A 60-Year-Old Hispanic Maintenance Worker Killed when a Pressure Vessel Exploded; Eight Others Injured
New Jersey Case Report: 08NJ003
Report Date: June 26, 2009
Summary
On January 15, 2008, a 60-year-old male Hispanic maintenance worker was killed when a large pressure vessel exploded. The victim worked for a foundry in northern New Jersey. On the day of the incident, the victim and two other workers were in the process of testing the vessel for leaks, following repairs to the front access hatch of the unit, when the hatch blew off and landed approximately 38 feet away. The victim was standing in front of the hatch checking for leaks as another employee (standing to the side of the vessel) increased the pressure. The fatal injury occurred when the vessel was overpressurized and the front hatch exploded outward, striking the victim. NJ FACE investigators recommend following these safety guidelines to prevent similar incidents:
- Employers should ensure that pressure vessels are not pressurized above allowable limits, all pressure relief valves are properly functioning, and that any repairs to this type or similar pressure units be conducted by a certified worker.
- Employers should ensure that workers are properly trained on the safe operation of pressure vessels and are knowledgeable about the associated hazards.
- A safety and health plan based on a job hazard analysis should be developed and followed at the worksite.
Introduction
On January 15, 2008, a Federal OSHA compliance officer notified NJ FACE staff of the death of a 60-year-old Hispanic maintenance worker who was killed after a pressure vessel exploded. A FACE investigator arranged to conduct a concurrent investigation with OSHA, which took place on January 16, 2008. During the visit to the incident site, FACE investigators were permitted to participate in the OSHA witness interviews and to examine the scene in detail. Additional information was obtained from the medical examiner and OSHA reports.
The victim's employer was an aluminum investment casting company for which he had worked for 20 years. The company employed 25 workers; nine of whom were working in the immediate vicinity of the vessel, and two who were working on the particular vessel where the incident occurred. Employee training was conducted on site by the employer.
Back to Top
Investigation
The incident occurred at a small-scale foundry in an urban area of New Jersey. The vessel that the victim was working with at the time of his death was one of three similar units with a hinged access hatch in the front with metal lugs (teeth) and a large O-ring (see Figure 1). The two similar, newer units were adjacent to the vessel that exploded, and were in operation at the time of the incident.
The vessels were used to pressurize/depressurize metal to specific levels in order to achieve proper conditions for the process of casting molten aluminum. The process of pressurizing and depressurizing eliminates porosity from the molten metal.
On the day of the incident, the vessel that exploded (vessel #3) was offline. The company had been having trouble with leaks from the O-ring gasket that creates the seal around the circumference of the hatch. The metal teeth on the hatch that engage with lugs on the vessel also had a history of cracks and breaks, and many had to be welded or replaced. In addition, the pressure relief valve on this unit was clogged and not working properly. In an effort to put the vessel back online, a new O-ring gasket was installed and tested. Two workers were involved in this process; one to work the pressure controls (on the side of the vessel, see Figure 2), and a second worker (the decedent) to stand in front of the unit to listen for leaks. The first worker began increasing the pressure until approximately 80 pounds per square inch (psi) when the decedent heard a "hiss," indicating a leak. Their initial reaction was to shut down the machine, but a process was attempted that had been successful in the past, which was to increase the pressure further, and force the gasket into place. Worker #1 then increased the pressure to approximately 112 psi, and the vessel exploded. The decedent, who was standing in front of the vessel, was struck by the hatch, thrown approximately 38 feet, and killed instantly. The hatch was propelled 35 feet. Worker #1 sustained injuries, and eight other workers in the immediate vicinity sustained injuries from shrapnel and/or the force of the explosion. Although the maximum allowable pressure of the unit was rated at 100 psi, the American Society of Mechanical Engineers (ASME), Section VII UG-125, permits this to be exceeded by three percent. At the time of the explosion, the maximum rated pressure was exceeded by eight percent.
![]() |
![]() |
![]() |
Figure 3. Broken Hatch |
Back to Top
Recommendations/Discussion
Recommendation #1: Employers should ensure that pressure vessels are not pressurized above allowable limits, all pressure relief valves are properly functioning, and that any repairs to this type or similar pressure vessels be conducted by a certified worker.
Discussion: Several factors likely contributed to the explosion of the pressure vessel. First, the vessel ruptured due to overpressurization. In an attempt to correct a leak, the workers pressurized the vessel to 112 psi, which is greater than 3% of the maximum allowable working pressure of the unit (100 psi). Second, it was discovered that the pressure relief valves were clogged with aluminum production material and were inoperative. According to the American petroleum Institute (API) 510, 8th Edition, Addendum #4, August 2003, Sections 6 and 7, all pressure vessels and pressure-relieving devices shall be inspected at specific intervals to ensure vessel integrity. Third, repairs and welds were performed on the vessel by a worker who was not certified by the American Society of Mechanical Engineers (ASME), or the National Board.
Recommendation #2: Employers should ensure that workers are properly trained on the safe operation of pressure vessels and are knowledgeable about the associated hazards.
Discussion:
All vessel operators should be properly trained in the safe use of the equipment. Employers should provide classroom and hands-on training to the operators, and training must be specific to the worksite and equipment used. Training on safe operation and the associated hazards must be taught by a competent person, and workers should be certified as having passed the training.
Recommendation #3: A safety and health plan based on a job hazard analysis should be developed and followed.
Discussion: Employers should conduct a job hazard analysis, with the participation of employees, in all work areas and job tasks. A job hazard analysis should begin by reviewing the work activities for which the employee is responsible, and the equipment that isused. Each task is further examined for mechanical, electrical, chemical, or any other hazard the worker may encounter. Additional information on conducting a job hazard analysis is included in the Appendix.
Appendix
Recommended Resources
It is essential that employers obtain accurate information on health, safety, and applicable OSHA standards. NJ FACE recommends the following sources of information which can help both employers and employees:
U.S. Department of Labor, Occupational Safety & Health Administration (OSHA)
Federal OSHA will provide information on safety and health standards on request. OSHA has four area offices in New Jersey that cover the following counties:
Hunterdon, Middlesex, Somerset, Union, and Warren counties
Telephone: (732) 750-3270
Essex, Hudson, Morris, and Sussex counties
Telephone: (973) 263-1003
Bergen and Passaic counties
Telephone: (201) 288-1700
Atlantic, Burlington, Cape May, Camden, Cumberland, Gloucester, Mercer, Monmouth, Ocean, and Salem counties
Telephone: (856) 757-5181
Federal OSHA
Web site: https://www.osha.gov/
New Jersey Public Employees Occupational Safety and Health (PEOSH) Program
The PEOSH Act covers all NJ state, county, and municipal employees. Two state departments administer the act; the NJ Department of Labor and Workforce Development (NJDLWD), which investigates safety hazards, and the NJ Department of Health and Senior Services (NJDHSS), which investigates health hazards. PEOSH has information available that may also benefit private employers.
NJDLWD, Office of Public Employees Safety
Telephone: (609) 633-3896
Web site: http://lwd.dol.state.nj.us/lsse/employer/Public_Employees_OSH.html
NJDHSS, Public Employees Occupational Safety & Health Program
Telephone: (609) 984-1863
Web site: http://www.nj.gov/health/peosh
On-site Consultation for Public Employers
Telephone: (609) 984-1863(health) or (609) 633-2587(safety)
Web site: www.state.nj.us/health/eoh/peoshweb/peoshcon.htm
New Jersey Department of Labor and Workforce Development, Occupational Safety and Health On-Site Consultation Program
This program provides free advice to private businesses on improving safety and health in the workplace and complying with OSHA standards.
Telephone: (609) 984-0785
Web site:
http://lwd.dol.state.nj.us/labor/lsse/employer/
Occupational_Safety_and_Health_Onsite_Consultation_Program.html
New Jersey State Safety Council
The NJ State Safety Council provides a variety of courses on work-related safety. There is a charge for the seminars.
Telephone: (908) 272-7712.
Web site: http://www.njsafety.org
Internet Resources
Other useful internet sites for occupational safety and health information:
- CDC/NIOSH - https://www.cdc.gov/niosh/
- Employment Laws Assistance for Workers and Small Businesses - http://www.dol.gov/elaws/
- National Safety Council - http://www.nsc.org/Pages/Home.aspx (Link updated 8/14/2012)
- NJDHSS FACE reports - http://www.nj.gov/health/surv/face/index.shtml
- CDC/NIOSH FACE - https://www.cdc.gov/niosh/face/
Reference
Job Hazard Analysis. US Department of Labor Publication # OSHA-3071, 1998 (revised). USDOL, OSHA/OICA Publications, PO Box 37535, Washington DC 20013-7535.
New Jersey FACE Program
Fatality Assessment and Control Evaluation (FACE) ProjectInvestigation #08-NJ-003
Staff members of the New Jersey Department of Health and Senior Services, Occupational Health Service, perform FACE investigations when there is a report of a targeted work-related fatal injury. The goal of FACE is to prevent fatal work-related injuries by studying the work environment, the worker, the task, the tools the worker was using, the energy exchange resulting in the fatal injury, and the role of management in controlling how these factors interact. FACE gathers information from multiple sources that may include interviews of employers, workers, and other investigators; examination of the fatality site and related equipment; and reviewing OSHA, police, and medical examiner reports, employer safety procedures, and training plans. The FACE program does not determine fault or place blame on employers or individual workers. Findings are summarized in narrative investigation reports that include recommendations for preventing similar events. All names and other identifiers are removed from FACE reports and other data to protect the confidentiality of those who participate in the program.
NIOSH-funded state-based FACE Programs include: California, Iowa, Kentucky, Massachusetts, Michigan, New Jersey, New York, Oregon, and Washington. Please visit the NJ FACE website at www.state.nj.us/health/eoh/survweb/face.htm or the CDC/NIOSH FACE website at www.cdc.gov/niosh/face for more information.
The NJ FACE Project is supported by Cooperative Agreement #1 U60 OH0345-01 from the Centers for Disease Control and Prevention (CDC). The contents of this report are solely the responsibility of the authors and do not necessarily represent the official views of the CDC.
To contact New Jersey State FACE program personnel regarding State-based FACE reports, please use information listed on the Contact Sheet on the NIOSH FACE web site. Please contact In-house FACE program personnel regarding In-house FACE reports and to gain assistance when State-FACE program personnel cannot be reached.
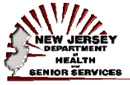
- Page last reviewed: November 18, 2015
- Page last updated: October 15, 2014
- Content source:
- National Institute for Occupational Safety and Health Division of Safety Research