Native Metals
A native metal is any metal that is found in its metallic form in nature, either pure or as an alloy. Metals that can be found as native deposits singly and/or in alloys include antimony, arsenic, bismuth, cadmium, chromium, cobalt, indium, iron, nickel, selenium, tantalum, tellurium, tin, titanium, and zinc.
Two groups of metals can also be found in nature: the gold group and the platinum group.
- The gold group consists of gold, copper, lead, aluminium, mercury, and silver.
- The platinum group consists of platinum, iridium, osmium, palladium, rhodium, and ruthenium.
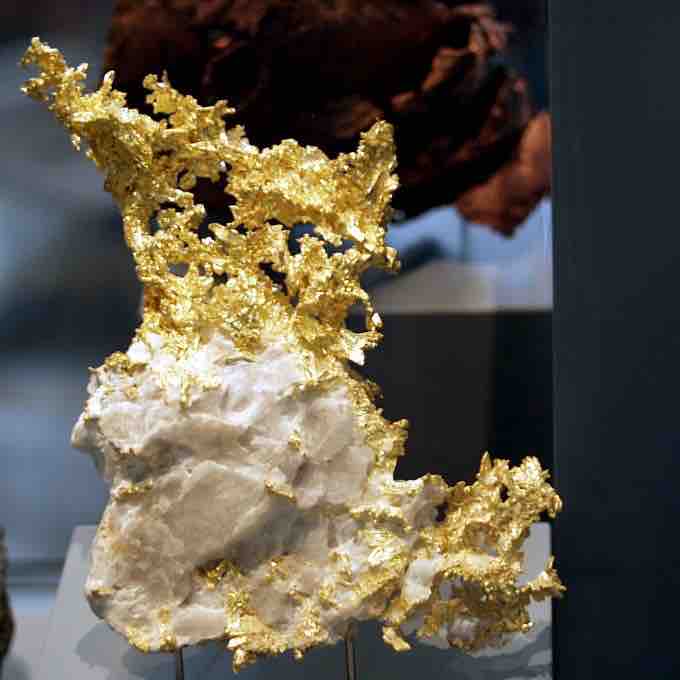
Native metal
Native gold partially embedded in quartz gangue.
Only gold, silver, copper and the platinum metals occur in nature in larger amounts. Over geological time scales, very few metals can resist natural weathering processes like oxidation. This is why only the less reactive metals such as gold and platinum are found as native metals. The others usually occur as isolated pockets where a natural chemical process reduces a common compound or ore of the metal. This leaves the pure metal behind as small flakes or inclusions.
Native metals were prehistoric man's only access to metal. The process of extracting metals from their ores (called smelting) is thought to have been discovered around 6500 BC. However, these metals could be found only in relatively small amounts, so they could not be used extensively. So while copper and iron were known well before the Copper Age and Iron Age, they would not have a large impact on humankind until the technology to smelt them from their ores, and thus mass-produce them, appeared.
Alloys
An alloy is a mixture of two or more elements in solid solution in which the major component is a metal. Most pure metals are either too soft, brittle, or chemically reactive for practical use. Combining different ratios of metals as alloys modifies the properties of pure metals to produce desirable characteristics. The aim of making alloys is generally to make the metals less brittle, harder, or more resistant to corrosion, or to improve their color or luster.
Of all the metallic alloys in use today, the alloys of iron (steel, stainless steel, cast iron, tool steel, and alloy steel) make up the largest proportion both by quantity and commercial value. Iron alloyed with various proportions of carbon gives low, mid and high carbon steels; the increased carbon levels reduce ductility and toughness. The addition of silicon produces cast irons, while the addition of chromium, nickel and molybdenum to carbon steels (more than 10%) results in stainless steels.
Other significant metallic alloys are those of aluminium, titanium, copper, and magnesium. Copper alloys have been known since prehistory—bronze gave the Bronze Age its name—and have many applications today, most importantly in electrical wiring. The alloys of the other three metals were developed more recently; due to their chemical reactivity, they require electrolytic extraction processes. The alloys of aluminium, titanium, and magnesium are valued for their high strength-to-weight ratios, and magnesium can also provide electromagnetic shielding. These materials are ideal for situations where high strength-to-weight ratio is more important than material cost, such as in aerospace and some automotive applications. Alloys specially designed for highly demanding applications, such as jet engines, may contain more than ten elements.
Ores
Metals are often extracted from the Earth by means of mining, resulting in ores that are relatively rich sources of the requisite elements. Ore is located by prospecting techniques, followed by the exploration and examination of deposits. Mineral sources are generally divided into surface mines, which are mined by excavation using heavy equipment, and subsurface mines.

Mining
Chuquicamata, Chile, is the site of the largest circumference and second deepest open pit copper mine in the world.
After the ore is mined, the metals must be extracted, usually by chemical or electrolytic reduction. Pyrometallurgy uses high temperatures to convert ore into raw metals, while hydrometallurgy employs aqueous chemistry for the same purpose. The methods used depend on the metal and their contaminants.
When a metal ore is an ionic compound of that metal and a non-metal, the ore must usually be smelted (or heated with a reducing agent) to extract the pure metal. Many common metals, such as iron, are smelted using carbon as a reducing agent. Some metals, such as aluminium and sodium, have no commercially practical reducing agent, and are extracted using electrolysis instead. Sulfide ores are not reduced directly to the metal, but are roasted in air to convert them to oxides.