Motor térmico
Un motor térmico es una máquina térmica que transforma calor en trabajo mecánico[1] por medio del aprovechamiento del gradiente de temperatura entre una fuente de calor (foco caliente) y un sumidero de calor (foco frío). El calor se transfiere de la fuente al sumidero y, durante este proceso, algo del calor se convierte en trabajo por medio del aprovechamiento de las propiedades de un fluido de trabajo, usualmente un gas o el vapor de un líquido.
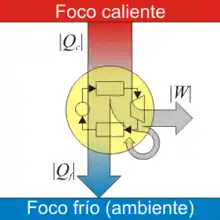
El calor requerido para el buen funcionamiento de una máquina térmica procede de la energía química liberada en una combustión, siendo absorbido por un fluido motor que pone en movimiento una serie de piezas mecánicas.
Si la combustión tiene lugar fuera del motor, las máquinas reciben el nombre de máquinas de combustión externa, y si la combustión tiene lugar dentro de la máquina, las máquinas reciben el nombre de máquinas de combustión interna. El movimiento producido puede ser alternativo o rotativo.
El fluido motor suele ser el vapor de agua, el aire o la mezcla de gases resultantes de la combustión del petróleo o de gases combustibles.[2] En los motores de combustión interna la combustión se realiza en el fluido motor, y en los motores de combustión externa existen dos fluidos, donde se intercambia calor entre ambos. En las centrales nucleares el calor procede de la energía liberada en la fisión nuclear del uranio o del plutonio, siendo extraído por una sustancia refrigerante que lo cede a un circuito secundario a través de un cambiador de calor.
Historia
En 1765 el escocés James Watt fabricó la primera máquina de vapor eficiente, y significó además el comienzo de la Revolución Industrial, nacida como consecuencia de la sustitución del esfuerzo muscular por el trabajo de las máquinas. La máquina de vapor fue un triunfo de la tecnología que hizo surgir fábricas en la mayoría de países, al mismo tiempo que elevaba el nivel de bienestar de la sociedad.
Un siglo más tarde los motores de combustión interna revolucionaron el transporte terrestre, marítimo y aéreo.
Máquina de vapor
La máquina de vapor es una máquina de combustión externa que aprovecha la fuerza expansiva del vapor de agua para mover un émbolo y producir trabajo.
Historia de la máquina de vapor
En 1691, el ingeniero militar inglés Thomas Savery fue pionero en utilizar la presión del vapor de agua para extraer agua de minas y pozos y mover una rueda hidráulica. Normalmente la presión del vapor de agua solía reventar calderas y tuberías, y además, era poco eficaz porque se perdía el calor del vapor de agua cada vez que se enfriaba el recipiente.
En 1698 Thomas Savery patentó su descubrimiento, y el herrero inglés Thomas Newcomen construyó una máquina más perfecta, que trabajaba a bajas presiones. Además, contaba con un pistón y un cilindro. Con la presión del aire podía mover el pistón.
En 1765 el mecánico escocés James Watt mejoró la máquina de Thomas Newcomen, y en 1782 construyó la primera máquina de vapor.
En 1787 el inventor estadounidense John Fitch construyó un barco de vapor, aunque este fracasó financieramente.
En 1807 Robert Fulton botó el Clermont, el primer barco de vapor.
En 1814 el inglés George Stephenson construyó la primera locomotora de vapor.
Funcionamiento de la máquina de vapor
- Hogar: Exterior de la máquina, donde se realiza la combustión.
- Caldera: Recipiente de acero donde se genera vapor de agua. Está provista de un nivel de agua para observar la altura de ésta, un manómetro para medir la presión interior, y una válvula de seguridad que se abre cuando la presión alcanza un determinado valor, evitando así que se produzca una explosión. El agua es impulsada por una bomba y penetra en la caldera en estado líquido, a alta presión y a temperatura ambiente. En la caldera el agua se calienta y se vaporiza pasando a un sobrecalentador conectado a la caldera, donde la temperatura aumenta y se mantiene la presión. El vapor de agua pasa finalmente al cilindro.
- Cilindro motor: Está constituido por la caja de distribución, la corredera y el émbolo. El vapor de agua penetra en la caja de distribución y entra en contacto con el émbolo a la vez que el vapor de agua es empujado hacia un orificio por donde escapa dirigiéndose hacia la chimenea o al condensador. En el condensador, el vapor restante se licúa y cede al refrigerante. El líquido condensado es enviado nuevamente por la bomba a la caldera, completando así el ciclo.
- Órganos transformadores del movimiento: Estos órganos son el vástago, la biela y la manivela, tres varillas articuladas que transformar el movimiento alternativo del émbolo en movimiento circular. El vástago está unido a la biela por medio de una cruceta. La manivela gira a un volante de inercia, cuya misión es mantener constante la velocidad angular. El volante lleva acoplado una excéntrica, que regula el movimiento de la corredera.
Ciclo de Rankine


El proceso de expansión del vapor de agua contra el émbolo es adiabático, pero no reversible, por lo que no es isoentrópico.
Para que una máquina térmica siguiese el ciclo de Carnot habría que detener la condensación del vapor antes de que se licue por completo y, por medio de un compresor, conseguir que la mezcla vapor-líquido alcance su licuación completa a la temperatura de la caldera.
Como esto resulta imposible, el ingeniero escocés J. M. Rankine propuso una modificación del ciclo de Carnot, denominado ciclo de Rankine.
- El agua líquida de la caldera absorbe el calor del hogar, eleva su temperatura a presión constante. Manteniendo la temperatura y la presión constantes se transforma en vapor saturado y seco reversiblemente.
- El vapor saturado se expande en el interior de la máquina de forma adiabática y reversible, hasta alcanzar la temperatura del refrigerador y se condensa. El trabajo en este caso es positivo.
- Prosigue la condensación a temperatura y presión constantes, formándose así líquido saturado.
- El líquido saturado se comprime hasta alcanzar la temperatura y la presión de la caldera.
En un ciclo de Rankine con sobrecalentamiento, la temperatura media a la que se absorbe el calor implica un mayor rendimiento. El vapor permanece seco durante toda la expansión adiabática, por lo que disminuye los peligros a la corrosión.
Potencia de la máquina de vapor
La potencia de una máquina de vapor depende de la presión y la cantidad de vapor de agua admitida por el cilindro en la unidad de tiempo. Como la presión varía, se considera un valor promedio llamado presión media efectiva.
La cantidad de vapor de agua por unidad de tiempo es igual al volumen del cilindro correspondiente a cada revolución multiplicado por el número de revoluciones en unidad de tiempo. El volumen se calcula multiplicando la sección del émbolo por la longitud de la carrera.
siendo
- la potencia de la máquina,
- la presión media efectiva,
- la longitud de la carrera,
- la sección del émbolo,
- el número de revoluciones por unidad de tiempo.
Cuando el vapor de agua actúa sobre ambas caras del émbolo, la potencia teórica desarrollada es el doble de este valor.
A causa de rozamientos y otras pérdidas, realmente la potencia suele ser un 70 o un 90 % que la potencia citada.
El tamaño de la máquina de vapor se limita a potencias de 1000 CV, a velocidades de 213 m/min, a presiones de 14 kp/cm², a temperaturas de 315 °C y a rendimientos del 30 %.
Las máquinas de vapor se han utilizado como órganos motores de locomotoras, y barcos. Actualmente, han sido sustituidas por motores de combustión.
Turbina de vapor
En la turbina de vapor el vapor de agua se distribuye por cuatro tubos y actúa directamente sobre las paletas de una rueda, haciéndola girar con una velocidad de unas 10 000 rpm.
La turbina de vapor carece de cilindro motor y de órganos transformadores del movimiento, por lo que el rendimiento es mayor.
Actualmente, la turbina de vapor se emplea en las centrales eléctricas, en la propulsión de buques y en las instalaciones soplantes de altos hornos.
Postulados de la termodinámica
- Cualquiera que sea el procedimiento empleado para convertir el calor en trabajo o viceversa, existe una relación constante entre el trabajo desarrollado y el calor consumido, siempre que el estado final del sistema sea igual al inicial (ciclo termodinámico). El equivalente mecánico del calor es 427 kgm/kcal o en el sistema de normas internacionales ISO 4184 julio/1000 cal.
- Una máquina térmica sólo puede efectuar trabajo si absorbe calor de un manantial a temperatura superior y lo cede en parte a otro a temperatura inferior. Es decir, el calor no puede transferirse espontáneamente de un cuerpo más frío a otro más caliente.
Principio básico de funcionamiento
En un motor térmico se producen una serie de transformaciones que conducen a un estado inicial (es decir, tiene un ciclo cerrado). En el transcurso de estas transformaciones, el motor recibe energía térmica en forma de calor y devuelve energía mecánica en forma de trabajo.
Eficiencia de los motores térmicos
La eficiencia de varios motores térmicos propuestos o usados hoy en día oscila entre el 3 % (97 % de calor desperdiciado) para los sistemas de conversión de energía térmica del océano, el 25 % para la mayor parte de los motores de automóviles, el 35 % para una planta generadora de carbón supercrítico, y el 60 % para una turbina de gas de ciclo combinado con enfriamiento de vapor. Todos estos procesos obtienen su eficiencia (o la pierden) debido a la depresión de la temperatura a través de ellos. Por ejemplo, los sistemas de conversión de energía térmica del océano emplean una diferencia de temperatura entre el agua sobre la superficie y el agua en las profundidades del océano, es decir, una diferencia de tal vez 25 °C, por lo que la eficiencia debe ser baja. Las turbinas de ciclo combinado utilizan quemadores de gas natural para calentar aire hasta cerca de 1530 °C, es decir, una diferencia de hasta 1500 °C, por lo que la eficiencia puede ser mayor cuando se añade el ciclo de enfriamiento de vapor.
Clasificación de los motores térmicos
Para la clasificación de los motores térmicos, además de los criterios ya mencionados en el caso de máquinas de fluido, se tienen en consideración dos aspectos adicionales:
- Si el fluido es condensable (agua) o no condensable (aire).
- Si el proceso es de combustión externa o interna.
Motores de combustión interna

El fundamento de los motores de combustión interna es la realización de la combustión en el interior del cilindro de la máquina, en los que el agente motor es el combustible mezclado con el aire necesario para la combustión.
Existen distintos tipos de máquinas de combustión interna dependiendo del combustible utilizado, las condiciones de la combustión y el número de carreras que efectúa el pistón en un ciclo. El movimiento puede ser alternativo, que lo realizan los motores de explosión y de combustión, o rotativo, que lo realizan las turbinas de explosión y de combustión.
En las máquinas de movimiento alternativo, la combustión es instantánea, producida por una chispa eléctrica, debiendo utilizarse combustibles gaseosos o líquidos muy volátiles, como por ejemplo la gasolina. En las máquinas de movimiento rotativo se realiza de una forma progresiva y a presión constante, utilizándose como combustibles líquidos menos volátiles, como por ejemplo el gasóleo.
En las máquinas de combustión interna, los gases de la combustión son los que circulan por la propia máquina. En este caso, la máquina será necesariamente de ciclo abierto, y el fluido motor será el aire (no condensable) empleado como comburente en la combustión.
Motores de combustión interna |
---|
Rotativo | Turbomáquina | Turbina de gas de ciclo abierto |
Volumétrico | Motor Wankel, Quasiturbina | |
Alternativo | Encendido por compresión | Motor diésel |
Encendido provocado | Motor de explosión (Otto, Miller, de mezcla pobre, de Ciclo Atkinson) | |
Reacción | Motor cohete | Cohete espacial de propulsante líquido/sólido |
Aerorreactor sin compresor | Estatorreactor Pulsorreactor | |
Aerorreactor con compresor | Turborreactor Turbofán Turbohélice | |
Motores de explosión o de encendido provocado (MEP)
El motor de explosión de uso más común es el motor de cuatro tiempos, que está formado por los siguientes componentes.
- Inyector: Dispositivo mecánico o eléctrico encargado de inyectar la gasolina en el cilindro o en el conducto de admisión. Los motores de explosión antiguos llevaban un carburador, donde se pulverizaba la gasolina y se mezclaba con el aire.
- Cilindro: Está constituido por el cuerpo de la bomba, un émbolo, una válvula de admisión y otra válvula de escape, y una bujía. En el cilindro se realiza la explosión del carburante, originándose un movimiento alternativo de pistón o émbolo. El émbolo tiene una forma de vaso invertido y está unido a la biela por medio de un bulón, ha de ser resistente a los esfuerzos mecánicos y térmicos y va provisto de segmentos alojados en ranuras en la parte superior.
- Las válvulas de admisión y de escape permiten la entrada del combustible y la salida de los gases de combustión. Están situadas en la culata, sobre el cilindro, y se mantienen en su posición de cierre mediante un muelle, abriéndose hacia el interior por medio de una leva. Las levas se sitúan en el árbol de levas, que está sincronizado con el cigüeñal.
- La culata es una pieza que cierra los cilindros en la zona de combustión, y está acoplada por medio de pernos. Las temperaturas elevadas que se alcanzan en la culata requiere un sistema de refrigeración, que puede ser por aire o por agua. El sistema de refrigeración por aire dota a los cilindros de aletas de enfriamiento, y el sistema de refrigeración por agua circula entre la cubierta de cilindro y culata, donde el agua recorre el circuito impulsada por una bomba y se enfría en el radiador por medio de una corriente de aire producida por un ventilador.
- La bujía está formada por dos electrodos separados unos 0,5 mm. Uno de ellos está unido a una masa, y otro procede del distribuidor, ambos aislados eléctricamente. La bujía produce una chispa que explosiona el carburante.
- Las válvulas de admisión y de escape permiten la entrada del combustible y la salida de los gases de combustión. Están situadas en la culata, sobre el cilindro, y se mantienen en su posición de cierre mediante un muelle, abriéndose hacia el interior por medio de una leva. Las levas se sitúan en el árbol de levas, que está sincronizado con el cigüeñal.
- Órganos transformadores del movimiento: Los órganos transformadores del movimiento son la biela-manivela y el cigüeñal, que transforman el movimiento alternativo del pistón en movimiento circular. La biela transmite el esfuerzo del pistón al cigüeñal, y este transmite la potencia desarrollada en los cilindros del árbol motor. Los cilindros, la biela-manivela y el cigüeñal se encierran en el bastidor-cárter, que debe ser resistente para soportar los esfuerzos provocados en el pistón, y además protege a todos los elementos, y sirve de depósito de lubricante.
- Es necesario una lubricación debido a la cantidad de piezas móviles, no solamente para aumentar el rendimiento, sino para evitar deterioros. Deben lubricarse especialmente las paredes del cilindro, las articulaciones de las bielas, el árbol de las levas, las válvulas, los cojinetes del cigüeñal y los engranajes. La lubricación se lleva a cabo mediante un circuito de aceite a presión. El aceite se encuentra en un cárter, desde donde se distribuye por medio de una bomba.
Ciclo de Otto
Una máquina térmica sigue el ciclo ideado en 1862 por Beau de Rochas y usado por primera vez en 1877 por Nikolaus Otto, denominando así al ciclo como ciclo de Otto.
El ciclo de Otto se efectúa por un gas perfecto, y consta de dos procesos adiabáticos y dos isocoros, que reciben el nombre de tiempos.
- Primer tiempo: Admisión. Baja el pistón, se abre la válvula de admisión y entra por aspiración el carburante y el aire en el cilindro.
- Segundo tiempo: Compresión. Sube el pistón, se cierran las válvulas y se comprime el carburante.
- Tercer tiempo: Explosión-expansión. Al alcanzar la máxima compresión salta la chispa de la bujía, explosiona el carburante y lanza el pistón hacia abajo. Durante este proceso el pistón se sitúa en la parte más alta, y las válvulas permaneces cerradas.
- Cuarto tiempo: Escape. Se abre la válvula de escape y el pistón expulsa los gases.
El rendimiento del ciclo de Otto viene dado por la expresión:
donde R es el grado de compresión de la mezcla, y es el coeficiente adiabático.
En los motores de gasolina existe un límite por encima del cual no puede elevarse el grado de compresión, ya que a temperaturas y presiones elevadas el carburante explosiona antes de saltar la chispa. Se dice que se ha alcanzado el nivel de autoignición.
Esta detonación produce un choque audible que perjudica al motor y disminuye el rendimiento. Añadiendo sustancias antidetonantes o catalizadores se consigue grados de compresión de 8 a 10.
Las razones por el bajo rendimiento son las siguientes:
- La combustión no suele ser completa, y se produce monóxido de carbono.
- Existe un intercambio de calor entre los gases y paredes, lo que obliga a refrigerar el cilindro.
- La combustión no se verifica de forma instantánea, y tiene lugar un aumento de volumen. Para corregirlo se realiza un avance de encendido, que consiste en provocar la explosión antes de que el pistón haya realizado el tiempo.
Octanaje de una gasolina
Las gasolinas de alto poder antidetonante son aquellas en las que predominan los hidrocarburos cícliclos y los hidrocarburos de cadena ramificada, que detonan con mayor dificultad. Para comparar las propiedades antidetonantes se utiliza el índice o número de octano, donde se toman como hidrocarburos el isooctano y el n-heptano, a los que se asignan poderes antidetonantes de 100 y 0.
El índice o número de octano es el tanto por ciento en volumen de isooctano en una mezcla de isooctano y n-heptano que tenga el mismo poder antidetonante que la gasolina.
La gasolina de aviación tiene un número de octano superior a 100, y constan de un 20 % de hidrocarburos aromáticos.
Para disminuir la detonación y aumentar el índice o número de octano de una gasolina, antiguamente se utilizaban antidetonantes, que actuaban como catalizadores negativos de las reacciones de combustión de los hidrocarburos. El más completo fue el tetraetilo de plomo, que se añadía un 0,1 % a la gasolina. Al explosionar la gasolina quedaban libres plomo metálico y óxido de plomo, que estropeaban el motor y contaminaban el aire. Actualmente, se utilizan gasolinas sin plomo empleando otro tipo de catalizadores.
Motores de combustión externa
Las causas que limitan el rendimiento de las máquinas de combustión externa radican en la imposibilidad de alcanzar temperaturas elevadas en la caldera, debido a la presión que se alcanza; y la dificultad de conseguir un aprovechamiento de la energía calorífica del carbón y otro combustible.
Si la combustión es externa, el calor de la combustión se transfiere al fluido a través de una pared, por ejemplo en un intercambiador de calor. Este tipo de máquinas no exige un proceso de combustión, como sucede en las instalaciones nucleares, si bien es el procedimiento usual. Dado que el fluido motor no sufre degradación alguna, estas máquinas pueden ser de ciclo cerrado, a lo que actualmente se tiende por razones económicas.
Motores de combustión externa |
---|
Fluido condensable |
Turbomáquina | Turbina de vapor ciclo abierto o cerrado |
Alternativo | Máquina de vapor ciclo abierto o cerrado | |
Fluido no condensable |
Turbomáquina | Turbina de gas de ciclo cerrado |
Alternativo | Motor Stirling | |
- NOTA: Los motores volumétricos rotativos y de reacción no han sido desarrollados.
Bibliografía
- Tecnología industrial II. España: Everest Sociedad Anónima. 2014. p. 440. ISBN 9788424190538.
Referencias
- Flórez, Jesús Andres Alvarez; Agramunt, Ismael Callejón; Farrús, Sergi Forns; Carles, Pere Roca; Grande, David Balsells; Rossell, Juan Casanova; Odriozola, Tomás Navarro; Freixa, Carles Forcadell et al. (31 de diciembre de 2004). Máquinas térmicas motoras (volum I). Univ. Politèc. de Catalunya. ISBN 9788498802047. Consultado el 15 de febrero de 2018.
- SÁNCHEZ, JOSÉ ANTONIO FIDALGO; PÉREZ, MANUEL FERNÁNDEZ; FERNÁNDEZ, FERNÁNDEZ NOEMÍ (2016). Tecnología Industrial II. Ediciones Paraninfo, S.A. ISBN 9788428333085. Consultado el 15 de febrero de 2018.