Moldeo por inyección
En ingeniería, el moldeo por inyección es un proceso semicontinuo que consiste en inyectar un polímero, cerámico o un metal[1] en estado fundido (o ahulado) en un molde cerrado a presión y frío, a través de un orificio pequeño llamado compuerta. En ese molde el material se solidifica, comenzando a cristalizar en polímeros semicristalinos. La pieza o parte final se obtiene al abrir el molde y sacar de la cavidad la pieza moldeada.
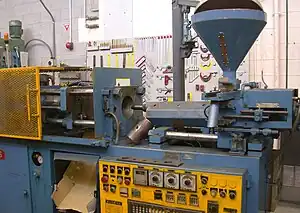
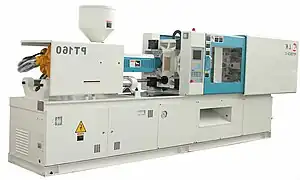
El moldeo por inyección es una técnica muy popular para la fabricación de artículos muy diferentes. Sólo en los Estados Unidos, la industria del plástico ha crecido a una tasa de 12 % anual durante los últimos 25 años, y el principal proceso de transformación de plástico es el moldeo por inyección, seguido de la extrusión. Un ejemplo de productos fabricados por esta técnica desde los años 50 son los famosos bloques incontestables LEGO y juguetes Playmobil, así como una gran cantidad de componentes de automóviles, componentes para aviones y naves espaciales.
Los polímeros han logrado sustituir otros materiales como son madera, metales, fibras naturales, cerámicas y hasta piedras preciosas; el moldeo por inyección es un proceso comparado con la fabricación de papel, la tala de árboles o cromados. Ya que no contamina el ambiente de forma directa, no emite gases ni desechos acuosos, con bajos niveles de ruido. Sin embargo, no todos los plásticos pueden ser reciclados y algunos susceptibles de ser reciclados son depositados en el ambiente, causando daños al medio ambiente.
La popularidad de este método se explica con la versatilidad de piezas que pueden fabricarse, la rapidez de fabricación, el diseño escalable desde procesos de prototipos rápidos, altos niveles de producción y bajos costos, alta o baja automatización según el costo de la pieza, geometrías muy complicadas que serían imposibles por otras técnicas, las piezas moldeadas requieren muy poco o nulo acabado pues son terminadas con la rugosidad de superficie deseada, color y transparencia u opacidad, buena tolerancia dimensional de piezas moldeadas con o sin insertos y con diferentes colores.
Antecedentes históricos
El diseño actual de la máquina de moldeo por inyección ha sido influido por la demanda de productos con diferentes características geométricas, con diferentes polímeros involucrados y colores. Además, su diseño se ha modificado de manera que las piezas moldeadas tengan un menor costo de producción, lo cual exige rapidez de inyección, bajas temperaturas, y un ciclo de moldeo corto y preciso.
John Hyatt registró en 1872 la primera patente de una máquina de inyección, la cual consistía en un pistón que contenía en la cámara derivados celulósicos fundidos. Sin embargo, se atribuye a la compañía alemana Cellon-Werkw el haber sido pionera de la máquina de inyección moderna. Esta firma presentó, en 1928, una patente incluyendo la descripción de nitrocelulosa (celuloide). Debido al carácter inflamable de la nitrocelulosa, se utilizaron posteriormente otros derivados celulósicos como el etanoato de celulosa. Los británicos John Beard y Peter Delafield, debido a ciertas diferencias en la traducción de la patente alemana, desarrollaron paralelamente la misma técnica en Inglaterra, con los derechos de patente inglesa para la compañía F.A. Hughes Ltd.
El primer artículo de producción masiva en Inglaterra fue la pluma fuente, producida durante los años treinta por la compañía Mentmore Manufacturing. La misma utilizaba máquinas de moldeo por inyección de Eckert & Ziegler (Alemania). Estas máquinas funcionaban originalmente con aire comprimido (aproximadamente 31 kg/cm²); el sistema de apertura de molde y la extracción de la pieza eran realizados manualmente, y los controles incluían válvulas manuales, sin control automático ni pantallas digitales; además, carecían de sistemas de seguridad.
El principio del moldeo
El moldeo por inyección es una de las tecnologías de procesamiento de plástico más famosas, ya que representa un modo relativamente simple de fabricar componentes con formas geométricas de alta complejidad. Para ello se necesita una máquina de inyección que incluya un molde. En este último, se fabrica una cavidad cuya forma es idéntica a la de la pieza que se desea obtener y para su tamaño se aplica un factor de contracción el cual se agrega en las medidas de la cavidad para que al enfriarse la pieza moldeada se logren las dimensiones deseadas. La cavidad se llena con plástico fundido, el cual se solidifica, manteniendo la forma moldeada.
Los polímeros conservan su forma tridimensional cuando son enfriados por debajo de su Tg —temperatura de transición vítrea— y, por tanto, también de su temperatura de fusión para polímeros semicristalinos. Los polímeros amorfos, cuya temperatura útil es inferior a su Tg, se encuentran en un estado termodinámico de pseudo equilibrio. En ese estado, no existen movimientos de rotación y de relajación (desenredo de las cadenas) del polímero. Es por esta causa que, en ausencia de esfuerzos, se mantiene la forma tridimensional. Los polímeros semicristalinos poseen, además, la característica de formar cristales. Estos cristales proporcionan estabilidad dimensional a la molécula, la cual también es —en la región cristalina— termodinámicamente estable. La entropía de las moléculas del plástico disminuye drásticamente debido al orden de las moléculas en los cristales.
Maquinaria
Las partes más importantes de la máquina son:
Unidad de inyección
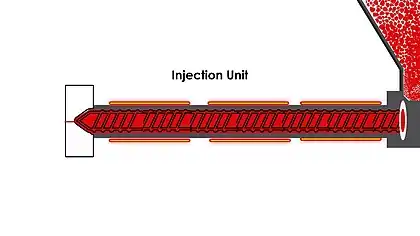
La función principal de la unidad de inyección es la de fundir, mezclar e inyectar el polímero. Para lograr esto se utilizan husillos de diferentes características según el polímero que se desea fundir. El estudio del proceso de fusión de un polímero en la unidad de inyección debe considerar tres condiciones termodinámicas:
- Las temperaturas de procesamiento del polímero.
- La capacidad calorífica del polímero Cp [cal/g °C].
- El calor latente de fusión, si el polímero es semicristalino.
El proceso de fusión necesita de un aumento de la temperatura del polímero, que resulta del calentamiento y la fricción de este con la cámara y el husillo. La fricción y esfuerzos cortantes son básicos para una fusión eficiente, dado que los polímeros no son buenos conductores de calor. Un incremento en temperatura disminuye la viscosidad del polímero fundido; lo mismo sucede al incrementar la velocidad de corte. Por ello ambos parámetros deben ser ajustados durante el proceso. Existen, además, cámaras y husillos fabricados con diferentes aleaciones de metales, para cada polímero, con el fin de evitar el desgaste, la corrosión o la degradación. Con algunas excepciones —como el PVC—, la mayoría de los plásticos pueden utilizarse en las mismas máquinas.
La unidad de inyección es en origen una máquina de extrusión con un solo husillo, teniendo la cámara calentadores y sensores para mantener una temperatura programada constante. La profundidad del canal del husillo disminuye de forma gradual (o drástica, en aplicaciones especiales) desde la zona de alimentación hasta la zona de dosificación. De esta manera, la presión en la cámara aumenta gradualmente. El esfuerzo mecánico, de corte y la compresión añaden calor al sistema y funden el polímero más eficientemente que si hubiera únicamente calentamiento, siendo ésta la razón fundamental por la cual se utiliza un husillo y no una autoclave para obtener el fundido.
Una diferencia sustancial con respecto al proceso de extrusión es que durante la dosificación el husillo retrocede transportando el material hacia la parte anterior de la cámara. Es allí donde se acumula el polímero fundido para ser inyectado. Esta cámara actúa como la de un pistón; el husillo entonces, se comporta como el émbolo que empuja el material. Tanto en inyección como en extrusión se deben tomar en cuenta las relaciones de P-V-T (Presión, Volumen, temperatura), que ayudan a entender cómo se comporta un polímero al fundir.
Unidad de cierre
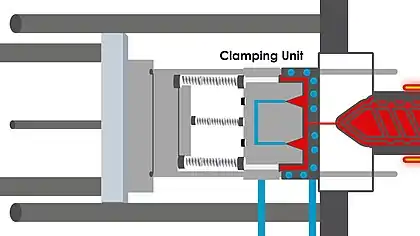
Es una prensa hidráulica o mecánica, con una fuerza de cierre suficiente para contrarrestar la fuerza ejercida por el polímero fundido al ser inyectado en el molde. Las fuerzas localizadas pueden generar presiones del orden de cientos de MPa, que únicamente se encuentran en el planeta de forma natural en los puntos más profundos del océano.
Si la fuerza de cierre es insuficiente el molde tenderá a abrirse y el material escapará por la unión del molde. Es común utilizar el área proyectada de una pieza (área que representa perpendicularmente a la unidad de cierre el total de la cavidad) para determinar la fuerza de cierre requerida, excluyendo posibles huecos o agujeros de la pieza.
Donde:
- F = Fuerza (N)
- Pm = Presión media (Pa)
- Ap = Área proyectada (m²)
El parámetro fundamental para dimensionar una unidad de cierre es su fuerza para mantener el molde cerrado. Usualmente se da este valor en toneladas (t). Otros parámetros importantes en una unidad de cierre son: la distancia mínima entre placas, la distancia máxima de apertura, las dimensiones de las placas y la distancia entre columnas, la carrera del sistema de expulsión. Estos datos se utilizan para dimensionar los moldes
Molde
Los moldes están construidos de aceros especiales de alta resistencia para que resistan altas presiones de cierre y de inyección para producción limitada. Los aspectos de construcción son similares a los moldes de compresión y de transferencia.
njection mold is a tool for producing plastic products; it is also a tool for giving plastic products complete structure and precise dimensions. Injection molding is a processing method used in the mass production of certain complex-shaped parts. Specifically, it means that the plastic melted by heat is injected into the mold cavity by high pressure from the injection molding machine, and after cooling and solidifying, the molded product is obtained.
Injection molds are divided into thermosetting plastic molds and thermoplastic plastic molds according to the molding characteristics; according to the molding process, they are divided into transfer molds, blow molds, casting molds, thermoforming molds, hot compression molds (compression molds), injection molds, etc. Among them, the hot pressing mold can be divided into three types: overflow type, semi-overflow type and non-overflow type according to the overflow method, and the injection mold can be divided into two types: cold runner mold and hot runner mold according to the pouring system; according to the loading and unloading method It can be divided into two types: mobile and fixed
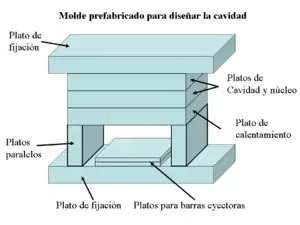
Control de parámetros
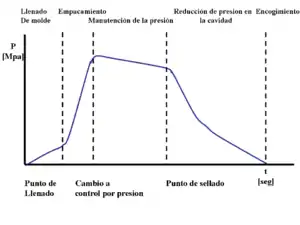
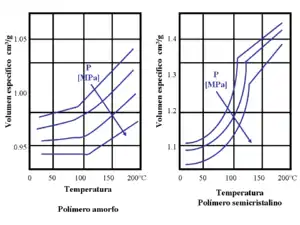
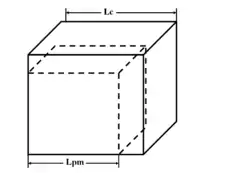
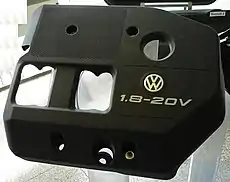
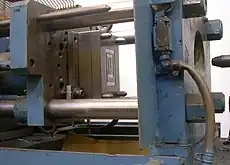
Los parámetros más importantes para un proceso de inyección son los siguientes.
Ciclo de moldeo
En el ciclo de moldeo se distinguen 6 pasos principales (aunque algunos autores llegan a distinguir hasta 9 pasos):
- 1. Molde cerrado y vacío. La unidad de inyección carga material y se llena de polímero fundido.
- 2. Se inyecta el polímero abriéndose la válvula y, con el husillo que actúa como un pistón, se hace pasar el material a través de la boquilla hacia las cavidades del molde.
- 3. La presión se mantiene constante para lograr que la pieza tenga las dimensiones adecuadas, pues al enfriarse tiende a contraerse.
- 4. La presión se elimina. La válvula se cierra y el husillo gira para cargar material; al girar también retrocede.
- 5. La pieza en el molde termina de enfriarse (este tiempo es el más caro pues es largo e interrumpe el proceso continuo), la prensa libera la presión y el molde se abre; las barras expulsan la parte moldeada fuera de la cavidad.
- 6. La unidad de cierre vuelve a cerrar el molde y el ciclo puede reiniciarse.
PvT (relaciones de presión-volumen-temperatura)
En cualquier polímero, las relaciones entre presión, volumen y temperatura son muy importantes para obtener un proceso de inyección eficiente, ya que el volumen de un polímero aumenta al ascender la temperatura del mismo. El comportamiento de los polímeros amorfos y semicristalinos en el paso de enfriamiento es muy diferente, lo que debe ser tenido en cuenta si se quiere obtener una pieza de alta calidad.
Para diseño de equipo de proceso es necesario conocer las relaciones de PvT de los polímeros que se utilizarán, en su forma final, es decir aditivos. A continuación se mencionan los parámetros más comunes para el inicio de las relaciones de PvT, basados en la ecuación de Flory:
- α = Coeficiente de expansión térmica
- β = Compresibilidad isotérmica
Y una ecuación empírica es:
Cuando
Las relaciones de PvT se utilizan en ingeniería de polímeros para lograr un sistema técnico que, basado en la teoría molecular, proporcione datos aplicados a los polímeros en estado fundido en un amplio rango de presión y temperatura. Esto se logra con datos empíricos concretos y limitados. Para determinar estas relaciones existen otras ecuaciones como la de Simha-Somcynsky, el modelo para fluidos de Sánchez y Lacombe y por supuesto, la ecuación de mayor éxito, la ecuación de Flory (Flory-Orwoll-Vrij).
Cristalización y deformación de la pieza al enfriarse (contracción)
Debe tenerse en cuenta que la razón de este fenómeno se debe al cambio de densidad del material, que sigue un propio comportamiento fisicoquímico, particular para cada polímero, y que puede ser isótropo o anisótropo.
De acuerdo con las relaciones de PVT anteriores, se infiere que la parte moldeada sufrirá una contracción, presentando cada polímero diferentes tipos de contracción; sin embargo, puede decirse que, en general, siguen las mismas ecuaciones para contracción isótropa:
Donde:
- Lc = longitud de la cavidad
- Lmp = longitud de la parte moldeada
- Cv = contracción volumétrica
- CL = contracción lineal
- Vc = Volumen de la cavidad
- Vpm = Volumen de la parte moldeada
Los polímeros semicristalinos modificarán más su tamaño dependiendo de la temperatura en la cual se les permita cristalizar. Las cadenas que forman esferulitas y lamelas ocupan menos espacio (mayor densidad) que las cadenas en estado amorfo. Por ello, el grado de cristalinidad afecta directamente a la densidad final de la pieza. La temperatura del molde y el enfriamiento deben ser los adecuados para obtener piezas de calidad.
A continuación se enumeran algunos valores comunes de contracción en polímeros para inyección (para diseño de moldes es conveniente solicitar una hoja de parámetros técnicos del proveedor de polímeros para obtener un rango específico).
Termoplástico | Contracción (%) |
Acrilonitrilo butadieno estireno | 0,4 – 0,8 |
Poliacetal | 0,1 – 2,3 |
Polimetilmetacrilato (PMMA) | 0,2 – 0,7 |
Acetato de celulosa | 0,5 |
Nylon 6,6 | 1,4 – 1,6 |
Policarbonato | 0,6 |
Polietileno de baja densidad | 4,0 – 4,5 |
Polipropileno | 1,3 – 1,6 |
Poliestireno | 0,4 – 0,7 |
PVC rígido | 0,6 – 1,2 |
PVC plastificado | 1,0 – 4,5 |
Colada fría y caliente
Existen dos tipos de colada. La colada fría es el remanente de polímero solidificado que queda en los canales, y que es necesario cortar de la pieza final. La colada caliente mantiene al polímero en estado fundido para continuar con la inyección. Con esta técnica se ahorra una considerable cantidad de plástico, aunque presenta algunos inconvenientes: los pigmentos deben tener mayor resistencia a la temperatura, el polímero aumenta su historia térmica, el molde debe ser diseñado especialmente para esto, etc.
Coloración de la pieza
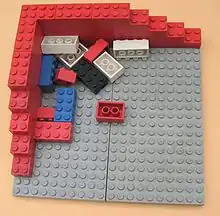
La coloración de las piezas a moldear es un paso crítico, puesto que la belleza de la pieza, la identificación y las funciones ópticas dependen de este proceso. Básicamente existen tres formas de colorear una pieza en los procesos de inyección:
- 1. Utilizar plástico del color que se necesita (pre coloreados).
- 2. Utilizar un plástico de color natural y mezclarlo con pigmento en polvo o colorante líquido.
- 3. Utilizar un plástico de color natural y mezclarlo con concentrado de color.
La elección cómoda y limpia es el uso del concentrado de color (en inglés Masterbatch), el cual se diseña con características de índice de fluidez y viscosidad acordes al polímero que se desea procesar. Con los concentrados de color se puede cambiar de un color a otro de manera rápida, sencilla y limpia. Los pigmentos en polvo presentan mayores problemas de coloración que los concentrados de color y estos más que los precoloreados; sin embargo, los precoloreados son los más caros y presentan una historia térmica mayor. Los problemas de procesamiento más comunes con relación al color de una pieza son: líneas de color más o menos intenso, puntos negros, ráfagas, y piel de naranja.
Los colores pueden ser opacos y, si el polímero es transparente, colores translúcidos. Es importante que el proveedor de los concentrados de color sea consciente de la aplicación final de la pieza, para utilizar pigmentos o colorantes que no migren a la superficie. En poliolefinas no debe utilizarse colorantes porque migran, un error muy común en la industria ya que son baratos, si bien este ahorro merma la calidad de la pieza y puede resultar en una reclamación por parte del cliente.
Los colores finales en la pieza pueden ser translúcidos, sólidos, pasteles, metálicos, perlados, fosforescentes, fluorescentes, etc. Algunos polímeros como el ABS son más difíciles de colorear que otros como el polietileno, por su alta temperatura de proceso y su color amarillento.
Un experto en diseño de un color ha de poseer una habilidad visual impresionante, puesto que sus ojos están entrenados para reconocer colores con diferencias mínimas, lo cual requiere una habilidad natural y amplia experiencia. Debe tomarse en cuenta también la teoría del color, ya que los pigmentos son sustractivos y la luz es aditiva; además, si como color objetivo se tiene una pieza de metal, vidrio, líquido, papel o polímero diferente al polímero final, es posible que bajo diferente luz sea igual o distinto el color final del objetivo. Por ello debe decidirse cuál será la luz bajo la cual los colores deben ser observados. Para personas que no son expertas en identificación de color, son muy útiles los colorímetros, aunque su grado de confianza no llega al 100 %. Una persona no entrenada puede ver dos colores diferentes como iguales y dos iguales como diferentes, debido a errores en el ángulo con respecto a la incidencia de la luz, distancia entre uno y otro objetivo, luz ambiental, etc.
Temperatura de proceso
Para inyectar un polímero, específicamente un termoplástico, es necesario conocer su temperatura de transición vítrea (Tg) y su temperatura de fusión de la región cristalina (Tm), si es un polímero semicristalino.
La temperatura de operación de cada termoplástico no es estándar, y varía según el proveedor (de acuerdo con el peso molecular, ramificación del polímero, polidispersidad y aditivos). Es por tanto necesario solicitarle una Hoja de Especificaciones donde se encuentre tanto el índice de fluidez como la temperatura de trabajo, que además es un rango de temperaturas, y la temperatura de degradación, con lo cual se obtiene un intervalo dentro del cual se puede trabajar el material eficientemente.
Dimensiones de la máquina
La efectividad de una máquina de inyección se basa en la cantidad de presión que esta pueda generar, por dos razones principales:
- 1. Incrementando la presión se puede inyectar más material
- 2. Incrementando la presión se puede disminuir la temperatura, que se traduce en menor costo de operación.
Las máquinas se venden dependiendo de su fuerza de cierre expresada en toneladas, y van desde 10 Toneladas las más pequeñas, hasta 4.400 Toneladas las de mayor capacidad.
Es aconsejable utilizar el cañón más largo posible si se necesita mezclar compuestos, y también hacer énfasis en el husillo adecuado. A continuación se muestra un husillo típico de laboratorio para polioleofinas:
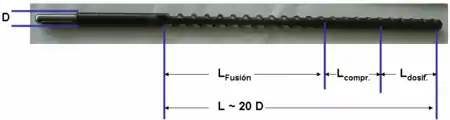
Aunque las dimensiones de la máquina dependen principalmente de la cantidad de polímero que se necesita para llenar la pieza deseada, es común que los proveedores de máquinas vendan equipos más o menos estándares. Las principales características para determinar las dimensiones de una máquina son: la capacidad de cierre, dimensiones del molde, carrera o recorrido del molde, presión de inyección, capacidad volumétrica de inyección, características de plastificado y velocidad de inyección..
Flujo y diseño de flujo
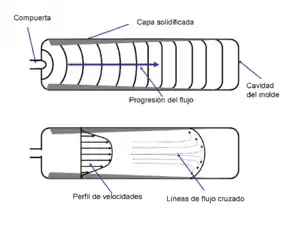
Los polímeros son materiales cuyas viscosidades son muy altas, por lo que su flujo es lento y complicado. La razón de esto es que son cadenas muy largas de unidades más simples, a causa de lo cual los polímeros presentan una orientación con respecto al esfuerzo cortante al que han sido sometidos. En general, es conveniente eliminar lo más posible la orientación de las moléculas, propiedad que se contrapone a la rapidez de moldeo (y por tanto al costo). Sin embargo, si el estrés debido a una orientación extremadamente alta no se libera, la pieza se deformará al enfriarse o al calentar el material en su aplicación.
El polímero entra en el molde y se va acumulando desde el punto de entrada, arrastrándose por las paredes y empujando el polímero en el centro. Cuando este toca las paredes del molde, comienza a enfriarse y solidificarse. Esto ocurre con cierta baja orientación, pero cuando se va llenando la cavidad en capas posteriores lejanas a la pared del molde, la orientación se incrementa y un inadecuado enfriamiento congela los estreses generados, siguiendo un perfil de velocidades semejante al del flujo parabólico en un tubo.
El flujo de un polímero a través de una cavidad rectangular se puede estudiar utilizando condiciones isotérmicas, o con el molde a temperaturas menores que la Tg del polímero a estudiar. Para los experimentos en condiciones isotérmicas, se observa que el tipo de polímero no modifica el flujo, que mantiene un perfil de velocidades constante, con un flujo radial después de la compuerta hasta llenar las esquinas. Después, el flujo se aproxima a un flujo tapón, perdiendo movilidad en las zonas de contacto con la pared fría. El flujo de cada polímero es estudiado por la reología.
Una aproximación al estudio del flujo de polímeros en el llenado de un molde es la ecuación de Hagen y Poiseuille, la cual considera parámetros en el régimen laminar. Esta ecuación, despejada para la viscosidad del material es:
Donde: η = Viscosidad
- r = Radio del tubo o canal
- ΔP = Caída de presión
- L = Longitud del tubo
- Q = Flujo volumétrico
- τ = Esfuerzo cortante
- = Velocidad de corte
Para el diseño de los canales en el molde, se observa de la ecuación anterior que la velocidad de corte y la viscosidad se ven afectadas por el diseño del radio del canal. Si el flujo volumétrico y la caída de presión se mantienen constantes, en condiciones isotérmicas entre los ciclos de moldeo, la viscosidad permanece constante y por lo tanto se espera que la calidad de la pieza moldeada sea constante.
En la práctica, los ingenieros toman en cuenta que los polímeros son fluidos no newtonianos (particularmente. son materiales viscoelásticos). Por lo tanto, se deberán hacer correcciones a la fórmula anterior dependiendo de para qué plástico se realizará el molde. También se utilizan "curvas de viscosidad", que grafican η frente a .
Un parámetro importante en el flujo incluye la temperatura; otra buena aproximación a polímeros obedece a la ecuación de Arrhenius:
Donde:
- = Constante del polímero en cuestión
- R = Constante universal de los gases ideales, Por lo general expresada en Joules, kelvins y moles
- T = Temperatura
- E = Energía de activación para el flujo viscoso
Ventilación y presión
Conforme el polímero avanza desde la entrada o tolva, va reduciendo el tamaño de sus gránulos por medios tanto mecánicos (fricción, compresión y arrastres) como térmicos (aumento en su temperatura interna), llegando al estado gomoso o fusión, dependiendo de si el material es amorfo o semicristalino. Conforme este material avanza, el aire presente experimenta un aumento de presión y generalmente escapa en dirección opuesta al avance del polímero. Si esto no ocurre, entonces es necesario abrir una compuerta de ventilación, igualando de esta manera la presión generada a la presión atmosférica. Debido a las propiedades de viscosidad y de arrastre del polímero, sólo escapa mediante la ventilación una parte mínima de plástico.
El error más común con la ventilación es el añadir aditivos espumantes desde la tolva. Los espumantes generan gas, aire o agua que queda atrapado en células abiertas o cerradas del polímero. No obstante, si la presión disminuye a presión atmosférica, este gas generado escapa, resultando así un polímero sin espumar. Para una eficiente alimentación del espumante, este debe ser añadido después de la ventilación o eliminar el mismo.
Técnicas modernas
Algunas de las técnicas modernas incluyen la inyección de multicomponentes, es decir, una pieza que contiene dos polímeros unidos entre sí o un polímero con diferentes colores y aditivos separados en capas. En esta técnica es posible inyectar dos polímeros en la misma pieza. Existen dos métodos para lograr esto: uno es con dos unidades de inyección, y otro con una unidad de inyección compuesta. Un polímero queda inmerso en el otro, o un color queda inmerso en el otro, ahorrando así costos: esta técnica es llamada inyección emparedado o sándwich. Otra posibilidad es inyectar con agentes formadores de celdas o espumantes que reducen la densidad de la pieza moldeada.
La inyección puede contener injertos metálicos, cerámicos o plásticos. Estos son colocados manual o automáticamente en el molde, sobre el cual es inyectado el polímero que, por medios geométricos, evita su separación al enfriarse.
En el moldeo con reacción química no se usa el extrusor, sino más bien componentes líquidos que se van administrando. Estas resinas pueden estar activadas o activarse al unir los diferentes fluidos. Un ejemplo típico de polímero inyectado por este proceso es el poliuretano y la poliurea. Generalmente, las temperaturas en este proceso son mucho más bajas que las temperaturas de la inyección con husillo.
La inyección de hule y de termoestables consiste en un proceso que incluye la inyección con todos los ingredientes necesarios para el curado o vulcanizado, pero a temperaturas bajas en el cañón. Este debe provocar poca fricción en el material para evitar el sobrecalentamiento y reacción prematura, cambiando así la cinética de reacción deseada. La reacción termina precisamente en el molde, el cual no es necesario enfriar.
La inyección con equipo moderno de polímeros semiconductores y de polímeros conductores requiere mucho menos cuidado que en el proceso de semiconductores tradicionales de silicio y germanio. El cuarto limpio no es necesario y el proceso se puede llevar a cabo con un cuidado semejante al de inyección de equipo médico.
La inyección de materiales compuestos como madera-plástico o fibras naturales con polímero, fibra de carbón y nanopartículas tienen una problemática particular, debido a que el husillo tiende a romper, cortar o aglomerar las partículas, por lo que presentan un doble reto: por una parte deben ser dispersadas y distribuidas (como cualquier pigmento), a la vez que deben permanecer lo más estables posible. Las nanopartículas generalmente forman aglomerados, que reflejan una pérdida de propiedades mecánicas y no un aumento, ya que el estrés es función directa del área de la unión partícula-polímero.
Entradas
Las funciones concretas de una entrada son simples: sirven para ayudar a que el polímero solidifique pronto cuando la inyección concluye, y para separar fácilmente los remanentes de inyección de la pieza final. Muchas veces elimina la necesidad de cortar o desbastar este sobrante y acelerar el flujo de material fundido, que se refleja en una menor viscosidad y mayor rapidez de inyección.
Para garantizar el buen funcionamiento de un polímero inyectado, es imprescindible tener en cuenta los fenómenos de transporte y particularmente el flujo del polímero. Recuérdese que no se habla de moléculas o iones como los metales fundidos, sino de largas cadenas de macromoléculas en estado gomoso. Las entradas son así diseñadas para mejorar el flujo y para permitir un orden distributivo del mismo. Las entradas más comunes son:
Tipo de entrada | Esquema | Característica |
Entrada de canal | (sin esquema) | Alimentan de manera directa desde la cavidad. |
Entrada cónica | ![]() |
Alimentan el polímero permitiendo una ligera relajación de esfuerzos. |
Entrada puntiforme | ![]() |
Se llenan desde los bebederos; comúnmente usadas en moldes de tres placas, permiten altas velocidades y se llenan con facilidad; pueden eliminarse sin dificultad de la pieza moldeada. |
Entrada lateral | ![]() |
Alimentan desde un lado del molde; comúnmente utilizadas para impresión múltiple. |
Entrada anular | ![]() |
Se usan para moldear partes huecas ya que su flujo es previamente modificado a la forma final. |
Entrada de diafragma | ![]() |
Similares a las compuertas anular, pero distribuyen el material fundido desde el canal de alimentación. |
Entrada de abanico | ![]() |
Sirven para cubrir áreas grandes o largas de manera homogénea y distributivamente correcta. |
Entrada de lengüeta | ![]() |
Estas compuertas minimizan el efecto de jet y ayudan a lograr un flujo de régimen laminar cuyo número de Reynolds es adecuado para la inyección. |
Entrada de cinta o laminar | ![]() |
Sirven para moldear homogéneamente áreas planas y delgadas, sobre todo en productos translúcidos y transparentes como objetivos de policarbonato, láminas de PMMA y dispositivos ópticos de medición, ya que minimiza las aberraciones cromáticas y ópticas debidas a ondas formadas por flujo en régimen turbulento. |
Estas entradas se utilizan en el diseño de molde preferentemente bajo la experiencia y el diseño por computadora, con programas como Moldflow que simulan el flujo de polímeros en el molde.
Disciplinas de Moldeo por Inyección
Moldeo Universal
Moldeo Universal (MU) es una disciplina de optimización de procesos de moldeo por inyección. Es un lenguaje que combina la rotulación de equipos y el uso de parámetros universales. MU combina trasfondos técnicos y científicos con el objetivo de aumentar la eficiencia de los procesos, disminuir los costos de los productos y recortar los ciclos de manufactura.
Defectos, causas posibles y soluciones en partes moldeadas
Los defectos en partes moldeadas requieren experiencia tanto para ser identificados como para ser resueltos. Los operarios con años de experiencia en inyección son los mejores maestros de identificación y solución de problemas, ya que su experiencia les da las ideas y recursos necesarios para solucionar problemas rápidamente. Aquí se sugieren algunas de las soluciones a los problemas más comunes:
Defecto | Causas posibles | Probables soluciones |
Achicamiento | Enfriamiento demasiado intensivo. Diseño inadecuado de la pieza. Tiempo de enfriamiento muy corto. Sistema de extracción inapropiado. Esfuerzos en el material. | Incremente el tiempo de enfriamiento dentro del molde. Utilizar un polímero reforzado. |
Flash | Presión de cierre demasiado baja. | Incrementar la presión de la unidad de cierre. |
Líneas de flujo | Mala dispersión del concentrado de color o del pigmento. Temperatura demasiado baja. | Cargar el material más lentamente. Incrementar la temperatura del barril. Modificar el perfil de temperaturas. |
Puntos negros | Hay carbonizaciones. | Purgar el husillo. Reducir la temperatura del proceso. Limpiar el husillo manualmente. |
Piel de naranja | Incompatibilidad del material. | Disminuir la temperatura del proceso. Incrementar la temperatura del molde. Cambiar el concentrado de color. |
Parte incompleta | Insuficiente material en la cavidad. Falta de material en la tolva. Cañón demasiado pequeño. Temperatura demasiado baja. Obstrucción de la tolva o de la boquilla. Válvula tapada. Tiempo de sostenimiento demasiado corto. Velocidad de inyección demasiado baja. Canales demasiado pequeños. Respiración insuficiente. | Inyectar más material. Cambiar el molde a una máquina de mayor capacidad. Incrementar la temperatura del barril. Incrementar la velocidad de inyección. Modificar el tamaño de los canales del molde. |
Parte con rebabas | Dosificación excesiva. Temperatura de inyección muy alta. Presión de inyección muy alta. Tiempo de inyección muy largo. Temperatura de molde muy alta. | Dosificar menos material. Disminuir la temperatura de inyección. Disminuir la presión. Disminuir el tiempo de inyección. Disminuir la temperatura del molde. |
Rechupados y huecos | Presión de inyección demasiado baja. Tiempo de sostenimiento de presión muy corto. Velocidad de inyección baja. Material sobrecalentado. Humedad. Enfriamiento del molde no uniforme. Canales o compuertas muy pequeños. Mal diseño de la pieza. | Incrementar la presión. Incrementar el tiempo de sostenimiento de presión. Disminuir la temperatura del barril. Incrementar la velocidad de inyección. Abrir el venteo o pre seque el material. Modificar los canales de enfriamiento del molde o el flujo del agua. Modificar el molde. |
Líneas de unión | Temperatura general muy baja en el molde. Temperatura del fundido no uniforme. Presión de inyección muy baja. Velocidad de inyección muy baja. Insuficiente respiración en la zona de unión de los flujos encontrados. Velocidad de llenado no uniforme. Flujo no adecuado del material por los canales o la cavidad. | Incrementar la temperatura. Incrementar la presión. Incrementar la velocidad de inyección. Modificar la respiración del material en el molde. Modificar la compuerta para uniformar el flujo. |
Degradación por aire atrapado | Humedad. Degradación de aditivos. Temperatura demasiado alta. Respiración del molde insuficiente. | Secar el material. Disminuir la temperatura. Modificar la respiración del molde. |
Delaminación de capas | Temperatura demasiado baja. Velocidad de inyección demasiado baja. Baja contrapresión de la máquina. Temperatura del molde muy baja. | Incrementar la temperatura. Incrementar la velocidad de inyección. Incrementar la contrapresión de la máquina. |
Fracturas o grietas en la superficie | Temperatura del molde demasiado baja. Sistema de eyección demasiado agresivo o inadecuado. Empacado excesivo. | Incrementar la temperatura. Modificar las barras eyectoras. Utilice un robot para extraer la pieza. Disminuir la presión de sostenimiento. |
Marcas de las barras eyectoras | Tiempo de enfriamiento muy corto. Temperatura del molde alta. Temperatura del polímero demasiado alta. Rapidez de eyección demasiado alta. Localización inadecuada de las barras eyectoras. | Incrementar el tiempo de enfriamiento. Disminuir la temperatura del fundido. Disminuir la rapidez de eyección. Modificar la ubicación de las barra eyectoras. |
Quemado de la pieza | Quemado por efecto de jet. | Disminuya la velocidad de inyección. |
El concentrado de color no se mezcla | Perfil incorrecto de temperaturas. | Probar un perfil inverso de temperaturas. Bajar la temperatura de las primeras dos zonas de la unidad de inyección. Usar un perfil de temperaturas más agresivo. |
El color es más oscuro | La temperatura es demasiado alta. La compuerta es demasiado pequeña y se quema el polímero por presión. | Disminuir la temperatura. Modificar la compuerta del molde. |
Véase también
Referencias
Bibliografía
- Bryce, Douglas M. Plastic injection molding: manufacturing process fundamentals. Dearborn: Society of Manufacturing Engineers, 1996. ISBN 0-87263-472-8
- Flory PJ, Orwoll RA, Vrij A. Statistical Thermodynamics of Chain Molecule Liquids. I. An Equation of State for Normal Paraffin Hydrocarbons. J Am Chem Soc 1964, 86, 3507. DOI: 10.1021/ja01071a023.
- Frenkler, D.; Zawistowski, H. Hot Runners in Injection Moulds. Shawbury, Shrewsbury, Shropshire: Rapra Technology, 2001, 1.ª ed. ISBN 1-85957-208-1.
- Goodship, Vannessa. Troubleshooting Injection Moulding. Shawbury, Shrewsbury, Shropshire: Rapra Technology, 2004. ISBN 1-85957-470-X.
- He J, Zoller J. Crystallization of polypropylene, nylon-66 and poly (ethylene terephthalate) at pressures to 200 MPa: Kinetics and characterization of products. Polymer Sci., Part B: Polym. Phys. 1994, 32, 1049. DOI: 10.1002/polb.1994.090320610.
- Johannaber, Friedrich. Injection molding machines: a user's guide. Múnich: Hanser, 1994, 3ª ed. ISBN 1-56990-169-4
- Kumar, Anil; Gupta, Rakesh K. Fundamentals of polymer engineering. Nueva York: Marcel Dekker, 2003. ISBN 0-8247-0867-9
- Morton-Jones, D.H. Procesamiento de plásticos: Inyección, moldeo y PVC. México: Limusa, 1999. ISBN 968-18-4434-3
- Platt, David K. Engineering and High Performance Plastics. Shawbury, Shrewsbury, Shropshire: Rapra Market Report, 2003. ISBN 1-85957-380-0
- Rees, Herbert. Understanding Injection Molding Technology. Múnich: Hanser Gardner, 1994. ISBN 1-56990-130-9
- Sánchez Valdés, Saúl; Rodríguez Fernández, Oliverio S.; Yáñez Flores, Isaura G. Moldeo por inyección de termoplásticos. México: Limusa, 2003. ISBN 968-18-5581-7
- Schultz, Jerold M. Polymer Crystalization, The development of Crystalline Order in Thermoplastic Polymers. Nueva York: Oxford University Press, 2001. ISBN 0-8412-3669-0
- Ingeniería de Sistemas y Automática. Tecnología de Fabricación y Tecnología de Máquinas.
- Dilán, Héctor, Moldeo Universal, Técnicas Modernas de Moldeo por Invección 2002
Enlaces externos
- Resumen de moldeo por inyección de DOW
- Textos científicos.com
- Artículo sobre moldeo por inyección
- Plásticos y Aplicaciones – Caso Práctico en la UPIICSA
- Videos moldeo
- inyección por molde
- Web sobre fabricación de moldes
- En inglés