NIOSH Update: NIOSH Finds Effective Interventions to Reduce Ergonomic Injuries in Meatpacking and Other Industries
January 1995
DHHS (NIOSH) Publication Number 95-102
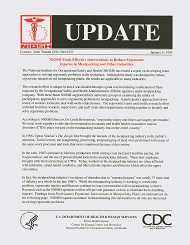
An ergonomic team of front line workers, supervisors, and staff from various departments solved ergonomic problems associated with meatpacking workers. Workers in meatpacking facilities are often afflicted with tendinitis, carpal tunnel syndrome, and other chronic injuries and illnesses that affect upper body extremities. Pressure to increase production, cut costs, and use power tools caused these problems. Disorders due to repeated trauma were nearly 75 times more common in the meatpacking industry than industry as a whole. Ergonomics means that a job is designed with the worker in mind. Successfully implementing a team approach to workplace ergonomic hazards requires strong in house direction, support, and staff expertise in team building and ergonomics. Training programs must develop teamwork and ergonomic skills. Team size should be minimal, but include production workers, supervisors, and maintenance and engineering staff. Evaluation permits teams to appraise their progress, provide feedback, and make corrections to improve the overall effort.
- Page last reviewed: April 12, 2017
- Page last updated: April 12, 2017
- Content source:
- National Institute for Occupational Safety and Health Education and Information Division