Convertisseur Peirce-Smith
Le convertisseur de Peirce-Smith est utilisé pour le procédé industriel d'affinage des mattes de cuivre et de nickel. Il est inventé en 1910 par les Américains William H. Peirce et Elias Anton Cappelen Smith à la Baltimore Copper Company's Smelter, dans l'Utah, aux États-Unis.
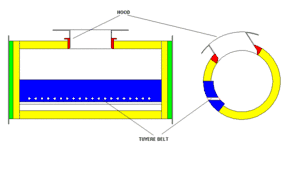
Il s'agit d'un convertisseur Manhès-David dont le revêtement réfractaire interne est basique au lieu d'être acide. Quoiqu'il ne change pas fondamentalement le principe du procédé Manhès-David, il représente une amélioration notable, en résolvant définitivement le problème de l'usure des réfractaires.
En 2010, avec 250 unités opérationnelles dans le monde, les convertisseurs Peirce-Smith assurent, 90 % de l'affinage des mattes cuivreuses. 60 % du nickel produit dans le monde est également affiné par ce type de convertisseur.
Historique
Contexte technique
Au début du XXe siècle, le convertisseur Manhès-David est révêtu d'un réfractaire siliceux, donc acide. Un convertisseur d'une capacité de 7 tonnes utilise 16 tonnes de réfractaire acide qui durent de 6 à 9 soufflages[L 1]. Ce réfractaire est consommé par les scories dans lesquelles il joue le rôle de fondant[1]. Un réfractaire basique, inspiré de celui mis au point par Sidney Thomas et Percy Gilchrist en 1877[2], avait bien été suggéré par John M. Hollway, précurseur de Pierre Manhès et Paul David, lors de ses essais au début des années 1800[L 2]. L'idée n'avait cependant pas été testée, des problèmes fondamentaux liés au soufflage étant alors plus prioritaires que l'optimisation du réfractaire[3].
L'évolution du procédé calque l'évolution de la métallurgie du fer : le convertisseur Thomas, inventé en 1877, est un convertisseur Bessemer doté d'un revêtement réfractaire basique. Mais, alors que dans le convertisseur Thomas, le réfractaire basique permet d'obtenir des réactions chimiques sensiblement différentes de celles obtenues dans un convertisseur Bessemer, il est uniquement question, dans la métallurgie du cuivre, de disposer d'un réfractaire qui ne réagisse pas avec les scories.
Intérêt et handicaps des réfractaires basiques
Un réfractaire basique ne réagissant pas avec les scories, il faut trouver un autre moyen d'apporter la silice issue du réfractaire acide, qui est indispensable au procédé. L'injection de poudre siliceuse dans le vent soufflé dans le convertisseur, déjà proposée par Manhès dès 1883 dans son brevet relatif au convertisseur cylindrique[4], échoue notamment car il faut toujours avoir de la silice en excès pour éviter la transformation de l'oxyde de fer(II) (FeO) en tétroxyde de trifer (Fe3O4)[note 1], beaucoup moins fusible[5].
Enfin, outre leur coût, les réfractaires basiques sont plus fragiles, et surtout se dilatent et dissipent plus la chaleur que les réfractaires acides[L 3].
Premiers essais d'un réfractaire basique dans un convertisseur Manhès-David
En 1888, Claude Vautin essaie un réfractaire basique à Cobar, en Australie, mais abandonne très vite[H 2]. En 1890, un revêtement réfractaire basique est essayé sur un des convertisseurs Manhès-David de Parrot Smelter, à Butte, sous la direction de Herman A. Keller. . Les essais ne débouchent pas sur un revêtement compatible avec une marche industrielle[L 4]. D'autres brefs essais sont aussi entrepris dans des usines américaines sans plus de succès[H 2].
En 1900, Ralph M. Baggaley, de Pittsburgh, commence des essais similaires. Il a analysé les échecs de John Hollway et, contrairement à d'autres, il en déduit qu'un revêtement basique est tout à fait possible. Il entre au capital de la Pittsburg and Montana Mining Company qui possède l'usine de Pittsmont Smelter[note 2]. Là, secondé de William A. Haywood, il parvient à faire durer un réfractaire basique du 7 octobre 1905 au 31 janvier 1906, alors qu'un revêtement acide ne dure guère plus qu'une journée. Il interrompt immédiatement ses recherches lorsque son fils décède brutalement le 12 février 1906, allant jusqu'à refuser une offre des Guggenheim, qui souhaitent moderniser leurs 16 usines. Les réfractaires basiques sont alors momentanément abandonnés : le fort tempérament de Baggaley[5] et les doutes sur la rentabilité du nouveau revêtement, beaucoup plus onéreux, amènent à l'abandon de la technique en 1908[L 4].
Pour autant, le norvégien Knudsen, avait aussi réussi dès 1903 à utiliser un revêtement basique à Sulijtelma : il y réalise deux soufflages successifs, dans un petit convertisseur au revêtement basique, qu'il continue dans un deuxième convertisseur classique, au revêtement acide[L 4].
La mise au point du réfractaire par Peirce et Smith
L'année 1906 voit la création du Kennecott Utah Copper rail line en Alaska par Stephen Birch. Aux États-Unis, ce chemin de fer minier à voie unique ouvre le canyon de Bingham, dans le comté de Garfield (Utah), pour le désenclaver. Les ingénieurs W.H. Peirce et A.A. Smith travaillent sur un four d'affinage permettant de mieux rentabiliser le minerai du canyon. Ils s'inspirent aussi des progrès réalisés au Chili par la Société des mines de cuivre de Catemu, qui en 1903 quadruple sa production grâce à d'excellents procédés pyrotechniques de transformation[réf. nécessaire].
En 1905, à la Baltimore Copper Company's Smelter, les américains William H. Peirce et E. A. Cappelen Smith, commencent à mettre au point un revêtement basique à partir de briques de magnésie que, depuis 1897, Smith adapte à d'autres applications[5]. En 1909, ils y démarrent leur premier convertisseur maçonné avec des réfrcataires basiques[6]. Celui-ci fonctionne jusqu'en février 1910. À ce moment une unité semblable démarre dans le comté de Garfield, dans l'Utah, bientôt imitée par d'autres. Des durées de vie de plusieurs mois, voire quelques années, sont fréquentes[5].
Les améliorations de Peirce et Smith touchent à de nombreux points techniques, dont notamment l'adoption de :
- une grande taille pour augmenter l’inertie thermique du convertisseur, qui devient nécessaire car les réfractaires basiques évacuent plus la chaleur[L 5] ;
- des réfractaires plus épais aux endroits sensibles, pour éviter d'échauffement de l'enveloppe métallique, sont préférés aux boîtes à eaux utilisées par Baggaley ;
- des joints de dilatation permettent d'anticiper les mouvements du réfractaire au moment de la mise à feu du convertisseur ;
- des trous de coulée latéraux pour couler les scories sans interrompre le soufflage ;
- des tuyères amovibles[5].
Leur convertisseur s'avère beaucoup plus économique. En 1921, il est alors considéré comme « le principal élément de la réduction des coûts dans la pyrométallurgie des minerais de cuivre[7] ». Dans certains cas, une baisse du coût de la conversion, de 15–20 dollars à 4–5 dollars, a été rapportée[8].
Le réfractaire basique, qui ne réagit pas avec les scories, dure beaucoup plus longtemps. Dès 1921, W. A. Mueller cite une durée de vie record pour un réfractaire de basique de 3 228 soufflages, soit 85 578 tonnes de matte affinées pendant 2 ans et demi[7]. Cette amélioration permet d'éviter la construction d'installations de maçonnage, de s'affranchir des manutentions dues au remplacement des convertisseurs[L 6] (outre le capital requis moindre, le personnel nécessaire est divisé par 2[5]), et de limiter les risques de percées dues à un mauvais contrôle de l'usure du réfractaire[P 1]. La couche de réfractaire peut alors être plus fine, ce qui augmente la capacité du convertisseur. Celle-ci ne dépend pas de l'usure du réfractaire, ce qui simplifie la gestion des flux de métal en fusion dans l'usine[L 7].
- Convertisseur Manhès-David : la quantité de réfractaire est maximisée.
- Convertisseur Peirce-Smith : des jeux de dilatation sont aménagés.
En 1912, aux États-Unis, 80 % de l'affinage du cuivre est réalisé dans des convertisseurs revêtus de réfractaire basique, dont beaucoup ont été conçus pour un réfractaire acide[5]. Dans le milieu des années 1920, le convertisseur basique Peirce-Smith supplante définitivement celui de Manhès et David[9].
Convertisseurs Peirce-Smith modernes
En 2010, une usine moderne dispose de 2 à 5 convertisseurs, d'une capacité unitaire de 100 à 250 tonnes[E 2], transformant chacun 600–1 000 tonnes de mattes en 500–900 tonnes de blister par jour[E 3]. La durée de vie d'un convertisseur Peirce-Smith moderne est de 50 000 à 90 000 tonnes (soit, en 1984, 100 à 200 jours[6]). Le maçonnage dure une semaine. Les réfractaires les plus performants sont les briques en magnésie liée au chrome[E 4]. En 1912, aux États-Unis, 80 % de l'affinage du cuivre est réalisé dans des convertisseurs revêtus de réfractaire basique, alors que beaucoup n'ont pas été conçus à cet effet[5]. En 2010, avec 250 convertisseurs opérationnels dans le monde, les convertisseurs Peirce-Smith assurent 90 % de l'affinage des mattes cuivreuses[E 5].
Acide (Manhès-David) Début du XXe siècle[L 8],[1] |
Basique (Peirce-Smith) Début du XXe siècle[L 1] |
Basique Début du XXIe siècle[E 6],[6] | |
---|---|---|---|
Capacité (tonnes de matte) | 7 (moyenne) | 35 à 45 | 220 |
Nombre de tuyères | 14 | 27 | 60 |
Épaisseur de réfractaire (cm) | 55 à 70 | 25 | 50 |
Durée de vie du réfractaire (tonnes de matte) | 42 à 63 | 2 000 à 3 000 | 60 000 à 90 000 (tuyères uniquement) |
Utilisation dans la pyrométallurgie du nickel

Le nickel peut être extrait à partir de latérites ou de pyrites cuivreuses. Ces dernières sont à l'origine de près de la moitié du nickel extrait. Les procédés d'extraction sont proches de ceux du cuivre, et permettent d'obtenir une matte contenant qutan de cuivre que de nickel[10].
Les mattes de cuivre-nickel sont affinées dans un convertisseur Peirce-Smith. L'affinage commence de la même manière qu'une matte cuivreuse mais, lorsqu'il reste dans la matte moins de 1 à 0,5 % de fer, le nickel commence à s’oxyder énergiquement, aussi vite que le soufre[note 3]. Par ailleurs, l'oxydation du nickel étant peu exothermique, il n'est pas possible de finir le soufflage. On l'interrompt donc au stade de la matte blanche, qui ne contient alors presque plus de fer, mais reste riche en soufre. Elle reste facile à traiter, le retrait du cuivre étant efficace par un grillage, par hydrométallurgie, le procédé Mond, etc.[K 1].
Au début du XXIe siècle, l'efficacité du convertisseur du Peirce-Smith fait qu'il est universellement adopté dans l'affinage de la matte issue des minerais sulfureux de nickel (pentlandite)[K 2]. Il permet de faire passer la teneur de la matte de 30 à 40 % de nickel à une matte affinée contenant 40 à 70 % de nickel et 20 % de soufre[K 3]. La température de travail,1 400 °C, est légèrement plus haute que pour le cuivre[K 4].
Le convertisseur Peirce-Smith permet donc de mettre en œuvre une variante efficace du procédé Manhès-David. En participant au traitement des minerais sulfureux de nickel, il intervient dans 60 % de l'extraction du nickel[K 1]. Quelques procédés consistent même à ajouter du soufre dans le ferronickel brut issu des latérites pauvres en fer (saprolite), afin d'en faire une matte compatible avec le procédé Manhès-David[K 5]. Mais, comme pour le cuivre, le convertisseur est pénalisé par ses émissions de fumées polluantes[K 6]. Le convertisseur n'étant qu'une étape parmi beaucoup (la métallurgie extractive du nickel étant beaucoup plus complxe que celle du cuivre), les procédés alternatifs d'affinage du nickel ont connu plus de succès. Par exemple, une fusion flash suffisamment oxydante peut donner directement une matte blanche. L'affinage en continu est aussi moins polluant que le convertisseur[K 3].
Notes et références
Notes
- Le point de fusion du FeO est de 1 377 °C. Si le FeO ne se combine pas immédiatement avec la silice pour former de la fayalite (Fe2SiO4)[H 1], dont le point de fusion est de 1 208 °C, son oxydation continue et il se transforme alors en Fe3O4. Or le point de fusion du Fe3O4 est de 1 597 °C ! Le Fe3O4 s'agglomère alors en une masse solide qui empêche le soufflage et ne peut être évacuée du convertisseur[E 1].
- Baggaley est associé à George Westinghouse qui cherche à s'affranchir d'un imaginaire -comme l'histoire le montrera- « trust du cuivre » susceptible de le bloquer dans le développement de ses affaires. Les efforts de George Westinghouse se concentrent alors sur le développement de la Mine Elizabeth (en), dans le Vermont[5].
- Pour descendre à 5 % de soufre dans la matte, il faut oxyder 80 % du nickel[11] !
Références
- (en) Marc E. Schlesinger, Matthew J. King, Kathryn C. Sole et William G. I. Davenport, Extractive Metallurgy of Copper, Elsevier, , 5e éd., 455 p. (ISBN 978-0-08-096789-9, lire en ligne)
- p. 127
- p. 128
- p. 138
- p. 142
- p. 143
- p. 130 ; 135
- (en) Donald M. Levy, Modern copper smelting, C. Griffin & company, limited, (lire en ligne)
- p. 202
- p. 193
- p. 198 ; 202
- p. 193-194
- p. 200-203
- p. 214
- p. 212
- p. 197-198 ; 201
- (en) Edward Dyer Peters, Modern copper smelting, The Engineering and Mining Journal, , 7e éd. (lire en ligne)
- p. 561-562
- (en) Heinrich Oscar Hofman, Metallurgy of copper (lire en ligne)
- p. 323
- p. 299-300
- (en) Frank K. Krundwell, Michael S. Moats, Venkoba Ramachandran, Timothy G. Robinson et William G. Davenport, Extractive Metallurgy of Nickel, Cobalt and Platinum Group Metals, Elsevier, , 610 p. (ISBN 978-0-08-096809-4, lire en ligne)
- p. 2 ; 15
- p. 215
- p. 237-238
- p. 103-104
- p. 104-105
- p. 242
- Autres références
- (en) « Analysis of Jawbone Flats Mine Dump Samples », Western Oregon University,
- (en) Hermann Wedding (trad. from the german by: William B. Phillips, PH. D. & Ernst Prochaska), Wedding's basic Bessemer process [« Basische Bessemer - oder Thomas-Process »], New York Scientific Publishing Company, , 224 p. (lire en ligne), p. 21-22 ; 30-32
- Paul Louis Weiss, Le Cuivre : Origine, Gisements, Propriétés physiques et chimiques, Métallurgie… Marché du cuivre, Principales applications… Alliages industriels, J.-B. Baillière et fils, , 344 p. (ASIN B0019TU3SK, lire en ligne), p. 192-
- (en) Pierre Manhès, « Process of treating copper matte (patent US 456516 A) »
- (en) Larry M. Southwick, « William Peirce and E.A. Cappelen Smith and Their Amazing Copper Converting Machine », JOM, The Mineral, Metals & Materials Society (TMS), vol. 60, no 10, (lire en ligne)
- [PDF](en) Alejandro Alberto Bustos, « Injection phenomena and heat transfer in copper converters »,
- (en) W. A. Mueller, « Progressive Steps In the Metallurgy of Copper », Ohio State University, College of Engineering,
- (en) Kenneth O. Bjork, Saga in Steel and Concrete, Norwegian-American Historical Association, , 504 p. (lire en ligne), p. 249-250
- (en) Victor Baynard Woolley, « United Verde Copper Co. v. Peirce-Smith Converter Co. : Circuit Court of Appeals, Third Circuit. »,
- Henri Moissan et Léon Victor René Ouvrard, Le Nickel, Gauthier-Villars et fils, Masson et Cie, (lire sur Wikisource), p. 65 ; 69
- (en) Hiram W. Hixon, Notes on lead and copper smelting and copper converting, (lire en ligne), p. 102-110
Articles connexes
- Convertisseur (métallurgie)
- Affinage des métaux
- Procédé Manhès-David
- Histoire de la production du cuivre
- Portail de la production industrielle
- Portail de la chimie