Rodamiento
Un rodamiento (también denominado cojinete con rodillos)[1] es un tipo de cojinete que transmite a un bastidor las cargas procedentes del eje rotatorio que soporta, utilizando elementos rodantes (como bolas o rodillos) confinados entre dos anillos provistos de surcos de rodadura para permitir su giro. El movimiento relativo de los surcos hace que los elementos rodantes presenten una reducida resistencia a la rodadura y un deslizamiento muy pequeño.
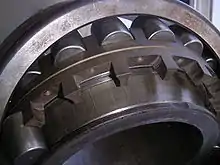
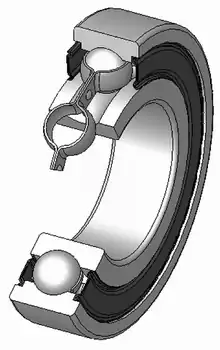
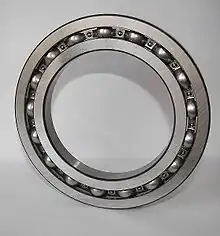
Los rodamientos presentan la ventaja de ser una buena solución de compromiso entre factores como costo, tamaño, peso, capacidad de carga, durabilidad, precisión o la fricción resultante.
Distintos diseños pueden ser mejores para un cometido específico, pero peores en la mayoría de los casos restantes, aunque los cojinetes de fluidos a veces pueden combinar simultáneamente capacidad de carga, durabilidad, precisión, fricción reducida, velocidad de rotación elevada, y en algunas ocasiones, un costo aceptable.
Solo los cojinetes de deslizamiento se usan de forma tan general como los rodamientos, que tienen una amplia presencia en componentes mecánicos comunes en diversas aplicaciones en los campos de la automoción, la industria, la navegación y la aviación. Dada su importancia, se han convertido en productos fundamentales de la tecnología moderna.
Denominaciones en español
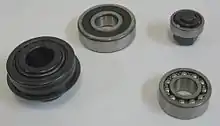
El rodamiento[2] (nombre habitual en España y Chile), recibe diversas denominaciones en distintos países hispanoparlantes: rolinera (en Venezuela); informalmente o vulgarmente bolillero, rulemán o rulimán[3] (en Argentina, Paraguay y Uruguay, derivado del francés «roulement»); rolinera, rodacho, balinera o balero (en Colombia, México, Panamá, Nicaragua y resto de Centroamérica); rodaje (en Perú); caja de bolas (en Cuba, República Dominicana y Puerto Rico); rol (en Costa Rica) o también bolillero, rodaje o rulimán (en Ecuador); o simplemente cojinete (como se le llama en Guatemala).
Así mismo, a los rodamientos montados en una pieza se les conoce como chumaceras en Colombia, Ecuador y otros países de Hispanoamérica. Los rodamientos axiales son llamados también rodamientos de empuje y los radiales de soporte.
Fundamento mecánico

Uno de los primeros y más conocidos cojinetes de elementos rodantes son los conjuntos de troncos colocados en el suelo con un gran bloque de piedra encima. A medida que se tira de la piedra, los troncos ruedan por el suelo con poco deslizamiento, evitando la fricción resultante de arrastrarla directamente sobre el terreno. A medida que cada tronco sale por la parte de atrás, se mueve hacia la parte frontal, donde el bloque rueda de nuevo sobre él.
Un cojinete giratorio con elementos rodantes utiliza un eje insertado en un orificio mayor que su diámetro, y se vale de una serie de cilindros denominados "rodillos" con los que se llena perimetralmente el espacio entre el eje y el orificio. A medida que gira el eje, cada rodillo actúa como los troncos del ejemplo anterior. Sin embargo, dado que el rodamiento es redondo, los rodillos nunca quedan por fuera de la carga.
Historia

El rodamiento se desarrolló a partir de una base firme consolidada durante miles de años, y su historia se remonta a más de siete siglos a. C. Durante las excavaciones de unos carros de guerra celtas, se descubrieron pequeñas piezas cilíndricas de madera de haya cerca de los bujes. Los investigadores concluyeron que el pueblo celta ya en el año 700 a. C. conocía el rodamiento de rodillos cilíndricos.[4]
El concepto surgió en su forma primitiva en la antigua Roma.[5] Los rodamientos fueron descritos por Vitruvio, y hacia el final de la República se utilizaban rodamientos de bolas en los polipastos.
Durante el rescate de los barcos de Nemi junto a la villa del emperador Calígula (que reinó entre el 37 y el 41 d. C.), se encontró un rodamiento que podría haber pertenecido a la base de una estatua giratoria.[6]
Después de un largo período inactivo en la Edad Media, el rodamiento fue revivido durante el Renacimiento por Leonardo da Vinci, siendo desarrollado de manera constante en los siglos XVII y XVIII.
En el curso de la industrialización, surgió la necesidad de un cojinete que se comportara mejor que los cojinetes lisos, que se desgastan muy rápidamente incluso a bajas velocidades y/o con una lubricación insuficiente. En las primeras locomotoras de vapor, por ejemplo, los cojinetes de las ruedas se reemplazaban a menudo.

Los progresivos avances en la metalurgia permitieron introducir una serie de mejoras y perfeccionamientos notables:
- En 1759, el relojero británico John Harrison inventó un rodamiento de rodillos enjaulados para su tercer cronómetro marino H3.[7][8]
- En 1794, el también británico Philip Vaughan obtuvo la primera patente de un eje con un rodamiento de bolas.
- En 1869, el francés Jules Suriray recibió una patente para rodamientos de bolas para su uso en bicicletas.
- En 1883, los alemanes Friedrich Fischer y Wilhelm Höpflinger desarrollaron decisivamente la máquina rectificadora de bolas de acero en Schweinfurt (Alemania), logrando producir esferas con muy poca desviación de la forma ideal. Este logro se considera el comienzo histórico de la industria de los rodamientos.[9]
- 1890-1910: Patentes de rodamientos de bolas de industriales de la ciudad de Schweinfurt, como Friedrich Fischer, Wilhelm Höpflinger, Ernst Sachs y August Riebe.
- En 1898, Henry Timken solicitó una patente para el rodamiento de rodillos cónicos en Estados Unidos, origen de la Timken Company.
- 1898-1901: Los fundamentos de la tecnología de elementos rodantes fueron examinados científicamente por primera vez por el Instituto de Investigación Técnica de Potsdam-Neubabelsberg bajo la dirección de Richard Stribeck.
- 1907: Sven Wingquist inventó el rodamiento de bolas a rótula y fundó la empresa sueca SKF en Gotemburgo.
- 1934: Erich Franke inventó el rodamiento con cercos de alambre basado en el principio de cables insertados.
Desde finales del siglo XIX, la industria metalúrgica alemana tuvo un gran protagonismo en el desarrollo de los rodamientos, adquiriendo un destacado papel en esta tecnología de precisión que ha mantenido con el paso de los años:
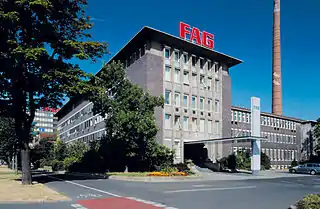
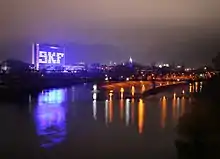
- En 1883, como ya se ha señalado, Friedrich Fischer construyó la primera máquina rectificadora de bolas en Schweinfurt y sentó las bases para la producción industrial de bolas redondas de acero con suficiente precisión para la industria de los rodamientos. En el mismo año fundó la empresa Kugelfischer. Su empleado Wilhelm Höpflinger hizo avances significativos en el desarrollo de la máquina rectificadora de bolas, y en 1890 y fundó la empresa Fries & Höpflinger junto con Engelbert Fries, también en Schweinfurt. "Los tres grandes" Kugelfischer, Fries & Höpflinger y Fichtel & Sachs consolidaron la posición de Schweinfurt como el centro de la industria alemana y europea de los rodamientos.
- Alrededor de 1910: aparecen otros productores alemanes de rodamientos de rodillos como Deutsche Waffen- und Munitionsfabriken AG Berlin-Karlsruhe (DWM), Maschinenfabrik Rheinland (Düsseldorf), Riebe-Werk (Berlín), Deutsche Kugellagerfabrik (DKF, Leipzig), Fritz Hollmann (Wetzlar), y G. y J. Jäger (Wuppertal).
- 1912: SKF adquiere una participación en la Norma-Compagnie, fundada por Albert Hirth en Stuttgart-Cannstatt.
- 1929: Bajo la presión de SKF, seis fabricantes alemanes de rodamientos (Fichtel & Sachs, Berlin-Karlsruher Industriewerke (DWF), Fries & Höpflinger, Maschinenfabrik Rheinland, Riebe-Werk y SKF-Norma) se unieron bajo el liderazgo sueco para formar juntos la fábrica de rodamientos de bolas United AG (VKF, de Schweinfurt). FAG Kugelfischer fue el único fabricante alemán de rodamientos de cierta reputación que se mantuvo independiente. Las dos empresas de Schweinfurt, VKF y FAG Kugelfischer, fueron los principales fabricantes alemanes de rodamientos de rodillos durante las siguientes décadas.
- 1933: Kugelfischer adquirió G. & J. Jaeger GmbH, de Wuppertal-Elberfeld.
- 1943–1945: Durante la Segunda Guerra Mundial, quince grandes ataques aéreos de británicos y estadounidenses dañaron gravemente la ciudad de Schweinfurt y sus instalaciones de producción de la industria de rodamientos.
- 1946: Georg y Wilhelm Schaeffler fundaron la empresa INA-Nadellager en Herzogenaurach.
- En 1949, Erich Franke y Gerhard Heydrich fundaron la empresa Franke & Heydrich KG, actualmente Franke GmbH, en Aalen. Erich Franke inventó el rodamiento con cercos de alambre en 1934, basado en el principio de cables insertados.
- 1953: United Ball Bearing Factory (VKF) pasó a llamarse SKF Deutschland GmbH, con sede en Schweinfurt.
- 1991: FAG Kugelfischer adquirió del fideicomiso el fabricante de rodamientos de la RDA DKF de Leipzig. Este compromiso resultó ser económicamente insostenible y en 1993 FAG Kugelfischer se encontró en una grave situación financiera que amenazó su existencia.
- 2001: INA-Holding Schaeffler KG, hasta entonces una empresa no muy conocida, tomó el control mediante una adquisición hostil del grupo FAG Kugelfischer, la primera empresa en formar parte del índice bursátil DAX en Alemania después de la guerra.
- 2006: FAG Kugelfischer e INA se fusionaron en Schaeffler KG y se convirtieron así en el segundo grupo de rodamientos más grande del mundo tras SKF, propietaria a su vez de la mayor planta de producción a escala mundial que también se encuentra en Alemania (Schweinfurt).
Con el paso del tiempo, se han agregado numerosas variantes al diseño de los rodamientos. En particular, se ha continuado investigando para incrementar la precisión de fabricación y el desarrollo de lubricantes cada vez más eficaces. Distintas normas también fijaron dimensiones estándar para su uso general, lo que simplificó su diseño y fabricación. Actualmente, los rodamientos industriales con estrictos requisitos de mantenimiento se ofrecen con sensores electrónicos integrados, capaces de monitorizar las tensiones y de medir el desgaste de los elementos mecánicos.
Diseño
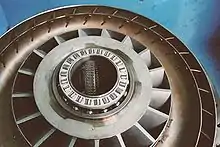
![]() |
![]() Rodamientos de empuje de bolas |

Los rodamientos se utilizan frecuentemente para soportar ejes de elementos rotativos debido a su baja fricción de rodadura. Su tamaño puede variar desde los 10 mm hasta unos pocos metros de diámetro, y tienen una capacidad de carga que va desde unas pocas decenas de gramos hasta muchos miles de toneladas. En la mayoría de los casos cuentan con jaulas, que reducen la fricción y el desgaste al evitar que los rodillos rocen entre sí. Dada la gran variedad de aplicaciones en las que pueden utilizarse, su diseño ha evolucionado hacia distintas configuraciones, orientadas a resistir cargas axiales, radiales o la combinación de ambas. En este sentido, los rodamientos de bolas suelen ser de propósito general, pero cuando se deben resistir grandes cargas radiales se tiende a recurrir a rodillos cilíndricos, cuando los esfuerzos radiales y axiales tienen importancia a la vez, por lo general se emplean elementos cónicos, y para cargas axiales considerables se utilizan rodamientos de empuje.
Por otro lado, las pistas de rodadura suelen ser anulares, como en el caso de los rodamientos de bolas, los cilíndricos o los cónicos, pero cuando se trata de disponer que el eje pueda desviarse ligeramente de su alineación teórica sin dañar el rodamiento (comportándose como una rótula), se suelen disponer pistas de rodadura esféricas o toroidales. Un caso especial es el de las pistas anulares dentadas, cuyo funcionamiento es similar al de un mecanismo epicíclico.
Atendiendo a su geometría, se pueden distinguir cinco tipos fundamentales de elementos rodantes que se utilizan en los rodamientos:
- Bolas esféricas
- Cilíndricos o agujas (cilíndricos muy alargados)
- Con forma de barril (tanto simétricos como con las bases de distinto radio)
- Diábolos (con forma de reloj de arena)
- Cónicos
Las pistas o surcos por los que ruedan pueden ser de cinco formas fundamentales:
- Anular
- Anular dentada
- Cónica
- Esférica
- Toroidal
Y la posición relativa de la pista de rodadura con respecto al eje de giro admite dos configuraciones principales:
- Rodadura radial (las bandas de rodadura son dos anillos concéntricos inscritos en dos superficies cilíndricas cuyo eje coincide con el eje de giro)
- Rodadura axial (las bandas de rodadura son dos anillos paralelos situados en dos planos perpendiculares al eje de giro)
En cuanto a la combinación de rodillos y rodaduras, no todas son posibles. Las bolas y los cilíndricos se utilizan con pistas anulares (con cilindros dentados en el caso de pistas dentadas); los rodillos cónicos requieren una pista también cónica, y los que tienen forma de barril se usan con rodaduras esféricas o toroidales (aunque también existen diseños de rodadura esférica que usan dos hileras de bolas). A continuación se describen los tipos más frecuentes.
Clasificación
La clasificación general de los rodamientos se establece según el tipo de elementos rodantes (bolas o rodillos de distintas formas), la dirección de la carga y la posible inclusión de desalineación de ejes (rodadura esférica):
Radiales | Radiales-axiales | Axiales |
Rodamientos de bolas | ||
![]() ![]() ![]() |
![]() ![]() ![]() |
![]() ![]() |
Rodamiento de bolas rígido y rodamientos de bolas autoalineables simple y doble |
Rodamientos de bolas angulares simple y doble y rodamiento de cuatro puntos |
Rodamientos de empuje de bolas rígido y autoalineable |
Rodamientos de rodillos | ||
![]() ![]() ![]() |
![]() ![]() ![]() |
![]() |
Rodamiento de rodillos cilíndricos (también de agujas), y rodamientos de rótula de rodillos de barril simples o dobles |
Rodamiento de rodillos cónicos, rodamiento de rodillos cilíndricos cruzados, y rodamiento de rodillos oscilantes axiales |
Rodamiento de empuje de rodillos cilíndricos |
Según la dirección de la carga, se hace una distinción entre rodamientos radiales y axiales (o de empuje). El "ángulo de presión" formado entre el "plano radial" y la "línea de presión" se utiliza para establecer las distintas categorías. La posición de la línea de presión depende en gran medida de los elementos rodantes y de la disposición de las pistas de rodadura.
- Rodamientos radiales:
- Rodamientos axiales:
- Rodamientos radiales-axiales: con un diseño intermedio que introduce restricciones geométricas a las pistas de rodadura
Tipos
Rodadura radial
En esta categoría se han incluido todos aquellos rodamientos en los que las pistas de rodadura son anillos concéntricos que no están dispuestos en dos planos paralelos entre sí, aunque algunos de ellos tienen capacidad de resistir tanto cargas radiales como axiales.
Rodamientos de bolas
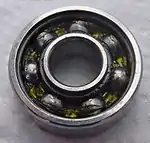

Un tipo particularmente común de cojinete de elementos rodantes es el rodamiento de bolas. Posee dos surcos, uno interno y otro externo, entre los que rueda un conjunto de bolas. Cada surco presenta un perfil ranurado generalmente con una forma diseñada para que las bolas queden ligeramente sueltas. Así, en principio, las bolas contactan con cada banda de rodadura a través de un área muy estrecha. Sin embargo, una carga en un punto infinitamente pequeño causaría una presión de contacto infinitamente alta. En la práctica, las bolas se deforman (aplanan) levemente donde hacen contacto con cada pista (algo parecido a como se aplana un neumático donde hace contacto con la carretera). A su vez, los surcos también ceden ligeramente donde son presionados por cada bola. Por tanto, el contacto entre la bola y la pista es de tamaño finito y tiene una presión finita. La bola deformada y la pista no ruedan de forma completamente uniforme porque diferentes partes de la bola se mueven a diferentes velocidades mientras rueda. Por lo tanto, hay fuerzas opuestas y movimientos deslizantes en cada contacto entre la bola y el surco, que causan un efecto de arrastre en los cojinetes.
![]() Rodamiento rígido de bolas |
![]() Rodamiento rígido de bolas de doble hilera |
![]() Rodamientos de bolas de hombro y |
![]() de contacto angular de una hilera |
Existen dos tipos fundamentales:
- Rodamientos radiales de bolas:
- También conocidos como rodamientos de bolas rígidos para distinguirlos de los que poseen efecto rótula, son usados en una gran variedad de aplicaciones. Son fáciles de diseñar, no separables, capaces de operar en altas e incluso muy altas velocidades y requieren poca atención o mantenimiento en servicio. Estas características, unidas a su precio ventajoso, hacen que sean los rodamientos más utilizados. Son capaces de soportar grandes cargas radiales, pero no empujes axiales elevados. Se usan por ejemplo, en bicicletas.
- Rodamientos radiales-axiales de bolas:
- Poseen una hilera de bolas, cuyas pistas de rodadura están diseñadas para facilitar un contacto angular, de forma que la presión ejercida por las bolas es aplicada oblicuamente con respecto al eje. Como consecuencia de esta disposición, el rodamiento es especialmente apropiado para soportar no solamente cargas radiales, sino también grandes cargas axiales, debiendo montarse en contraposición con otro rodamiento que pueda recibir carga axial en sentido contrario.

Rodamientos de rodillos cilíndricos

Los rodamientos de rodillos cilíndricos son el primer tipo de cojinete con elementos rodantes, y se remontan al menos al año 40 a. C. Los diseños más comunes usan cilindros de una longitud ligeramente mayor que el diámetro. Suelen tener una mayor capacidad de carga radial que los rodamientos de bolas, pero una menor capacidad y mayor fricción bajo cargas axiales. Si las pistas de rodadura interna y externa están desalineadas, la capacidad de carga a menudo cae rápidamente en comparación con un rodamiento de bolas o con un rodamiento de rodadura esférica.
Como en todos los rodamientos radiales, la carga exterior se redistribuye continuamente entre los rodillos (en especial, cuando se trata de ruedas dispuestas verticalmente). A menudo, menos de la mitad del número total de rodillos soportan una parte significativa de la carga. La animación de la derecha muestra cómo los rodillos del rodamiento soportan una carga radial estática a medida que gira el aro interior.
Un rodamiento de rodillos cilíndricos normalmente tiene una hilera de rodillos guiados por pestañas de uno de los aros, mientras que el otro aro puede tener pestañas o no.
Según sea la disposición de las pestañas, hay varios tipos de rodamientos de rodillos cilíndricos:
- Tipo NU: con dos pestañas en el aro exterior y sin pestañas en el aro interior. Sólo admiten cargas radiales, son desmontables y permiten desplazamientos axiales relativos del alojamiento y eje en ambos sentidos.
- Tipo N: con dos pestañas en el aro interior y sin pestañas en el aro exterior. Sus características similares al anterior tipo.
- Tipo NJ: con dos pestañas en el aro exterior y una pestaña en el aro interior. Puede utilizarse para la fijación axial del eje en un sentido.
- Tipo NUP: con dos pestañas integrales en el aro exterior y con una pestaña integral y dos pestañas en el aro interior. Una de las pestañas del aro interior no es integral, es decir, es similar a una arandela para permitir el montaje y el desmontaje. Se utilizan para fijar axialmente un eje en ambos sentidos.
Los rodamientos de rodillos son más rígidos que los de bolas y se utilizan para cargas pesadas y ejes de gran diámetro.
Rodamientos de agujas

Los rodamientos de agujas utilizan cilindros muy largos y delgados, de pequeño diámetro. A menudo, los extremos de los rodillos se estrechan en puntas, que se utilizan para mantenerlos cautivos, o pueden ser semiesféricos y no cautivos, pero sostenidos por el propio eje o con alguna disposición similar. Dado que los rodillos son delgados, el diámetro exterior del cojinete es solo un poco más grande que el orificio central. Sin embargo, los rodillos de diámetro pequeño se flexionan bruscamente donde hacen contacto con las pistas de rodadura y, por lo tanto, puede experimentar problemas de fatiga relativamente rápido.
A pesar de su pequeña sección, estos rodamientos tienen una gran capacidad de carga y son especialmente apropiados para las aplicaciones donde el espacio radial es limitado. Este tipo de rodamientos es comúnmente muy utilizado en los pedales para bicicletas y en muchos tipos de avionetas.
Rodamientos de engranaje

En un rodamiento de engranaje se combinan rodillos dentados para formar un engranaje epicicloidal. Está formado por unos rodillos cuyos dentados hacen que engranen en los surcos de rodadura, que también disponen de un sistema de dientes conjugados, que suelen tener forma de espiga o una disposición oblicua para lograr un contacto axial de rodadura más eficiente. La principal desventaja de este rodamiento es su complejidad de fabricación. Se han usado para la suspensión de elementos rotativos y como mecanismo de engranaje planetario cinemáticamente simplificado en instrumentos de medición y relojes mecánicos.
Rodamientos de rodillos cónicos

Estos rodamientos utilizan rodillos cónicos que se desplazan sobre pistas cónicas. La mayoría de los rodamientos solo aceptan cargas radiales o axiales, pero los rodamientos de rodillos cónicos soportan cargas tanto radiales como axiales y, en general, pueden soportar cargas más altas que los rodamientos de bolas debido a su mayor área de contacto. Se utilizan, por ejemplo, en las ruedas de la mayoría de los vehículos terrestres. La desventaja de este rodamiento es que, debido a su complejidad de fabricación, suelen ser más caros que los rodamientos de bolas; y además, bajo cargas pesadas, el rodillo cónico se comporta como una cuña y las cargas que soportan tienden a tratar de expulsar el rodillo. En consecuencia, la fuerza del collarín que mantiene el rodillo en el rodamiento aumenta la fricción del rodamiento si se compara con los rodamientos de bolas.
El rodamiento de rodillos cónicos, debido a la posición oblicua de los rodillos y caminos de rodadura, es especialmente adecuado para resistir cargas radiales y axiales simultáneas. Para casos en que la carga axial es muy importante hay una serie de rodamientos cuyo ángulo es muy abierto. Este rodamiento debe montarse en oposición con otro rodamiento capaz de soportar los esfuerzos axiales en sentido contrario. El rodamiento es desmontable; el aro interior con sus rodillos y el aro exterior se montan cada uno separadamente.
Rodamientos de rodadura esférica
![]() Rodamiento de rodillos a rótula |
![]() Rodamiento de bolas a rótula |
Un rodamiento de rodadura esférica se comporta parcialmente como una rótula, gracias a que dispone de un anillo exterior con la pista de rodadura de perfil esférico. Los rodillos, con forma de barril, son más gruesos en el medio y más delgados en los extremos. Puede adaptarse tanto a la desalineación estática como a la dinámica. Sin embargo, son un tipo de rodamientos difíciles de producir y, por lo tanto, costosos, y presentan una fricción mayor que un rodamiento de rodillos cilíndricos o cónicos ideal, ya que deben tolerar una cierta cantidad de deslizamiento entre los elementos rodantes y los anillos que los contienen.
Son utilizados en aplicaciones donde pueden producirse desalineaciones considerables, por ejemplo, por efecto de las dilataciones, de flexiones en el eje o por el modo de construcción. De esta forma, disponen de dos grados de libertad, correspondientes al giro del aro interior respecto a los dos ejes geométricos perpendiculares al eje del aro exterior. Este tipo de rodamientos tienen menor fricción que otros tipos, por lo que se calientan menos en las mismas condiciones de carga y velocidad, siendo aptos para mayores velocidades.
Existen dos tipos principales:
- Rodamiento de rodillos a rótula:
- Sus rodillos tienen forma de barril. Dispone de dos hileras de rodillos con una pista de rodadura esférica común en el aro exterior siendo, por lo tanto, de alineación automática. El número y tamaño de sus rodillos le dan una capacidad de carga muy grande. La mayoría de las series puede soportar fuertes cargas radiales y también cargas axiales considerables en ambas direcciones.
- Rodamiento de bolas a rótula:
- Tiene dos hileras de bolas que se apoyan sobre una pista de rodadura esférica en el aro exterior, permitiendo desalineaciones angulares del eje respecto al soporte.
Rodamientos de rodadura toroidal (CARB)
Los CARB son rodamientos de rodadura toroidal, similares a los rodamientos de rodadura esférica, pero pueden adaptarse tanto a la desalineación angular como al desplazamiento axial.[10] En comparación con un rodamiento de rodadura esférica, su radio de curvatura es mayor, lo que los convierte en una forma intermedia entre los de rodadura esférica y los cilíndricos. Generalmente se usan formando una pareja con otro rodamiento que fija axialmente el eje, que suele ser un rodamiento de rodadura esférica.[10] Esta rodadura libre puede ser una ventaja, ya que se puede utilizar para permitir que un eje y el soporte que lo aloja experimenten expansiones térmicas de forma independiente.
Los rodamientos de rodadura toroidal fueron introducidos en 1995 por la compañía SKF como "rodamientos CARB".[11] Su inventor fue el ingeniero Magnus Kellström.[12]
Rodadura axial
![]() Rodamiento de empuje con cilindros |
![]() Rodamiento axial a rótula |
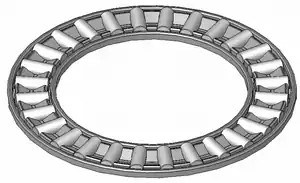

En esta categoría se han incluido aquellos rodamientos en los que los anillos de rodadura son iguales y están dispuestos en dos planos paralelos, entre los que ruedan los rodillos o bolas.
Rodamientos de empuje
Los rodamientos de empuje o axiales, como su nombre indica, están diseñados para soportar esfuerzos axiales, como los transmitidos por ejes verticales. Diseños comunes son los rodamientos de empuje, los rodamientos de empuje de rodadura esférica, los rodamientos axiales de rodillos cónicos o los rodamientos axiales de rodillos cilíndricos.
Existen varios tipos:
- Rodamiento axial de bolas de simple efecto:
- Consta de una hilera de bolas entre dos aros, uno de los cuales, el aro fijo al eje, es de asiento plano, mientras que el otro, el aro apoyado en el soporte, puede tener asiento plano o esférico. En este último caso, el rodamiento se apoya en una contraplaca. Los rodamientos con asiento plano deberían, sin duda, preferirse para la mayoría de las aplicaciones, pero los de asiento esférico son muy útiles en ciertos casos, para compensar pequeñas inexactitudes de fabricación de los soportes. El rodamiento está destinado a resistir solamente carga axial en una dirección. Un ejemplo son los rodamientos del eje de giro del manillar de una bicicleta.
- Rodamientos de empuje de aguja:
- Diseñados para soportar cargas axiales pesadas, son insensibles a las cargas de choque y se utilizan en aplicaciones que exijan una gran resistencia, requiriendo un mínimo de espacio axial.
- Rodamientos de empuje de rodillos cilíndricos:
- Son apropiados para aplicaciones que deben soportar cargas axiales pesadas. Además, también son insensibles a los choques, son fuertes y requieren poco espacio axial. Solamente pueden recibir cargas axiales en un sentido (en el que los rodillos quedan comprimidos). Su uso principal es en aplicaciones donde la capacidad de carga de los rodamientos de empuje de bolas es insuficiente.
- Rodamientos axiales de rodillos a rótula:
- El rodamiento axial de rodillos a rótula tiene una hilera de rodillos situados oblicuamente, que guiados por una pestaña del aro fijo al eje, giran sobre la superficie esférica del aro apoyado en el soporte. En consecuencia, el rodamiento posee una gran capacidad de carga y es de alineación automática. Debido al diseño de la superficie de apoyo de los rodillos en la pestaña de guía, los rodillos giran separados de la pestaña por una fina capa de aceite. El rodamiento puede, por lo mismo, girar a una gran velocidad mientras soporta cargas elevadas. Contrariamente a los otros rodamientos axiales, también puede resistir cargas radiales.
Rodamientos de movimiento lineal
Los rodamientos de movimiento lineal generalmente están diseñados para ejes o superficies planas. A menudo son cilindros montados en un armazón, que luego se coloca entre dos superficies planas. Un ejemplo común son los herrajes de soporte de un cajón. También existen rodamientos especiales que permiten el desplazamiento lineal de un eje, que se valen de bolas de rodamiento insertadas en una ranura diseñada para que recirculen de un extremo al otro a medida que se desplaza el eje respecto al rodamiento. Se denominan rodamientos lineales de bolas[13] o rodamientos de recirculación.
Jaulas
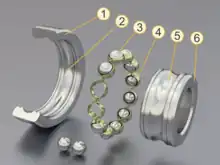
1. Anillo exterior
2. Surco exterior
3. Bolas
4. Jaula
5. Surco interior
6. Anillo interior

En los rodamientos modernos, los elementos rodantes (bolas, cilindros, agujas, barriles o conos) se mantienen a la misma distancia mediante una jaula. Los tipos de rodamientos de rodillos más antiguos y los diseños especiales no requieren de este elemento. En particular, los rodamientos en los sistemas de control de las aeronaves carecen de jaula. Como resultado, se pueden usar más elementos rodantes por rodamiento, lo que aumenta significativamente la capacidad de carga. Sin embargo, solo son adecuados para velocidades altas.
El material de la jaula solía ser latón debido a un funcionamiento más suave. Hoy en día, por razones de coste y peso, la jaula suele estar hecha de plástico poliamida (normalmente reforzado con fibra de vidrio). En muchos tipos de rodamientos se utiliza una jaula de acero sin templar de baja aleación. Las jaulas de latón se siguen usando, especialmente en los rodamientos más grandes, donde los costos del herraje necesario para producir jaulas de plástico o chapa de acero no merecen la pena.
Materiales
Los rodamientos suelen estar hechos de acero al cromo, muy duro pero fácilmente oxidable (tipo 100Cr6), un acero con un contenido de aproximadamente 1% de carbono y 1,5% de cromo. Otros aceros son, por ejemplo, los 100CrMnSi6-4 y 100CrMo7, en los que se añade manganeso (Mn) y molibdeno (Mo) para obtener una mayor dureza y resistencia al desgaste.
Para aplicaciones en ambientes corrosivos, se utilizan aceros de alta aleación como el X65Cr13 y el X30CrMoN15-1. Este último también se puede utilizar en el organismo humano, al menos durante unos días. Los aceros templables nunca son completamente "inoxidables", sino que solo tienen una mayor resistencia a la corrosión durante un cierto período de tiempo.
Existen rodamientos para condiciones de funcionamiento especiales:
- De acero inoxidable para ambientes agresivos
- De dos materiales, donde los anillos del rodamiento son de acero y los elementos rodantes son de cerámica (nitruro de silicio o dióxido de circonio), por ejemplo en rodamientos para husillos de máquinas herramienta
- Rodamientos cerámicos donde tanto los anillos del rodamiento como los elementos rodantes están hechos de nitruro de silicio, dióxido de zirconio o carburo de silicio
- Cojinetes de plástico con elementos rodantes de vidrio o cerámica resistente contra ácidos o lejías agresivos en la industria química y alimentaria
- Rodamientos con jaula de plástico para obtener un funcionamiento silencioso
- Rodamientos con un revestimiento aislante de corriente en el anillo exterior o interior, con el fin de evitar el paso de corriente no deseado a través del rodamiento y, por lo tanto, el daño causado por la corrosión eléctrica, como por ejemplo cuando se utilizan convertidores de frecuencia para controlar la velocidad de motores trifásicos
Aplicaciones
Los rodamientos se emplean en aplicaciones que requieren trabajar con baja fricción a bajas velocidades y altas cargas, y donde las velocidades cambian con frecuencia.
Ventajas de los rodamientos de rodillos frente a los cojinetes lisos | Desventajas de los rodamientos de rodillos frente a los cojinetes lisos |
---|---|
|
|
Instalación
|
Los rodamientos generalmente se montan en semiejes o ejes.
En el caso de diseños especiales (sin aro interior y exterior separados), las superficies de rodadura rectificadas o laminadas y templadas se pueden presionar directamente sobre el eje y/o en la carcasa del cojinete y, por lo tanto, el rodamiento se puede integrar en estos componentes. Esta solución se elige principalmente por razones de espacio. Por lo tanto, los rodillos de agujas en particular son muy adecuados para este cometido.
Los rodamientos a menudo se aseguran para evitar su deslizamiento con un anillo de retención, una contratuerca o un manguito espaciador. Para protegerse contra la contaminación, se instalan con una carcasa o se cubren con un sello retenedor del lubricante.
Para no dañar el cojinete, la presión ejercida durante la instalación no debe transmitirse a través de los elementos rodantes. Con herramientas especiales como, por ejemplo, un manguito de arrastre, el rodamiento solo se introduce a través del aro exterior. Los cojinetes de agujas se deben presionar con un mandril.
Con rodamientos grandes, las fuerzas de presión también son mayores, por lo que se calientan a 80-100 °C en un baño de aceite o con un calentador eléctrico antes del montaje. Los anillos se expanden mínimamente y, por lo tanto, se pueden presionar más fácilmente sobre el eje.
A su vez, al retirar los rodamientos, es necesario asegurarse de utilizar la herramienta adecuada. Existen numerosos tipos de soportes normalizados que permiten alojar rodamientos en su interior, utilizados en el diseño de numerosos tipos de máquinas.
Fallo de un rodamiento

Los rodamientos suelen funcionar bien en condiciones no ideales, pero problemas menores a veces hacen que fallen rápida y misteriosamente. Por ejemplo, con una carga estacionaria (no giratoria), las pequeñas vibraciones pueden expulsar gradualmente el lubricante entre las pistas y los rodillos o las bolas (falso punzonamiento). Sin lubricante, el rodamiento falla, aunque no esté girando y, por lo tanto, aparentemente no se esté utilizando. Por este tipo de razones, gran parte del diseño de rodamientos tiene que ver con el análisis de fallos. El análisis de las vibraciones registradas se puede utilizar para la identificación de fallos en los rodamientos.[14]
Hay tres límites habituales para la vida útil o la capacidad de carga de un rodamiento: la abrasión, la fatiga y la soldadura inducida por presión. La abrasión se produce cuando la superficie es erosionada por contaminantes duros que arañan los materiales del cojinete. La fatiga se produce cuando un material se vuelve quebradizo después de haberlo cargado y descargado repetidamente. Donde la bola o el rodillo tocan la pista, siempre se produce alguna deformación y, por lo tanto, existe riesgo de fatiga. Las bolas o rodillos más pequeños se deforman más bruscamente y, por lo tanto, tienden a fatigarse más rápido. La soldadura inducida por presión puede producirse cuando dos piezas de metal que están en contacto se someten a una presión muy alta y se vuelven una. Aunque las bolas, los rodillos y las pistas pueden parecer lisos, son microscópicamente ásperos. Por lo tanto, hay puntos de alta presión en el rodamiento donde tiende a expulsarse el lubricante. A veces, el contacto metal con metal resultante suelda una parte microscópica de la bola o el rodillo a la pista. A medida que el cojinete continúa girando, la soldadura se rompe, pero puede dejar un fragmento de la pista soldado al cojinete o una parte del material del cojinete soldada a la pista.
Aunque hay muchas otras causas aparentes de fallos en los rodamientos, la mayoría se puede reducir a estas tres. Por ejemplo, un rodamiento que funciona sin lubricante falla no porque esté "sin lubricante", sino porque la falta de lubricación provoca fatiga y soldadura, y los desechos de desgaste resultantes pueden causar abrasión. Fenómenos similares se dan en el daño por falso punzonamiento. En aplicaciones de alta velocidad, el flujo de aceite también reduce la temperatura del metal del cojinete por convección, y se convierte en el disipador del calor generado de las pérdidas causadas por la fricción en el rodamiento.
ISO ha categorizado los fallos de los rodamientos en un documento con el número ISO 15243.[15]
Modelos de cálculo de la vida útil
La vida útil de un rodamiento se expresa como el número de revoluciones o el número de horas de funcionamiento a una velocidad determinada que el rodamiento es capaz de soportar antes de que se produzca la primera señal de fatiga del metal (también conocida como astillado) en las pistas de rodadura interior o exterior, o en un elemento rodante. Es posible calcular la vida útil de los rodamientos con la ayuda de los llamados modelos de vida. Más específicamente, los modelos de vida útil se utilizan para determinar el tamaño del rodamiento, ya que esto debe ser suficiente para garantizar que el rodamiento sea lo suficientemente fuerte como para brindar la vida útil requerida en determinadas condiciones de funcionamiento definidas.
Sin embargo, en condiciones de laboratorio controladas, los rodamientos aparentemente idénticos que funcionan en condiciones idénticas pueden tener vidas útiles individuales diferentes. Por lo tanto, la vida útil de los rodamientos no se puede calcular en función de rodamientos específicos, sino que se relaciona en términos estadísticos, en referencia a las poblaciones de rodamientos. Toda la información con respecto a las capacidades de carga se basa entonces en la vida útil que se espera que alcance o supere el 90% de un grupo suficientemente grande de rodamientos aparentemente idénticos. Esto da una definición más clara del concepto de vida útil del rodamiento, que es esencial para calcular su tamaño correcto. Por lo tanto, los modelos de vida pueden ayudar a predecir el rendimiento de un rodamiento de manera más realista.
La predicción de la vida útil de los rodamientos se describe en la norma ISO 281[16] y en los estándares 9 y 11 del American Bearing Manufacturers Association a través del Instituto Nacional Estadounidense de Estándares.[17]
El modelo de predicción de vida tradicional para rodamientos utiliza la ecuación de vida básica:[18]
Donde:
- es la 'vida útil básica' (normalmente expresada en millones de revoluciones) para una fiabilidad del 90 %, es decir, no se espera que falle más del 10 % de los rodamientos
- es el índice de carga dinámica del rodamiento, indicado por el fabricante
- es la carga dinámica equivalente aplicada al rodamiento
- es una constante: 3 para rodamientos de bolas, 4 para contacto lineal puro y 3,33 para rodamientos de rodillos
La vida básica o es la vida que se espera que alcance o supere el 90 % de los rodamientos.[16] La vida media o promedio, a veces llamada tiempo medio entre fallos (MTBF), es aproximadamente cinco veces la vida nominal básica calculada.[18]
Se pueden usar varios factores, el 'modelo de cinco factores ASME',[19] para ajustar aún más la vida útil dependiendo de la fiabilidad, lubricación o contaminación esperables.
La principal implicación de este modelo es que la vida útil del cojinete es finita y se reduce en una potencia cúbica de la relación entre la carga de diseño y la carga aplicada. Este modelo fue desarrollado a partir de sus trabajos de 1924, 1947 y 1952 por Arvid Palmgren y Gustaf Lundberg en su artículo "Capacidad dinámica de los rodamientos".[19][20] El modelo data de 1924, y los valores de la constante de los trabajos de posguerra. Los valores más altos de se traducen en una vida útil más larga para un rodamiento usado correctamente por debajo de su carga de diseño, o también como una mayor tasa de reducción de la vida útil cuando se sobrecarga.
Se reconoció que este modelo se había vuelto inexacto para los rodamientos modernos. Particularmente debido a las mejoras en la calidad de los aceros para cojinetes, los mecanismos por los que se desarrollan los fallos en el modelo de 1924 ya no son tan significativos. En la década de 1990, se descubrió que los rodamientos reales daban una vida útil hasta 14 veces mayor que la prevista.[19] Se presentó una explicación basada en la fatiga de materiales; si el rodamiento se cargara para nunca exceder la tensión de fatiga, entonces el mecanismo de fallo por fatiga de Lundberg-Palmgren simplemente nunca se produciría.[19] Esto se basó en estudios realizados con aceros fundidos al vacío homogéneos, como el AISI 52100, que evitaban las inclusiones internas que anteriormente habían actuado como elevadores de tensión dentro de los elementos rodantes, y también en acabados más suaves para las pistas de rodamiento que evitaban las cargas de impacto.[17] La constante ahora tenía valores de 4 para rodamientos de bolas y de 5 para rodamientos de rodillos. Siempre que se observaran los límites de carga, la idea de un 'límite de fatiga' entró en los cálculos de la vida útil del rodamiento: si el rodamiento no se cargaba más allá de este límite, su vida útil teórica estaría limitada solo por factores externos, como la contaminación o un fallo de lubricación.
FAG presentó un nuevo modelo de vida útil del rodamiento, que desarrolló SKF como el modelo Ioannides-Harris.[20][21] La norma ISO 281:2000 incorporó por primera vez este modelo y la ISO 281:2007 se basa en él.
El concepto de límite de fatiga y, por tanto, la norma ISO 281:2007 sigue siendo controvertido, al menos en EE. UU.[17][19]
Modelo generalizado de vida útil del rodamiento (GBLM)
En 2015, se introdujo el Modelo generalizado de vida útil de los rodamientos (GBLM por sus siglas en inglés) de SKF.[22] A diferencia de los modelos de vida anteriores, el método GBLM separa explícitamente los modos de fallo de la superficie y del soporte, lo que hace que el modelo sea flexible para adaptarse a varios modos de fallo diferentes. Los rodamientos y las aplicaciones modernas muestran menos fallos, pero que están más relacionados con las tensiones superficiales. Al separar la superficie del soporte, se pueden identificar más fácilmente los mecanismos de mitigación. El método hace uso de modelos tribológicos avanzados[23] para introducir una función de modo de fallo por fallos superficiales, obtenida a partir de la evaluación de la fatiga superficial. Para la fatiga del soporte, el método GBLM utiliza el modelo de contacto rodante hertziano clásico. Además, incluye los efectos de la lubricación, la contaminación y las propiedades de la superficie del camino de rodadura, que en conjunto influyen en la distribución de tensiones en el contacto rodante.
En 2019 se relanzó el Modelo Generalizado de Vida del Rodamiento. El modelo actualizado también ofrece cálculos de vida útil para rodamientos híbridos, es decir, rodamientos con anillos de acero y elementos rodantes de cerámica (nitruro de silicio).[24][25] Incluso si la versión GBLM de 2019 se desarrolló principalmente para determinar de manera realista la vida útil de los rodamientos híbridos, el concepto también se puede usar para otros productos y modos de fallo.
Restricciones de diseño
Todas las partes de un rodamiento están sujetas a muchas restricciones de diseño. Por ejemplo, las pistas interior y exterior suelen tener formas complejas, lo que dificulta su fabricación. Las bolas y los rodillos, aunque de forma más simple, son pequeños; dado que se flexionan bruscamente donde corren en las pistas, los rodamientos son propensos a fatigarse. Las cargas dentro de un conjunto de rodamientos también se ven afectadas por la velocidad de funcionamiento: los rodillos pueden girar a más de 100 000 rpm y el principal esfuerzo puede estar ligado a la cantidad de movimiento en lugar de a la carga aplicada. Los elementos rodantes más pequeños son más livianos y, por lo tanto, tienen menos impulso, pero los elementos más pequeños también se flexionan más bruscamente donde hacen contacto con la pista, lo que hace que fallen más rápidamente por fatiga. Las velocidades máximas de los cojinetes de elementos rodantes a menudo se especifican en 'nDm', que es el producto del diámetro medio (en mm) y las RPM máximas. Para los rodamientos de contacto angular, se ha encontrado que nDm de más de 2,1 millones son fiables en aplicaciones de cohetes de alto rendimiento.[26]
También hay muchos problemas con los materiales: un material más duro puede ser más duradero contra la abrasión, pero es más probable que sufra fracturas por fatiga, por lo que el material varía según la aplicación, y mientras que el acero es más común para rodamientos, plásticos, vidrio y cerámica también son de uso común. Un pequeño defecto (irregularidad) en el material suele ser responsable del fallo del rodamiento; una de las mayores mejoras en la vida útil de los rodamientos comunes durante la segunda mitad del siglo XX fue el uso de materiales más homogéneos, en lugar de mejores materiales o lubricantes (aunque ambos también fueron significativos). Las propiedades del lubricante varían con la temperatura y la carga, por lo que el mejor lubricante varía según la aplicación.
Aunque los rodamientos tienden a desgastarse con el uso, los diseñadores pueden hacer concesiones entre el tamaño y el costo del rodamiento y su vida útil. Un rodamiento puede durar indefinidamente, más que el resto de la máquina, si se mantiene sin temperaturas elevadas, limpio, lubricado, funcionando dentro de la carga nominal y si los materiales del rodamiento están lo suficientemente libres de defectos microscópicos. El enfriamiento, la lubricación y el sellado son, por lo tanto, partes importantes del diseño del rodamiento.
La vida útil necesaria del rodamiento también varía según la aplicación. Por ejemplo, Tedric A. Harris informa en su "Análisis de rodamientos"[27] sobre un rodamiento de bomba de oxígeno en el transbordador STS estadounidense que no se pudo aislar adecuadamente del oxígeno líquido que bombeaba. Todos los lubricantes reaccionaron con el oxígeno, lo que provocó incendios y otros fallos. La solución fue lubricar el rodamiento con el oxígeno. Aunque el oxígeno líquido es un lubricante deficiente, era adecuado, ya que la vida útil de la bomba era de unas pocas horas.
El entorno operativo y las necesidades de servicio también son consideraciones de diseño importantes. Algunos conjuntos de rodamientos requieren la adición rutinaria de lubricantes, mientras que otros vienen sellados de fábrica, por lo que no requieren más mantenimiento durante la vida útil del conjunto mecánico. Aunque los sellos son atractivos, aumentan la fricción y, en un rodamiento sellado permanentemente, el lubricante puede contaminarse con partículas duras, como virutas de acero de la pista o el rodamiento, arena o gravilla que atraviesa el sello. La contaminación en el lubricante es un factor abrasivo y reduce en gran medida la vida útil del conjunto del rodamiento. Otra causa importante de fallo es la presencia de agua en el aceite de lubricación. Los monitores de agua en aceite en línea se han introducido en los últimos años para monitorizar los efectos de las partículas y la presencia de agua en el aceite y su efecto combinado.
Denominación técnica
Los rodamientos de elementos rodantes métricos tienen denominaciones alfanuméricas, definidas por la norma ISO 15, que sirven para definir todos sus parámetros físicos. La designación principal es un número de siete dígitos con caracteres alfanuméricos opcionales antes o después para definir parámetros adicionales. Así, los dígitos se definirán con la forma: 7654321. Cualquier cero a la izquierda del último dígito definido no se imprime; p.ej. una designación de 0007208 se imprime como 7208.[28]
Los dígitos uno y dos juntos se utilizan para definir el diámetro interior (ID) del rodamiento. Para diámetros entre 20 y 495 mm, inclusive, la designación se multiplica por cinco para dar el ID; por ejemplo, la designación 08 es un DI de 40 mm. Para diámetros interiores inferiores a 20, se utilizan las siguientes designaciones: 00 = 10 mm DI, 01 = 12 mm DI, 02 = 15 mm DI y 03 = 17 mm DI. El tercer dígito define la "serie de diámetros", que especifica el diámetro exterior (OD). La serie de diámetros, definida en orden ascendente, es: 0, 8, 9, 1, 7, 2, 3, 4, 5, 6. El cuarto dígito define el tipo de rodamiento:[28]
- 0. Radial con una hilera de bolas
- 1. Radial esférico con dos hileras de bolas
- 2. Radial con cilindros
- 3. Radial esférico con dos hileras de cilindros
- 4. Agujas o con cilindros largos
- 5. Radial con cilindros en espiral
- 6. Radial-axial con una hilera de bolas
- 7. Cónico
- 8. Axial con bolas, o axial-radial con bolas
- 9. Axial con cilindros, o axial-radial con cilindros
El quinto y sexto dígitos definen modificaciones estructurales al cojinete. Por ejemplo, en los rodamientos radiales-axiales, los dígitos definen el ángulo de contacto o la presencia de sellos en cualquier tipo de rodamiento. El séptimo dígito define la "serie de grosor", o espesor, del rodamiento. La serie de grosor, definida de más ligera a más pesada, es: 7, 8, 9, 0, 1 (serie extra ligera), 2 (serie ligera), 3 (serie media), 4 (serie pesada). El tercer dígito y el séptimo dígito definen la "serie dimensional" del rodamiento.[28][29]
Hay cuatro caracteres de prefijo opcionales, aquí definidos como A321-XXXXXXX (donde las X son la designación principal), que están separados de la designación principal con un guion. El primer carácter, A, es la clase de rodamiento, que se define en orden ascendente: C, B, A. La clase define requisitos adicionales de vibración, desviaciones de forma, tolerancias de la superficie de rodadura y otros parámetros que no están definidos por un carácter de designación. El segundo carácter es el momento friccional (la fricción que se opone al giro), que se define, en orden ascendente, por un número del 1 al 9. El tercer carácter es el juego radial, que normalmente se define con un número entre 0 y 9 (inclusive), en orden ascendente; sin embargo, para los rodamientos de radiales-axiales, se define con un número entre 1 y 3, inclusive. El cuarto carácter son las clasificaciones de precisión, que normalmente son, en orden ascendente: 0 (normal), 6X, 6, 5, 4, T y 2. Las clasificaciones 0 y 6 son las más comunes; las clasificaciones 5 y 4 se utilizan en aplicaciones de alta velocidad; y la calificación 2 se usa en giróscopos. Para rodamientos cónicos, los valores son, en orden ascendente: 0, N y X, donde 0 es 0, N es "normal" y X es 6X.[28]
Hay cinco caracteres opcionales que se pueden definir después de la designación principal: A, E, P, C y T; estos se clavan directamente al final de la designación principal. A diferencia del prefijo, no todas las designaciones deben definirse. "A" indica una clasificación de carga dinámica aumentada. "E" indica el uso de una jaula de plástico. "P" indica que se utilizan acero resistente al calor. "C" indica el tipo de lubricante utilizado (C1–C28). "T" indica el grado en que los componentes del rodamiento han sido tempered (T1–T5).[28]
Si bien los fabricantes siguen la norma ISO 15 para las designaciones de números de pieza en algunos de sus productos, es común que adopten sistemas de números de pieza patentados que no se corresponden con la norma ISO 15.[30]
Véase también
Referencias
- ISO 15
- Real Academia Española. «rodamiento». Diccionario de la lengua española (23.ª edición). 1. m. Mec. Rodamiento: Cojinete formado por dos cilindros concéntricos entre los que se intercala una corona de bolas o rodillos que ruedan sobre ambas superficies.
- Título:Vistazo, Números 128-132; Publicado en 1968
- Hans-J. Engelke (2015). SolidWorks 2015 Teil 3 Lagerungen: Baugruppentraining (en alemán). BoD – Books on Demand. pp. 6 de 564. ISBN 9783738634297. Consultado el 30 de enero de 2022.
- Hamrock, B. J.; Anderson, W. J. (1 de junio de 1983). «Rolling-Element Bearings». NASA Technical Reports Server.
- Fritz Kretzschmer (1983). «5.». En Verlag des Vereins Deutscher Ingenieure, ed. Bilddokumente römischer Technik. Düsseldorf. pp. 113–116. ISBN 3-18-400598-4.
- «20120906». nmm.ac.uk.
- Sobel, Dava (1995). Longitude. London: Fourth Estate. p. 103. ISBN 0-00-721446-4. «Un novedoso dispositivo antifricción que Harrison desarrolló para su cronógrafo H-3 ha sobrevivido hasta el día de hoy: ...cojinetes de bolas enjaulados. »
- «Schaeffler in Deutschland» (en alemán). 23 de octubre de 2018.
- «CARB toroidal roller bearings». SKF.
- «The CARB bearing – a better solution for the front side of drying cylinders». SKF. Archivado desde el original el 3 de diciembre de 2013. Consultado el 2 de diciembre de 2013.
- «CARB - a revolutionary concept». SKF. Consultado el 2 de diciembre de 2013.
- «McMaster-Carr».
- Slavic, J; Brkovic, A; Boltezar M (December 2011). «Typical bearing-fault rating using force measurements: application to real data.». Journal of Vibration and Control 17 (14): 2164-2174. S2CID 53959482. doi:10.1177/1077546311399949.
- «Daño de rodamientos y análisis de fallas». SKF. Consultado el 28 de enero de 2022.
- «Rolling bearings -- Dynamic load ratings and rating life». ISO. 2007. ISO281:2007.
- Erwin V. Zaretsky (August 2010). «In search of a fatigue limit: A critique of ISO standard 281:2007». Tribology & Lubrication Technology (Society of Tribologists and Lubrication Engineers (STLE)): 30-40. Archivado desde el original el 18 de mayo de 2015.
- Daniel R. Snyder, SKF (12 de abril de 2007). «The meaning of bearing life». Machine Design.
- «ISO 281:2007 bearing life standard – and the answer is?». Tribology & Lubrication Technology (Society of Tribologists and Lubrication Engineers (STLE)): 34-43. July 2010. Archivado desde el original el 24 de octubre de 2013.
- «ISO Adopts SKF Bearing Life Calculations». eBearing News. 28 de junio de 2006.
- Ioannides, Stathis; Harris, Ted (1985). A New Fatigue Life Model for Rolling Bearings. SKF.
- Morales-Espejel, Guillermo E.; Gabelli, Antonio; de Vries, Alexander J. C. (2015). «A Model for Rolling Bearing Life with Surface and Subsurface Survival—Tribological Effects». Tribology Transactions 58 (5): 894-906. S2CID 137670935. doi:10.1080/10402004.2015.1025932.
- Morales-Espejel, Guillermo E.; Brizmer, Victor (2011). «Micropitting Modelling in Rolling–Sliding Contacts: Application to Rolling Bearings». Tribology Transactions 54 (4): 625-643. S2CID 137662003. doi:10.1080/10402004.2011.587633.
- Morales-Espejel, Guillermo E.; Gabelli, Antonio (April 2016). «A model for rolling bearing life with surface and subsurface survival: Sporadic surface damage from deterministic indentations». Tribology International 96: 279-288. doi:10.1016/j.triboint.2015.12.036.
- Morales-Espejel, Guillermo E; Gabelli, Antonio (2019). «Application of a rolling bearing life model with surface and subsurface survival to hybrid bearing cases». Proceedings of the Institution of Mechanical Engineers, Part C 233 (15): 5491-5498. S2CID 164456996. doi:10.1177/0954406219848470.
- Design of liquid propellant rocket engines -Dieter K. Huzel and David H.Huang pg.209
- Harris, Tedric A. (2000). Rolling Bearing Analysis (4th edición). Wiley-Interscience. ISBN 0-471-35457-0.
- Grote, Karl-Heinrich; Antonsson, Erik K. (2009). Springer handbook of mechanical engineering 10. New York: Springer. pp. 465-467. ISBN 978-3-540-49131-6.
- Brumbach, Michael E.; Clade, Jeffrey A. (2003), Industrial Maintenance, Cengage Learning, pp. 112-113, ISBN 978-0-7668-2695-3..
- Renner, Don; Renner, Barbara (1998). Hands on Water and Wastewater Equipment Maintenance. CRC Press. p. 28. ISBN 978-1-56676-428-5.
Lectura adicional
- Johannes Brändlein; Paul Eschmann; Ludwig Hasbargen; Karl Weigand (1999). Ball and Roller Bearings: Theory, Design and Application (3rd edición). Wiley. ISBN 0-471-98452-3.
Enlaces externos
Wikimedia Commons alberga una categoría multimedia sobre Cojinetes.
Wikimedia Commons alberga una categoría multimedia sobre Rodamientos.
- Tipos de Rodamientos - Comunidad
- Publicación técnica sobre la lubricación de rodamientos
- Manual técnico de la NASA Rolling-Element Bearing (NASA-RP-1105)
- Manual técnico de la NASA Lubricación de elementos de máquinas (NASA-RP-1126)
- Cómo funcionan los rodamientos
- Modelos Cinemáticos para la Biblioteca Digital de Diseño (KMODDL) - Películas y fotos de cientos de modelos de sistemas mecánicos en funcionamiento en la Universidad de Cornell. También incluye una biblioteca de libros electrónicos de textos clásicos sobre diseño mecánico e ingeniería.
- Características de amortiguamiento y rigidez de los rodamientos de elementos rodantes: teoría y experimento (tesis doctoral, Paul Dietl, TU Viena, 1997