Sistema de control industrial
Sistema de control industrial (ICS) es un término general que abarca varios tipos de sistemas de control e instrumentos asociados utilizados para el control de procesos industriales.
Ingeniería química | |
---|---|
![]() | |
Generalidades | |
| |
Fundamentos | |
Aspectos | |
Procesos Unitarios | |
Glosarios | |
| |
Tales sistemas pueden abarcar desde unos pocos controladores modulares montados en panel hasta grandes sistemas de control distribuidos interactivos e interconectados con muchos miles de conexiones de campo. Todos los sistemas reciben datos recibidos de sensores remotos que miden las variables del proceso (PV), los comparan con los puntos de ajuste deseados (SP) y derivan funciones de comando que se utilizan para controlar un proceso a través de los elementos de control finales (FCE), como las válvulas de control.
Los sistemas más grandes generalmente se implementan mediante sistemas de control de supervisión y adquisición de datos ( SCADA ), o sistemas de control distribuido (DCS) y controladores lógicos programables (PLC), aunque los sistemas SCADA y PLC son escalables a sistemas pequeños con pocos circuitos de control.[1] Dichos sistemas se utilizan ampliamente en industrias como el procesamiento químico, la fabricación de pasta y papel, la generación de energía, el procesamiento de gas y petróleo y las telecomunicaciones.
Controladores discretos

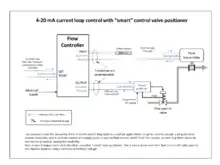
Los sistemas de control más simples se basan en pequeños controladores discretos con un solo bucle de control cada uno. Por lo general, estos paneles se montan en el panel, lo que permite la visualización directa del panel frontal y proporciona medios de intervención manual por parte del operador, ya sea para controlar manualmente el proceso o para cambiar los puntos de control. Originalmente, estos serían controladores neumáticos, algunos de los cuales todavía están en uso, pero casi todos son ahora electrónicos.
Se pueden crear sistemas bastante complejos con las redes de estos controladores que se comunican utilizando protocolos estándar de la industria. Las redes permiten el uso de interfaces de operador SCADA locales o remotas, y permiten la conexión en cascada y el enclavamiento de los controladores. Sin embargo, a medida que aumenta el número de bucles de control para un diseño de sistema, hay un punto en el que el uso de un controlador lógico programable (PLC) o un sistema de control distribuido (DCS) es más manejable o rentable.
Sistemas de control distribuido

Un sistema de control distribuido (DCS) es un sistema de control de procesador digital para un proceso o planta, en el que las funciones del controlador y los módulos de conexión de campo se distribuyen por todo el sistema. A medida que aumenta el número de bucles de control, DCS se vuelve más rentable que los controladores discretos. Además, un DCS proporciona supervisión de visualización y gestión en grandes procesos industriales. En un DCS, una jerarquía de controladores está conectada por redes de comunicación , lo que permite salas de control centralizadas y monitoreo y control local en planta.
Un DCS permite una fácil configuración de los controles de la planta, tales como bucles en cascada y enclavamientos, y fácil conexión con otros sistemas informáticos como el control de producción. También permite un manejo más sofisticado de las alarmas, introduce el registro automático de eventos, elimina la necesidad de registros físicos, como los registradores gráficos, y permite que los equipos de control se conecten en red y, por lo tanto, se ubiquen localmente en los equipos que se controlan para reducir el cableado.
Un DCS generalmente utiliza procesadores diseñados a medida como controladores y utiliza interconexiones propietarias o protocolos estándar para la comunicación. Los módulos de entrada y salida forman los componentes periféricos del sistema.
Los procesadores reciben información de los módulos de entrada, procesan la información y deciden las acciones de control que deben realizar los módulos de salida. Los módulos de entrada reciben información de los instrumentos de detección en el proceso (o campo) y los módulos de salida transmiten instrucciones a los elementos de control finales, como las válvulas de control .
Las entradas y salidas de campo pueden o bien estar cambiando continuamente las señales analógicas , por ejemplo, bucle de corriente o 2 señales de estado que cambian encendido o apagado, tales como contactos de relé o un interruptor semiconductor.
Normalmente, los sistemas de control distribuido también pueden admitir Foundation Fieldbus, PROFIBUS , HART , Modbus y otros buses de comunicación digital que transportan no solo señales de entrada y salida, sino también mensajes avanzados, como diagnósticos de error y señales de estado.
Sistemas SCADA
El control de supervisión y la adquisición de datos (SCADA) es una arquitectura de sistema de control que utiliza computadoras, comunicaciones de datos en red e interfaces gráficas de usuario para la gestión de supervisión de procesos de alto nivel. Las interfaces del operador que permiten el monitoreo y la emisión de comandos de proceso, como los cambios del punto de ajuste del controlador, se manejan a través del sistema de computadora de supervisión SCADA. Sin embargo, la lógica de control en tiempo real o los cálculos del controlador se realizan mediante módulos en red que se conectan a otros dispositivos periféricos, como controladores lógicos programables y controladores PID discretos que se conectan a la planta o maquinaria de proceso.
El concepto SCADA se desarrolló como un medio universal de acceso remoto a una variedad de módulos de control local, que podrían ser de diferentes fabricantes y permitir el acceso a través de protocolos de automatización estándar. En la práctica, los grandes sistemas SCADA se han vuelto muy similares a los sistemas de control distribuido en función, pero utilizando múltiples medios de interfaz con la planta. Pueden controlar procesos a gran escala que pueden incluir múltiples sitios y trabajar a grandes distancias.[2] Esta es una arquitectura de uso común en los sistemas de control industrial, sin embargo, existe la preocupación de que los sistemas SCADA sean vulnerables a la guerra cibernética o los ataques de ciberterrorismo .[3]
El software SCADA funciona en un nivel de supervisión ya que las acciones de control se realizan automáticamente mediante RTU o PLC. Las funciones de control de SCADA suelen estar restringidas a la intervención básica o de supervisión. La RTU o el PLC controlan directamente un circuito de control de retroalimentación, pero el software SCADA controla el rendimiento general del circuito. Por ejemplo, un PLC puede controlar el flujo de agua de refrigeración a través de parte de un proceso industrial hasta un nivel de punto de ajuste, pero el software del sistema SCADA permitirá a los operadores cambiar los puntos de ajuste para el flujo. El SCADA también permite mostrar y registrar condiciones de alarma, como pérdida de flujo o alta temperatura.
Controladores lógicos programables
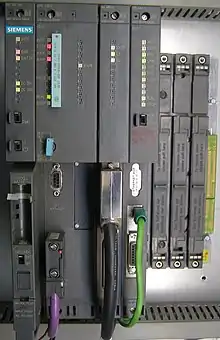
Los PLC pueden abarcar desde pequeños dispositivos modulares con decenas de entradas y salidas (I/O) en una carcasa integral con el procesador, hasta grandes dispositivos modulares montados en bastidor con un recuento de miles de I/O, y que a menudo están conectados en red a otros Sistemas PLC y SCADA. Se pueden diseñar para disposiciones múltiples de entradas y salidas digitales y analógicas, rangos de temperatura ampliados, inmunidad al ruido eléctrico y resistencia a las vibraciones y los impactos. Los programas para controlar el funcionamiento de la máquina generalmente se almacenan en una memoria con respaldo de batería o no volátil.
Historia


El control de procesos de grandes plantas industriales ha evolucionado a través de muchas etapas. Inicialmente, el control era desde paneles locales a la planta de proceso. Sin embargo, esto requería que el personal atendiera estos paneles dispersos, y no había una visión general del proceso. El siguiente desarrollo lógico fue la transmisión de todas las mediciones de la planta a una sala de control central con personal permanente. A menudo, los controladores estaban detrás de los paneles de la sala de control, y todas las salidas de control manual y automático se transmitían individualmente a la planta en forma de señales neumáticas o eléctricas. Efectivamente, esta fue la centralización de todos los paneles localizados, con las ventajas de la reducción de los requisitos de personal y la visión general consolidada del proceso.
Sin embargo, aunque proporcionaba un enfoque de control central, esta disposición era inflexible, ya que cada bucle de control tenía su propio hardware de controlador, por lo que los cambios en el sistema requerían la reconfiguración de las señales mediante una nueva tubería o un nuevo cableado. También requería el movimiento continuo del operador dentro de una gran sala de control para poder monitorear todo el proceso. Con la llegada de procesadores electrónicos, redes de señalización electrónica de alta velocidad y pantallas gráficas electrónicas, fue posible reemplazar estos controladores discretos con algoritmos basados en computadora, alojados en una red de racks de entrada / salida con sus propios procesadores de control. Estos podrían distribuirse alrededor de la planta y se comunicarían con las pantallas gráficas en la sala de control. Se realizó el concepto de control distribuido .
La introducción del control distribuido permitió la interconexión flexible y la reconfiguración de los controles de la planta, como los bucles en cascada y los interbloqueos, y la interconexión con otros sistemas informáticos de producción. Permitió el manejo sofisticado de alarmas, introdujo el registro automático de eventos, eliminó la necesidad de registros físicos, como los registradores gráficos, permitió que los bastidores de control estuvieran conectados en red y, por lo tanto, localizados localmente para que la planta redujera los tendidos de cableado, y proporcionó información general de alto nivel sobre el estado de la planta y Niveles de producción. Para sistemas de control grandes, el sistema de control distribuido de nombre comercial general (DCS) se acuñó para referirse a sistemas modulares patentados de muchos fabricantes que integraban redes de alta velocidad y un conjunto completo de pantallas y racks de control.
Si bien el DCS se adaptó para satisfacer las necesidades de grandes procesos continuos industriales, en industrias donde la lógica combinatoria y secuencial era el requisito principal, el PLC (controlador lógico programable) evolucionó a partir de la necesidad de reemplazar los racks de temporizadores y temporizadores utilizados para eventos. control impulsado Los controles antiguos eran difíciles de reconfigurar y encontrar fallas, y el control PLC permitía la conexión en red de señales a un área de control central con pantallas electrónicas. Los PLC se desarrollaron por primera vez para la industria automotriz en líneas de producción de vehículos, donde la lógica secuencial se estaba volviendo muy compleja. Pronto se adoptó en un gran número de otras aplicaciones impulsadas por eventos tan variadas como prensas de impresión y plantas de tratamiento de agua.
La historia de SCADA se basa en aplicaciones de distribución, como las tuberías de energía, gas natural y agua, donde existe la necesidad de recopilar datos remotos a través de enlaces de baja latencia y ancho de banda potencialmente poco confiables o intermitentes. Los sistemas SCADA utilizan el control de bucle abierto con sitios que están muy separados geográficamente. Un sistema SCADA utiliza RTU (unidades terminales remotas, también conocidas como unidades de telemetría remotas) para enviar datos de supervisión a un centro de control. La mayoría de los sistemas RTU siempre tuvieron una capacidad limitada para manejar los controles locales mientras la estación maestra no está disponible. Sin embargo, a lo largo de los años, los sistemas RTU han crecido cada vez más capaces de manejar controles locales.
Los límites entre los sistemas DCS y SCADA/PLC se difuminan a medida que pasa el tiempo.[4] Los límites técnicos que impulsaron los diseños de estos diversos sistemas ya no son tan problemáticos. Muchas plataformas de PLC ahora pueden funcionar bastante bien como un pequeño DCS, usando E/S remotas y son lo suficientemente confiables para que algunos sistemas SCADA realmente administren el control de bucle cerrado en largas distancias. Con la velocidad cada vez mayor de los procesadores de hoy, muchos productos DCS tienen una línea completa de subsistemas similares a PLC que no se ofrecieron cuando se desarrollaron inicialmente.
En 1993, con el lanzamiento de IEC-1131, que luego se convertiría en IEC-61131 -3, la industria avanzó hacia una mayor estandarización del código, un software de control reutilizable e independiente del hardware. Por primera vez, la programación orientada a objetos (OOP) se hizo posible dentro de los sistemas de control industrial. Esto llevó al desarrollo de ambos (controladores de automatización programables) (PAC) y PC industriales (IPC). Estas son plataformas programadas en los 5 lenguajes IEC estandarizados (lógica de escalera, texto estructurado, bloque de funciones, lista de instrucciones y tabla de funciones secuenciales). También pueden programarse en lenguajes modernos de alto nivel como C o C ++. Además, aceptan modelos desarrollados en herramientas analíticas como MATLAB y Simulink. A diferencia de los PLC tradicionales, que utilizan sistemas operativos propietarios, los IPC utilizan Windows IoT. Los IPC tienen la ventaja de los potentes procesadores de múltiples núcleos con costos de hardware mucho más bajos que los PLC tradicionales y se adaptan bien a múltiples factores de forma, como el montaje en riel DIN, combinado con una pantalla táctil como "panel-pc" o como una PC integrada. Las nuevas plataformas de hardware y la tecnología han contribuido significativamente a la evolución de los sistemas DCS y SCADA, borrando aún más los límites y cambiando las definiciones.
Véase también
- Automatización
- Sistemas de seguridad industrial
- MTConnect
- Fundación OPC
- Sistema de seguridad instrumentado (SIS)
- Sistema de control de seguridad
- Tecnología operacional
Referencias
- NIST SP 800-82
- Boys, Walt (18 de agosto de 2009). «Back to Basics: SCADA». Automation TV: Control Global - Control Design.
- «Cyberthreats, Vulnerabilities and Attacks on SCADA Networks». Rosa Tang, berkeley.edu. Archivado desde el original el 13 de agosto de 2012. Consultado el 1 de agosto de 2012.
- «Introduction to Industrial Control Networks». IEEE Communications Surveys and Tutorials. 2012.
Otras lecturas
- Guía de seguridad de sistemas de control industrial (ICS) , SP800-82 Rev2, Instituto Nacional de Estándares y Tecnología , mayo de 2015.
- Walker, Mark John (8 de septiembre de 2012). The Programmable Logic Controller: its prehistory, emergence and application. Department of Communication and Systems Faculty of Mathematics, Computing and Technology: The Open University. Consultado el 20 de junio de 2018.
- 10 razones para elegir PC Based Control , Manufacturing Automation, febrero de 2015
Enlaces externos
- New Age of Industrial Controllers
- Proview Open source Process Control System
- A simple guide to Embedded PLCs