Accumulateur lithium-ion
Une batterie lithium-ion, ou accumulateur lithium-ion, est un type d'accumulateur lithium.

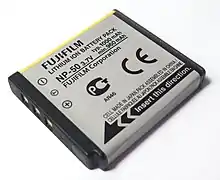
Ses principaux avantages sont une énergie massique élevée (deux à cinq fois plus que le nickel-hydrure métallique par exemple) ainsi que l'absence d'effet mémoire. Enfin, l'auto-décharge est relativement faible par rapport à d'autres accumulateurs. Cependant, le coût reste important et a longtemps cantonné le lithium aux systèmes de petite taille[1].
Historique
Commercialisée pour la première fois par Sony Energitech en 1991, la batterie lithium-ion occupe aujourd'hui une place prédominante sur le marché de l'électronique portable[2].
Le prix Nobel de chimie 2019 a été attribué aux innovateurs de la batterie lithium-ion : l’Anglais Stanley Whittingham, l’Américain John B. Goodenough et le Japonais Akira Yoshino. Stanley Whittingham est à l’origine de la toute première batterie li-ion, conçue dans les années 1970 avec le soutien financier du groupe pétrolier Exxon, inquiété par la crise pétrolière, qui finit par interrompre ses subventions au sortir de cette crise. John Goodenough modifie le prototype de Stanley Whittingham en remplaçant les électrodes en sulfure de tantale par de l’oxyde de cobalt, rendant la batterie au lithium plus efficace et permettant d'envisager une commercialisation. En 1986, le Japonais Akira Yoshino la perfectionne en abandonnant le lithium pur dans l’anode, le mélangeant avec du coke de pétrole, ce qui permet à la fois d’alléger la batterie, de gagner en stabilité et en longévité[3].
Principe de fonctionnement
Aspect microscopique
La batterie lithium-ion est basée sur l'échange réversible de l'ion lithium entre une électrode positive, le plus souvent un oxyde de métal de transition lithié (dioxyde de cobalt ou manganèse) et une électrode négative en graphite (sphère MCMB)[4]. L'emploi d'un électrolyte aprotique (un sel LiPF6 dissous dans un mélange de carbonate d'éthylène, de carbonate de propylène ou de tétrahydrofurane) est obligatoire pour éviter de dégrader les électrodes très réactives.
La tension nominale d’un élément Li-ion est de 3,6 ou 3,7 V selon la technologie.
Cette équivalence : 1 élément Li-ion = 3 éléments Ni-MH est intéressante car elle permet parfois une substitution (du Li-ion par du Ni-MH uniquement, l'inverse pouvant s'avérer catastrophique). Le Ni-MH est d'une utilisation plus sûre, notamment lors de la charge.
Les problèmes de sécurité imposent d'intégrer un système électronique de protection embarqué (BMS), qui empêche une charge ou décharge trop profonde et permet l'équilibrage des tensions entre éléments dans les batteries constituées de plusieurs éléments en série ; à défaut, le danger peut aller jusqu'à l'explosion de la batterie. Les courants de charge et de décharge admissibles sont aussi plus faibles qu'avec d'autres technologies.
Cependant, certains accumulateurs Li-ion industriels de grande puissance (plusieurs centaines de watts par élément) durent jusqu'à quinze ans, grâce à une chimie améliorée et une gestion électronique optimisée. Ils sont utilisés en aéronautique, dans les véhicules hybrides et électriques, les systèmes de secours, les navires… EDF Énergies nouvelles a mis en service un ensemble de batterie Li-Ion de 20 MWh à McHenry (Illinois), destiné à réguler le réseau haute tension pour le compte de l'opérateur PJM Interconnection (en)[5]. Les sondes spatiales Galileo par exemple sont équipées de batteries Li-ion prévues pour douze ans[6]. L'utilisation de la technique Li-ion à ces échelles de puissance n'en était qu'à ses débuts dans les années 2000.
Aspect microscopique : électrochimie
Les réactions électrochimiques permettant le fonctionnement d'un accumulateur forcent le déplacement d'ions lithium d'une électrode vers l'autre. En phase de décharge, l'ion Li+ est libéré par une matrice de graphite pour laquelle il a peu d'affinité et se déplace vers un oxyde de cobalt avec lequel il a une grande affinité. Lors de la charge, l'ion Li+ est relâché par l'oxyde de cobalt et va s'insérer dans la phase graphitique[alpha 1].
Lors de la décharge de l'accumulateur, cela se traduit par les équations chimiques suivantes :
À l'électrode (+) :
À l'électrode (-) :
Lors de la charge, les équations sont à considérer dans l'autre sens. Le processus de décharge est limité par la sursaturation de l'oxyde de cobalt et la production d'oxyde de lithium Li2O qui n'est plus susceptible de restituer l'ion Li+.
Une surcharge de 5,2 V conduit à la synthèse d'oxyde de cobalt(IV) CoO2.
Au sein de l'accumulateur lithium-ion, les ions Li+ font donc la navette entre les deux électrodes à chaque cycle de charge/décharge mais la réversibilité n'est possible que pour < 0,5.
La capacité d'un tel accumulateur est égale à la charge globale des ions transportés multipliée par la tension d'utilisation. Chaque gramme d'ions lithium déplacé d'une électrode vers l'autre transporte une charge égale à la constante de Faraday/6,941 soit 13 901 C. Pour une tension de 3 V, cela correspond à 41,7 kJ/g de lithium donneur d’électron, soit 11,6 kWh/kg. Le lithium seul ne serait toutefois pas capable de générer la décharge électrique, le système fonctionnant seulement en présence d'un anion (CoO2- dans l'application industrielle). Si on considère que la masse de l'anion Oxyde de Cobalt est 13 fois la masse du cation, un accumulateur en LiCoO2 fonctionnel pourrait théoriquement accumuler 0,83 kWh/kg d’énergie électrique, sans considérer la masse des autres composantes nécessaires à son fonctionnement qui réduit la capacité énergétique de l'accumulateur.
Avantages et inconvénients de l'accumulateur lithium-ion
Avantages
- Ils possèdent une haute densité d'énergie, grâce aux propriétés physiques du lithium (densité massique d'énergie de 100 à 265 Wh/kg ou 0,36 à 0,95 MJ/kg, densité d'énergie de 250 à 620 Wh/L, ou 900 à 1 900 J/cm3, puissance massique 300 à 1 500 W/kg et 285 Wh/L). Ces accumulateurs sont donc très utilisés dans le domaine des systèmes embarqués.
- Ils ne présentent aucun effet mémoire contrairement aux accumulateurs à base de nickel.
- Ils ont une faible auto-décharge (quelques % par an à 10 % par mois).
- Ils ne nécessitent pas de maintenance.
- Ils peuvent permettre une meilleure sécurité que les batteries purement lithium, mais ils nécessitent toujours un circuit de protection et de gestion de la charge et de la décharge.
Inconvénients
- La nature des cycles de décharge : ces batteries préservent mieux leur capacité lorsqu'elles sont rechargées à partir d'un état de décharge partielle que lorsqu'elles subissent des cycles complets de décharge/recharge[7].
- La décharge profonde (< 2,5 V par élément ou < 5 % de la capacité totale) est destructrice et peut altérer irrémédiablement l'endurance de ces batteries.
- Les éléments lithium-ion sont passivés par construction (par exemple par dépôt d'un mince film de chlorure de lithium sur l'anode) afin de les protéger contre l'auto-décharge pendant le stockage et, contre la corrosion. Cependant, cette passivation peut avoir des inconvénients car, en augmentant la résistance interne de l'élément, elle génère une chute de tension lors de l'utilisation (au début de l'application de la charge). Ceci est d'autant plus sensible que le courant demandé par l'utilisation est élevé, ce qui peut conduire à l'intervention du circuit de protection qui coupe alors le circuit si la tension par élément descend en dessous de 2,5 V. Cette résistance de la couche de passivation augmente avec la durée et la température de stockage (les températures élevées augmentent la passivation). D'autre part, cet effet est accentué si la température de décharge est basse et augmente avec les cycles d'utilisation. Mais, l'amplitude du phénomène est aussi fonction de la conception chimique qui n'est pas la même selon les fabricants[8].
- Les courants de charge et de décharge admissibles sont plus faibles qu'avec d'autres techniques.
- Il peut se produire un court-circuit entre les deux électrodes par croissance dendritique de lithium.
- L'utilisation d'un électrolyte liquide présente des dangers si une fuite se produit et que celui-ci entre en contact avec de l'air ou de l'eau (transformation en liquide corrosif : l'hydroxyde de lithium). Cette technique mal utilisée présente des dangers potentiels : elles peuvent se dégrader en chauffant au-delà de 80 °C en une réaction brutale et dangereuse. Il faut toujours manipuler les accumulateurs lithium-ion avec une extrême précaution, ces batteries peuvent être explosives.
- Comme avec tout accumulateur d'électricité ne jamais mettre en court-circuit l'accumulateur, inverser les polarités, surcharger ni percer le boîtier.
- Pour éviter tout problème, ces batteries doivent toujours être équipées d'un circuit de protection, d'un circuit de régulation (en anglais le BMS de Battery Management System signifiant « gestion de la batterie »), d'un fusible thermique et d'une soupape de sécurité.
- Elles doivent être chargées en respectant des paramètres très précis et ne jamais être déchargées en dessous de 2,5 V par élément ;
- Selon une analyse du cycle de vie de 2013 ayant notamment porté sur leur recyclabilité, des tests standardisés de lixiviation ont montré qu'au regard de la règlementation fédérale américaine, ces batteries Li-ion doivent être classées dangereuses pour la santé et l'environnement (cf. teneur moyenne en plomb de 6,29 mg/L), mais qu'au regard d'autres normes (ex. : règlementation californienne), toutes les batteries Li-ion testées étaient à classer dangereuses pour leur teneur excessive en cobalt (163 544 mg/kg en moyenne), en cuivre (98 694 mg/kg en moyenne) et en nickel (9 525 mg/kg en moyenne) ; et pour certaines d'entre elles, les quantités de chrome, de plomb et de thallium lixiviées dépassaient également les limites règlementaires californiennes[9].
Risques liés à la surchauffe d'élément
Plusieurs constructeurs comme Nokia et Fujitsu-Siemens ont lancé un programme d'échange de batteries à la suite de problèmes de surchauffe sur certaines batteries qu'ils avaient vendues[10],[11],[12].
En 2016, le constructeur de produits mobile Samsung a même dû retirer son Galaxy Note 7 à la suite de plusieurs cas d'incendies et d'explosions[13].
Charge et décharge
La charge se passe généralement en deux phases, une première phase à courant limité de l'ordre de C/2 à 1 C (C étant la capacité de l'accumulateur). Cette phase permet une charge rapide jusqu'à environ 80 %, puis une deuxième phase à tension constante et courant décroissant pour se rapprocher des 100 % de charge en environ deux heures de plus. La charge est terminée lorsque le courant de charge chute en dessous d'une valeur appelée courant de fin de charge.
La tension de fin de charge des accumulateurs Li-ion peut être de 4,1 à 4,2 V suivant la spécification du fabricant de l'accumulateur. La tolérance couramment admise est de ± 0,05 V par élément, ils sont très sensibles à la surcharge et demandent une protection lorsqu'ils sont connectés en série. Les chargeurs doivent être de bonne qualité pour respecter cette tolérance. Il importe de toujours respecter la feuille de données fournie par le fabricant, qui fait état des conditions de charge de l'accumulateur (tolérance, courant de charge, courant de fin de charge, etc.). Toutefois, certains éléments destinés au grand public possèdent une électronique interne qui les protège des mauvaises manipulations (surcharge, décharge profonde). En effet, la décharge doit être limitée à une tension de 3 V par élément, une tension de décharge inférieure à 2,5 V peut conduire à une destruction de l'élément.
Les accumulateurs Li-ion ne doivent pas être confondus avec les piles au Lithium qui ne sont pas rechargeables. La confusion est entretenue par le terme anglais Battery qui désigne aussi bien une pile électrique[alpha 2] (primary battery ou primary cell en anglais[14],[15]) qu'un accumulateur (secondary battery ou secondary cell en anglais[14],[16]), alors qu'en français le terme batterie est utilisé, improprement, pour désigner généralement une « batterie d'accumulateurs électriques ».
Le taux d'auto-décharge des batteries lithium-ion est faible : moins de 10 %/an[17], contrairement à certains types de batteries qui se déchargent même à l'arrêt : c'était le cas de la batterie lithium/métal/polymère (LMP) de Bolloré, qui ont été un fiasco car elle doit être maintenue à une température de 60 °C, ce qui imposait de la recharger en permanence lorsqu’elle n’était pas en circulation, sans quoi elle se déchargeait[18].
La perte de capacité des batteries est très variable selon les modèles, le climat et le mode de recharge. En moyenne, selon une étude menée en 2019 sur 6 300 véhicules électriques, cette perte est de 2,3 % par an. Les charges rapides accélèrent fortement cette perte : sans charge rapide, une batterie perd moins de 2 % en cinq ans, contre plus de 10 % avec des charges rapides régulières[19].
Amélioration de la durée de vie, conditions requises
Si l'on respecte rigoureusement les conditions de charge et décharge, ces accumulateurs peuvent durer 5 à 6 ans pour des produits « grand-public » (vélos électriques, smartphones, appareils photos) et plus d'une dizaine d'années pour des produits industriels.
- Respecter les particularités électriques
- La tension de fin de charge à ne « jamais » dépasser est de 4,1 à 4,2 V par élément.
- La tension de décharge ne devrait jamais descendre en dessous de 2,5 V.
Avec un chargeur adapté de qualité et un système de gestion de batterie (BMS), ces impératifs sont normalement respectés.
- Respecter quelques consignes d'utilisation[20]
Éviter l'échauffement de l'accumulateur :
- contenant noir, exposé au soleil ;
- ne pas recharger immédiatement après une utilisation intensive ;
- ne pas utiliser immédiatement après une recharge ;
- éviter les décharges importantes (exemple : monter une côte à vélo électrique sans pédaler)[21] ;
- stockage[22].
Les accumulateurs s'usent même sans servir (à l'achat, vérifier la date de fabrication).
- Stocker si possible dans un endroit frais (le froid ralentit les réactions chimiques)[23].
- Si le stockage doit être long (plusieurs semaines ou mois), il est préférable de ne pas charger complètement l'accumulateur (passivation des électrodes) mais le laisser à mi-charge ET il faudra faire des recharges partielles tous les mois pour réactiver l'électrolyte et les électrodes et compenser l'auto-décharge (5 à 10 % par mois).
En respectant ces conditions, l'accumulateur pourra continuer à fonctionner, tout en sachant néanmoins que sa capacité (en Ah) diminuera d'année en année.
La fin de vie intervient quand, lors de la décharge, le BMS détecte une tension inférieure au seuil de coupure, même sur un seul élément, et coupe l'alimentation. Il peut rester 10 à 20 % de capacité dans l’accumulateur, mais on ne peut plus l'utiliser. La fin de vie peut aussi advenir parce qu'on a épuisé le nombre de cycles charge-décharge du produit, mais cela devient rare, le nombre de cycles possibles ayant augmenté (environ de 500 à 1 000).
Un appareil équipé d'une batterie au lithium-ion fournit moins d'énergie lorsque les températures sont négatives. Il est conseillé de garder son smartphone, sa tablette ou tout autre appareil électronique équipé d'une batterie au lithium-ion dans un endroit à la température comprise entre 0 °C et 35 °C, avec une zone de confort entre 16 °C et 22 °C. Lorsque les températures chutent, les réactions chimiques qui produisent de l'énergie sont moins actives. De ce fait, l'énergie fournie est moindre. Les performances de la batterie reviennent toutefois à la normale, lorsque les températures remontent[24].
Production
En 2013, les industriels japonais représentaient 70 % du marché mondial des batteries destinées au marché automobile ; leur part de marché est tombée à 41 % en 2016, alors que celle de la Chine est passée de 3 à 26 %[25].
En 2020, près de 140 GWh de batteries ont été affectés à la fabrication de véhicules électriques et hybrides. Les six principaux fabricants de ces batteries totalisent environ 90 % du marché ; trois sont coréens : LG Energy Solutions, en tête avec une capacité de 40 GWh, Samsung SDI et SK Innovation ; deux sont chinois : CATL, au 2e rang mondial avec une capacité de 30 GWh, et BYD ; un est japonais : Panasonic, leader sur le marché américain grâce à son partenariat avec Tesla[26]. Pour l'approvisionnement du marché européen, la tendance est à la fabrication des cellules en Europe par des fabricants asiatiques : LG Chem en Pologne pour les batteries de la Renault ZOE II, Nissan AESC (coentreprise entre Nissan et NEC) au Royaume-Uni pour celles de la Nissan LEAF II, Samsung SDI en Hongrie pour celles de la BMW i3, LG Chem en Allemagne pour la Volkswagen ID3[27].
En 2021, CATL a une part de marché de 32 %, suivi par LG Energy Solution (21 %) et Panasonic. En janvier 2022, LG Energy Solution (LGES) lève l'équivalent de 10,6 milliards de dollars à la Bourse de Séoul pour financer le développement d'usines à l'étranger (États-Unis et Pologne). LGES fournit déjà des batteries à Tesla, Hyundai, Volkswagen et General Motors et vient de signer un accord avec Stellantis[28]. Le marché des batteries pour voitures électriques et hybrides a progressé de 113 % en 2021. Les trois principaux fabricants alimentent 67 % du marché mondial : CATL (31 %), qui progresse de 204 %, LGES (22 %), en hausse de 72 %, et Panasonic (14 %), en progression de 39 %. Leur principal client est Tesla (23 %). CATL alimente surtout la Chine, LGES l'Europe et Panasonic l'Amérique[29].
Asie
Le groupe japonais Panasonic reste au 1er rang mondial des fabricants de cellules pour batteries au premier quadrimestre 2018 avec une production de 3 330 MWh, en progression de 21,5 % par rapport à 2017, mais sa part de marché recule de 31,4 % à 21,1 % ; au 2e rang, le chinois CATL a produit 2 274 MWh, en progression de 261 % (14,4 % du marché), et au 3e rang, le chinois BYD 1 735 MWh (+180,6 % ; 11 % du marché) ; au 4e rang, le coréen LG Chem, avec 1 670 MWh (+39 %) recule de 13,8 % à 10,6 % du marché et au 5e rang, le coréen Samsung SDI 879 MWh (+47 %) recule de 6,8 % à 5,6 % du marché. Au total, ces cinq producteurs représentent 64 % du marché mondial[30].
Une alliance financée par le gouvernement japonais a été créée en mai 2018 pour accélérer le développement des batteries solides ; elle comprend des constructeurs (Toyota, Nissan et Honda), des fabricants de batteries (Panasonic et GS Yuasa) et le Libtec, organisme de recherche nippon sur les batteries lithium-ion. L'objectif est de doubler l’autonomie des voitures électriques pour passer à 800 kilomètres d’ici 2030, avec un premier objectif fixé à 550 kilomètres à l’horizon 2025.
En , le gouvernement chinois a supprimé toute subvention pour les batteries qui n'assurent pas une autonomie d'au moins 150 km ; cette nouvelle politique va déclencher une consolidation à grande échelle dans l'industrie des batteries automobiles en Asie, où sévit une centaine d'acteurs. Les producteurs japonais et sud-coréens ont eux aussi programmé une montée en puissance rapide. Entre 2017 et 2020, Panasonic, qui travaille quasi exclusivement pour Tesla, va plus que doubler ses volumes de production avec l'inauguration de sa Gigafactory au Nevada au début des années 2020. CATL va quintupler ses capacités de production d'ici à 2020 grâce à une usine chinoise géante. Le nouveau site de LG Chem à Wroclaw en Pologne va approvisionner Renault, Audi ou Volvo. Samsung SDI a transformé une ancienne usine d'écrans plasma à Goed en Hongrie en un centre de production de batteries lithium-ion afin de livrer Volkswagen et BMW ; ce dernier a cependant signé un contrat avec CATL[31].
La société chinoise Contemporary Amperex Technology Limited (CATL) annonce en une batterie lithium-ion, pour voitures électriques, capable de durer 16 ans et une distance de 2 millions de kilomètres, deux fois plus que les garanties actuelles, limitées à huit ans en moyenne, et 1 million de kilomètres au maximum chez Lexus. En revanche, le prix de ces batteries serait 10 % plus élevé que celles actuelles. Tesla annonce 1,6 million de kilomètres pour ses batteries, moins chères à produire, et General Motors a présenté ses batteries Ultium, ayant une durée de vie annoncée supérieure à 1 million de kilomètres[32].
En 2020, l'Inde envisage un plan analogue à l'« Airbus des batteries » afin de s’affranchir de sa dépendance à la Chine pour ses cellules de batteries lithium-ion. Le gouvernement estimerait qu’il y aurait sur son territoire le potentiel suffisant pour créer au moins 5 Gigafactories de type Tesla pour une capacité totale de 50 GWh[33].
États-Unis
Tesla a construit sa Gigafactory 1 au Nevada avec une capacité de 35 GWh/an et prévoit des Gigafactory 2 et suivantes à Buffalo dans l'État de New York, au Japon et en Chine. Tesla a sécurisé en ses approvisionnements en lithium pour trois ans grâce à un contrat avec la compagnie australienne Kidman Resources[34].
General Motors construit trois « Gigafactories » de batteries : la première doit ouvrir en 2022 à Lordstown (Ohio) avec une capacité de 30 GWh/an, la seconde (40 GWh/an) en 2023 à Spring Hill (Tennessee), et la troisième (50 GWh/an) en 2024 à Lansing (Michigan). Leur production de 120 GWh/an au total permettra à General Motors de produire 1 million de voitures électriques par an à l’horizon 2025. Un quatrième site devrait être annoncé prochainement. Ces usines, implantées à proximité de sites d’assemblage de véhicules GM, appartiennent à Ultium Cells, une coentreprise rassemblant GM et le groupe coréen LG Chem[35].
Stellantis et Samsung SDI annoncent en mai 2022 une coentreprise pour la construction d'une usine de batteries dans la ville de Kokomo (Indiana), qui produira des modules de batterie à partir de 2025 pour les différents modèles du groupe en Amérique du Nord, avec une capacité de production initiale de 23 GWh/an, avec une possibilité d'aller jusqu'à 33 GWh/an[36].
Europe
Le projet Northvolt, soutenu par la Commission européenne via un prêt de la Banque européenne d'investissement (BEI) de 52,5 millions d’euros, a été initié par deux anciens de chez Tesla ; il rassemble Scania, Siemens et ABB pour construire en Suède une usine de batteries qui devrait entrer en service en 2020 avec un objectif de production de 8 GWh/an de cellules, puis 32 GWh/an d’ici 2023[37]. La construction de l'usine a commencé le à Skellefteå, en Suède ; le consortium Northvolt a reçu l'adhésion du fabricant danois d'éoliennes Vestas[30]. Les deux fondateurs, Peter Carlsson, ancien responsable production de la Model S, et Paulo Cerruti, ont choisi la Suède parce qu'on y dispose d'une énergie pas chère et à 100 % hydraulique, ce qui permet de minimiser les émissions de CO2 ; ils espèrent aussi pouvoir s'approvisionner en nickel, cobalt, lithium et graphite en Scandinavie. Afin d'être compétitifs avec les géants asiatiques, ils comptent réduire leurs coûts par une intégration verticale très forte et automatiser les process[38].
Soutenue par la Commission européenne et sa banque d’investissement, l’European Battery Alliance (EBA) veut promouvoir un « Airbus des batteries » ; elle estime qu’il faudrait « au moins 10 à 20 gigafactories » pour satisfaire la demande de l’Union européenne en batteries. Dès 2025, le continent pourrait capter un marché de 250 milliards d’euros, alors qu'en 2018 les constructeurs asiatiques monopolisent ce marché. Après avoir soutenu le projet Northvolt, ils poussent les projets du français Saft, récemment racheté par Total et du consortium allemand Terra-E[39].
Les entreprises coréennes LG Chem et Samsung SDI exploitent déjà (en 2018) des usines de cellules pour batteries en Europe, respectivement en Pologne et en Hongrie, et le fabricant chinois de batteries CATL (Contemporary Amperex Technology), qui a signé des contrats de fourniture avec BMW, Volkswagen, Daimler et l’alliance Nissan-Renault, envisage la construction d’une usine en Europe[40]. CATL a décidé en de construire cette usine à Erfurt en Allemagne ; elle aura une capacité de 14 GWh/an[41].
Le , Peter Altmeier, ministre de l'Économie et de l'Énergie allemand, annonce la mobilisation d'un milliard d'euros d'ici à 2021 pour faciliter le lancement d'une production de cellules lithium-ion en Allemagne, afin que l'Allemagne et l'Europe puissent satisfaire 30 % de la demande mondiale d'ici à 2030[42].
La Commission européenne donne le son accord « de principe » au versement par Paris et Bruxelles de subventions aux projets d'« Alliance européenne des batteries », sans que celles-ci soient jugées comme des aides d'état illégales. Le montant des subventions autorisées sera cependant limité à 1,2 milliard d'euros, soit moins que le 1,7 milliard promis par la France et l'Allemagne. En ajoutant les fonds privés, les investissements dans cette initiative pourraient représenter jusqu'à 5 à 6 milliards d'euros. Peter Altmaier, ministre allemand de l'Économie, annonce avoir reçu plus de trente-cinq marques d'intérêt[43].
La Roumanie annonce en la réouverture de plusieurs mines pour contribuer au projet d’Alliance européenne des batteries. Il s'agit de mines de cobalt, utilisé pour la fabrication des cathodes dans les cellules des accumulateurs lithium-ion, et de graphite, principal constituant des anodes[44].
La Commission européenne attribue, le , le label « projet européen d'intérêt commun » (IPCEI) au projet d'« Airbus des batteries » lancé par la France et rejoint par six autres États membres de l'UE (Allemagne, Belgique, Pologne, Italie, Suède, Finlande) ; ce label autorise les aides d'État. Le projet réunit dix-sept entreprises, dont PSA, Saft, BASF, BMW, Varta, Eneris, Solvay et Umicore. Le total des aides d'État promises devrait atteindre 3,2 milliards d'euros, qui s'ajouteront aux 5 milliards d'investissement prévus par les entreprises[45].
La coentreprise Volkswagen-Northvolt annonce en mai 2020 la construction d'une première usine de batteries sur le site Volkswagen de Salzgitter en Allemagne. Elle produira 16 GWh d’accumulateurs chaque année dès 2024, soit environ le dixième de la demande européenne, estimée à 150 GWh par an en 2025[46].
En novembre 2020, le fabricant chinois de batteries SVolt annonce la construction d'une usine de batteries pour voitures électriques en Allemagne, dans la région de Sarrelouis ; sa capacité de production de 24 GWh permettra d'équiper entre 300 000 et 500 000 voitures par an ; elle devrait démarrer à la fin de 2023[47].
En mars 2021, Volkswagen annonce son objectif de produire 240 GWh de batteries en 2030 dans six usines, contre 30 GWh en 2023 lors du démarrage des deux premières usines : l’usine suédoise de Skellefteå sera la première à atteindre 40 GWh en 2023, puis celle de Salzgitter en 2025. Un modèle unique de batterie sera utilisé sur 80 % de la gamme, ce qui devrait permettre une réduction du prix des voitures de 30 % en milieu de gamme et de 50 % sur le segment d’entrée de gamme[48],[49].
Les projets d'usines géantes de batteries se multiplient en Europe : avant même les annonces de Volkswagen, les experts de l'ONG Transport & Environnement avaient recensé 22 projets, dont 8 en Allemagne, représentant 460 GWh de capacité en 2025 et 730 GWh en 2030[50].
Le 29 décembre 2021, la première usine de Northvolt démarre sa production de batteries, les premières à avoir été entièrement conçues, développées et assemblées par une entreprise créée en Europe[51].
Au Royaume-Uni, le projet d'usine de batteries de Britishvolt dans la région du Northumberland, annoncé en 2000, a sécurisé son investissement de 1,7 milliard £ (2 milliards €). Ses 30 GWh de capacité devraient représenter un tiers de besoin en batteries de l’industrie automobile britannique en 2030. Son démarrage est prévu pour 2024[52].
ACC, la coentreprise fondée en août 2020 par PSA et TotalEnergies, rejoints en septembre 2021 par Mercedes-Benz, annonce le 22 mars 2022 un rehaussement majeur de son objectif 2030 de capacité de production de batteries à 120 GWh au lieu de 48 GWh initialement prévus. Un troisième site de production est choisi : Termoli en Italie. Les deux autres sites choisis antérieurement, Douvrin en France et Kaiserslautern en Allemagne, devaient au départ atteindre progressivement une cadence de 450 000 batteries par an. Douvrin, qui doit être mis en service en 2023, voit son objectif porté à 700 000 ou 800 000 batteries par an[53].
A la mi-2022, l'Europe compte près de 40 projets majeurs de gigafactories (de plus de 10 GWh) pour un total d'au moins 1 400 GWh, qui seraient installés dans les dix prochaines années, permettant d'équiper environ 17,5 millions de véhicules par an à cet horizon, alors que l'Europe produisait sur son territoire environ 20 millions de voitures particulières avant la crise du Covid-19. La capacité annoncée pour 2030 a quasiment doublé par rapport à mars 2021 : l'ONG Transport et Environnement l'estimait alors à 730 GWh. L'Allemagne compte sept projets majeurs (plus de 500 GWh), la Grande-Bretagne 4 projets (170 GWh), la France 3 projets (120 GWh), l'Espagne 4 projets (90 GWh) et l'Italie 2 projets (85 GWh). Plus de 40 % des capacités annoncées (620 GWh) proviennent d'acteurs non européens, dont 250 GWh par Tesla et le solde par les acteurs asiatiques qui dominent jusqu'ici le marché[54].
France
Après l'accord « de principe » donné par la Commission européenne le au versement par Paris et Bruxelles de subventions aux projets d'« Alliance européenne des batteries », Bruno Le Maire confirme que le premier projet est porté par Saft, propriété du groupe Total, et PSA, via sa filiale allemande Opel ; il débutera par une usine pilote de 200 salariés, dès 2020, en France, puis deux usines de production, l'une en France et l'autre en Allemagne, de 1 500 salariés chacune, d'ici 2022-23, qui produiront d'abord des batteries lithium-ion liquides « améliorées », puis adopteront à partir de 2025-2026 la technologie solide[55]. Le PDG de Total, marqué par son échec dans le secteur des panneaux solaires, estime que ce projet ne serait pertinent qu’en investissant dans la future génération de batteries. Il demande également des garanties de l’Union européenne afin de protéger le marché face aux concurrents asiatiques. Il explique que l’initiative nécessitera d’« énormes » subventions publiques[43].
Le 3 septembre 2020, le constructeur automobile PSA et le pétrolier Total (avec sa filiale Saft) annoncent la création d’Automotive Cells Company (ACC), une coentreprise chargée de créer deux usines de cellules de batteries dès 2023 en France et Allemagne. ACC développe déjà les cellules lithium-ion sur le site Saft de Nersac, près d’Angoulême ; la production de ses batteries sera relocalisée en 2023 sur deux autres sites à forte capacité : en France à Douvrin (62) pour Peugeot/Citroën, et à Kaiserslautern en Allemagne pour Opel, avec 8 GWh de capacité annuelle, portée progressivement à 48 GWh en 2030, soit l’équivalent d’un million de véhicules électriques[56].
Le , Renault annonce deux partenariats majeurs pour des usines géantes de batteries, le premier avec le chinois EnVision pour la construction d'une « gigafactory » à Douai (9 GWh en 2024, 24 GWh en 2030), représentant un investissement de 2 milliards € et 2 500 emplois à horizon 2030, le second avec la startup grenobloise Verkor, dont il prend plus de 20 % du capital, afin de lui permettre de construire une ligne pilote dès 2022 pour codévelopper des batteries haute performance, qui équiperont les véhicules à batterie haut de gamme de Renault (de segment C et plus), ainsi que les Alpine électriques. Verkor construira ensuite une « gigafactory » de 16 GWh, qui démarrera en 2026 et emploiera 1 200 personnes à plein régime[57].
Prix
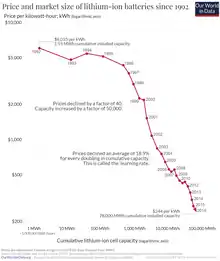
Selon Bloomberg BNEF[58], le prix des packs de batteries pour voiture électrique est passé en 10 ans (2010-2020) de 1 100 $ à 137 $ par kWh (102 $ pour les cellules + 35 $ pour le pack). Le prix moyen des batteries pour bus en Chine est à 105 $/kWh. BloombergNEF estime que le prix pourrait baisser de 40 % pour atteindre 58 $/kWh à l’horizon 2030[59].
En 2021, Bloomberg estime le coût d’une batterie à 116 €/kWh en 2021, soit 6 % de moins qu’en 2020 (124 €/kWh), tous types de batteries confondus. La baisse de prix sur les batteries pour voitures électriques est encore plus marquée, à 104 €/kWh. En Chine, le prix moyen des batteries est à 98 €/kWh. Les États-Unis et l’Europe contribuent à faire remonter le prix mondial moyen, affichant respectivement des tarifs 40 et 60 % plus élevés. Nissan envisage pour 2030 des batteries solides à un coût de 65 €/kWh[60].
Réglementation
La Commission européenne présente en décembre 2020 un projet de règlement, qui devra être validé par les États membres et le Parlement européen, qui imposera des critères environnementaux sur l'ensemble de la chaîne de vie des batteries, de l'extraction des matières premières au recyclage, en passant par la production. Pour limiter l'empreinte carbone de leur production, les fabricants devraient d'abord la mesurer et la déclarer à compter de . Un système de « passeport numérique » permettra un suivi fin de l'origine et du traitement des matériaux utilisés. En , des labels de classe de performance seront introduits. Sur la base des données alors recueillies, des seuils maximaux d'empreinte carbone seraient fixés, à chaque niveau de la chaîne, à partir de juillet 2027. Des critères de performance et de sécurité seront aussi définis. Les critères écologiques à respecter porteront en particulier sur la durabilité des matières premières utilisées, le recours à des matériaux recyclés et la propreté de l'énergie consommée pour la fabrication. Le volet recyclage du plan entrerait en vigueur dès 2025. L'objectif de collecte séparée des batteries portables passerait alors à 65 % (puis 70 % en 2030), contre 45 % dans les textes actuels. Thierry Breton avertit : « Les batteries ne respectant pas totalement les normes que nous fixerons sont interdites au sein du marché unique ». Le commissaire à l'Énergie, Maros Sefcovic, se dit « persuadé que d'ici à 2025, l'Union européenne sera en mesure de produire suffisamment de cellules de batteries pour répondre aux besoins de l'industrie automobile européenne »[61].
Recyclage
Une usine de recyclage des batteries de véhicules électriques, lancée à titre expérimental en 2011 à Dieuze (Moselle) par Veolia et Renault, va passer au stade industriel avec des aides du « programme investissements d'avenir », passant de 1 000 t recyclées en 2014 à 5 000 t prévues en 2020[62].
La Société nouvelle d'affinage des métaux (SNAM) à Viviez (Aveyron), filiale du holding belge Floridienne, retraite 6 000 t d'accumulateurs par an, dont 8 % de batteries d'automobiles ; elle fabriquera à partir de 2018 des batteries avec les composants recyclés. SNAM ouvrira d'abord au printemps 2018 un atelier pilote de batteries lithium-ion recyclées. Pour la fabrication en série, l'entreprise cherche un nouveau site dans l'Aveyron pour ouvrir en 2019 une usine d'une capacité de 20 MWh par an. Elle améliorera ensuite les procédés pour passer à 4 000 MWh par an vers 2025. Les constructeurs automobiles ne voulant pas de batteries recyclées, la société vise le marché en croissance du stockage de l'électricité dans l'industrie, le bâtiment et les énergies renouvelables[63].
La société belge Umicore exploite une usine de recyclage de batteries à Hoboken près d’Anvers. L’entreprise allemande Saubermacher et sa filiale autrichienne Redux Recycling ont inauguré en une usine de recyclage de batteries pour véhicules électriques à Bremerhaven, dans le nord de l’Allemagne. Le site est capable de traiter tous les types de batteries lithium-ion et a une capacité de 10 000 t/an. Le volume de batteries en fin de seconde vie étant encore faible, les partenaires s’attendent à ne recycler que 2 000 à 3 000 t/an au cours des prochaines années[30].
Recherche et développement
En 2011, le Laboratoire d'innovation pour les technologies des énergies nouvelles et les nanomatériaux bat le record du monde de distance pour une propulsion électrique en équipant un véhicule de batteries lithium-ion à base de phosphate de fer qui parcourt 1 280 kilomètres en 24 heures autour de Grenoble[64].
En 2013, le programme européen Life + soutient un projet dit « LIFE BIBAT » porté par le Commissariat à l'énergie atomique et aux énergies alternatives visant à « valider une ligne pilote pour une nouvelle génération de batteries lithium-ion écologiques de conception bipolaire. Le projet BiBAT vise à satisfaire aux besoins énergétiques et à remédier au problème de l'épuisement des ressources dans le cadre de la fabrication de batteries lithium-ion »[65].
Les batteries solides semblent bien placées pour succéder à terme aux batteries lithium-ion. Elles promettent une capacité de stockage accrue, une meilleure sécurité, un coût réduit, une plus grande durabilité et même une charge plus rapide. L'électrolyte liquide y est remplacé par un matériau solide de type céramique ou un polymère ; elles ne contiennent aucun composant liquide ou combustible et offrent donc une meilleure sécurité en réduisant notamment les risques d'incendie. Hyundai, Toyota, Fisker, BMW, Google, Solvay, Bosch, Dyson, Continental travaillent au développement de cette technologie[66]. Les batteries sodium-ion semblent également une alternative prometteuse, le sodium étant quarante fois plus abondant que le lithium[67].
Le projet européen Lisa (de l'anglais Lithium Sulfur for Safe Electrification), regroupant 13 partenaires (instituts de recherche et industriels dont Renault), est lancé le pour mettre au point en quatre ans une batterie de traction lithium-soufre pour la mobilité électrique. Moins dangereuses que les batteries lithium-ion grâce à leur électrolyte solide non inflammable, elles seraient aussi deux fois moins lourdes et moins encombrantes, autorisant leur utilisation dans les véhicules lourds, notamment dans les cars et bus[68].
En 2020, la startup californienne Enevate annonce la commercialisation à partir de 2024 d’une nouvelle génération de cellules lithium-ion très performantes, dotées d'une anode en silicium : plus légères que celles qui sont actuellement utilisées, elles devraient permettre de charger 75 % de la capacité d’une batterie en cinq minutes. Elles pourront être produites en grande quantité sur les lignes de fabrication existantes, ce qui devrait accélérer leur adoption par les constructeurs[69].
En , la société californienne QuantumScape présente une batterie lithium-ion tout-solide basée sur des séparateurs en céramique flexibles, qui pourrait se charger à 80 % en 15 minutes et aurait une durée de vie améliorée. Créée en 2010 et issue de l’université Stanford, cette start-up compte parmi ses soutiens Volkswagen, qui l'accompagne en tant que partenaire industriel depuis 2012 et a investi plus de 300 millions de dollars dans son développement ; QuantumScape a conclu un partenariat avec Volkswagen pour fournir 20 GWh de batteries d’ici 2024-2025 ; elle est cotée à Wall Street et dispose d’une enveloppe de 1,5 milliard de dollars pour ce projet[70],[71].
Le , la Commission européenne approuve une aide publique de 2,9 milliards € octroyée par 12 États membres, dont l'Allemagne, la France, l'Italie et l'Espagne, pour un vaste projet commun de recherche sur des batteries de nouvelle génération, baptisé « The european battery innovation ». Il complète le premier projet européen dit « Airbus des batteries », lancé fin 2019 par sept États avec 3,2 milliards € d'aides d'État, qui vise à lancer les premières « giga factories » européennes dans les deux ans. Le projet de recherche réunira jusqu'en 2028 une quarantaine d'entreprises, dont les constructeurs BMW, Fiat-Chrysler et Tesla, le spécialiste suédois des piles Northvolt et le chimiste français Arkema, pour innover sur toute la chaine de valeur[72].
Notes et références
Notes
- D'après l'article anglais correspondant.
- En français le terme « pile » désigne un empilement d'éléments quels qu'ils soient. Néanmoins le terme pile électrique désigne uniquement un générateur d’électricité chimique (non rechargeable).
Références
- (en) I. Hanin, W. Van Schalkwijk et B. Scrosati, Advances in Lithium-Ion Batteries, Kluwer Academic Publishers, (ISBN 0306475081).
- Marie-Liesse Doublet, « Batteries Li-ion – Conception théorique », Paris, Techniques de l'ingénieur, vol. AFP4, no AF6612, Éditions techniques de l'ingénieur, 2009, p. 2 [lire en ligne].
- Le prix Nobel de chimie 2019 attribué aux inventeurs de la batterie lithium-ion, sur automobile-propre.com, 9 octobre 2019.
- (en) Overview of Lithium Ion Batteries [PDF], janvier 2007, sur panasonic.com.
- Les batteries lithium-ion, nouvel Eldorado américain ?, sur edf.com (consulté le 8 novembre 2016).
- (en) saftbatteries.com, communiqué de presse [PDF], sur pictime.fr.
- (en) How to Charge - When to Charge Table, sur batteryuniversity.com.
- (en) « Passivation », sur spectrumbatteries.com (consulté le ).
- (en) Daniel Hsing Po Kang, Mengjun Chen et Oladele A. Ogunseitan, « Potential Environmental and Human Health Impacts of Rechargeable Lithium Batteries in Electronic Waste », Environmental Science & Technology, vol. 47, no 10, , p. 5495–5503 (ISSN 0013-936X et 1520-5851, PMID 23638841, PMCID PMC5920515, DOI 10.1021/es400614y, lire en ligne, consulté le ).
- Nokia, remplacement des batteries BL-5C, sur batteryreplacement.nokia.com.
- Fujitsu-Siemens, programme d'échange de batterie, sur fujitsu-siemens.fr.
- (en) Keith Bradsher, « China Vies to Be World’s Leader in Electric Cars », The New York Times, .
- (en) Samsung recalls Galaxy Note 7 worldwide due to exploding battery fears, sur theverge.com, 2 septembre 2016 (consulté le 8 novembre 2016).
- « IEC 60050 - International Electrotechnical Vocabulary - Details for IEV number 482-01-04: "battery" », sur electropedia.org (consulté le )
- « IEC 60050 - International Electrotechnical Vocabulary - Details for IEV number 482-01-02: "primary cell" », sur electropedia.org (consulté le )
- « IEC 60050 - International Electrotechnical Vocabulary - Details for IEV number 482-01-03: "secondary cell" », sur electropedia.org (consulté le )
- Les batteries Lithium-ion, Avem.fr.
- Le fiasco des batteries de voiture de Bolloré, Capital, 8 janvier 2019.
- Batteries : quelle perte de capacité pour les voitures électriques ?, automobile-propre.com, 22 décembre 2019.
- « Entretien batterie vélo électrique », sur power-e-bike.fr (consulté le ).
- « Règles de durabilité », sur cyclurba.fr (consulté le ).
- « courbes et tests », sur power-e-bike.fr (consulté le ).
- « Batterie, chimie… », sur Electropedia, (consulté le ).
- « Pourquoi le froid n’est pas l’ami de votre smartphone », leparisien.fr, 2018-02-25cet12:34:16+01:00 (lire en ligne, consulté le )
- Un consortium nippon pour développer les batteries solides, automobile-propre.com, 9 mai 2018.
- Voiture électrique : LG leader des batteries en 2020, automobile-propre.com, 9 février 2021.
- D’où viennent les batteries de nos voitures électriques ?, automobile-propre.com, 23 juin 2020.
- Quand les batteries de LG électrisent la Bourse de Séoul, Les Échos, 27 janvier 2022.
- Batterie : Tesla pèse 23 % des capacités mondiales, 11 février 2022.
- Batteries et mobilité électrique : l’essentiel de l’actu, sur automobile-propre.com, 17 juin 2018.
- Les géants asiatiques des batteries condamnés à une consolidation brutale, Les Échos, 4 juillet 2018.
- Voiture électrique : des batteries à 2 millions de km chez CATL, automobile-propre.com, 9 juin 2020.
- Inde : Un Airbus des batteries et des droits à l’importation pour les cellules, automobile-propre.com, 13 juillet 2020.
- Lithium – Tesla sécurise ses approvisionnements en Australie, automobile-propre.com, 18 mai 2018.
- Batteries : GM choisit le Michigan pour sa troisième Gigafactory, automobile-propre.com, 27 janvier 2022.
- Automobile : Stellantis annonce une nouvelle usine de batteries aux États-Unis, Les Échos, 25 mai 2022.
- Batteries : Siemens s’associe au projet de Gigafactory de Northvolt, sur automobile-propre.com, 25 mai 2018.
- Batterie : le projet fou de deux anciens de Tesla, Les Échos, 3 juillet 2018.
- Un nouveau plan stratégique pour créer un Airbus des batteries, sur automobile-propre.com, 20 mai 2018.
- Une usine de CATL en Europe ? La décision sera bientôt prise, sur automobile-propre.com, 21 mai 2018.
- Batteries : la Chine installe sa première usine en Allemagne, Les Échos, 9 juillet 2018.
- Batterie électrique : Berlin et Paris veulent convaincre les industriels d'y aller, Les Échos, 13 novembre 2018.
- Batteries européennes : Bruxelles donne son feu vert « de principe » à Paris et Berlin, Les Échos, 2 mai 2019.
- La Roumanie va rouvrir des mines de cuivre, de cobalt et de graphite pour l’Airbus des batteries, sur automobile-propre.com, 25 juin 2019.
- Paris prend les commandes du premier Airbus des batteries, Les Échos, 9 décembre 2019.
- Volkswagen va construire sa gigafactory de batteries à Salzgitter, automobile-propre.com, 11 mai 2020.
- Voiture électrique : une nouvelle gigafactory de batteries en Allemagne, Les Échos, 17 novembre 2020.
- Power Day : Volkswagen annonce 6 Gigafactories en Europe, automobile-propre.com, 15 mars 2021.
- Volkswagen suit la voie de Tesla en annonçant six « gigafactories » de batteries, Les Échos, 15 mars 2021.
- Voitures électriques : une déferlante d'usines de batteries s'annonce en Europe, Les Échos, 29 mars 2021.
- Auto : Northvolt livre les premières batteries électriques « made in Europe », Les Échos, 29 décembre 2021.
- Batteries : 2 milliards d’euros pour la Gigafactory Britishvolt, automobile-propre.com, 24 janvier 2022.
- Automobile : ACC, le pionnier franco-allemand de la batterie, monte en puissance, Les Échos, 23 mars 2022.
- Anne Feitz, Voiture électrique: où se situe la France dans la course aux gigafactories ?, Les Échos, 10 juillet 2022.
- Batteries européennes : Bruxelles donne son feu vert « de principe » à Paris et Berlin, Les Échos, 2 mai 2019.
- Automotive Cells Company : la nouvelle entreprise de batteries PSA-Total, Les Échos, 3 septembre 2020.
- Deux nouvelles usines géantes de batteries en France pour Renault, Les Échos, 28 juin 2021.
- (en) Battery Pack Prices Cited Below $100/kWh for the First Time in 2020, While Market Average Sits at $137/kWh, bnef.com, 16 décembre 2020.
- Voiture électrique : la chute spectaculaire du prix des batteries en 10 ans, automobile-propre.com, 30 décembre 2020.
- Voiture électrique : le prix des batteries continue de chuter drastiquement, automobile-propre.com, 6 décembre 2021.
- Bruxelles veut imposer des batteries électriques « propres » en Europe, Les Échos, 11 décembre 2020.
- Veolia multiplie les innovations dans le recyclage, Les Échos, 3 décembre 2014
- SNAM va fabriquer des batteries recyclées, Les Échos, 11 décembre 2017.
- Record : une voiture électrique parcourt 1 280 kilomètres en 24 heures, sur maxisciences.com, 7 décembre 2011.
- Environnement et climat : la Commission investit 281,4 millions d'euros dans de nouveaux projets relatifs à l'environnement et au climat, sur europa.eu, 3 juillet 2013 (consulté le 8 novembre 2016).
- « BMW et la start-up Solid Power partenaires dans les batteries solides », automobile-propre.com, 22 décembre 2017.
- Une start-up pour des batteries de plus en plus rapides, CNRS, 23 novembre 2017.
- Lisa : un projet européen pour le développement de batteries lithium-soufre, automobile-propre.com, 24 décembre 2018.
- Enevate annonce une révolution dans les technologies de batterie, sur automobile-propre.com, 12 février 2020.
- La batterie QuantumScape va-t-elle révolutionner la voiture électrique ?, automobile-propre.com, 12 décembre 2020.
- QuantumScape a présenté le 8 décembre les performances de sa cellule de batterie tout-solide, 11 décembre 2020.
- L'Europe lance un deuxième Airbus des batteries électriques avec Tesla et BMW, Les Échos, 26 janvier 2021.
Articles connexes
- Accumulateur lithium
- Accumulateur électrique
- Lithium
- Système de contrôle des batteries d'accumulateurs
- Stockage de l'énergie
- Portail de l’énergie
- Portail de l’automobile
- Portail de l’électricité et de l’électronique
- Portail de la chimie