Seating Design Principles
Introduction
Seating for most industrial applications generally includes an adjustable backrest, a suspension system, a fore-and-aft track adjustment, an up-and-down seat adjustment, and sometimes an armrest and/or footrest. Some manufacturers also include devices for lumbar region support.
Unfortunately, many factors combine to make it difficult to design a suitable seat for underground mobile applications. These include height limitations due to seam thickness, fore-aft and lateral space limitations due to the small size of the operators compartments, and the natural wear and tear in the harsh underground mining environment. To compound the problem, suspension systems used extensively in surface mining equipment and other off-road applications cannot be used with underground mobile underground mining equipment, except in the higher-seam mines due to the strict restriction on height.
Also, for mobile underground mining equipment, the whole-body vibration levels are often higher than advocated in International Standard Organization ISO 2631. This is especially true for shuttle cars and to a lesser extent, for scoops. In addition, injuries sometimes occur when a rigid seat frame transmits a shock or jolt through to the seated operators, causing them to hit their head on the bottom of the canopy or strike their arms or shoulders on the machine frame. The fact that the operator is sometimes forced to make do with such improvised seating as crib blocks or rock dust bags only worsens the situation.
Due to the problems listed above, satisfying the guiding first principles for seating design for underground mobile mining equipment for a given seat-workstation design will be difficult. Nevertheless, the designer should attempt to do so, given that the operator's comfort and productivity depends in large part on his/her seating.
Seat Dimensions - Design the seat to fit and adjust to body dimensions, and distribute weight to relieve pressure points and support posture. In other words, the seat should be comfortable.
Vibration Isolation - Provide design features to guard against the dynamic forces caused by rough roadways and minor collisions that tend to "unseat" a person.
Workstation Integration - Design the seat so that it does not hinder the operator's ability to control the machine or hinder ingress or egress from the workstation.
Maintainability - Design the seat so that maintenance personnel can easily maintain or replace it. Use modular components when possible.
A seat designed according to the principles listed above would:
- Provide adequate support, would not impose any undue stress on the body, and would allow optimum posture.
- It would be comfortable, not contribute to fatigue, and allow the worker to be productive.
- It would address such factors as the alignment of the spine to reduce intradiscal pressure, how much work the muscles have to do to maintain required work postures, and the compression of the blood vessels and nerves at the back of the thigh and behind the knee.
- Due to the differences in size and shape of workers, adjustability would be incorporated into the seat, i.e., operators could move it up and down and forwards and backwards.
- Padding would prevent discomfort and decrease the effects of whole-body vibration and shock. Its design would reduce interference to trunk, head, and limb movement and visibility.
- An adjustable backrest and armrests would give additional postural support and be an aid to standing up and sitting down.
Seating Design Guidelines
The following sections expand on the first principles of seating design for mobile underground mining machinery.
Seat Dimensions
A good fitting seat depends on many anthropometric and biomechanical factors, which we discuss generally in the following paragraphs. Be aware that the different shapes and sizes of workers suggest that a seat be adjustable by moving it in the up-down and fore-aft directions. You should design this ability into any seat for mobile equipment applications.
Seat Height
As the height of the seat increases beyond the popliteal height of the user, pressure will be felt on the underside of the thighs. The resulting reduction of circulation to the lower extremities may lead to a "pins and needles" feeling, swollen feet, and considerable discomfort. As the height decreases, the user will flex the spine more (due to the need to achieve an acute angle between the thigh and trunk), experience greater problems in standing up and sitting down, due to the distance through which his or her center of gravity must move, and require greater leg room. Usually, the optimal seat height for many purposes is close to the popliteal height. If this is not possible, a seat that is too low is preferable to one that is too high. For many purposes, the 5th-percentile female popliteal height represents the best compromise. If making a seat higher than this is necessary (e.g., to increase the eye height for better visibility), the ill effects may be mitigated by shortening the seat and rounding off its front edge to reduce the under-thigh pressure.
Seat Pan Depth
If the design increases the seat pan depth beyond the buttock-popliteal length, the user cannot engage the backrest effectively without putting pressure on the backs of the knees. Furthermore, the deeper the seat pan, the greater the problems of standing up and sitting down.
Backrest
The higher the backrest, the more effective it will be in supporting the weight of the trunk. This is always desirable, but in some circumstances other requirements, such as the mobility of the shoulders needed to look to the rear, may be more important.
Seat Width
Most people require a width between 18 in (45.7 cm) and 20 in (50.8 cm) for support. This distance should provide adequate clearance between the armrests for the largest user.
Seat Pan to Seat Back Angle
This angle should be between 100 and 165 degrees as the seat back approaches the vertical position and will approach 180 degrees in cabs designed for low-seam mines. As the backrest angle increases, a person supports more of the weight of the trunk; therefore, they diminish the compressive force between the trunk and pelvis. However, the horizontal component of the compressive force increases. This will drive the buttocks forward out of the seat unless counteracted by an adequate seat tilt, high-friction upholstery, or muscular effort from the subject. An increased seat back angle also leads to increased difficulty in getting in to and out of the seat.
Seat Back to Headrest Angle
In partially or fully reclined seats, a headrest is needed to allow operators to effectively view their primary visual areas over extended periods.
Seat Pan Angle
The angle of the seat pan relative to the cab floor is important for comfort and body support during rapid decelerations or collisions. Excessive tilt reduces the hip-trunk angle and makes getting in to and out of the seat more difficult.
Armrests
Armrests may give additional postural support and be an aid to standing up and sitting down. Armrests should support the fleshly part of the forearm, but unless very well padded they should not engage the bony parts of the elbow where the highly sensitive ulnar nerve is near the surface. Arm rests should tilt up and out of the way when not in use and be adjustable in both height and angle.
Seat Surface
The seat surface should be mostly flat rather than shaped, although a rounded front edge is desirable to reduce under-thigh pressure. You can raise the sides of the seat pan slightly to aid in postural stability during lateral accelerations. The covering materials should be waterproof and rough to aid stability.
Personal Protective Equipment
The design should make accommodations for the operator's personal protective equipment. The seat pan and backrest should make allowances for the cap lamp battery, self-rescue device, and tool belts. Also, the headrest and backrest should accommodate the operator's hard hat.
Seat design specifications are recommended for three compartment heights (see below): over 36 in (91.4 cm), 24 in to 36 in (61.0 cm to 91.4 cm), and under 24 in (61.0 cm). You may adapt these design values to individual cab configurations, as necessary. For those applications where including adjustable headrest-back-seat pan configuration is not practical, a curved transition from the headrest to back support with a radius of 24 in to 32 in (61.0 cm to 81.3 cm) may be used. You should take care, however, to ensure that you never lock the operator's head into a position of more than 45 degrees relative to the back.
Compartment Height Over 36 in (91.4 cm)
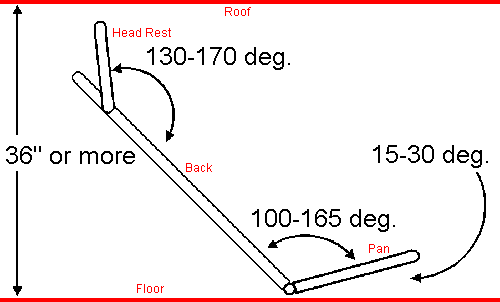
Seam Height in (cm) | Pan Angle from Floor degrees | Back to Pan Angle degrees | Head Rest to Back Angle degrees |
---|---|---|---|
36 or more (91.4 or more) |
15-30 | 100-165 | 130-170 |
Head Rest Travel along Back in (cm) | Seat and Head Rest Width in (cm) | Pan Length in (cm) | Height of Back in (cm) |
---|
Compartment Height from 24 in to 36 in (61.0 cm to 91.4 cm)
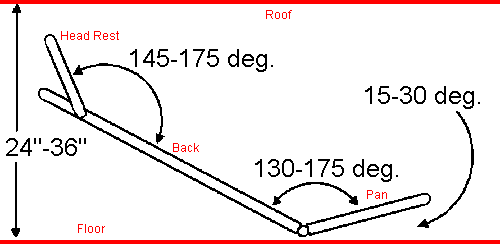
Seam Height in (cm) | Pan Angle from Floor degrees | Back to Pan Angle degrees | Head Rest to Back Angle degrees |
---|---|---|---|
24-36 (61.0-91.4) | 15-30 | 130-175 | 145-175 |
Head Rest Travel along Back in (cm) | Seat and Head Rest Width in (cm) | Pan Length in (cm) | Height of Back in (cm) |
---|---|---|---|
7 (17.8) | 18-20 (45.7-50.8) | 12-14 (30.5-35.6) Adjustable |
16-24 (40.6-61.0) |
Compartment Height Less Than 24 in (61.0 cm)
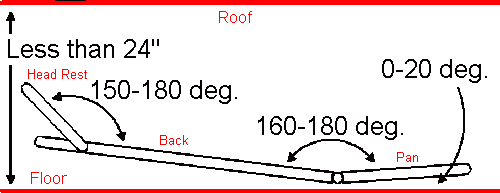
Seam Height in (cm) | Pan Angle from Floor degrees | Back to Pan Angle degrees | Head Rest to Back Angle degrees |
---|---|---|---|
Less than 24 (Less than 61.0) |
0-20 | 160-180 | 150-180 |
Head Rest Travel along Back in (cm) | Seat & Head Rest Width in (cm) | Pan Length in (cm) | Height of Back in (cm) |
---|---|---|---|
7-12 (17.8-30.5) | 20-22 (50.8-55.9) | 12-14 (30.5-35.6) | 16-24 (40.6-61.0) Adjustable |
Vibration Isolation
You should design vibration isolation into the seat-workstation installation whenever possible to reduce operator exposure to bumps, jolts, and other mechanical shocks. When space permits, this isolation is generally achieved by a spring and shock absorber or damper. Although cushions are used primarily for static comfort, they are also effective in decreasing the transmission of vibration above the resonance range of the human body. They are ineffective in the resonance range and may even amplify the vibration in the subresonance range. The seat should also offer lateral support (as in a concave seat back) against jerks, heavy swaying, or shocks while tramming. The shock-absorbing qualities of the seat should be suitable for fitting operators ranging in weight from the 5th-percentile female to the 95th-percentile male. A passive (molded seat pan) or active (seat belt) occupant restraint system should also be incorporated into the seat-workstation to prevent the operator from being thrown out of the seat during a turn, hard bump, or collision.
Workstation Integration
All seat adjustment levers, knobs, or buttons should be within hand's reach by 5th-percentile female and 95th-percentile male operators, should not block ingress or egress, and should not pose impact hazards in the event that unexpected machine motions throw the operator from the seat. All adjustment operations should be quick and should not require great force or the use of tools. The seat adjustment controls and moving parts should be able to be operated without risk of trapping fingers and should be designed so that they cannot be inadvertently removed. The adjustments should lock in all positions and should be spring loaded, where necessary, to help the operator in moving forward to a more upright position. All operating instructions should be clear and permanently displayed near the seat.
The seat should not interfere with trunk, head, or limb movements needed to operate the machine. The seat should not restrict the operator's ability to see primary Visual Attention Locations.
Maintainability
The seat pan and backrest covers should be easily changed or repaired and should be washable so that they can be maintained in good condition. The edges of the seat assembly should be smoothed or rounded so as not to catch clothing or equipment.
The seat adjustment mechanisms should be self-cleaning and able to withstand excessive water, dirt, and debris. The seat assembly components should be corrosion-resistant. The seat assembly construction should be robust, and the seat should feel solid and safe to the user. The seat should be easily removed from the workstation to effect repairs or to be replaced.
Improved Seating Example
In an attempt to improve low seam seating in shuttle cars, researchers at the NIOSH Pittsburgh Research Center modified the original seat in a JOY 21SC shuttle car used at an eastern Kentucky mine. The coal seam at this mine is 35 in (88.9 cm) thick with an operating height of approximately 43 in (109.22 cm). Owing to the low mining height, operators must adopt a reclining posture to operate the shuttle car.
From observing and talking with the shuttle car operators, it became obvious that the original seat provided little adjustability or lower back support. Modifications to the original seat resulted in a more ergonomically designed version with an easily adjustable lumbar support, fore-aft seat pan movement, and viscoelastic foam padding.
The padding included six layers of foam, each .5 in (1.27 cm) in thickness. Three of the layers were CONFOR medium-density, open-celled polyurethane foams from E-A-R Specialty Composites Corporation, Newark, DE. The remaining three foam materials were an organic composition of more than 50% plant derivatives manufactured by Dynamic Systems, Inc., Leicester, NC.
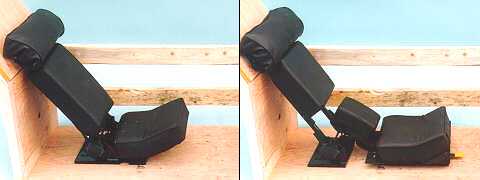
The picture on the left is the original JOY 21 SC shuttle car seat. The picture on the right is the modified seat with an adjustable lumbar support, fore-aft seat pan movement, and viscoelastic foam padding.
See Also
- A Checklist for Evaluating Cab Design of Construction Equipment
- Control Design Principles
- Engineered Solutions - Dump Truck Vibrations and Impact on Operator Safety in High-Impact Shovel Loading Operations
- Ergonomic and Existing Seat Designs Compared on Underground Mine Haulage Vehicles
- Experiments on Personal Equipment for Low Seam Coal Miners: IV. Incorporating Coiled Cord Into Cap Lamp Battery Cords
- Impact of Maintainability Design on Injury Rates and Maintenance Costs for Underground Mining Equipment
- Implementation of an Ergonomics Process at a US Surface Coal Mine
- Job Design: An Effective Strategy for Reducing Back Injuries
- Laboratory Investigation of Seat Suspension Design Performance during Vibration Testing
- Task Analysis
- Underground Workstation Design Principles
- Working in Unusual or Restricted Postures
- Page last reviewed: 4/10/2014
- Page last updated: 5/3/2013
- Content source: National Institute for Occupational Safety and Health, Mining Program