Câble électrique à haute tension
Un câble électrique à haute tension est un câble utilisé pour le transport d'électricité, que ce soit en courant alternatif ou en courant continu. Il est composé de différentes parties assemblées de manière concentrique, les principales sont : au centre un conducteur permet de transporter l'électricité, ensuite vient une isolation électrique pour empêcher le courant de s'écouler vers la terre, le tout est entouré d'une gaine métallique afin de confiner le champ électrique à l'intérieur du câble et d'une protection extérieure qui assure de bonnes propriétés mécaniques et le protège des agressions extérieures. Les câbles électriques à haute tension, utilisés pour des liaisons souterraines ou sous-marines est donc à distinguer des Conducteurs haute tension pour Ligne à haute tension qui eux ne comportent pas d'isolation.
On peut distinguer 3 grandes familles technologiques : les câbles à papier imprégné de masse, ceux sous pression et ceux extrudés. Les premiers ne sont plus utilisés que pour les liaisons HVDC très haute tension. Ceux sous pression sont divisés entre ceux utilisant l'huile et ceux utilisant le gaz pour maintenir la pression et refroidir le conducteur d'une part et entre ceux à pression interne et ceux à pression externe d'autre part. Ces câbles sont très répandus mais ne sont quasiment plus installés. En effet les câbles extrudés, principalement à isolation en polyéthylène réticulé se sont imposés dans tous les domaines depuis les années 1970. Toutefois la durée de vie longue des câbles à papier imprégné de masse et sous pression étant grande, ils restent très présents dans les réseaux électriques.
La connexion de différentes sections de câble ou d'un câble aux appareils électriques est délicate, des raccords spéciaux sont utilisés : boîtes de jonction entre câbles, extrémité entre câbles et autres appareils.
L'enterrement des lignes à haute tension est un sujet de débat permanent. Le comportement très capacitif des câbles oblige la construction de station de compensation électrique à intervalles réguliers, 20 km pour le 400 kV, pour permettre le transport de puissance dans le cas du courant alternatif. Ceci explique que la proportion de lignes enterrées au-delà de tension de 220 kV est très faible en France et dans le monde. Parmi les autres applications des câbles, le transport d'électricité sous-marine occupe une place importante. Pour les raisons précitées le transport en courant continu, qui ne nécessite pas de compensation, est privilégié.
La fabrication des câbles électriques haute tension est délicate, la qualité doit être particulièrement élevée pour assurer une durée de vie satisfaisante. Des techniques de diagnostics ont été développées pour garantir l'intégrité du câble à sa livraison puis lors de son exploitation.
Parmi les développements en cours, la tension supportée par les câbles XLPE est appelée à augmenter. Ils doivent également devenir compatibles avec les stations HVDC commutées par les lignes. Par ailleurs, des câbles en supraconducteurs sont déjà en exploitation à petite échelle sur des projets expérimentaux et devraient se développer dans le futur.

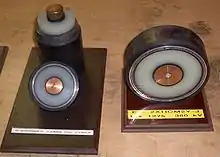
Histoire
Les précurseurs des câbles électriques haute tension sont les câbles télégraphiques[1]. Les premières liaisons souterraines de transmission d’énergie électrique sont des systèmes primaires peu performants, ne permettant pas d’excéder quelques dizaines de volts. En 1879, l’invention de la presse à plomb par l’ingénieur suisse Borel permet de mouler une gaine de plomb directement sur les conducteurs isolés aux fibres de jute et supprime en partie les problèmes d’absorption d’humidité en rendant le câble étanche. Peu après, en imprégnant l’isolant en jute d’un mélange d’huile et de résine, des câbles monopolaires concentriques à 3 000 V peuvent être fabriqués et sont posés à Paris en 1890[1].
Sebastian Ziani de Ferranti construit en 1887 un câble à isolation fait de papier sec, le conducteur est en cuivre, la gaine en acier. Il peut transporter une tension de 11 kV[2]. L'association de bandelettes de papier enroulées en hélice et d'une gaine de plomb est réalisée aux États-Unis en 1893[1]. Par ailleurs, le caoutchouc vulcanisé est breveté en 1844 par Charles Goodyear, il n'a été utilisé pour l'isolation des câbles afin d'alléger l'ensemble que dans les années 1880[3]. Un câble isolé avec du caoutchouc est utilisé en 1897 pour le transport de l'électricité depuis les chutes du Niagara en 1897. Les câbles à papier imprégné de masse sont disponibles commercialement depuis 1895.
Les câbles à isolation papier imprégné se développent et atteignent une tension de 15 kV en 1910, 30 à la veille de la Première Guerre mondiale, puis 63 kV après celle-ci. La taille de l'isolant et donc des câbles est également réduite avec le temps. Sans pression, la technologie touche à ses limites, des câbles à 3 conducteurs permettent de faire progresser les transmissions[1].
En 1916, Martin Hochstadter brevette la couche semi-conductrice séparant le conducteur de l'isolant. Elle porte ainsi son nom[3]. Cette couche est au potentiel du conducteur. Des "cônes" permettent de limiter le stress électrique à ses extrémités. Avant les années 1960, ces cônes étaient fabriqués à la main sur place après la mise en place du câble. Ils étaient protégés par un pothead, autrement dit un diélectrique entouré d'un isolateur constitué de métal et de porcelaine et placé autour du câble. À partir des années 1960, des terminaux faits de caoutchouc ou d'élastomère ont été développés, ils sont posés sur les extrémités du câble[4].

En 1917, l’ingénieur italien Emmanuelli, de la société Pirelli, dépose un brevet décrivant les principes d’un câble novateur appelé par la suite câble à huile fluide, c'est-à-dire avec un canal d'huile sous pression en son centre[1]. Un câble 132 kV est expérimenté en 1926, aux États-Unis, puis des essais sont effectués entre 1932 et 1934 pour tenter de réaliser un câble souterrain capable de fonctionner sous une tension d’exploitation de 225 kV. L'isolation de ces câbles est également optimisée, leur taille diminue[1].
Les câbles tripolaires à pression externe de gaz neutre, constitués donc de 3 conducteurs maintenus dans de l'azote, sont développés au début des années 1930 à Cologne. Un résultat similaire est également possible en utilisant de l'huile pour maintenir la pression extérieure[1],[5].
Le polyéthylène est mis au point en 1938 en Angleterre[1]. À partir de la Seconde Guerre mondiale, diverses sortes de caoutchouc synthétique et de polyéthylène sont utilisées pour l'isolation des câbles[6]. Des câbles à 63 kV en polyéthylène basse densité ont été mis en service dans les années 1960[7]. Le polyéthylène haute densité est utilisé 10 ans plus tard, leur température de fonctionnement peut être plus élevée. Les polyéthylènes réticulés sont eux mis au point dans les années 1950[1].
En outre, la première ligne haute tension à courant continu a été construite en 1954 à Gotland et a utilisé un câble électrique pour relier l'île au continent[8].
Dans les années 1990, un câble en polyéthylène à faible densité d'une tension de 500 kV a été utilisé avec succès en France[7]. Depuis leur fort développement dans les années 1970, les câbles XLPE se sont imposés dans quasiment toutes les applications. Ils ont été utilisés pour la première fois de manière sous-marine en 1973[9]. À l'exception des câbles HVDC, en 2010, quasiment uniquement des câbles de ce type sont posés[10],[11].
Les câbles XLPE sont appelés à atteindre des tensions supérieures dans un futur proche, tout en étant capables de supporter les inversions de polarité des stations HVDC-LCC.
Des conducteurs supraconducteurs à haute température, en YBCO par exemple, sont en développement[7]. Ceux-ci pourraient permettre de faire transiter des courants élevés de manière compacte et avec peu de pertes. Leurs caractéristiques rendent par ailleurs l'usage de très hautes tensions facultatif, pour transporter 1 000 MW une ligne en supraconducteur de 66 kV suffit alors que pour un câble classique il faut 275 kV, un transformateur peut ainsi être économisé. Un dernier avantage est qu'en cas de court-circuit, le courant devenant très grand, le matériau supraconducteur perd son état supraconducteur et limite ainsi le courant. En 2002, un travail important de développement restait toutefois encore à réaliser concernant les matériaux, l'assemblage des câbles, le refroidissement sur de longues distances[12].
En 2011, le National Institute of Standards and Technology annonce avoir découvert comment réaliser des câbles supraconducteurs 10 fois plus fins qu'auparavant mais pouvant conduire le même courant[13].
Début 2012 Nexans annonce que les câbles supraconducteurs sont prêts à entrer en phase commerciale[14]. HTS Triax, filiale de Nkt cables, a également réalisé plusieurs projets en supraconducteur, avec notamment une station inaugurée en 2006 à Columbus dans l'Ohio[15].
Construction
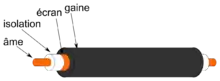
Les câbles à haute tension sont constitués comme ceux basse tension de trois parties principales : conducteur, isolation et gaine de protection. Mais à la différence des câbles basse tension, une couche supplémentaire est ajoutée pour que le champ électrique soit homogène autour du conducteur[2].
Âme conductrice
L'âme conductrice ou conducteur, est faite soit de cuivre soit d'aluminium[16]. Sa principale caractéristique est son ampacité et sa résistance. Le cuivre ayant une meilleure conductivité électrique, ces deux paramètres sont meilleurs avec le cuivre qu’avec l'aluminium. La section peut ainsi être réduite et les autres éléments constitutifs du câble économisés. Toutefois ce dernier permet d'obtenir des câbles plus légers[2]. La majorité des câbles sous-marins actuels ont un conducteur en cuivre[17]. Pour les câbles à papier imprégné de masse, la section atteint les 2 500 mm2 pour ceux à huile 3 000 mm2[18],[19].
Elles sont de différents types [20] :
- simple, pour des sections allant jusqu'à 400 mm2 ; cette section limite son usage pratique à des tensions d'environ 150 kV. L'avantage est que sa construction est aisée. Il peut être rond ou ovale[21] ;
- segmenté : le conducteur est divisé en plusieurs segments ;
- tressé et compressé : plusieurs conducteurs cylindriques sont torsadés ensemble. Un facteur de remplissage d'environ 92 % peut être atteint, et les conducteurs peuvent être isolés entre eux électriquement pour limiter l'effet de peau ;
- profilé ou compact : le profilage permet de gagner en facteur de remplissage, lequel peut atteindre 96 % ;
- creux : des conducteurs creux sont utilisés afin de permettre la circulation d'huile dans certains câbles. Une spirale centrale peut être construite pour éviter que les conducteurs ne se retrouvent dans le centre du canal.
Enveloppe isolante ou isolation
L'isolation a pour rôle de séparer électriquement 2 surfaces aux potentiels très différents : le conducteur d'une part et la terre de l'autre. L'isolation idéale a une haute résistivité (qui détermine le courant de fuite), une haute propriété diélectrique, coefficient thermique faible, une faible absorption de l'humidité, faible permittivité (qui détermine la capacité du câble), est ininflammable, stable chimiquement, a une haute résistance mécanique, haute viscosité à la température d'imprégnation, haute tension de rupture et plasticité[22]. En outre elle doit être régulière, sans impureté, résistante au temps et à la température résultant de l'échauffement du conducteur[7]. Enfin les pertes diélectriques dues à la polarisation dans les polymères et aux mouvements des charges doivent être faibles. Le facteur de dissipation, ou de perte, noté représente le rapport du courant de fuite résistif sur le courant de fuite capacitif et doit être faible[2].
Pour les basses tensions, des isolations au caoutchouc naturel, vulcanisé, gutta-percha, PVC peuvent être utilisés mais leurs propriétés sont trop limitées pour la haute tension[22]. Pour les câbles d'une tension supérieure à 10 kV les isolations suivantes sont utilisées en pratique:
- papier imprégné d'huile ;
- polyéthylène à faible densité (abrégé LDPE en anglais) ;
- polyéthylène à haute densité ;
- polyéthylène réticulé (abrégé XLPE en anglais).
L'éthylène-propylène (EPR) peut aussi être utilisé, mais il a de fortes pertes diélectriques et des propriétés diélectriques généralement moins bonnes que celle du XLPE[23],[24].
L'isolation à papier imprégné est constituée de nombreuses fines bandes de papier basse densité enroulées en couches autour du conducteur. Plus la contrainte électrique est forte plus les bandes doivent être fines. La pâte à papier choisie a peu d'impureté et de longues fibres. Il est fabriqué en suivant le procédé Kraft. Une grande densité est un avantage pour les propriétés diélectriques, mais un défaut pour la permittivité et le facteur de pertes[25]. Elles sont ensuite imprégnées d'huile minérale ou depuis les années 1980 d'alkylbenzène linéraire[26]. Ce dernier a l'avantage d'être stable chimiquement, notamment en présence d'oxygène. Il a également de bonnes propriétés diélectriques, une faible permittivité, une faible viscosité et absorbe l'hydrogène[25]. Il est donc devenu standard[27]. L'isolation à papier imprégné est très sensible à l'humidité, des cavités se forment également avec le temps si le papier n'est pas maintenu sous pression[10]. Il est nécessaire de la sécher sous vide[2]. Par ailleurs, l'huile peut prendre feu ce qui est un problème important dans les tunnels[23]. Les isolations à papier imprégné atteignent des valeurs d'isolation d'environ 15 kV/mm en courant alternatif[25]. Une amélioration possible de l'isolation papier, consiste à placer une couche de polypropylene entre deux couches de papier. On parle de « paper polypropylene laminate » (PPL). Cette technologie améliore l'isolation diélectrique[28].
Le polyéthylène a le défaut de ne pas supporter une température pour le conducteur supérieur à 70-80 °C sous peine de fondre. Le polyéthylène réticulé, qui a une structure cristalline, a un meilleur comportement thermique et peut accepter 90 °C en régime permanent et au-delà de 200 °C pendant un court-circuit (quelques secondes donc)[9]. Il a une résistance diélectrique d'environ 15 kV/mm[25].
Matériau | Température nominale maximale (°C) | Température de court-circuit maximale (°C) |
---|---|---|
LDPE | 70 | 125 |
XLPE | 90 | 250 |
EPR | 90 | 250 |
Papier imprégné de masse | 50-55 | |
Papier imprégné d'huile, refroidi par huile | 85-90 | |
Papier imprégné d'huile, refroidi par gaz[27] | 65-85 |
Écrans semi-conducteurs
Un écran semi-conducteur est placé[29] entre le conducteur et l'isolation d'une part, et entre l'isolation et les couches suivantes d'autre part. Ainsi, les écrans semi-conducteurs sont situés sur les faces interne et externe de l'isolant. Cet ensemble est parfois appelé "Triplex", lorsqu'il est fabriqué par coextrusion. Leur rôle est de rendre le champ électrique homogène autour du conducteur[2], évitant ainsi tout effet de pointe pouvant conduire à des décharges partielles qui pourraient endommager l'isolation[30]. En particulier, il est nécessaire d'éviter la formation de cavités entre le métal (âme, écran) et l'isolant, susceptibles d'être le lieu de fortes hétérogénéités de champ électrique.
Concrètement pour les câbles XLPE, cette couche est réalisée à l'aide d'un mélange semi-conducteur à base de polyéthylène réticulé et de graphite[10], mélange de grande homogénéité et de très faible rugosité. Cette couche a une épaisseur de 1 à 2 mm et son coût est élevé à cause du prix de cette matière première[31].
Pour les câbles isolés avec du papier imprégné, cette couche est réalisée grâce à du papier graphite ou à une couche de cuivre[10]. Elle porte le nom de couche Hochstadter[32].
Écran métallique
Le conducteur extérieur est mis à la terre et sert à évacuer les courants de fuites et de court-circuit[16]. Il a également la fonction de protéger le câble contre les infiltrations d'eau[33]. Il rend enfin quasi nul le champ électrique extérieur[34].
La manière dont l'écran est mis à la terre est importante pour la détermination du courant maximum que peut conduire le câble. Idéalement, le schéma de mise à la terre permet de limiter le courant circulant (source d'échauffement, il réduit la capacité de transit du câble) et les montées de tension induite en tout point de la liaison, en situation opérationnelle. En pratique, il existe trois possibilités :
- Mise à la terre à une extrémité du câble[anglais 1]
- Mise à la terre aux deux extrémités du câble[anglais 2]
- Mise à la terre transposée : cross-bonding
Dans le premier cas, comme l'écran n'est relié à la terre qu'en un seul point, aucun courant ne peut y circuler. Il n'y a donc pas de pertes par courants de Foucault. Par contre, la tension à l'extrémité non mise à la terre peut devenir élevée. Il est possible de la limiter à l'aide d'un parafoudre. Toutefois, le dimensionnement de l'isolation extérieure doit prendre en compte cette haute tension. Dans le second cas, un courant important peut être induit dans l'écran par l'âme et causer des pertes élevées. Par contre, la tension est nulle. La dernière solution consiste à transposer à intervalle régulier les écrans de chaque phase. Si chaque section occupe un tiers de la longueur totale du câble, et si le système triphasé est équilibré, les courants induits s'annulent (). La tension est limitée par des parafoudres à chaque transposition. Si le système triphasé est déséquilibré, il y a présence d'une composante homopolaire. L'impédance homopolaire d'un câble mis à la terre à une seule extrémité est infinie, celles d'un câble mise à la terre aux deux extrémités et mise à la terre transposée sont identiques[35].
- Écran mis à la une seule extrémité du câble. La tension à l'autre extrémité n'est pas limitée.
- Écran mis à la terre aux deux extrémités. Le courant induit par l'âme dans l'écran circule par la terre.
- Écrans transposés. Le courant induit par chacune des âmes dans les écrans se compensent et s'annulent.
Quatre possibilités existent pour construire cet écran : tube en plomb, tube en aluminium, fils de cuivre en hélice ou combinaison cuivre et plomb. Les matériaux se différencient par leur résistivité et leur poids. D'autres sujets comme le prix, la tenue en corrosion ou la raideur peuvent être pris en compte pour ce choix. La résistivité électrique de l'écran doit être suffisamment faible pour limiter l'échauffement lors d'un court-circuit et éviter ainsi la dégradation des matériaux adjacents. Toutefois, plus faible est la résistivité et plus forts seront les courants induits qui limitent la capacité de transit du câble. En comparaison avec les autres métaux, le plomb a une résistance électrique élevée, qui doit être compensée par une plus grande épaisseur. Ses principaux défauts sont d'être cher, lourd et toxique. L'aluminium est léger, relativement économique, n'a pas de problème lié à l'humidité, sa résistivité est faible. La faible résistance électrique du cuivre permet de se contenter de simples fils, plutôt qu'un tube massif, au bénéfice de la légèreté, du prix et de la raideur. L'espacement dégagé permet de faire passer une fibre optique dans certains cas. Enfin la combinaison de plusieurs matériaux peut permettre de cumuler leurs avantages respectifs en distribuant les fonctionnalités attendues de l'écran, mais peut générer des couplages galvaniques. Le couple gaine de plomb et fils de cuivre est identifié comme cher et toxique[34],[5]. Dans le cas des câbles à pression extérieure, la fonction est réalisée par un tube rigide, d'acier[27], de plomb ou d'aluminium.
Gaine de protection extérieure
La gaine ou enveloppe de protection extérieure est une garniture continue et uniforme entourant le conducteur ou l’ensemble de conducteurs et assurant la protection de ces conducteurs contre l’humidité et les détériorations d’origine mécanique ou chimique[16]. Elle protège aussi contre les dommages mécaniques et des pertes d'huile provenant du câble[10],[21]. Elle est faite à base de PVC ou de polyéthylène[36],[37].
Technologies
Câble monophasé et triphasé
.JPG.webp)
Les câbles peuvent être soit monophasés, soit triphasés. Dans le premier cas, un seul conducteur traverse le câble, 3 câbles sont nécessaires pour réaliser le système triphasé usuel dans les réseaux en courant alternatif. Dans le cas des câbles triphasés les trois phases se trouvent dans une seule gaine, 3 conducteurs et enveloppes isolantes sont présentes. La solution en monophasé a l'avantage de nécessiter des câbles de diamètre inférieur, une plus grande longueur par section de câble peut être alors fabriquée. Ils peuvent également transporter plus de courant. Leur rayon de courbure (ou courbure) est réduit, ceci combiné à leur poids plus faible les rend plus facilement installables. Ils sont aussi plus faciles à réparer. La pose d'un câble de secours est également envisageable dans ce cas : un câble supplémentaire en monophasé représente un surcoût de 33 %, alors qu'en triphasé le surcoût est de 100 %. Par contre les câbles monophasés occupent globalement plus d'espace. Leur disposition n'étant pas symétrique il est nécessaire de réaliser des transpositions entre câbles. Enfin le champ magnétique induit par une phase n'est pas annulé par celui des autres phases dans un câble monophasé, cela induit du courant dans l'écran métallique et cause donc des pertes[21].
Câble à papier imprégné de masse
Les câbles à papier imprégné de masse utilisent de l'huile très visqueuse, qui ne s'écoule pas, notamment en cas de dommage ou au niveau des boîtes de jonction. Les câbles de ce type sont en général très vieux. Ils sont limités à la basse et moyenne tension en courant alternatif, la tension maximale étant d'environ 60 kV[21]. Cette technologie est bien adaptée aux grandes profondeurs[18]. Ils contiennent 1 ou 3 conducteurs en courant alternatif. Leur diamètre est d'environ 110 - 140 mm et ils pèsent entre 30 et 60 kg/m[19]. Leur seule application en 2005 est pour les liaisons haute tension en courant continu[38]. En courant continu l'activité dans les cavités et autres défauts apparaissant dans le papier est réduite, cela permet d'employer les câbles à papier imprégné de masse même pour de hautes tensions en courant continu[25]. Le développement de câble XLPE atteignant de plus hautes tensions pourrait les faire disparaître[10],[32]. C'est la technologie employée par la plupart des connexions sous-marines à courant continu actuelles[38].
À pression interne
Afin d'éviter les vides et les décharges partielles et ainsi de pouvoir atteindre des tensions supérieures à celles disponibles avec les câbles à masse, l'huile peut être mise sous pression. Une enveloppe rigide ou semi-rigide en aluminium ou en plomb permet de maintenir cette pression[2]. Un canal d'huile passe au centre du conducteur pour le refroidir et fournir la pression nécessaire à la préservation de l'isolation. Celle-ci est comprise entre 2 et 4 bars[21]. Afin de contenir l'excédent d'huile en cas de dilatation thermique et de maintenir une pression d'huile supérieure à celle exercée par l'eau de mer dans le cas de câble sous-marin, de larges réservoirs de pression sont à prévoir pour l'huile[26]. Leur diamètre est d'environ 110 - 160 mm et ils pèsent entre 40 et 80 kg/m[19].
Ils peuvent atteindre de très hautes tensions[2],[10]. Leur longueur est par contre limitée à environ 30 à 60 km, si aucun réservoir de pression intermédiaire n'est présent, au-delà la bonne circulation de l'huile ne peut plus être garantie[26]. La fabrication des câbles à huile est également relativement compliquée[39].
Ils sont les solutions privilégiées pour les câbles sous-marins avec les XLPE[2]. Ils représentent en 1996, la majorité des câbles dont la tension est supérieure à 150 kV installés[40]. Par contre, ils sont très peu utilisés en courant continu[41]. Standard dans les années 1960, les câbles à papier imprégné sont de moins en moins utilisés, toutefois leur longue durée de vie explique que de nombreux câbles de ce type sont toujours en service à travers le monde[2].
À pression externe
Des pressions encore plus élevées, de l'ordre de 15 bars peuvent être utilisées pour obtenir de meilleures propriétés diélectriques. Elle peut atteindre 60 kV/mm[42]. L'huile est alors choisie très fluide. On place les trois conducteurs dans un tube résistant à la pression. Toutefois cela entraîne de grandes pertes d'huile en cas de fuite. Ces câbles, parfois commercialisés sous la marque oilostatic, étaient relativement répandus aux États-Unis et en URSS, mais peu ailleurs. Ils sont adaptés à la distribution dans les villes dans laquelle leur robustesse est appréciée. Les tubes sont assez onéreux comparés aux gaines métalliques des câbles à pression interne, par ailleurs le fait de mettre les trois phases sans blindage métallique entre elles augmentent les pertes[43],[44],[27].
Câbles à refroidissement forcé
Dans les années 1970 des projets ont tenté d'augmenter les capacités de transport de puissance de câbles électriques, à pression interne ou externe, en les refroidissant au moyen d'eau, d'air ou de vapeur. Un ou plusieurs câbles doivent alors servir de circuit aller les autres de circuit retour[11]
À pression interne
Les câbles à pression interne de gaz fonctionnent sur un principe similaire aux câbles à pression externe d'huile[27]. Le gaz, en fait de l'azote, remplace l'huile pour comprimer l'isolation en papier imprégné, et fait partie intégrante de l'isolation diélectrique[5]. Par rapport à l'huile, le gaz a l'avantage de ne pas être inflammable[34].
D'autres points trouvent moins de consensus ; ainsi, si R. K. Rahkut affirme que les câbles à gaz profitent du fait que la convection du gaz est plus importante que celle de l'huile, ce qui est un avantage pour le refroidissement, M.A. Laughton note que les isolations refroidies à gaz ne peuvent être portées qu'à 65-85 °C alors que celles refroidies à huile peuvent être portées à 90 °C. De même, pour la maintenance, Nexans affirme que le système de maintien de la pression du gaz a besoin de plus de maintenance que celui utilisé pour l'huile, alors que R. K. Rahkut écrit que les câbles au gaz sont utilisés là où la dilatation de l'huile pose problème, ce qui peut sembler contradictoire[22],[34],[27].
À pression externe
La principale différence entre les câbles à gaz pression interne et externe est que dans le second cas une gaine métallique, généralement en plomb, recouvre individuellement chaque ensemble conducteur isolation, alors que pour la pression interne ils sont nus[21]. Les conducteurs sont disposés en triangle et entouré d'une membrane de pression[22]. Ils sont remplis de gaz à une pression d'environ 15 bars[5]. Ce gaz maintient le papier sous pression mais ne fait pas partie de l'isolation diélectrique[21]. Ces câbles requièrent globalement peu de maintenance mais sont onéreux[22].
Câble à isolation gazeuse
Les câbles à pression externe de gaz peuvent utiliser du gaz circulant ou statique. Ils peuvent atteindre les plus hautes tensions[10].
Les câbles à isolation gazeuse sont des conducteurs rigides utilisant un conducteur en aluminium, une isolation gazeuse faite d'un mélange azote - SF6 et une enveloppe métallique externe en aluminium. Leurs capacités vis-à-vis du sol est moindre que pour les autres câbles ce qui limite le besoin en compensation électrique. Ils peuvent atteindre les plus hautes tensions, ce qui est utilisé pour évacuer l'énergie des centrales électriques et ont l'avantage de pouvoir être montés à la verticale. Ceci est mis à profit surtout dans les centrales hydrauliques. Ces systèmes permettent également de faire se croiser plusieurs lignes à haute tension[45],[46],[47].
Câble extrudé à isolation synthétique XLPE
Les câbles à isolation synthétique sont aujourd'hui les plus vendus, en particulier ceux à isolant XLPE. Les premiers câbles à isolation en polyéthylène réticulé, extrudé, notés XLPE[48] avaient la réputation d'être peu fiables à cause de leur propension à former des arborescences électriques en présence d'eau. Les méthodes d'extrusion modernes ont permis de résoudre ce problème. Ses excellentes propriétés diélectriques, sa résistance au vieillissement et sa bonne fiabilité en font une solution de choix pour les applications sous-marines et souterraines[30],[10].
Les conducteurs utilisés pour les XLPE sont souvent compacts[2]. Le diamètre de ces câbles est d'environ 90 - 120 mm et ils pèsent entre 20 et 35 kg/m[19]. Leur résistance mécanique est inférieure à celle des câbles à isolation en papier imprégné[21], car ces derniers sont sensibles au déchirement du papier.
Ils ont l'avantage de ne pas contenir d'huile, le risque de fuite est donc éliminé[21].
Jonctions et extrémités
Jonctions
Connecter deux tronçons d'un câble haute tension nécessite de prolonger chacune des couches qui sont interrompues. Ceci concerne en premier lieu les deux conducteurs qui sont connectés ensemble par un raccord (soudure, raccord vissé, sertissage, poinçonnage profond, contacteur lamellaire). La tricouche isolante est aussi reproduite dans la jonction et se place autour du raccord des conducteurs. Sa forme est étudiée pour répartir de façon la plus régulière le champ électrique et éviter le claquage[49]. Enfin, les écrans métalliques sont raccordés au moyen d'un caisson métallique externe qui peut être interrompu si le mode de mise à la terre de la liaison le nécessite. Ces problèmes ont été résolus par NKF à Delft en 1965[50] grâce à l'introduction d'une boîte de jonction[anglais 3].
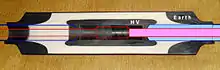
L'image ci-contre montre une photographie de la section d'un tel appareil. Le champ électrique est dévié comme montré dans la seconde image.
Plusieurs types de jonctions existent :
- pré-moulée[anglais 4] ou rubanée[anglais 5]
- en 1 partie ou 3,
- rétractable à froid[anglais 6],[51]avec une rupture entre les écrans ou non.
Jusqu'à 110 kV les jonctions rubanées sont employées, au-delà celles pré-moulées prennent le pas. Dans le premier cas on reconstitue l'enveloppe isolante du câble sur place, cette solution est économique. mais sa qualité de réalisation et donc sa fiabilité dépendent fortement de l'attitude du jointeur la réalisant. La technologie rubanée, bien que délicate à maîtriser et longue à mettre en œuvre, est privilégiée pour les liaisons sous-marines, car elle ne génère que peu de sur-épaisseur. Ceci permet de relier les longueurs produites directement à l'usine avant de les charger sur le navire câblier. Celles pré-moulées consistent en un bloc de plastique formé d'une électrode centrale et deux cônes déflecteurs, séparés par un volume isolant. Celles en 3 parties doivent être assemblée sur place. Les jonctions permettent également de raccorder des câbles de designs différents[34], on parle alors de jonctions de transition.
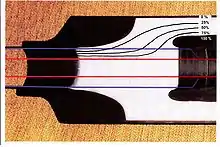
Le montage d'une jonction ou d'une extrémité est une opération délicate. Pour assurer la qualité de la jonction, elle doit être réalisée dans une certaine plage de température extérieure et il faut éviter toute pénétration d’humidité[1]. Il faut couper puis dénuder les câbles à leur extrémité, puis reconstituer les couches une par une. Pour le raccord des âmes, plusieurs méthodes existent : placer un cylindre de cuivre autour des conducteurs et les compresser dessus avec une pince adaptée (raccord serti ou raccord poinçonné), ou en les vissant sur les conducteurs à la manière d'un domino (raccord vissé), ou souder les conducteurs entre eux (raccord soudé). Ensuite l'isolation doit être mise à nu, l'élément déflecteur est ensuite placé autour de cette dernière. Cette opération est complexe et demande du personnel formé[52].
Le taux de défaut des boîtes de jonction sur les câbles sous-marins est plus élevé que celui des autres composants[53].
En 2011, les boîtes de jonction peuvent supporter des tensions pour les câbles XLPE allant jusqu'à 400 kV[53].
Extrémités
En première approche, une extrémité peut être vue comme une demi-jonction. Fonctionnellement, les couches du câble sont interrompues successivement jusqu'à ce que le conducteur soit mis à nu. Si la constitution interne de l'extrémité est une véritable demi-jonction, la mise à nu de chacune des couches successivement jusqu'au conducteur conduit (dans le cas des extrémités aériennes) à libérer le champ électrique dans le milieu externe et nécessite la mise en place d'une enveloppe externe appelée "coiffe". Elle est réalisée en matériau céramique, synthétique ou composite. La coiffe est couverte d'ailettes qui allongent la ligne de fuite en surface de l'extrémité. Ces ailettes évitent la formation d'un arc électrique depuis les anneaux répartiteurs de champ situés au sommet, jusqu'à la base de l'extrémité. Malgré ces ailettes, en première approche la hauteur de l'extrémité reste proportionnelle à la tension du câble qui y est raccordé.
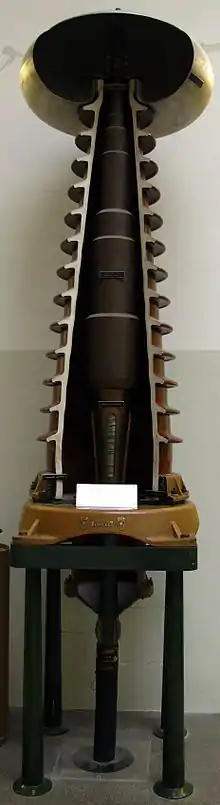
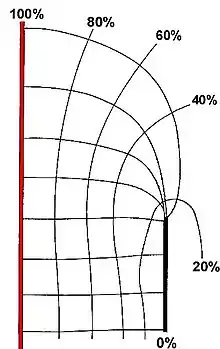
Comme pour les jonctions, la forme de l'électrode déflectrice des extrémités est étudiée pour répartir de façon la plus régulière le champ électrique et éviter le claquage des matériaux (isolant solide ou gazeux).
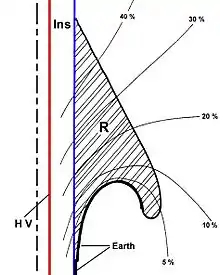
Le bloc déflecteur est généralement constitué du même matériau que la partie isolante du bloc, mais celui-ci est chargé d'additifs réduisant ses propriétés isolantes de façon que l'interface entre les deux forme une électrode, c'est-à-dire une surface équipotentielle de géométrie régulière et en contact intime avec la pièce isolante. Ce principe est illustré ci-contre[54],[10].
Un 1er système a été inventé par NKF à Delft en 1964[55],[56]. Il a été ensuite généralisé par les constructeurs, en particulier pour les équipements sous enveloppes [57].
En 2011, les extrémités peuvent supporter des tensions pour les câbles XLPE allant jusqu'à 500 kV[53].
Applications
Souterrain pour courant alternatif
On parle de haute tension quand la tension est supérieure à 1 kV. Des câbles de 3 et 6 kV existent certes, mais la plupart ont des tensions supérieures à 10 kV[58]. Ceux dont la tension est comprise entre 1 et 50 kV sont couramment appelés HTA, ceux au-delà de 50 kV HTB.
Dans le cas des câbles souterrains, ils sont enterrés à une profondeur d'approximativement 1 à 1,5 mètre[18]. Les éoliennes offshore sont en général reliées par des câbles XLPE d'une tension allant de 10 à 36 kV à une plate-forme qui rehausse la tension, puis depuis cette plateforme reliées au sol grâce à un câble d'une tension supérieure à 100 kV[59].
Intégration dans les réseaux électriques et comparaison avec les lignes aériennes


Les câbles isolés (souterrains et sous-marins) ont une capacité (en µF/km) qui limite le linéaire des liaisons HVAC. À mesure que la liaison s'allonge et que la tension augmente, la part de courant réactif augmente, et réduit le transit de puissance active. Au-delà d'une certaine distance, 60 à 80 km environ pour des liaisons souterraines ou sous-marines, l'importance du courant capacitif rend peu intéressant le transport d'électricité en courant alternatif. Autrement dit la puissance transportée par le câble devient intégralement réactive. Afin de réduire cet effet capacitif, il peut être nécessaire d'installer dans les liaisons classiques en courant alternatif des réactances de compensation, notamment pour le raccordement de parcs éoliens offshore situés à grande distance des côtes. Ce besoin de compensation augmentant avec la tension, les lignes THT sont rarement enterrées. Ainsi pour une ligne 400 kV il faudrait une station de compensation tous les 20 km environ[60],[19],[61].
Une autre solution est d'exploiter la liaison en courant continu, ce qui supprime la question du réactif. En effet - hormis les phases d'inversion de polarité spécifiques aux liaisons exploitées en LCC - en régime permanent le courant étant continu, la capacité parasite du câble ne se charge pas. Toutefois, les liaisons à courant continu nécessitent l'implantation de stations de conversion AC/DC aux deux extrémités, ce qui renchérit significativement la liaison. Pour cette raison, elles sont plus adaptées aux échanges d'énergie point à point qu'aux implantations en réseau maillé. En pratique, cette solution est réservée aux applications suivantes :
- interconnexions entre pays distants ou exploitant des réseaux non-synchrones
- "interconnexions internes" entre régions disposant l'une d'un excédent et l'autre d'un déficit de production
- raccordement de centrales de production lointaines et de forte puissance (parcs éoliens offshore de puissance installée dépassant le MW)
Les lignes souterraines en courant alternatif sont typiquement entre 7 et 20 fois plus chères que les lignes aériennes, cela dépend cependant de nombreux paramètres : par exemple le type de sol. Ce facteur augmente avec le niveau de tension[62]. Les câbles sont donc surtout utilisés en milieu urbain, où la construction de ligne aérienne est difficile. À cause de leur absence d'impact visuel en dehors de leur point d'entrée et de sortie du sol, les câbles sont beaucoup mieux acceptés par la population que les lignes aériennes à haute tension[2]. Ils utilisent également moins de sol et conduisent à moins de dévaluation des biens immobiliers environnants[63]. Ainsi Europacable affirme que pour transporter une puissance de 5 GW il faut au moins un couloir de 50 m de large avec une ligne aérienne alors que 12 suffisent pour des câbles[64]. Pour réduire encore l'empreinte au sol, il est possible de regrouper plusieurs câbles dans un « faisceau », par exemple mettre 2 câbles électriques en parallèle et les associer à une fibre optique[19].
Il est à noter cependant que lors de leur construction les câbles engendrent plus de nuisance que les lignes aériennes, le creusement du tracé étant plus long que la pose de pylônes[2]. Les câbles subissent moins de défaut électrique que les lignes aériennes. Ils ne sont pas touchés par la foudre ou les tempêtes par exemple. Même si on enlève les coupures brèves (en cas de foudre la coupure dure quelques millisecondes), les lignes aériennes ont plus d'interruptions longues. Ceci doit cependant être nuancé par le fait qu'il est difficile de localiser le défaut dans un câble (alors que pour les lignes aériennes, une inspection visuelle suffit la plupart du temps), la réparation est également plus longue, de l'ordre de 3 semaines[2],[64]. La maintenance des câbles est également moindre, il ne faut pas élaguer les arbres à ses environs par exemple, ce qui représente un budget important[2]. Ainsi le budget d'exploitation des câbles HVDC est négligeable[64].
En 1996 le CIGRÉ recensait les statistiques suivantes sur la répartition entre lignes enterrées et lignes aériennes[65],[66],[67] :
Niveau de tension (kV) | Part des lignes enterrées existante (%) | Part des lignes enterrées planifiées et approuvées (%) |
---|---|---|
110-219 | 3,1 | 11 |
220-362 | 0,94 | 1,9 |
363-764 | 0,26 | 0,33 |
Ces chiffres indiquaient que la tendance est certes à plus d'enterrement que par le passé, mais qu'une majorité de lignes restent aériennes. Le rapport de l'assemblée nationale numéro 3477, déclare qu'à l'époque avec 813 km de lignes 225 kV enfouies, la France était en tête en Europe sur ce terrain. La proportion de ligne en 225 et 400 kV est négligeable[60]. La demande publique restant la principale raison d'enterrer les câbles[68].
Câbles sous-marin
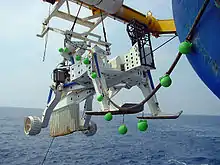
Comme dans le cas des câbles souterrains, la longueur maximale d'un câble électrique alimenté en courant alternatif est d'environ 60 à 80 km, au-delà il est nécessaire d'utiliser de la compensation. Pour cette raison le transport en courant continu est souvent privilégié[61],[19].
La réparation des câbles sous-marins est complexe, il faut localiser le défaut, couper la partie endommagée, mettre un câble de rechange et poser les boîtes de jonction le tout en mer[18],[69].
Le coût des câbles sous-marins dépend de très nombreux facteurs : caractéristiques électriques, longueur, tracé, profondeur, protections à mettre en place… Pour cette raison, il est difficile de donner un ordre d'idée général[18]. Toutefois, on peut dire que dans le cas des liaisons HVDC, le coût des câbles excède en général de plusieurs fois le coût des stations de conversion.
Câble pour courant continu
Si la construction d'un câble pour le transport de courant continu est similaire à celle d'un câble pour courant alternatif certaines différences sont remarquables. La division en diverses parties est identique, par contre la physique contraignant l'isolation est différente, les tests également[70].

Un des problèmes rencontrés par les câbles XLPE en présence de courant continu est l'accumulation de charges à certains endroits de leur isolation qui en limitent les propriétés diélectriques. Un changement de champ les fait migrer créant un courant dans l'isolation générant des pertes joules, chauffant celle-ci. Par ailleurs le champ électrique créé par ces charges peut mener à l'arc électrique. Ainsi les câbles XLPE ont également des difficultés à supporter les inversions de polarité des stations HVDC commutées par les lignes (LCC), ils sont donc réservés aux stations en source de tension (VSC) qui ont une polarité constante[64]. Pour résoudre ces problèmes des charges migrant dans l'isolation, des chercheurs japonais, travaillant pour J-Power et Viscas ont développé un polyéthylène piégeant les charges et ayant une meilleure résistance volumique. La champ est plus régulier dans l'isolation. En 2004, ils avaient annoncé avoir développé un polyéthylène piégeant les charges et ayant une meilleure résistance volumique. La champ est plus régulier dans l'isolation. Un câble électrique pour courant continu avec une tension de 500 kV a été testé avec succès[71]. En 2011, ils annoncent avoir surmonté le problème et pouvoir utiliser un câble XLPE avec une station LCC[72].
En 2012, les câbles XLPE pour HVDC sont limités à des tensions de +/- 320 kV et une puissance par bipôle de 1 000 MW[64]. Pour les très hautes tensions des câbles à papier imprégné de masse restent nécessaires. Les câbles à huile fluide ne sont quasiment pas utilisés pour le HVDC[41]. Ils peuvent atteindre des tensions de +/- 500 kV (ABB commercialise même 550 kV[73]), pour une puissance de 1 600 MW par bipôle ce qui représente une section de conducteur de 2 500 mm2[64]. Leur conception est légèrement différente de celle des câbles à huile en courant alternatif, le fait que les câbles DC ne soient pas sujets aux pertes diélectriques leur permet d'utiliser du papier plus dense[39]. À noter que les câbles XLPE ont besoin d'un plus grand nombre de jonctions pour une même distance que les câbles à papier imprégné de masse[41].
En 2012, la majorité des câbles HVDC sont utilisés pour réaliser des liaisons sous-marines, le courant AC étant inadéquat pour transporter la puissance sur des distances supérieures à environ 80 km. Les câbles HVDC ne rencontrent pas de problème avec la distance, ainsi le plus long câble sous-marin en 2012 est celui du projet NorNed, reliant la Norvège aux Pays-Bas, qui a une longueur de 580 km et transporte 700 MW[38]. Parmi les applications de la haute tension à courant continu conjointement à des câbles électriques, on trouve les plateformes offshore reliant les fermes éoliennes éloignées du sol, à l'heure actuelle présentes avant tout en mer du Nord[18].
Pour les lignes HVDC, Europacable parle d'un coût allant de 1 à 2,5 millions d'euros par kilomètre pour les lignes enterrées, soit 2 à 3 fois plus cher qu'en ligne aérienne[64].
Câbles pour matériel radiographique
Les câbles haute tension destinés à connecter les tubes à rayons X[anglais 7] des équipements de radiographie sont assez différents de ceux utilisés pour le transport de puissance. Ils sont parcourus par un courant relativement faible : quelques milliampères à une tension de 30 à 200 kV. Ils sont flexibles, isolés grâce à du caoutchouc ou de l'élastomère, leur conducteur est tressé et dispose d'une gaine en fils de cuivre [74].
Mise en place
Pour l'installation de câbles souterrains, il existe trois options:
- en tunnel[75]
- en fourreaux avec disposition en trèfle[75]
- en fourreaux avec les câbles simplement déroulés sur une surface plane, en nappe[75]
Quand le câble est directement enfoui, une tranchée est creusée, le câble installé sur une semelle dure et ensuite couvert d'un sable spécial à basse résistance thermique (ou de ciment maigre) puis la tranchée est rebouchée[64],[75] . Cette solution est plus économique que la construction d'un tunnel. Par contre dans ce dernier cas, la section des câbles est moins importante et on envisage de passer le câble dans un tuyau rigide[34]. La longueur des sections de câbles est limitée par le transport des bobines. Typiquement ces sections excédent le kilomètre, les bobines pèsent jusqu'à 40 tonnes[64]. RTE parle d'une distance entre jonctions allant de 500 m à 1 km[75].
L'installation des câbles sous-marins est quelque peu différente, des navires spéciaux, comme le Giulio Verne, transportent et installent le câble. Ils peuvent transporter environ 100 km de câble standard à la fois. Pour le projet Cometa, entre l'Espagne et Majorque, le câble étant plus fin il a pu être posé en un seul tenant de 242 km de long. Si le courant marin est important ou que l'on veut placer le câble avec précision, un robot est utilisé au fond de la mer pour mettre le câble en place. Il creuse une tranchée afin de protéger le câble contre les dommages potentiels, provenant des ancres des navires ou des équipements de pêche par exemple. Pour les très grandes profondeurs, ces risques n'existant pas, l'enfouissement n'est pas nécessaire. Il existe plusieurs méthodes pour ouvrir la tranchée : pelleteuse, à chaîne, « jetting »[18]… Afin d'améliorer encore la protection du câble, un matelas fait de sacs de ciment ou sable peut être placé sur son tracé. Il peut aussi être tubé[19]. Il est à noter, que lors de la mise en place du câble celui-ci "pend" au bateau, au plus la profondeur est importante, au plus la contrainte mécanique exercée sur le câble est forte. Une solution consiste à utiliser une gaine en acier pour obtenir de bonnes propriétés mécaniques, une autre consiste à utiliser une gaine en aluminium pour alléger le câble.
Fabrication, qualité, test et diagnostics
Fabrication
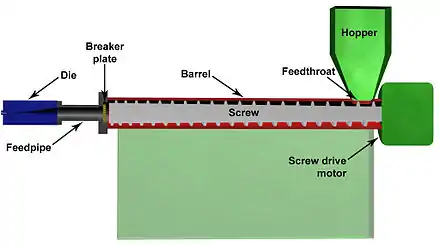
La coopération entre les fabricants de câble et de matériaux a permis de définir différents types d'XLPE aux spécifications très strictes. Les producteurs exigent en général un polymère « extra clean », ce qui garantit que le nombre et la taille des particules restent faible. Le stockage de la matière première dans un environnement parfaitement propre, salle blanche, est nécessaire pour le producteur de câble. Le développement des extrudeuses pour les plastiques réticulées a permis d'obtenir une extrusion sans défaut des câbles.
Elles peuvent être de trois sortes différentes : à vulcanisation continue verticale, VCV [anglais 8], à vulcanisation continue en caténaire, CCV [anglais 9] ou à vulcanisation continue dite Mitsubishi Dainichi, MDVC[anglais 10]. Dans le premier cas le câble est vertical, dans le second il forme une caténaire et dans le dernier est horizontal lors de son extrusion[23].
Qualité
Le développement de l'isolation haute tension est limité par deux problèmes relatifs à la qualité. Tout d'abord les couches de semi-conducteur doivent être parfaitement homogènes, sans aucune saillie, même de quelques microns. De même l'isolation et ces couches doivent être parfaitement en contact : les fissures, poches d'air et autres défauts, de l'ordre du micron, peuvent diminuer les propriétés diélectriques du câble[76].
Ensuite, l'isolation en elle-même ne doit pas contenir de particules extérieures, de cavité ou d'autres défauts. Les imperfections suivantes peuvent se manifester dans l'isolation d'un câble[77] :
- Arborescence électrique
- Vide à l’interface
- Vide dans l’isolant
- Contaminant
- Protubérance dans le semi-conducteur
- Décharge à partir d’un contaminant
- Décharge à partir d’un vide
- Décharge à partir de l’isolant
- Décharge à partir du conducteur
- Humidité
Tout défaut réduit la durée de vie du câble qui est normalement d'environ 30 ans ou plus[78].
Fiabilité
Au niveau de la fiabilité, les câbles électriques à haute tension ont les statistiques suivantes en fonction de l'isolation choisie[25] :
Composant | Unité | Isolation papier | XLPE |
---|---|---|---|
Câble | défaut/100 unités/km/an | 0,05 | 0,05 - 0,07 |
Jonction | défaut/100 unités/an | 0,08 | 0,01 |
Extrémité | défaut/100 unités/an | 0,07 | 0,04 |
Tests et diagnostics
Inéluctablement, l’isolant agencé autour du conducteur d’un câble vieillit et se dégrade au cours du temps. Les câbles doivent donc faire l’objet d’un diagnostic régulier ayant pour principale mission de vérifier la qualité de leur isolation. Dans le cas des câbles à isolation en papier ces diagnostics déterminent le vieillissement général, dans le cas des XLPE les arbres électriques sont plus particulièrement recherchés[10]. Les diagnostics permettent de connaître l'état de vieillissement du câble et de planifier les maintenances nécessaires[79].
Les câbles peuvent présenter différents types de défauts. Différentes méthodes de tests et de diagnostics sont donc utilisées pour valider la conformité des câbles : mesure des décharges partielles, du facteur de perte. Les câbles doivent être exempts de décharge partielle, signe d'une détérioration de l'isolation[10].
Le comportement très capacitif des câbles empêche de faire ces tests à la fréquence nominale du réseau, une puissance bien trop importante serait alors exigée du réseau. Des tests en courant continu ont donc été développées pour les câbles à isolation en papier imprégné. Toutefois dans le cas des câbles XLPE, elles se sont révélées très peu sensibles. On peut alors augmenter la tension mais cela peut endommager le câble. Cette méthode n'est utile que pour tester la gaine métallique. Des méthodes à faibles fréquences (dite méthode VLF) pour mesurer les décharges partielles sont donc utilisées. Les fréquences utilisées sont comprises entre 0,01 et 0,1 Hz[10].
D'autres méthodes existent comme celle à une fréquence comprise entre la 50 Hz on-line, c'est-à-dire que le câble n'est pas déconnecté du réseau à la différence de la méthode 50 Hz off-line, et enfin la méthode « Damped AC voltages energizing » abrégé OWTS[80]. Si le câble n'est pas déconnecté, il faut plus de traitement du signal pour distinguer les décharges partielles du bruit. Une des difficultés est de localiser le défaut dans le câble[81].
L'usage haute fréquence est meilleur pour distinguer le bruit blanc du signal, le premier diminuant quand la fréquence augmente. Des fréquences de 100 MHz sont typiquement utilisées Les signaux sont mesurés au moyen de capteurs inductifs ou capacitifs[82].
Les arborescences d'eau peuvent être détectées par la mesure du facteur de perte du câble, la ou par une mesure de décharges partielles[83],[84]. Les valeurs mesurées lors des diagnostics doivent être comparées à celles acquises lors des tests en usine, cela permet notamment de détecter des erreurs de montage[10].
Les méthodes acoustiques et ultra-soniques de détection des décharges partielles peuvent également être employées[85].
Conséquences environnementales
Les câbles à huile ont le défaut de rejeter de l'huile dans la nature en cas de fuite[39]. Ils ont très peu d'impact visuel. Les inquiétudes se concentrent davantage sur le champ électrique[68]. Leur occupation des sols est plus limitée que celle des lignes aériennes[63].
Fabricants
Liste de fabricants de câbles haute tension[86] :
- ABB, groupe suèdo-suisse.
- Borealis, groupe norvégo-finlandais
- Condumex, groupe mexicain
- Furukawa, groupe japonais
- J-Power Systems, groupe japonais issu de Hitachi câble notamment.
- JDR Cables, groupe britannique
- LS Cable & System, groupe coréen issu du LG Group
- Nexans, groupe français
- nkt Cables, groupe danois
- NSW, groupe allemand
- Prysmian, ex Pirelli[87]
- Solidal, groupe portugais
- Southwire, groupe américain
- Sumitomo, groupe japonais
- Viscas, groupe japonais
- ZTT, groupe étatique chinois[88]
Pour les accessoires tels que les boîtes de jonction d'autres fabricants s'ajoutent tel Pfisterer[89].
Normes applicables
- CEI 60141 - Essais de câbles à huile fluide, à pression de gaz et de leurs dispositifs accessoires - version 1993
- CEI 60502-2 Câbles d'énergie à isolant extrudé et leurs accessoires pour des tensions assignées de 1 kV (Um = 1,2 kV) à 30 kV (Um = 36 kV) – Partie 2: Câbles de tensions assignées de 6 kV(Um = 7,2 kV) à 30 kV (Um = 36 kV)
- CEI 60840 - Câbles d'énergie à isolation extrudée et leurs accessoires pour des tensions assignées supérieures à 30 kV (Um = 36 kV) et jusqu'à 150 kV (Um = 170 kV) – Méthodes et exigences d'essai - version 2011
- CEI 62067 - Câbles d'énergie à isolation extrudée et leurs accessoires pour des tensions assignées supérieures à 150 kV (Um = 170 kV) et jusqu'à 500 kV (Um = 550 kV) – Méthodes et exigences d'essai - version 2011
Références
- « 100 ans de haute tension à Paris » (consulté le )
- (en) Houssem Rafik et El- Hana Bouchekara, Transmission and Distribution of Electrical Power, (lire en ligne)
- (en) Underground Systems Reference Book, New York, Edison Electric Institute,
- Kreuger 1991, p. figure 10.7
- (de) « Catalogue nkt » (consulté le )
- (en) R. M. Black, The History of Electric Wires and Cables, Londres, Peter Pergrinus, , 290 p. (ISBN 0-86341-001-4)
- Worzyk 2009, p. 17
- Worzyk 2009, p. 1
- Worzyk 2009, p. 18
- Kuechler 2005, p. 427-435
- « présentation transport énergie électrique à jicable » (consulté le )
- (en) Groupe de travail 38.01.11, Superconducting cablesimpact on network structure and control, Cigré, coll. « Brochure », , chap. 199
- (en) « Super-thin Superconducting Cables » (consulté le )
- Thierry Lucas, « Les câbles supraconducteurs sont prêts à entrer en phase commerciale », L'usine nouvelle, (lire en ligne, consulté le )
- (en) « Projet à Columbus » [archive du ], sur HTS Triax (consulté le )
- « Sécurité des câbles électriques », sur Élia (consulté le )
- Worzyk 2009, p. 10
- (en) « An Introduction to High Voltage Direct Current (HVDC) Subsea Cables Systems » (consulté le )
- « présentation câble HVDC » [archive du ] (consulté le )
- Worzyk 2009, p. 11
- (de) Wilfried Knies et Klaus Schierack, Elektrische Anlagentechnik, Hanser, , 463 p. (ISBN 978-3-446-40574-5 et 3-446-40574-7, lire en ligne)
- (en) R. K. Rajkut, Utilisation of Electrical Power, New Delhi, LAXMI Publication, (lire en ligne)
- (en) A. Haddad et D. Warne, Advances in high voltage engineering, Londres, IET power and energy series, , 647 p. (ISBN 978-0-85296-158-2, lire en ligne)
- Worzyk 2009, p. 23
- (en) Hugh M. Ryan, High voltage engineering and testing, Londres, The institution of electrical engineers, (ISBN 0-85296-775-6, lire en ligne)
- Worzyk 2009, p. 24
- (en) M. A. Laughton et D. F. Warne, Electrical Engineer's Reference Book, Oxford, Elsevier Science, (ISBN 0-7506-4637-3, lire en ligne)
- (en) Gianluigi Migliavacca, Advanced Technologies for Future Transmission Grids, Springer (lire en ligne), p. 64
- see [3] and Kreuger 1992, p. 118
- Worzyk 2009, p. 19
- Worzyk 2009, p. 20
- Worzyk 2009, p. 27
- Worzyk 2009, p. 30
- (en) « Brochure Nexans » (consulté le )
- (en) O.E. Gouda et Adel Farag, « Bonding methods of underground cables », sur Researchgate (consulté le )
- CEI 60840, version 2011, clause 4.4
- (en) Ravindra arora et Wolfgang Mosxh, High voltage and electrical insulation engineering, John Wiley and sons, , 352 p. (ISBN 978-0-470-60961-3, lire en ligne)
- (en) « THE NORNED HVDC CABLE LINK A power transmission highway between Norway and the Netherlands », sur ABB (consulté le )
- Worzyk 2009, p. 26
- Cigré 110 1996, p. 11
- (en) Gianluigi Migliavacca, Advanced technologies for future transmission grids, Londres, Springer, , 400 p. (ISBN 978-1-4471-4548-6, lire en ligne)
- (de) Joseph Kindersberger, Isoliertechnik, TU Munich, 2010/2011, p. 280
- (de) Elektrische Kraftwerke und Netze, Springer, (lire en ligne)
- (en) « Overhead lines and underground cables » (consulté le )
- (en) « Alstom, GIL » (consulté le )
- (en) « When cables don't » (consulté le )
- « rapport 2008 sur la liaison France-Espagne » [archive du ] (consulté le )
- « Cross linked polyethylene »
- Kreuger 1991, p. 156
- Dutch Patent 149955 of Netherlands Cable Works NKF, submitted 4-11-1965, granted 17-11-1976
- Cigré 476 2011, p. 40-44
- Cigré 476 2011, p. 10-40
- Cigré 476 2011, p. 4
- Kreuger 1991, p. 147-153
- Dutch Patent 123795, Netherlands Cable Works NKF, submitted 21-4-1964, granted 27-3-1968
- cas similaire dans Kreuger 1991, p. 160
- Cas similaire dans Kreuger 1991, p. 157
- Kreuger 1991, p. 133-137
- Worzyk 2009, p. 4
- « Rapport numéro 3477, du 9 décembre 2001, sur L'APPORT DE NOUVELLES TECHNOLOGIES DANS L'ENFOUISSEMENT DES LIGNES ÉLECTRIQUES À HAUTE ET TRÈS HAUTE TENSION, », sur Assemblée nationale (consulté le )
- (en) M. P. Bahrman, HVDC Transmission Overview, IEEE, (lire en ligne)
- Cigré 110 1996, p. 12
- Cigré 110 1996, p. 14
- (en) « An Introduction to High Voltage Direct Current (HVDC) Underground Cables » (consulté le )
- Cigré 110 1996, p. 9
- Autres chiffres dans « présentation transport énergie électrique à jicable » (consulté le )
- D'autres chiffres sont disponibles dans « rapport 2008 sur la liaison France-Espagne » [archive du ] (consulté le )
- Cigré 110 1996, p. 10
- (en) « HVDC Submarine Power Cables in the World », sur JRC (consulté le )
- Kreuger 1992, p. 15-19
- (en) « Development of a 500-kV DC XLPE Cable System », Furukawa Review, no 25, (lire en ligne, consulté le )
- (en) HVDC XLPE cable systems applicable for higher temperature and polarity reversal operation, Versailles, Jicable, (lire en ligne)
- (en) « Site d'ABB sur les câbles HVDC » (consulté le )
- Kreuger 1991, p. 65, 133
- « Rapport du CESI (Centro Elettrotecnico Sperimentale Italiano)] n°B4023551, 74 pages, commande RTE n. 4500547131 / R0DI, rapport demandé par la Préfecture du Nord - Bureau de l'environnement dans le cadre du projet de reconstruction de la ligne 400 kV Avelin-Gavrelle : Réponses aux questions posées durant la phase de concertation » (consulté le )
- Kreuger 1992, p. figure 8.1e
- Lebas 2008, p. 7
- Kreuger 1992, p. 87-91
- Lebas 2008, p. 1
- Lebas 2008, p. 27
- Lebas 2008, p. 33
- (en) On-line monitoring of MV and HV distribution cables using VHF partial discharge detection, Paris, Cigré, , « D1-202 »
- (en)« Explication de la mesure du facteur de perte pour diagnostiquer les câbles » (consulté le )
- (en)« Explication de la mesure des décharges partielles pour diagnostiquer les câbles » (consulté le )
- (en) Groupe de travail D1.33, Guidelines for Unconventional Partial Discharge Measurements, Cigré, coll. « brochure », , chap. 444
- (en) « Étude sur le marché des câbles haute tension » [archive du ], sur pikeresearch (consulté le )
- « Histoire de Prysmian » (consulté le )
- (en) « Présentation de ZTT » (consulté le )
- « Pfisterer » (consulté le )
Articles connexes
Traductions
- single point bonding
- Bonded at two-points ou Solid Bonding
- « bi-manchet »
- « premoulded »
- « tapped »
- « Slip on » ou non,
- « slip over »
- « X-ray cable »
- « vertically continuous vulcanisation »
- « catenary continuous vulcanisation »
- « Mitsubishi Dainichi continuous vulcanisation »
Bibliographie
- (en) F.H. Kreuger, Industrial High Voltage, t. 1, Delft University Press, , 180 p. (ISBN 90-6275-561-5)
- (en) F.H. Kreuger, Industrial High Voltage, t. 2, Delft University Press, , 167 p. (ISBN 90-6275-562-3)
- (en) E. Kuffel et W.S. Zaengl, High Voltage Engineering, Oxford, Pergamon Press, (ISBN 0-7506-3634-3)
- (en) Houssem Rafik et El- Hana Bouchekara, Transmission and Distribution of Electrical Power, (lire en ligne)
- (en) Thomas Worzyk, Submarine power cables, Dordrecht, Springer, (ISBN 978-3-642-01269-3, lire en ligne)
- (en) Groupe de travail 21/22.01, Comparison of high voltage overhead lines and underground cables, Cigré, coll. « brochure », , chap. 110
- (en) Groupe de travail B1.22, Cable Accessory Workmanship on Extruded High Voltage Cables, Cigré, coll. « brochure », , chap. 476
- Pierre Lebas, Diagnostic des câbles souterrains par détection de décharges partielles, Université de Liège, (lire en ligne)
- (de) Andreas Kuechler, Hochspannungstechnik, Grundlagen, Technologie, Anwendungen, Berlin, Springer, , 543 p. (ISBN 3-540-21411-9, lire en ligne), p. 224-232 et 376-389
- Portail de l’énergie
- Portail de l’électricité et de l’électronique