Mining Topic: Methane Detection and Monitoring
Methane Detection and Monitoring
What is the health and safety problem?
The use of machine-mounted methane monitors is required by federal regulations to alert miners to the presence of potentially dangerous concentrations of methane while mining coal. The monitors must be permanently mounted on a mining machine to provide continuous readings of methane levels near a working face. An unknown with the use of methane monitors is their response time, defined as the time interval between the application of a gas to the sensor head and the final steady-state reading of the instrument. Response time is critical because while the mining machine is cutting coal, methane levels can rise and fall rapidly and miners have to be able to respond rapidly to these changing conditions.
What is the extent of the problem?
Machine-mounted methane monitors must provide a warning whenever methane levels are 1% or higher. An effective monitoring system will indicate a methane concentration of 1% before methane levels at the face reach 5%. Proper placement of the methane monitor on the mining machine is one of the most important factors determining how effectively face methane levels can be predicted.
How is the NIOSH Mining program addressing this problem?
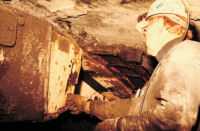
Methane detection and monitoring
The NIOSH Mining Program is currently investigating methods to reduce methane emissions at the face during deep cut mining. NIOSH Mining is also conducting full-scale testing coupled with sophisticated numerical modeling to determine the size and concentration gradient of a methane cloud at the cutting face. Understanding the distribution of methane gas at the face is critical in deciding where to place methane monitors in order to most effectively monitor these levels.
What are the significant findings?
NIOSH Mining research has determined that the design of the protective dust cap over the sensor has the greatest effect on monitor response time. All sensors have dust caps to protect the sensor head from the harsh influences of the mining environment. Although instruments with faster response times provide more accurate measurements of methane concentrations, the sensor heads must be continuously protected from exposure to excessive amounts of dust and water.
Through testing, the mining program has also identified possible locations for a methane monitor on a continuous mining machine and found that those on the return side of the machine offered the most accurate assessment of face methane levels. However, locations closest to the face would likely suffer from damage during mining activities, while those furthest from the face would not provide sufficient accuracy.
What are the next steps?
Future research is exploring the benefits of placing a secondary methane monitor on a mining machine to provide earlier warning of hazardous methane accumulations. Further refinements to the design of the protective dust cap may also be considered. Effective performance of these options can only be determined by long-term underground tests.
See Also
- Adapting Remote Methane Leak Detector (RMLD) to Coal Miner Rescue
- Coal Dust and Methane
- Development of a Gas Monitor Simulator and Mine Rescue Contest Field Trials
- Evaluating Performance Characteristics of Machine-Mounted Methane Monitors by Measuring Response Time
- Evaluation of Person-Wearable Methane Monitors
- Factors Affecting the Location of Methanometers on Mining Equipment
- Guidelines for the Control and Monitoring of Methane Gas on Continuous Mining Operations
- Guidelines for the Prediction and Control of Methane Emissions on Longwalls
- Ignition of Methane-Air Mixtures by Laser Heated Small Particles
- Methane Emission Rate Studies in a Northern West Virginia Mine
- Predicting Methane Emissions from Longer Longwall Faces by Analysis of Emission Contributors
- Remote Fiber-Optic Methane Monitor
- Remote Methane Sensors
- Review of Horizontal Drilling Technology for Methane Drainage From U. S. Coalbeds
- Use of a Test Box to Measure Response Times for Machine-Mounted Monitors
- Page last reviewed: 9/16/2012
- Page last updated: 9/22/2015
- Content source: National Institute for Occupational Safety and Health, Mining Program