Sambalpuri sari
A Sambalpuri sari is a traditional handwoven bandha (ikat) sari (locally called "sambalpuri bandha" sadhi or saree) wherein the warp and the weft are tie-dyed before weaving. It is produced in the Sambalpur, Balangir, Bargarh, Boudh and Sonepur districts of Odisha, India. The sari is a traditional female garment in the Indian subcontinent consisting of a strip of unstitched cloth ranging from four to nine metres in length that is draped over the body in various styles.[1]
![sambalpuri saree design]](../I/Sambalpuri_saree1.jpg.webp)
![mayur design sambalpuri saree pallu]](../I/Sambalpuri_saree_pallu.jpg.webp)
Sambalpuri saris are known for their incorporation of traditional motifs like shankha (Conch), chakra (wheel), phula (flower), all of which have deep symbolism with the native Odia culture. The colours red, black and white represents Lord Kaalia (Jagannatha)'s face colour. The salient feature of these saris is the traditional craftsmanship of the 'Bandhakala'- the Tie-dye art reflected in their intricate weaves, also known as Sambalpuri "Ikkat". In this technique, the threads are first tie-dyed and later woven into a fabric, with the entire process taking many weeks. These saris first became popular outside the state when the late Prime Minister Indira Gandhi started wearing them. In the 1980s and 1990s they became popular across India.[2] To provide protection to the weavers practicing this art, the handloom silk saris manufactured in Sambalpur and Berhampur (Berhampur Patta) in Odisha were included in the Government of India's Geographical Indications (GI) registry.[3][4]
The Sambalpuri sari


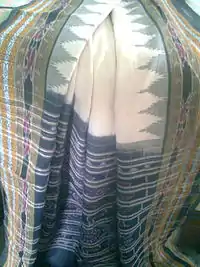
.jpg.webp)
The Sambalpuri sari is made from fabric woven on a hand-loom. Varieties of the Sambalpuri sari include Sonepuri, Pasapali, Bomkai, Barpali, and Bapta saris, which are in high demand. Most of them have been named after their places of origin and are popularly known as Pata. Paintings on Tussar saris depicting Mathura Vijay, Raslila and Ayodhya Vijay owe their origin to ‘Raghurajpur patta paintings’.
Fabric and design
.jpg.webp)
Baandha fabric is created using a tie-dye technique. The yarns are tied according to the desired patterns to prevent absorption of dyes, and then dyed.[5] The yarns or set of yarns so produced is called 'Baandha'. The unique feature of this form of designing is that the designs are reflected almost identically on both sides of the fabric. Once the fabric is dyed it can never be bleached into another colour.[6]
This versatile technique enables a craftsman to weave colourful designs, patterns and images into a fabric capable of inspiring a thought or conveying a message. Traditionally, craftsmen created Baandhas with images of flora or fauna or with geometrical patterns. More recently, new types of Baandha depicting portrait, landscape and flower pods are being designed.
It is believed that this art migrated to Western Odisha along with the Bhulia community who fled Northern India in the year 1192 AD after the fall of the Chouhan empire at the hands of the Mughals. Since then and up to the year 1925 it flourished in Western Odisha in a limited number of designs and in vegetable colours and consisted mostly of saris used by the womenfolk of the Odisha.
Development
Today the Baandha fabric is popularly known by its geographical and cultural name Sambalpuri owing to the pioneering efforts of Sri Radhashyam Meher, who brought about a radical improvement in the skills of the craftsmen and the quality of the products. Other master craftsmen who contributed to the development of Sambalpuri textiles were Padmashree Kailash Chandra Meher, Padmashree Kunja Bihari Meher, Padmashree Chatrubhuja Meher and Padmashree Krutharth Acharya, Handloom Technologist Mr. Ramkrishna Meher. Sambalpuri textiles today include furnishing materials, dress materials and saris in silk, cotton and mercerised cotton in a variety of colours and many different designs. Baandha craftsmen are also masters of the 'extra warp' and 'extra weft' style of designing which can be seen in almost all forms of Baandha textiles.
In 1926, Radhashyam designed the first handloom to weave textiles of ninety inches width. His dexterity in the Baandha art and his ability to motivate the weaving community in the region to improve their skills by providing the necessary training and incentives enabled the creation of new designs that received international fame and recognition.
Radhashyam Meher established his proprietary concern, named 'Utkal Parda Agency', at Sambalpur for the research, production and marketing of Sambalpuri textiles.
Important handloom clusters of Odisha
Serial No. | Category of cluster | Name of district | Name of cluster | Number of clusters |
---|---|---|---|---|
1 | A | Bargarh | Attabira, Bargarh, Bheden, Barpali, Bijepur, Padampur, Sohela, Bhatli | 8 |
2 | A | Subarnapur/Sonepur | Birmaharajpur, Sonepur, Ulunda, Binika | 4 |
3 | A | Boudh | Boudh | 1 |
4 | B | Balangir | Patnagarh, Agalpur, Bangamunda | 3 |
5 | B | Nuapada | Khariar (Sinapali) | 1 |
6 | B | Sambalpur | Rengali | 1 |
Further reading
- The Orissan art of weaving, by Kesabachandra Mehera, Publisher: Keshab Chandra Meher, 1995.
- Indian ikat textiles, V & A Museum Indian Art Series. by Rosemary Crill, Victoria and Albert Museum. V & A Publications, 1998. ISBN 1851772421.
References
- Alkazi, Roshan (1983) "Ancient Indian costume", Art Heritage; Ghurye (1951) "Indian costume", Popular book depot (Bombay); Boulanger, Chantal; (1997)
- "How sambalpuri sarees are suitable for all season" Archived 13 January 2022 at the Wayback Machine Hindustan Times, 5 September 2009.
- "'Sambalpuri saree' and 'Berhampuri pattu' to get GI recognition soon" The Hindu, 8 March 2009.
- "Sambalpuri saree set to be protected" NISCAIR Online Periodicals Repository, March 2006.
- "A glimpse at Sambalpuri Saree of Odisha".
- "The History of Indian Sarees: A Legacy for Centuries". 13 February 2020.