaces externos
Wikimedia Commons alberga una categoría multimedia sobre Horno de reverbero.