Woodblock printing on textiles
Woodblock printing on textiles is the process of printing patterns on textile, usually of linen, cotton or silk, by means of carved wooden blocks.

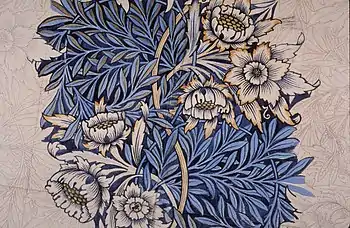
History
Origins
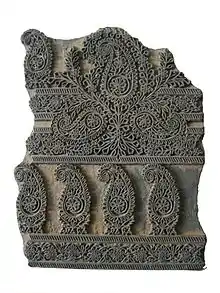

Printing patterns on textile is so closely related in its ornamental effects to other methods of similar intention, such as by painting, dyeing, and weaving, that it is almost impossible to determine from the picturesque indications afforded by ancient records and writings of pre-Christian, classical or even medieval times, how far, if at all, allusion is being made in them to this particular process. Hence its original invention must probably remain a matter of inference only.
Woodblock printing on textiles is perhaps traceable to a primeval use of blocks of stone, wood, etc, so cut or carved as to make impressions on surfaces of any material. Ancient civilisations, such as China, Egypt, and Assyria, in which the existence of these can be traced, probably used printing on textiles in addition to other materials from a very early period. For example, there is direct evidence that peoples in South Asia, including some from the Punjab and Mumbai, used printing for the decoration of textiles extensively from an early date. Starting in the 16th century, European and especially Dutch merchants bought printed and painted calico for trade. In contrast, despite the great skill displayed by the Chinese in ornamental weaving and other branches of textile art, there seems to be no direct evidence of their having used printing for the decoration of textiles. Woodblock printing was developed and modified in Europe in the nineteenth century by machinery and the adoption of stereotypes and engraved metal plates.
Ancient world
As in, the case of weaving and embroideries, specimens of printed stuffs have of recent years been obtained from disused cemeteries in Upper Egypt (Akhmim and elsewhere) and tell us of Egypto-Roman use of such things. Some few of them are now lodged in European museums. For indications that early Egyptians, Greeks and Romans were acquainted with the process, one has to rely upon less evidence. Of textiles painted by Egyptians there are many actual examples. Apart from these there are wall paintings, e.g., those of Beni Hasan (c. 2200–1800 BC), which depict Egyptian people wearing costumes irregularly patterned with spots, stripes and zigzags, which may have been more easily stamped than embroidered or woven. A more complicated and orderly pattern well suited to stamping occurs in a painting about 1320 BC, of Hathor and King Meneptha I. Herodotus, referring to the garments of inhabitants of the Caucasus, showing representations of various animals.
When Alexander invaded India in 327 BC, there were reportedly block-printed textiles produced there.[1][2][3]
Pliny the Elder describes a process employed in Egypt for the colouring of cloth. After pressing the material, which is white at first, they saturate it, not with colours, but with mordants that are calculated to absorb colour. He does not explain how this saturation is done. But as it is clearly for the purpose of obtaining a decorative effect, stamping or brushing the mordants into the material may be inferred. When this was finished the cloth was plunged into a cauldron of boiling dye and removed the next moment fully coloured. It is a singular fact, too, that although the dye in the pan is of one uniform colour, the material when taken out of it is of various colours according to the nature of the mordants that have been respectively applied to it. Egypto-Roman bits of printed textiles from Akhmim exhibit the use, some three hundred years later than the time of Pliny, of boldly cut blocks for stamping figure-subjects and patterns onto textiles. Almost concurrent with their discovery was that of a fragment of printed cotton at Arles in the grave of St Caesarius, who was bishop there about AD 542. Equal in archaeological value are similar fragments found in an ancient tomb at Quedlinburg. These, however, are of comparatively simple patterns.
Medieval Europe
Museum specimens establish the fact that more important pattern printing on textiles had become a developed industry in parts of Europe towards the end of the 12th and the beginning of the 13th century.
According to Forrer (Die Kunst des Zeugdrucks, 1898) medieval Rhenish monasteries were the cradles of the artistic craft of ornamental stamp or block cutting, although it is now recognised that some of the examples he relied on are modern forgeries. In rare monastic manuscripts earlier in date than the 13th century, initial letters (especially those that recurred frequently) were sometimes stamped from hand-cut blocks; and German deeds of the 14th century bear names of block cutters and textile stampers as those of witnesses. Amongst the more ancient relics of Rhenish printed textiles are some of thin silken stuff, impressed with patterns in gold and silver foil. Of these, and of a considerable number of later variously dyed stout linens with patterns printed in dark tones or in black, specimens have been collected from reliquaries, tombs and old churches.
The first written reference to printed textiles in Europe is found in Florentine trade regulations from the fifteenth century. In 1437, Cennino Cennini published a treatise describing the technique.[4]
Early modern Europe
Augsburg, famous in the 17th century for its printing on linens, etc., supplied Alsace and Switzerland with many craftsmen in this process. After the revocation of the edict of Nantes, French refugees took part in starting manufactories of both painted and printed cloths in Holland, England and Switzerland; some few of the refugees were allowed back into France to do the same in Normandy: manufactories were also set up in Paris, Marseilles, Nantes and Angers; but there was still greater activity at Geneva, Neuchtel, Zurich, St Gall and Basel. The first textile printing works in Great Britain are said to have been begun towards the end of the 17th century by a Frenchman on the banks of the Thames near Richmond, and soon afterwards a more considerable factory was established at Bromley Hall in Essex; many others were opened in Surrey early in the 18th century. At Muihouse the enterprise of Koechlin, Schmatzer and Dollfus in 1746, as well as that of Oberkampf at Jouy, led to a still wider spread of the industry in Alsace. In almost every place in Europe where it was taken up and followed, it was met by local and national prohibitions or trade protective regulations and acts, which, however, were gradually overcome.
Technique
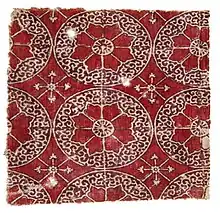
Preparing the block
Woodblocks for textile printing may be made of box, lime, holly, sycamore, plane or pear wood, the latter three being most generally employed. They vary in size considerably, but must always be between two and three inches thick, otherwise they are liable to warping, which is additionally guarded against by backing the wood chosen with two or more pieces of cheaper wood, such as deal or pine. The several pieces or blocks are tongued and grooved to fit each other, and are then securely glued together, under pressure, into one solid block with the grain of each alternate piece running in a different direction.
The block, being planed quite smooth and perfectly flat, next has the design drawn upon, or transferred to it. This latter is effected by rubbing off, upon its flat surface, a tracing in lampblack and oil, of the outlines of the masses of the design. The portions to be left in relief are then tinted, between their outlines, an ammoniacal carmine or magenta, for the purpose of distinguishing them from those portions that have to be cut away. As a separate block is required for each distinct colour in the design, a separate tracing must be made of each and transferred (or put on as it a termed) to its own special block.
Having thus received a tracing of the pattern the block is thoroughly damped and kept in this condition by being covered with wet cloths during the whole process of cutting. The blockcutter commences by carving out the wood around the heavier masses first, leaving the finer and more delicate work until the last so as to avoid any risk of injuring it during the cutting of the coarser parts. When large masses of colour occur in a pattern, the corresponding parts on the block are usually cut in outline, the object being filled in between the outlines with felt, which not only absorbs the colour better, but gives a much more even impression than it is possible to obtain with a large surface of wood. When finished, the block presents the appearance of flat relief carving, the design standing out like letterpress type.
Fine details are very difficult to cut in wood, and, even when successfully cut, wear down very rapidly or break off in printing. They are therefore almost invariably built up in strips of brass or copper, bent to shape and driven edgewise into the flat surface of the block. This method is known as coppering, and by its means many delicate little forms, such as stars, rosettes and fine spots can be printed, which would otherwise be quite impossible to produce by hand or machine block printing.
Frequently, too, the process of coppering is used for the purpose of making a mold, from which an entire block can be made and duplicated as often as desired, by casting. In this case the metal strips are driven to a predetermined depth into the face of a piece of lime-wood cut across the grain, and, when the whole design is completed in this way, the block is placed, metal face downwards in a tray of molten type-metal or solder, which transmits sufficient heat to the inserted portions of the strips of copper to enable them to carbonize the wood immediately in contact with them and, at the same time, firmly attaches itself to the outstanding portions. When cold a slight tap with a hammer on the back of the limewood block easily detaches the cake of the type-metal or alloy and along with it, of course, the strips of copper to which it is firmly soldered, leaving a matrix, or mold, in wood of the original design. The casting is made in an alloy of low melting-point, anti, after cooling, is filed or ground until all its projections are of the same height and perfectly smooth, after which it is screwed onto a wooden support and is ready for printing. Similar molds are also made by burning out the lines of the pattern with a red-hot steel punch, capable of being raised or lowered at will, and under which the block is moved about by hand along the lines of the pattern.
Other tools
In addition to the engraved block, a printing table and colour sieve are required. The table consists of a stout framework of wood or iron supporting a thick slab of stone varying in size according to the width of cloth to be printed. Over the stone table top a thick piece of woolen printers blanket is tightly stretched to supply the elasticity necessary to give the block every chance of making a good impression on the cloth. At one end, the table is provided with a couple of iron brackets to carry the roll of cloth to be printed and, at the other, a series of guide rollers, extending to the ceiling, are arranged for the purpose of suspending and drying the newly printed goods. The colour sieve consists of a tub (known as the swimming tub) half filled with starch paste, On the surface of which floats a frame covered at the bottom with a tightly stretched piece Of mackintosh or oiled calico. On this the colour sieve proper, a frame similar to, the last but covered with fine woolen cloth, is placed, and forms when in position a sort of elastic colour trough over the bottom of which the colour is spread evenly with a brush.
Printing process

The printer commences by drawing a length of cloth, from the roll, over the table, and marks it with a piece of coloured chalk and a ruler to indicate where the first impression of the block is to be applied.
They then applies the block in two different directions to the colour on the sieve and finally presses it firmly and steadily on the cloth, ensuring a good impression by striking it smartly on the back with a wooden mallet. The second impression is made in the same way, the printer taking care to see that it fits exactly to the first, a point which he can make sure of by means of the pins with which the blocks are provided at each corner and which are arranged in such a way that when those at the right side or at the top of the block fall upon those at the left side or the bottom of the previous impression the two printings join up exactly and continue the pattern without a break. Each succeeding impression is made in precisely the same manner until the length of cloth on the table is fully printed. When this is done it is wound over the drying rollers, thus bringing forward a fresh length to be treated similarly.
If the pattern contains several colours the cloth is usually first printed throughout with one, then dried, re-wound and printed with the second, the same operations being repeated until all the colours are printed.
Many modifications of block printing have been tried from time to time, but of these only two tobying and rainbowing are of any practical value. The object of tobey printing is to print the several colours of a multicolour pattern at one operation and for this purpose a block with the whole of the pattern cut upon it, and a specially constructed colour sieve are employed. The sieve consists of a thick block of wood, on one side of which a series of compartments are hollowed out, corresponding roughly in shape, size and position to the various objects cut on the block. The tops of the dividing walls of these compartments are then coated with melted pitch, and a piece of fine woolen cloth is stretched over the whole and pressed well down on the pitch so as to adhere firmly to the top of each wall; finally a piece of string soaked in pitch is cemented over the woolen cloth along the lines of the dividing walls, and after boring a hole through the bottom of each compartment the sieve is ready for use. In operation each compartment is filled with its special colour through a pipe connecting it with a colour box situated at the side of the sieve and a little above it, so as to exert just sufficient pressure on the colour to force it gently through the woolen cloth, but not enough to cause it to overflow its proper limits, formed by the pitch-soaked string boundary lines.
The block is then carefully pressed on the sieve, and, as the different parts of its pattern fall on different parts of the sieve, each takes up a certain colour that it transfers to the cloth in the usual way. By this method of tobying from two to six colours may be printed at one operation, but it is only applicable to patterns where the different coloured objects are placed at some small distance apart, and that, therefore, it is of but limited application.
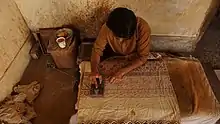
See also
References
- "Textile Printing: History & Techniques | Study.com". Study.com. Retrieved 2018-05-20.
- Imagawa, Misaki. "Printing In Progress... - History of woodblock printing". Retrieved 3 June 2018.
- "Textile - Printing". Encyclopedia Britannica. Retrieved 2018-06-03.
- "Printed linen". Victoria and Albert Museum. Retrieved 12 June 2017.
- This article incorporates text from a publication now in the public domain: Cole, Alan Summerly (1911). "Textile-printing". In Chisholm, Hugh (ed.). Encyclopædia Britannica. Vol. 26 (11th ed.). Cambridge University Press. pp. 694–708.