Bloc de béton manufacturé
Le bloc de béton manufacturé (BBM) est un élément de maçonnerie moulé, inauguré avec l'invention du ciment, et qui a été produit en masse à partir des années 1950.
Pour les articles homonymes, voir BBM.


Dénominations courantes
- En France
Les fabricants vendent des blocs de béton manufacturé (abrégé « BBM » ou « bloc de béton ») puis la maîtrise d'œuvre concevant les bâtiments prescrit des agglomérés de ciment ou agglomérés de béton creux (« agglo » dans le langage courant).
Selon les régions, le BBM porte couramment et plus ou moins improprement d'autres noms :
Caractéristiques
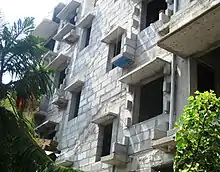
C'est un bloc de béton moulé fréquemment en forme de parallélépipède creux ou non. On comptabilise plus de 150 références de blocs de béton différents, en forme comme en composition. C'est parmi les matériaux de construction conventionnels celui qui a le meilleur rapport qualité/prix. Il fait partie des matériaux lourds (ayant une forte masse thermique).
De forme régulière, extrêmement résistant, peu coûteux, le bloc de béton est le composant principal des murs extérieurs des constructions conventionnelles. Il peut être utilisé seul, notamment dans la construction de hangars, de murs de clôture, éventuellement recouvert d'un enduit.
Selon les pays, on recouvre le bloc de béton d'une couche d'isolant thermique. L'isolant est lui couvert d'un enduit coloré (crépi), d'un bardage ou dans le cas du mur creux, apparu dans les pays à la pluviométrie élevée, dédoublé par un parement en brique ou en bloc. Il existe pour cet usage des blocs de béton de couleur destinés à rester apparents, notamment dans le nord de la France.
Les blocs sont empilés les uns sur les autres par rangs successifs jointés entre eux grâce à une fine épaisseur de mortier en général de 1 cm à 1,5 cm.
Composition
Les blocs les plus courants sont en béton de ciment ou en terre cuite, suivant les habitudes régionales. Ils sont de poids moyen (ceux en ciment sont plus lourds que ceux en terre cuite) et d'isolations thermique et phonique médiocres.
Les blocs en terre cuite alvéolaire permettent de respecter la réglementation thermique actuelle lorsqu'ils sont de forte épaisseur (et leur isolation phonique est alors correcte).
Les blocs de béton léger incorporent des granulats peu denses comme l'argile expansée, la pierre ponce, le schiste expansé, ou encore la pouzzolane, dans le but d'améliorer leur isolation thermique (mais leur isolation phonique est aussi médiocre).
Les blocs de béton cellulaire sont comparables aux précédents, à la différence que le matériau est homogène (pas de granulat).
Les blocs silico-calcaires, obtenus par autoclavage de chaux et de sable siliceux, sont lourds et non isolants, mais permettent une isolation phonique correcte.
Enfin, il existe aussi des blocs de torchis, mais leur utilisation est beaucoup plus rare, et limitée à certaines régions spécifiques.
Dimensions

Leurs dimensions sont en France généralement de 20 cm de hauteur, 50 cm de longueur, leur épaisseur totale est variable. Les épaisseurs les plus courantes sont 10 cm, 15 cm (refend), ou 20 cm (190 mm) (porteur extérieur) ; plus rarement 5 cm (planelle).
En Belgique, les dimensions usuelles sont : longueur 39 cm, hauteur 19 cm, épaisseurs 9 cm, 14 cm, 19 cm et 29 cm.
Il existe plusieurs types de bloc de béton :
- les blocs de béton courants creux ;
- les blocs de béton pleins (utilisés principalement en infrastructure et pare-feu) ;
- les blocs de béton d'angle (pour chaînages verticaux) ;
- les blocs de béton en « U » (pour chaînages horizontaux et pour linteaux) ;
- les blocs de béton à joints minces de dernière génération : ceux-ci ne nécessitent plus l'utilisation de truelles ni bétonnières pour utiliser à la place un mortier-colle ;
- les blocs béton de schiste et de pierre ponce commencent à apparaître sur le marché. Basés sur le même principe que le bloc béton, ils présentent de nombreux avantages (plus légers, plus isolants).
Composition
Associé à des rupteurs de ponts thermiques et à la plâtrerie traditionnelle, le bloc de béton nécessite généralement un isolant (intérieur ou extérieur). Il est en effet composé de 87 % de granulats (pierres, graviers, sable) issus de carrières locales, de 7 % de ciment (calcaire et argile) et de 6 % d'eau.
À noter : seuls les 7 % de ciment nécessitent une cuisson, le bloc, quant à lui étant moulé à froid, l'énergie utilisée pour sa fabrication est donc relativement faible (voir fiche de déclaration environnementale et sanitaire). Étant 100 % minéral, il est totalement recyclable.
Classe de résistance
Sa structure peut être creuse ou pleine selon sa classe de résistance. En effet, plus le bloc de béton aura de charge à supporter, plus sa classe de résistance devra être élevée, et plus il sera lourd.
Les classes de résistance des blocs de béton avec granulats ordinaires sont :
- B40 : résistance à 40 bars soit 4 MPa
- B60 : résistance à 60 bars soit 6 MPa
- B80 : résistance à 80 bars soit 8 MPa
- B120 : résistance à 120 bars soit 12 MPa
- B160 : résistance à 160 bars soit 16 MPa
Caractéristiques thermiques
La conductivité thermique λ (en watts par mètre-kelvin) des blocs de béton avec granulats ordinaires oscille entre 1,07 W/m.K. et 2,71 W/m.K. selon sa masse volumique, son utilisation intérieure ou extérieure[1].
Celle des blocs de béton en argile expansée oscille entre 0,14 W/m.K. et 1,10 W/m.K. selon sa masse volumique et son utilisation intérieure ou extérieure[1].
Celle des blocs de béton cellulaire oscille entre 0,10 W/m.K. et 0,52 W/m.K. selon sa masse volumique et son utilisation intérieure ou extérieure[1].
Les blocs silicocalcaires oscillent entre 0,36 W/m.K. et 3,71 W/m.K. selon leur masse volumique et leur utilisation intérieure ou extérieure[1].
Pour un bloc de conductivité thermique = 0,9 W/m.K. La résistance thermique R est donc de :
- pour 5 cm d'épaisseur : R = 0,05 m².K/W
- pour 10 cm d'épaisseur : R = 0,11 m².K/W
- pour 15 cm d'épaisseur : R = 0,16 m².K/W
- pour 20 cm d'épaisseur : R = 0,22 m².K/W
- pour 22 cm d'épaisseur : R = 0,25 m².K/W
La norme française RT2005 pour les murs en contact avec l'extérieur nécessite un R situé entre 2,5 et 2,7 m2.K/W.(après isolation).
Fabrication des blocs de béton
Usines à blocs
Les blocs sont fabriqués dans des usines : on en trouve 400, réparties sur l'ensemble du territoire français. Elles comportent une centrale à béton et des presses fixes, vibrantes : des vibrations importantes permettent de diminuer la quantité de ciment dans le béton tout en conservant les mêmes capacités. Les blocs sont ensuite placés en étuves pendant vingt-quatre à quarante-huit heures, où ils sèchent et se solidifient de manière naturelle, sans aucune adjonction. À la fin de ce processus de séchage, ils sont prêts à être livrés sur les chantiers de construction voisins et ne nécessitent aucun emballage.
En France : Installation classée pour la protection de l'environnement
Selon la législation française, les usines à blocs sont des Installations classées pour la protection de l'environnement (ICPE). En effet, ce type d'installation est concerné par la rubrique no 2522 de la nomenclature des installations classées (« installation de fabrication de produits en béton par procédé mécanique[2] ») :
- les installations ayant une puissance installée du matériel de malaxage et de vibration supérieure à 400 kW sont soumises à autorisation préfectorale simplifiée (régime de l'enregistrement). Cette autorisation simplifiée est délivrée sous la forme d'un arrêté préfectoral qui impose à l'exploitant le respect d'un certain nombre de prescriptions techniques, notamment celles de l'arrêté ministériel du 8 août 2011 relatif aux prescriptions générales applicables aux installations relevant du régime de l’enregistrement au titre de la rubrique no 2522[3] ;
- les installations ayant une puissance installée du matériel de malaxage et de vibration comprise entre 40 kW et 400 kW doivent être déclarées. Les exploitants de ces installations doivent respecter les prescriptions techniques de l'arrêté ministériel du 26 novembre 2011 relatif aux prescriptions générales applicables aux installations de fabrication de produits en béton, soumises à déclaration sous la rubrique no 2522[4].
L'instruction des demandes d'autorisation simplifiée d'exploiter ainsi que le contrôle du respect des prescriptions techniques par les exploitants sont réalisés par l'inspection des installations classées[5].
Pondeuses
Plus artisanalement, des pondeuses peuvent être utilisées pour la fabrication de ces blocs (pleins, creux, hourdis, chaînages, et blocs de tout type)… Certaines machines permettent aussi la fabrication de pavés autobloquants, de claustras ou bien de bordures et caniveaux. Ce sont des presses mobiles, qui déposent les blocs au sol par rangées de trois à dix, selon les dimensions des blocs et la capacité de la machine.
Ce type de matériel, manuel ou semi-automatique, peut être utilisé dans des pays en voie de développement, en raison de son coût relativement faible, de son encombrement réduit qui lui permet d'être facilement déplacé sur les lieux de fabrication, et surtout de la qualité des produits finaux, en comparaison avec de simples blocs-ciment, à base de mortier et non de béton.
Moules manuels
Une autre méthode artisanale pour la fabrication des blocs ou des pavés consiste à utiliser des moules manuels ; la matière, béton ou mortier, est déposée sur le sol par retournement du moule. Cette méthode est évidemment beaucoup plus fastidieuse, et le rendement est bien moindre. De plus la qualité des produits est inférieure, comparativement aux pondeuses qui offrent la possibilité de fabriquer des blocs réguliers et mieux « compactés ». Cette méthode peut être améliorée par l'utilisation d'une table vibrante.
Comparatif des productions
Une presse fixe peut produire en moyenne 5 000 à 10 000 blocs par jour, tandis que la production par pondeuse varie de 1 000 à 3 500 blocs, dans le cas des manuelles, et de 3 000 à 8 000 blocs pour les semi-automatiques.
Notes et références
- « La conductivité thermique d'un matériau (λ) », www.energieplus-lesite.be, Architecture et climat de l'UCL (consulté le 29 avril 2019).
- « 2522. Installation de fabrication de produits en béton par procédé mécanique », sur www.ineris.fr (consulté le ).
- « Arrêté du 8 août 2011 relatif aux prescriptions générales applicables aux installations relevant du régime de l’enregistrement au titre de la rubrique no 2522 de la nomenclature des installations classées pour la protection de l’environnement », sur www.ineris.fr (consulté le ).
- « Arrêté du 26 novembre 2011 relatif aux prescriptions générales applicables aux installations de fabrication de produits en béton, soumises à déclaration sous la rubrique no 2522 de la nomenclature des installations classées pour la protection de l’environnement », sur www.ineris.fr (consulté le ).
- « Missions », sur installationsclassees.developpement-durable.gouv.fr (consulté le ).
- Portail de l’architecture et de l’urbanisme
- Portail du bâtiment et des travaux publics