Corrosion sous contrainte
La corrosion sous contrainte d'un métal ou d'un alliage résulte de l'action conjuguée d'une contrainte mécanique en tension (contrainte résiduelle ou appliquée) et d'un milieu environnant agressif vis-à-vis d'un matériau sensible au phénomène. On considère généralement que ces trois conditions (contrainte, environnement et sensibilité du matériau au phénomène) doivent être réunies simultanément pour observer la corrosion sous contrainte. Cependant, dans certains cas, deux de ces conditions réunies (dont nécessairement la contrainte mécanique) sembleraient pouvoir être suffisantes à déclencher le processus. Le phénomène est particulièrement insidieux car il peut conduire à une défaillance soudaine et catastrophique du matériau à une valeur bien inférieure à sa limite de résistance mécanique normale.
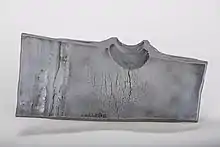

Contrainte mécanique
La contrainte mécanique de traction en jeu dans le phénomène de corrosion sous contrainte peut être d'origine résiduelle (cintrage, écrouissage, laminage à froid, soudage…), thermique (dilatation, variation de pression), ou inhérente à la fonction d'une installation (gazoducs, oléoducs, câbles de ponts suspendus, structures de soutènement, coques de sous-marin…). Ce type de corrosion, particulièrement pernicieux et dangereux pour les installations, se caractérise par l'apparition de fissures intergranulaires ou transgranulaires dont la direction générale de propagation est perpendiculaire à la contrainte principale.
Les contraintes en tension (traction) sont particulièrement néfastes pour la corrosion du matériau car elles ouvrent les fissures naissantes et facilitent de ce fait l'accès des surfaces des fissures à l'environnement agressif (généralement une solution aqueuse), tandis que les contraintes en compression referment les fissures et protègent ainsi la surface du matériau fissuré du contact avec le milieu agressif.
Les conditions de chargement cyclique peuvent altérer les propriétés de l'acier et favoriser l'initiation de fissures intergranulaires[1].
Environnement chimique
L'environnement agressif est spécifique. Il joue un rôle important et souvent encore mal compris, car des concentrations minimes en certaines espèces chimiques très actives en corrosion localisée comme les chlorures (corrosion par piqûres) et les espèces réduites du soufre (H2S, sulfures, thiosulfates, ions polythionates)[2],[3] suffisent à produire une fissuration catastrophique, pouvant conduire à une défaillance soudaine et dévastatrice[4]. L'acier inoxydable austénitique sensibilisé souffre de fissuration par corrosion sous contrainte dans les solutions aqueuses de tous les anions halogénures (F−, Cl−, Br− et I−), les chlorures semblant être les plus agressifs[5]. La présence d'hydrogène (H2 moléculaire et surtout H• atomique) dans le milieu est également susceptible de causer de la fragilisation par l'hydrogène (stress corrosion cracking, SCC)[6]. La corrosion sous contrainte en présence de sulfure d'hydrogène (H2S), un poison empêchant la recombinaison de l'hydrogène atomique H• en H2 moléculaire et favorisant sa diffusion dans les métaux, est un cas particulièrement aigu qui affecte l'industrie du pétrole et du gaz exploitant des gisements d'hydrocarbures riches en hydrogène sulfuré. Le terme usité en anglais attribué à ce phénomène est celui de sulfide stress cracking (en), qui pourrait se traduire par « corrosion sous contrainte induite par les sulfures ».
Nature du métal ou composition de l'alliage
La nature du métal ou la composition de l'alliage déterminent la nature, la composition, la porosité, la densité et l'épaisseur de la couche d'oxydes qui se forment à la surface du métal et le protègent. Les aciers inoxydables à base de fer (Fe), de chrome (Cr) et de nickel (Ni) présentent des teneurs en Cr et Ni dont dépendent les caractéristiques de la couche d'oxyde protectrice et sa perméabilité aux agents agressifs (O2, H2, H•, H+, et ions).
Pour les teneurs de chrome élevées dans un acier inoxydable Cr/Ni, il se forme du Cr2O3 protecteur alors que pour quelques pourcents de chrome seulement dans l’alliage, Ni(OH)2, moins protecteur, se forme préférentiellement[7].
La dimension des cristallites, leur orientation, les joints de grains, les dislocations, les défauts cristallins et la présence de carbures, de nitrures, ou d'hydrures au sein de la structure cristalline du matériau sont également des éléments importants pour sa sensibilité à la corrosion sous contrainte et qui dépendent directement de la nature et de la mise en œuvre du matériau (procédé de fabrication, soudure, traitements thermiques...)[7]. La teneur en carbone dans les aciers inoxydables austénitiques et la présence, ou non, d'additions stabilisantes comme le niobium (Nb) ou le titane (Ti) est également importante. En effet, si la teneur de l'acier en carbone est trop élevée, il se forme du carbure de chrome aux dépens de l'oxyde de chrome(III) (Cr2O3) protecteur qui constitue essentiellement la couche d'oxyde imperméable passivant la surface des aciers inoxydables. Quelques centaines de ppm (mg/kg = 10-6) de niobium ajouté à l'acier lors de sa fabrication peuvent suffire à piéger de faibles teneurs en carbure et en nitrure interstitiels sous forme de carbure et de nitrure de niobium et améliorent considérablement les propriétés mécaniques de l'acier et sa résistance à la corrosion. Pour pouvoir résister à la corrosion sous contrainte, les aciers inoxydables AISI 304 et AISI 316 doivent être bas carbone (low carbon) d'où le suffixe L qui leur est alors ajouté. L'abaissement de la teneur en carbone de l'acier inoxydable permet de minimiser la précipitation de carbures de chrome comme Cr23C6 (1 atome de carbone accapare à lui seul de près de 4 atomes de chrome protecteur !) lorsque l'acier est porté à haute température, notamment au moment d'une soudure[8].
En effet, la sensibilisation des aciers inoxydables se produit par leur exposition à des températures élevées pendant le soudage, le traitement thermique ou les conditions de service, provoquant une précipitation de carbure de chrome aux joints de grains et un appauvrissement en chrome (déchromisation) dans les zones proches des joints de grains, favorisant ainsi l'attaque intergranulaire (IG) et la fissuration par corrosion sous contrainte intergranulaire (IGSCC)[5].
Des traitements thermiques appropriés (trempe très rapide) peuvent également être mis en œuvre pour limiter la formation délétère de carbure de chrome au droit des soudures. Lors de la perte locale de l'oxyde de chrome par précipitation de carbure de chrome, des zones anodiques (réaction d'oxydation) se forment à cet endroit dans l'acier et le fer métallique (Fe0) de l'alliage se dissout sous forme d'ions ferreux (Fe2+). Simultanément, des zones cathodiques (réaction de réduction) se forment dans des régions avoisinantes où l'oxygène (O2) (conditions oxiques) ou les protons (H+) de l'eau (conditions anoxiques) sont réduits. Il s'ensuit une corrosion galvanique localisée (formation d'une pile électrique)[3].
- Réaction d'oxydation à l'anode: Fe → Fe2+ + 2 e−
- Réaction de réduction à la cathode: 2 H+ + 2 e− → 2 H•
Une partie des atomes d'hydrogène atomique (H•) naissants diffusent ensuite dans le métal et se concentrent au niveau de défauts cristallins ou de dislocations. Ils se recombinent alors sous forme d'hydrogène moléculaire (H2) et des bulles gazeuses se forment dans le métal. Ces bulles exercent des pressions très élevées qui mettent sous tension (contrainte de traction) le métal qui se fissure ou se délamine avec parfois apparition de cloques en surface (blistering). C'est le phénomène de fragilisation par l'hydrogène (hydrogen embrittlement).
Initiation et propagation
L'évolution de la fissuration par corrosion sous contrainte se fait en deux étapes : initiation puis propagation[9].
Durant la période d'initiation (temps d'incubation, d'amorçage), la fissure est de très petite taille et ne se propage pas, même lorsque les conditions mécaniques requises sont présentes. De ce fait sa détection est très difficile et elle peut facilement passer inaperçue.
Les fissures ne se propagent que lorsque la contrainte en traction est supérieure à un certain seuil (contrainte limite de rupture) qui dépend de la sensibilité du matériau et du milieu aqueux agressif environnant. Au-delà, la vitesse de propagation augmente avec la contrainte.
Mécanismes de corrosion sous contrainte
Différents mécanismes sont avancés pour la propagation des fissures dans les métaux et les alliages métalliques. Les phénomènes incriminé concernent des couplages mécano-électrochimiques.
Historiquement, le premier mécanisme identifié est la fragilisation par l'hydrogène. L'hydrogène, généralement produit par corrosion aqueuse (provenant de la réduction des protons (ions H+ ou H3O+) de l'eau) ou introduit lors d'opérations de soudage mal maîtrisées (baguettes de soudage à l'arc humides ou mal-séchées préalablement à l'étuve et thermolyse de l'eau avec production d'hydrogène atomique), se déplace dans le métal sous forme monoatomique. Il se concentre dans les zones de fortes contraintes triaxiales (en pointe de fissure) et abaisse l'énergie de cohésion du réseau cristallin de l'alliage métallique. C'est ainsi que la fissure ou le défaut initial peut se propager périodiquement à des niveaux de contraintes inférieurs à celui de la limite mécanique du matériau.
Si ce mécanisme est pertinent pour les aciers ferritiques ou ferrito-martensitiques, qui sont particulièrement sensibles à la fragilisation par l'hydrogène, son rôle est plus controversé pour les aciers austénitiques. Dans tous les cas, ce mode de fragilisation disparaît aux températures élevées, par exemple au-delà de 200 °C, car l'interaction de l'hydrogène avec le réseau cristallin diminue quand la température augmente et que l'hydrogène peut diffuser plus rapidement et ainsi s'échapper du métal.
Un deuxième mécanisme de corrosion sous contrainte évoqué à partir des années 1970 fait appel à une dissolution assistée par le glissement. Localement, la contrainte induit une déformation plastique locale qui se traduit par l'émergence en surface de dislocations. Celles-ci rompent ou endommagent localement le film d'oxydes de chrome protecteur, et la corrosion s'accroît localement de manière temporaire, jusqu'à ce que le film protecteur se reconstitue (repassivation). La répétition périodique de cette séquence – au cours de laquelle les émergences de dislocations se concentrent en pointe de fissure – aboutit à une propagation de la fissure par enlèvement local de matière. Un argument fort en faveur de ce mécanisme, notamment pour les alliages austénitiques, a été l'observation d'une relation globalement linéaire entre la vitesse de corrosion et la vitesse de propagation des fissures lorsqu'on fait varier l'agressivité du milieu.
Cependant, des limitations à cette théorie ont été relevées, notamment la difficulté à expliquer des faciès de rupture en apparence fragiles. D'autres mécanismes plus complexes, faisant notamment intervenir des interactions entre corrosion, hydrogène et plasticité ont été plus récemment avancés[Quand ?][Qui ?][réf. nécessaire][10],[11].
Parc nucléaire en France
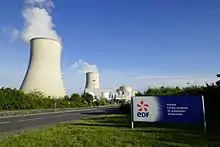
En 2021 et 2022, des phénomènes de corrosion sous contrainte ont été détectés au voisinage de soudures sur les tuyaux d'injection d'eau de refroidissement de secours des circuits primaires de plusieurs réacteurs nucléaires opéré en France par EDF[12],[13],[14],[15],[16]. Par mesure de précaution plusieurs réacteurs du parc nucléaire français (paliers N4 et N3 de 1 450 et 1 300 MWe de puissance électrique respective) ont été mis à l'arrêt (centrales de Civaux, Chooz et Penly), ce qui contribue à l'augmentation des prix de l'énergie durant cette période[17],[18],[19].
Les indications de corrosion sous contrainte ont été mises en évidence et confirmées par examen non destructif (END) recourant in situ sur la canalisation affectée à la radiographie industrielle et aux contrôles par ultrasons, deux procédés volumiques permettant de détecter les défauts enfouis dans la pièce[16],[17].
Cette corrosion sous contrainte est inattendue et inédite, la nuance d'acier inoxydable utilisée pour la canalisation affectée étant supposée résister à l'environnement chimique du circuit primaire principal. En effet, l'eau du circuit primaire est très pure (pas de chlorures, ni de sulfures), ne contient plus d'oxygène dissout et sa composition chimique est rigoureusement contrôlée (B(OH)3, LiOH...). L'environnement chimique était donc a priori considéré comme peu agressif et l'alliage métallique supposé non-sensible. La haute température et la présence d'hydrogène dissout dans l'eau (ajout de H2 pour protéger le circuit primaire contre les radicaux oxydants produits par la radiolyse de l'eau), ou d'autres facteurs encore inconnus et restant à identifier (comportement cyclique contrainte-déformation avec des cycles de variation de température ; conditions de réalisation des soudures incriminées ?), devront être pris en considération lors de la recherche de la cause première (root cause) de ce phénomène de dégradation inattendu et découvert inopinément. Une hypothèse de base qui pourrait être ici remise en cause est celle souvent admise des trois conditions à réunir simultanément dans un diagramme de Venn pour pouvoir observer le phénomène. Peut-être, suffit-il de réunir seulement deux de ces conditions pour déclencher ce processus particulièrement insidieux.
Matériaux non-métalliques
Hormis les métaux et les alliages, d'autres matériaux non-métalliques comme les polymères, les céramiques et le verre sont parfois également susceptibles de présenter de la fissuration sous contrainte environnementale. Les mécanismes en oeuvre sont différents mais impliquent tous la présence de contraintes mécaniques en traction. Ces phénomènes de dégradation de matériaux non-métalliques sous contrainte sont repris sous l'appellation de environmental stress cracking (en) (ESC) en anglais, distincts de la corrosion métallique sous contrainte.
Articles connexes
Notes et références
- (en) Hamid Niazi, Reg Eadie, Weixing Chen et Hao Zhang, « High pH stress corrosion cracking initiation and crack evolution in buried steel pipelines: A review », Engineering Failure Analysis, vol. 120, , p. 105013 (ISSN 1350-6307, DOI 10.1016/j.engfailanal.2020.105013).
- Ruel 2014.
- Elboujdaini et Revie 2009.
- (en) ASM International, Metals Handbook (Desk Edition), chapitre 32 (« Failure Analysis »), American Society for Metals.
- Kappes 2019.
- Richard Rios, « Étude des mécanismes de corrosion sous contrainte de l'alliage 600 (NC15Fe) dans l'eau à haute température », sur theses.fr, (consulté le ).
- Pierre Laghoutaris, « Corrosion sous contrainte de l'alliage 600 en milieu primaire des réacteurs à eau sous pression : apport à la compréhension des mécanismes », sur pastel.archives-ouvertes.fr, (consulté le ).
- Holterbach 2005.
- Raquet 1994.
- S. P. Lynch (2007-03-11) « Progress towards understanding mechanisms of hydrogen embrittlement and stress corrosion cracking » dans Corrosion 2007 , OnePetro. Consulté le 2022-06-04.
- Gary S. Was, Diana Farkas et Ian M. Robertson, « Micromechanics of dislocation channeling in intergranular stress corrosion crack nucleation », Current Opinion in Solid State and Materials Science, vol. 16, no 3, , p. 134–142 (ISSN 1359-0286, DOI 10.1016/j.cossms.2012.03.003).
- Autorité de sûreté nucléaire (ASN), « Phénomène de corrosion sous contrainte détecté sur le circuit d’injection de sécurité du réacteur 1 de la centrale de Civaux – Arrêt des réacteurs de 1 450 MWe pour réalisation de contrôles », sur asn.fr, (consulté le )
- IRSN, « Note d'information : Détection de fissures sur des tuyauteries du système d’injection de sécurité des réacteurs n° 1 et n° 2 de la centrale nucléaire de Civaux », sur irsn.fr, (consulté le )
- Autorité de sûreté nucléaire, « Phénomène de corrosion sous contrainte détecté sur certains réacteurs » (consulté le )
- Autorité de sûreté nucléaire, « Phénomène de corrosion sous contrainte : l’ASN demande à EDF d’approfondir ses analyses » (consulté le )
- Autorité de sûreté nucléaire, « Centrale nucléaire de Civaux Réacteurs de 1450 MWe – EDF. Inspection du 17/01/2022 au 18/01/2022. Corrosion sous contrainte des tuyauteries auxiliaires du Circuit Primaire Principal réacteur 1. INSSN-BDX-2022-0833.pdf » (consulté le )
- IRSN, « Endommagement par corrosion sous contrainte de tuyauteries connectées au circuit primaire principal de réacteurs d’EDF », sur IRSN, (consulté le )
- « Des réacteurs nucléaires à l’arrêt en raison d’un problème de corrosion « sérieux et inattendu » », Le Monde, (lire en ligne, consulté le )
- « EDF de plus en plus inquiet pour son parc nucléaire, en raison de problèmes de corrosion », Le Monde, (lire en ligne, consulté le )
Bibliographie
: document utilisé comme source pour la rédaction de cet article.
- V.S. Raja et T. Shoji, Stress Corrosion Cracking: Theory and Practice, Elsevier, (ISBN 978-0-85709-376-9, lire en ligne)
- ASM International, Metals Handbook (Desk Edition) Chapter 32 (Failure Analysis), American Society for Metals, (1997) pp 32–24 to 32-26
- ASM Handbook Volume 11 "Failure Analysis and Prevention" (2002) "Stress-Corrosion Cracking" Revised by W.R. Warke, American Society of Metals. Pages 1738-1820
- "Mechanical Properties of Ceramics" by John B. Wachtman, W. Roger Cannon, and M. John Matthewson. Chapter 8.
- ASTM, « ASTM G36-94 (2018) Standard practice for evaluating stress-corrosion-cracking resistance of metals and alloys in a boiling magnesium chloride solution », sur astm.org, (consulté le )
- O. Raquet, M. Helie, Ph. Sornay et G. Santarini, « Amorçage et propagation des fissures de corrosion sous contrainte. », Revue de métallurgie, vol. 91, no 9, , p. 1325–1325 (ISSN 0035-1563, DOI 10.1051/metal/199491091325).
- Redvers N. Parkins (2000-03-26) « A review of stress corrosion cracking of high pressure gas pipelines » dans Corrosion 2000 , OnePetro. Consulté le 2022-06-04.
- (en) B. Gu, J. Luo et X. Mao, « Hydrogen-facilitated anodic dissolution-type stress corrosion cracking of pipeline steels in near-neutral pH solution », Corrosion, vol. 55, no 1, , p. 96–106 (ISSN 0010-9312, DOI 10.5006/1.3283971, lire en ligne)
- Fiona Ruel, Contribution électrochimique à l'étude de la corrosion sous contrainte des aciers inoxydables lean duplex en milieu purement chloruré et sous présence de sulfure d'hydrogène, École nationale supérieure des mines de Saint-Étienne, (lire en ligne).
- Holterbach, « Cours ENSITM (corrosion partie 3) : La corrosion sous contrainte (CSC) » [PDF], sur n6a.free.fr, (consulté le ).
- P. Scott, « A review of irradiation assisted stress corrosion cracking », Journal of Nuclear Materials, vol. 211, no 2, , p. 101–122 (ISSN 0022-3115, DOI 10.1016/0022-3115(94)90360-3)
- M. Elboujdaini et R. W. Revie, « Metallurgical factors in stress corrosion cracking (SCC) and hydrogen-induced cracking (HIC) », Journal of Solid State Electrochemistry, vol. 13, no 7, , p. 1091–1099 (ISSN 1432-8488, DOI 10.1007/s10008-009-0799-0).
- Peter M. Scott et Pierre Combrade, « General corrosion and stress corrosion cracking of Alloy 600 in light water reactor primary coolants », Journal of Nuclear Materials, vol. 524, , p. 340–375 (ISSN 0022-3115, DOI 10.1016/j.jnucmat.2019.04.023)
- Sridhar Ramamurthy et Andrej Atrens, « Stress corrosion cracking of high-strength steels », Corrosion Reviews, vol. 31, no 1, , p. 1–31 (ISSN 0334-6005, DOI 10.1515/corrrev-2012-0018)
- M.A. Mohtadi-Bonab, « Effects of different parameters on initiation and propagation of stress corrosion cracks in pipeline steels: A Review », Metals, vol. 9, no 5, , p. 590 (DOI 10.3390/met9050590
)
- Mariano A. Kappes, « Localized corrosion and stress corrosion cracking of stainless steels in halides other than chlorides solutions: A Review », Corrosion Reviews, vol. 38, no 1, , p. 1–24 (ISSN 0334-6005, DOI 10.1515/corrrev-2019-0061).
Voir aussi
- Portail des sciences des matériaux
- Portail de la physique
- Portail de la chimie