Construction Laborer Dies After Falling Through Temporary Bridge "Catch" Platform, 75 Feet To Ground
New Jersey Case Report: 07NJ077
Report Date: June 21, 2011
Summary
A construction laborer fell 75 feet to the ground after falling through a temporary wooden platform during a bridge renovation project. The worker was not equipped with fall protection, and no fall protection system was in place. The wooden platform, also referred to as a "catch" platform, was intended to collect debris generated by work on the bridge deck. However, it was not uncommon for workers to use the platform as a walking or working surface. The victim fell through the temporary wooden platform immediately after he stepped down from a steel structural I-beam onto one of the wooden planks, which broke into two large pieces. The road and bridge construction company was working on a bridge located on a major New Jersey highway when the fatal event occurred. The company employed union laborers for this large-scale, multi-year construction project. NJ FACE investigators recommend following these safety requirements and guidelines to prevent similar incidents:
- Personnel working at heights of six feet or greater should have effective fall protection and prevention.
- Temporary surfaces that are accessed and used by personnel must be designed, maintained, and inspected to assure that they are safe.
- Surfaces that are not designed for worker access use must be clearly identified and entry to those areas must be prevented.
- Wooden planks or other materials used for temporary work platforms and the supports that hold them in place must be designed and made of material that can support at least four times the maximum intended weight.
- Catch designs and/or construction procedures that hold individual planks together to prevent shifting of the planks should be employed.
- Employees must be trained to report any problems with wooden decking planks that might be damaged or planks that have their integrity compromised. Companies must designate a person to actively survey the planks and promptly replace any planks that have compromised integrity.
- A safety and health plan based on a job hazard analysis should be developed by the employer and followed for each communications tower where workers are assigned tasks.
Introduction
This fatal incident occurred at a large highway bridge construction project. The construction project was typical of other highway bridge projects that involved work on a bridge deck. A "catch" platform below the work area was designed to prevent any construction debris generated on site from falling to the ground below. Debris can be generated from a multitude of activities, including the breaking up of concrete or other surface material that is to be replaced or the installation of support structures and concrete for a new or expanded bridge. The "catch" platform is typically a set of wooden planks (e.g. 2' X 10') that are placed from the bottom of one I-beam to the bottom of another I-beam, with the end of the planks set to simply rest on the lip of the I-beam. The planks are typically not secured to the I-beam and it is common to observe gaps and shifting of the planks in a "catch" platform (See Figure 1).
During the initial OSHA investigation, the company contended that the "catch" platform was not a working surface or scaffold. However, on January 5, 2009, OSHA issued a letter that indicated that in OSHA's viewpoint, a "catch" platform in this case is considered a scaffold. As such, bridge "catch" platforms should meet OSHA scaffold standards, even if they are used only temporarily.
![]() |
Figure 1. Example of shifting bridge deck "catch" platform wooden planks (view from ground). |
Back to Top
Investigation
The fatal incident occurred on a typical work day in 2007 shortly after the morning shift began. An OSHA Compliance Safety and Health Officer (COSHO) who had visited the work site several times since the fatal accident reported that it was not uncommon for employees to walk and work on the platform. The victim was not using any fall protection devices at the time of the incident. According to the COSHO, the victim stepped down from the I-beam onto the wooden catch platform to move a "pic" board, a metal runway used to transport concrete between work areas on the bridge. The distance from the top flange of the I-beam to the bridge "catch" surface was 16 inches. Immediately after the victim stepped down, one plank broke across its width, resulting in the employee falling partially through the platform. As the employee fell, other wooden planks making up the platform shifted because the planks were not affixed to one another, and the victim fell completely through the platform (see Figure 2, incident site).
The wooden plank that failed was a nominal 2' X 10' piece of economy-grade, white pine that was 671/2 inches long. The height and width of the failed plank was 17/8 by 93/4 inches, respectively. The plank broke with a curved split at approximately 29 to 291/2 inches from its end, near the location where the victim stepped onto it. This curved split caused the board to break into two large sections and one smaller triangular section. A failure analysis of the broken plank by OSHA revealed that the major strength reducing feature of the plank was the Slope-of-Grain (SOG), which was 1:2 (i.e., the grain along the length of the board deviated from the long axis of the plank by a distance of 1 inch for every 2 inches in length). Acceptable SOG for scaffold-grade lumber is a minimum of 1:12. The OSHA failure analysis demonstrated that the wood used in this platform was inadequate as a walking/working surface. In addition, the COSHO observed planks being reused on the bridge "catch" that had been previously removed from service due to structural concerns, and noted visibly damaged wooden planks as well as planks that had shifted, leaving open spaces in the platform.
The victim was working with one other employee at the time of the accident, and they were separated from the rest of the work crew. Neither the victim nor his co-worker had electronic communication devices. After the fall, the co-worker of the victim had to run over a mile to summon help, which delayed the call for assistance and emergency medical care.
![]() |
Figure 2. Bridge deck where incident occurred |
Back to Top
Recommendations/Discussion
Recommendation #1: Personnel working at heights of six feet or greater should have effective fall protection and prevention.
Discussion: Employers must comply with the provisions of OSHA 29 CFR 1926 subpart M (Fall Protection). In many cases this may include personal protective devices such as safety nets, harnesses, and tied off safety lines, but if this is not feasible other fall protection means must be considered. In addition, fall prevention is also crucial because in certain instances during highway construction projects it can be difficult to utilize standard fall protection devices. Examples of fall prevention may include items such as guardrails, barriers, and warning signs. In addition, as per OSHA 29 CFR 1926.502(k), a fall protection plan should be developed and implemented on site.
Recommendation #2: Surfaces that are accessed and used by personnel must be designed, maintained, and inspected to assure that they are safe.
Discussion:OSHA walking/working surface regulations under 29 CFR 1926 subpart L (scaffolds), must be met. There should be an inspection schedule for working/walking surfaces and a plan in place to immediately fix any deficiencies detected. It is important to note that in many cases employees will walk on surfaces they can access, and therefore these surfaces should be designed, inspected, and maintained accordingly. Employees should receive training to understand the potential fall hazards associated with a given work site and the need to be cognizant of the surface they are walking or working on.
Recommendation #3: Surfaces that are not designed for worker access must be clearly identified and entry to those areas must be prevented.
Discussion:Barriers should be used to prevent intentional or accidental egress onto surfaces not designed as walking or working surfaces. Employees, site managers, and foremen must be trained and reminded about the importance of preventing the use of surfaces that are not designed to support personnel. Walkways should be installed that meet the standards for scaffolds on site for the express purpose of allowing movement of workers around the construction site.
Recommendation #4: Wooden planks or other materials used for temporary work platforms and the supports that hold them in place must be designed and made of material that can support at least four times the maximum intended weight.
Discussion: Wooden planks or other materials used for temporary work platforms must be designed and made of material that can support at least four times the maximum intended weight (i.e. safety factor of at least four) as per OSHA regulations (29 CFR 1926.451(a), Scaffolding). In addition, OSHA has requirements for lumber used in scaffold systems that require the use of scaffold-grade wood, as well as many other important structural requirements that can prevent failure of the temporary work platform when in use (29 CFR 1926 Subpart L, Scaffolding). In addition, there are several wood products grading agencies that have standards for acceptable wood characteristics, such as the Western Wood Products Association's requirement that scaffold grade wood have a minimum SOG of 1:16. In addition, the knot size for scaffold-grade wood is limited to very small sizes. Materials used in temporary work platforms must be inspected to assess the integrity of the material in use. For wooden planks in particular, someone trained to grade wood and other load bearing materials must identify planks that need to be replaced and assure that needed replacements are completed in a timely manner. Materials used in temporary work platforms must be maintained in a manner that preserves the structural integrity of the platform material. For example, wooden planks should not be subjected to conditions that will cause warping or cracking of the wood, which may include long-term exposure to water without the ability to dry quickly, storage underneath objects of significant weight that will eventually warp or damage the wood, or the use of the wood for other purposes such as ground traction support for heavy construction vehicles. In this case, employee interviews and the OSHA inspection suggested that the reused wood planks subjected to maltreatment over several years prior to the accident were placed in the "catch" platform.
Recommendation #5: Catch designs and/or construction procedures that hold individual planks together to prevent shifting of the planks should be employed.
Discussion: Devices and/or designs for catch platforms to hold individual planks together to prevent shifting of the planks should be used. In this incident, although the plank that failed was only 9-3/4" wide several planks shifted allowing the victim to fall through the bridge "catch" platform. If the planks were affixed together, this may have prevented the victim from falling through the bridge "catch" platform. This can be accomplished through several means, including nailing the edges of the wooden planks together. However, it is important to note that OSHA 29 CFR 1926.451(b)(9) prohibits the use of any material that will obscure a visual inspection of the top or bottom surface of the wood planks. Some contractors have suggested covering the entire "catch" platform with plywood, however this would eliminate the ability to visually detect and replace defective or damage wood planks. This could be a particularly problematic if the plywood alone can not support four times the weight potentially placed upon it.
Recommendation #6: Employees must be trained to report any problems with wooden decking planks that might be damaged or planks that have their integrity compromised. Companies must designate a person to actively survey the planks and promptly replace any planks that have compromised integrity.
Discussion: Prompt inspection by trained personnel must follow any employee report and if necessary corrective action taken should be taken, including the replacement of damaged or defective wooden planks. A system should be in place that will assure that defective planks are replaced and not reused. In this case, it was documented by the OSHA inspector that planks removed from service due to recognized deficiencies ended up back in use on the bridge catch platform. The work site appeared to lack a clear protocol for plank inspection and replacement and also appeared to lack a person who clearly had responsibility for the day to day platform maintenance and inspection. This type of construction work requires the presence of a competent person trained in the proper use of wood in working/walking platforms.
Recommendation #7: A safety and health plan based on a job hazard analysis should be developed by the employer and followed for each communications tower where workers are assigned tasks.
Discussion: Employers should conduct a job hazard analysis, with the participation of employees, of all work areas and job tasks. A job hazard analysis should begin by reviewing the work activities for which the employee is responsible, and the equipment that is needed. Each task is further examined for mechanical, electrical, chemical, or any other hazard the worker may encounter. A source of information on conducting a job hazard analysis is included in the Appendix.
Appendix
Recommended Resources
It is essential that employers obtain accurate information on health, safety, and applicable OSHA standards. NJ FACE recommends the following sources of information which can help both employers and employees:
U.S. Department of Labor, Occupational Safety & Health Administration (OSHA)
Federal OSHA will provide information on safety and health standards on request. OSHA has four area offices in New Jersey that cover the following counties:
Hunterdon, Middlesex, Somerset, Union, and Warren counties
Telephone: (732) 750-3270
Essex, Hudson, Morris, and Sussex counties
Telephone: (973) 263-1003
Bergen and Passaic counties
Telephone: (201) 288-1700
Atlantic, Burlington, Cape May, Camden, Cumberland, Gloucester, Mercer, Monmouth, Ocean, and Salem counties
Telephone: (856) 757-5181
Federal OSHA
Web site: https://www.osha.gov/
New Jersey Public Employees Occupational Safety and Health (PEOSH) Program
The PEOSH Act covers all NJ state, county, and municipal employees. Two state departments administer the act; the NJ Department of Labor and Workforce Development (NJDLWD), which investigates safety hazards, and the NJ Department of Health and Senior Services (NJDHSS), which investigates health hazards. PEOSH has information available that may also benefit private employers.
NJDLWD, Office of Public Employees Safety
Telephone: (609) 633-3896
Web site: http://lwd.dol.state.nj.us/lsse/employer/Public_Employees_OSH.html
NJDHSS, Public Employees Occupational Safety & Health Program
Telephone: (609) 984-1863
Web site: http://www.nj.gov/health/peosh
On-site Consultation for Public Employers
Telephone: (609) 984-1863(health) or (609) 633-2587(safety)
Web site: www.state.nj.us/health/eoh/peoshweb/peoshcon.htm
New Jersey Department of Labor and Workforce Development, Occupational Safety and Health On-Site Consultation Program
This program provides free advice to private businesses on improving safety and health in the workplace and complying with OSHA standards.
Telephone: (609) 984-0785
Web site:
http://lwd.dol.state.nj.us/labor/lsse/employer/
Occupational_Safety_and_Health_Onsite_Consultation_Program.html
New Jersey State Safety Council
The NJ State Safety Council provides a variety of courses on work-related safety. There is a charge for the seminars.
Telephone: (908) 272-7712.
Web site: http://www.njsafety.org
Internet Resources
Other useful internet sites for occupational safety and health information:
- CDC/NIOSH - https://www.cdc.gov/niosh/
- Employment Laws Assistance for Workers and Small Businesses - http://www.dol.gov/elaws/
- National Safety Council - http://www.nsc.org/Pages/Home.aspx (Link updated 8/14/2012)
- NJDHSS FACE reports - http://www.nj.gov/health/surv/face/index.shtml
- CDC/NIOSH FACE - https://www.cdc.gov/niosh/face/
- OSHA - http://www.osha.gov (Link updated 11/12/2013)
- ANSI - http://www.ansi.org
Reference
- Job Hazard Analysis. US Department of Labor Publication # OSHA-3071, 1998 (revised). USDOL, OSHA/OICA Publications, PO Box 37535, Washington DC 20013-7535.
New Jersey FACE Program
Fatality Assessment and Control Evaluation (FACE) ProjectInvestigation #07-NJ-077
Staff members of the New Jersey Department of Health and Senior Services, Occupational Health Service, perform FACE investigations when there is a report of a targeted work-related fatal injury. The goal of FACE is to prevent fatal work-related injuries by studying the work environment, the worker, the task, the tools the worker was using, the energy exchange resulting in the fatal injury, and the role of management in controlling how these factors interact. FACE gathers information from multiple sources that may include interviews of employers, workers, and other investigators; examination of the fatality site and related equipment; and reviewing OSHA, police, and medical examiner reports, employer safety procedures, and training plans. The FACE program does not determine fault or place blame on employers or individual workers. Findings are summarized in narrative investigation reports that include recommendations for preventing similar events. All names and other identifiers are removed from FACE reports and other data to protect the confidentiality of those who participate in the program.
NIOSH-funded state-based FACE Programs include: California, Iowa, Kentucky, Massachusetts, Michigan, New Jersey, New York, Oregon, and Washington. Please visit the NJ FACE website at www.state.nj.us/health/eoh/survweb/face.htm or the CDC/NIOSH FACE website at www.cdc.gov/niosh/face for more information.
The NJ FACE Project is supported by Cooperative Agreement #1 U60 OH0345-01 from the Centers for Disease Control and Prevention (CDC). The contents of this report are solely the responsibility of the authors and do not necessarily represent the official views of the CDC.
To contact New Jersey State FACE program personnel regarding State-based FACE reports, please use information listed on the Contact Sheet on the NIOSH FACE web site. Please contact In-house FACE program personnel regarding In-house FACE reports and to gain assistance when State-FACE program personnel cannot be reached.
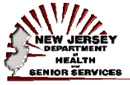
- Page last reviewed: November 18, 2015
- Page last updated: October 15, 2014
- Content source:
- National Institute for Occupational Safety and Health Division of Safety Research